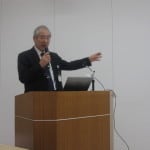
Yesterday, our Lean Healthcare tour of Japan (with Kaizen Institute) took us to our second hospital, this time in Tokyo. The CEO, Shuhei Iida, MD, pictured at left, spent a lot of time with us, talking generally about their “MQI” program – or Medical Quality Improvement. I suggest checking out their website using Google Chrome (which will translate it) or use the Google Translate service.
Dr. Iida talked about the connections between “Kaizen” (small improvements) and innovation (larger improvements) and how, together, they lead to breakthroughs. He also talked about how one is absolutely necessary for the other to occur.
Hear Mark read this post — subscribe to Lean Blog Audio
Dr. Iida has been the CEO for just over 20 years and his hospital receives visitors from around the world, including Europe and Africa. They were on the verge of bankruptcy when he took the job in 1991 and they are now “in the black” and had the money to build a new hospital, while most Japanese hospitals are losing money today, he said.
Their annual “theme” for MQI activities is “think for yourself and take action.” Dr. Iida stated that it's easy for an organization to talk about change and innovation, but harder to do.
Dr. Iida said, multiple times, that Kaizen (small change) alone won't transform the hospital or lead to breakthroughs. But, he emphasized that:
“if you keep doing Kaizen, you will get innovation.”
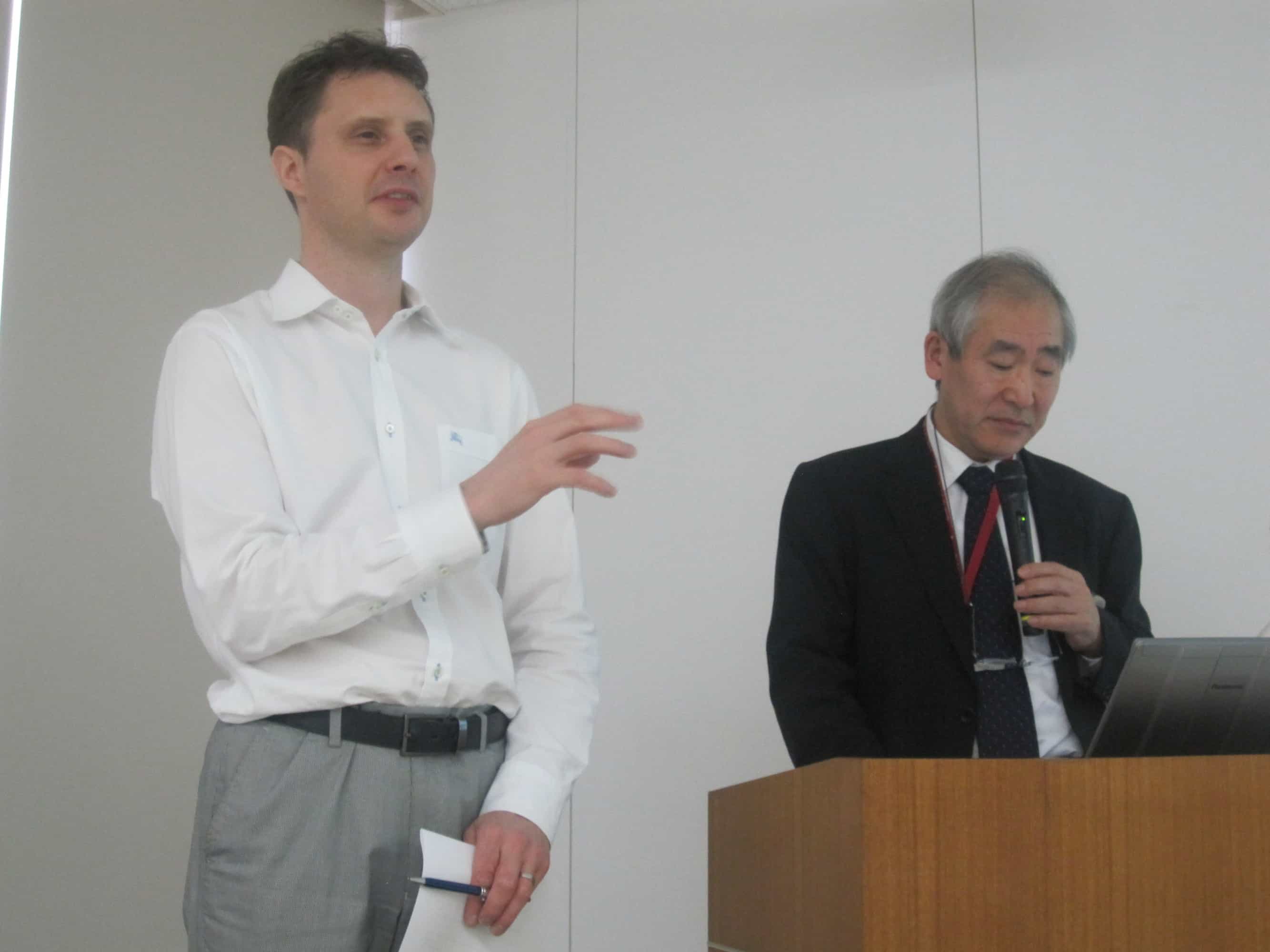
People love talking about “innovation” as a goal (I would add it's a “sexier” concept than continuous incremental improvement, if you will.)
Dr. Iida said that you don't plan to innovate — it happens by accident or chance, not by design.
“As you do Kaizen, you increase your chance of innovation, as you stumble into things. As you keep doing Kaizen, you also look for big jumps.”
The final thought on Kaizen was that “it is not just about improving operations, but also breaking down walls and building a better place.”
Part of building a better place is Dr. Iida's view that “we are not just interested in improving processes, but also developing people.”
Update: This idea of being a “development company” is something I blogged about after a later trip to Japan in 2018:
On this topic, there's an amazing video that was made last night by two Belgian tour members and a member of the tour organizing team. They made this in a bar, using beer coasters, at about 11 pm and midnight last night. It's brilliant. See their blog post about the video and follow them on Twitter:
- Thomas (@tdgroote)
- Gert (@gertlinthout)
- Brian (@brian_hk)
p.s. You can read a detailed blog post about the first hospital that we visited and their 5S program – written by Thomas and Gert.
Learn about future tours:

Please scroll down (or click) to post a comment. Connect with me on LinkedIn.
Let’s work together to build a culture of continuous improvement and psychological safety. If you're a leader looking to create lasting change—not just projects—I help organizations:
- Engage people at all levels in sustainable improvement
- Shift from fear of mistakes to learning from them
- Apply Lean thinking in practical, people-centered ways
Interested in coaching or a keynote talk? Let’s start a conversation.
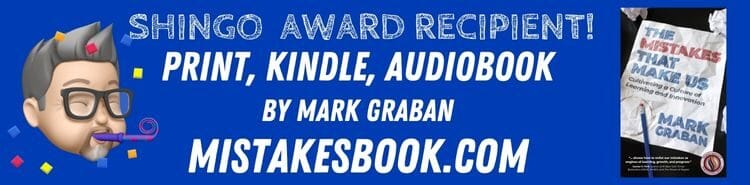
Mark
In fact, creativity follows an increasingly better understood neural pathway– relationship based on communication, willingness to engage for involvement, and then furtile ground to learn and even be able to be creative–appear to match to different and sometimes conflicting brain areas.
‘Increasing the chances of innovation’ results when we pay attention to cultivating the neural path– just so happens many, if not most Lean practices do just that. No surprise for this correlation.
‘You can read a detailed blog post about the first hospital that we visited and their 5S program – written by Thomas and Gert.’
5S as a communication strategy and tool—brilliant!
Keep the cards and letters coming!
Mark
[…] appreciate the $50 savings won’t get the $50,00 savings [in a later improvement].” As I wrote about yesterday, doing lots of small Kaizen improvements allows you to stumble across larger opportunites, as they […]
Maybe I’ve just become more observant recently, but it seems that much of the current “leadership” thought coming out of Lean discussions includes “developing people”. Can organizations that are stuck on “holding people accountable” as a development scheme really do Lean? Sorry for all the quote marks.
It is not ‘accountability’ that is the issue, but the intent behind accountability that matters.
If ‘holding people accountable’ is intended to get people to do something I want them to do, then it would not be compatible with Lean.
But if it reflects people following through on commitments they have been part of formulating and have made in order to learn if their countermeasures perform as intended, and so as to adjust and refine the process being studied, then it is very much in keeping with a Lean approach.
Mark
Yeah, I think anonymous put “accountability” in quotes because that term “hold people accountable” is often just a way of describing bullying management behaviors – including blaming and forcing others to do what we want.
Yes, another example of words and phrases hijacked by those managing for conformity, rather than engagement. Just like ‘buy in’, ‘team’, ‘associate’, and ‘naysayer’.
[…] In his latest book, Maurer brings these ideas back to the workplace, with stories about how this same kaizen mindset can be applied to improve quality, boost morale, reduce costs, reduce healthcare expenses, and more. The book is focused more on businesses, hospitals, and organizations, rather than individuals – but the understanding of how change happens is based on our own personal brain chemistry and evolution. Maurer calls kaizen “a doable path to innovation” because we’re more likely to have big changes occur when we start small. I wrote about similar thoughts from a Japanese hospital CEO back in November. […]
[…] The practice of Kaizen, of course, brings lots of small improvements. But, it’s often surprising how breakthrough ideas with a really impact come out of the process of identifying, exploring, implementing, and tweaking relatively small ideas. Read what I saw a Japanese hospital CEO say about this in a post from last year. […]
I’m working with Kaizen Institute to do another Lean Healthcare study trip to Japan, the week of November 17. 2014.
Contact me if you’re interested in learning more.
[…] million dollar ideas from the start and we shouldn’t pressure people for ROI or cost savings. As a hospital CEO said in 2012, the best way to find ideas with a big impact is to find and implement lots of […]
[…] Mark’s note: Today’s guest post is by Gert Linthout, from Belgium. Gert and I were part of the same Lean healthcare study trip to Japan last November. He was the co-creator of this creative video on Kaizen that I featured in this blog post. […]
[…] study trip to Japan back in 2012. He was the co-creator of this creative video on Kaizen that I featured in this blog post. See his previous guest […]
[…] study trip to Japan back in 2012. He was the co-creator of this creative video on Kaizen that I featured in this blog post. See his previous guest […]
[…] has also written about his experience visiting Nerima General, as well many reflections on Lean in Japan and in Japanese […]