Listen:
LeanBlog Podcast #30 is an interview with Bob Emiliani, author of the books Better Thinking, Better Results, and Real Lean: Understanding the Lean Management System (Volume One) (and Volume Two). Bob had a long career at United Technologies, Pratt & Whitney and also has degrees in Mechanical Engineering and Chemical Engineering, as well as a PhD in engineering from Brown University.
Better Thinking, Better Results, which is now out in a 2nd revised edition, has a new epilogue about Wiremold, the subject of the book, and how they have moved away from Lean after their acquisition by another company. In this podcast, we'll talk about why that happened and what others can learn from the story, in efforts to prevent the dismantling of even the most successful of Lean transformations. You can visit the page for this podcast at leanpodcast.org for links to Bob and his books, including the “Real Lean” series.
Keywords and Main Points, Episode #30
- Why did you update the Wiremold story and produce a second edition of your book Better Thinking, Better Results?
- So what happened?
- Why didn't Legrand value the Lean transformation that Art, his team, and the people of Wiremold did?
- So it looks like Legrand made some mistakes.
- What can we learn from what happened to Wiremold?
If you have feedback on the podcast, or any questions for me or my guests, you can email me at leanpodcast@gmail.com or you can call and leave a voicemail by calling the “Lean Line” at (817) 372-5682 or contact me via Skype id “mgraban”. Please give your location and your first name. Any comments (email or voicemail) might be used in follow ups to the podcast. Click here for the main LeanBlog Podcast page with all previous episodes.
Automated Transcript:
Mark Graban:
Well, joining us from Connecticut today is Bob Emiliani, thank you for joining us on the Lean blog podcast.
Bob Emiliani:
It's my pleasure.
Mark Graban:
So, I wanted to talk about why you updated the Wiremold story. What was behind producing a second edition of the book Better Thinking, Better Results?
Bob Emiliani:
Well, I did it because people wanted to know what happened to Wiremold's lean effort since they were bought by Legrand in 2000. People also wanted to know what happened after Art Byrne and the other top managers started to retire in 2002. And ultimately they wanted to know, did Lean stick? In the first edition of the book, I wrote that I was skeptical the Lean management would continue at Wiremold under new ownership and with a new leadership team in which the Legrand personnel would eventually hold key positions. So I wrote that Legrand management did not buy Wiremold because it was lean.
Bob Emiliani:
They did not have any real interest in Wiremold's lean capabilities or the management team's skills as lean practitioners. So Legrand, like most manufacturers, has long operated their business according to Batch and Q principles and practices, and therefore it was just unrealistic to expect Legrand senior management to recognize the value of Wiremold's lean management system. I also said in the first edition that it would be very interesting to see how Wiremold fares in the years to come under a parent company whose management practices are rooted in wasteful batch and queue. The question was, will Wiremold managers be able to keep the lean management system alive, or will it succumb to the strong force of conventional management practices? So it turns out that Lagrange, conventional batch and queue management practices prevailed.
Bob Emiliani:
How and why this happened is something that all lean practitioners should know about because there's so much to learn from it.
Mark Graban:
Yeah, that's unfortunate, and I'd agree it's something to learn from after reading the epilogue to the book. So what happened? What's the story behind it?
Bob Emiliani:
First of all, I'd like to say that I think it's extremely important to be consistent and apply a lean mindset to these types of situations where lean has failed, just as we would do to any problem. So we start by seeing things as they actually are, even if it's ugly and even if it's not what we want to see, and we confront the reality, and then we can identify ways to improve. Something that troubled me for a while is that, too often, a company's lean efforts are characterized as problem-free. Basically, people just talk about the good stuff and tend to present a much better picture than what actually exists, and it's just not reality. There are a lot of problems, and we need each of these problems to surface in order to understand the root causes and identify and implement practical countermeasures.
Bob Emiliani:
So many people see what happened in Wiremold as a bad thing, and in many respects, it is. But it's also a very valuable story from which we can all learn from to help other people's lean transformation efforts. I firmly believe that bringing this story to light is fully consistent with the lean principles, continuous improvement and respect for people. Sure, Wiremold backslid rather dramatically. Within three years after Ardburn retired, Wiremold had a very strong management bench, two to three layers deep to backfill art and the other senior managers who retired or might leave.
Bob Emiliani:
But each member of Art's management team had great difficulty getting Legrand senior management to understand lean. They all struggled and so they eventually left. And of course, when that happened, LeGron inserted their personnel into key leadership positions and they knew little or nothing about the lean management system. So they didn't support lean in any significant way, and they did not participate in process improvement activities. And in a lot of instances, they purposefully dismantled what art and his team had done.
Bob Emiliani:
You know, this isn't, it's not uncommon. Changes in company ownership or top leadership are a huge discontinuity that is almost always fatal to lean. And history bears this out all the way back to the days of the scientific management system. In the late 18 hundreds, when company owners are top leaders change, the management system quickly reverts back to the old ways of leading and managing the business. And I thought the same thing might happen at Wiremold, and it did.
Bob Emiliani:
I think it's important to understand. What happened at Wiremold illustrates how wrong headed the thinking is that if people practice lean for several years, it will stick, that it will become part of the company's DNA. And guess what? It doesn't stick. And executives and others need to confront that reality.
Bob Emiliani:
Lean requires constant attention, maintenance and improvement to keep it alive and healthy. It's people that keep lean alive through the daily practice of lean principles, processes and tools. And when the top leaders who have an interest in keeping Lean alive leave the company and are replaced by leaders who don't have the same interest, then lean dive. As you can imagine, it was personally very painful for Wyrmwell people to go backwards. They fought very hard.
Bob Emiliani:
But in the end, what choice do you have? You either do what the boss wants or you leave.
Mark Graban:
Yeah. So why do you think it was that Legrand didn't value the lean transformation that Art and his team and all the people at Wiremold had gone through those previous years?
Bob Emiliani:
Well, Le Guan senior managers didn't learn like most senior managers, they didn't learn lean in college or graduate school. They didn't get exposed to it on the job, wasn't relevant. And those at the top apparently had little or no curiosity to learn about lean management. Art and his management team did not expect that to be the case, especially since Wiremult had done so well with lean early on. There were good indications that Legrand senior management did want to learn about Lean.
Bob Emiliani:
After all, who wouldn't want to adopt a winning management system? But apparently they didn't want to. So, Lagrand senior management is not at all unique in this respect. They're just like most other top managers.
Mark Graban:
Yeah, so it sounds like unfortunately Legrand made some mistakes along the way, or at least we might view it that way, as proponents of lean. So I was wondering if you could maybe talk about what you view some of those mistakes to be, or you talked about dismantling some of the lean practices. Maybe if you can share an example or two of you know how and why that was done.
Bob Emiliani:
Okay, well, from a lean perspective, yes, they clearly did make some mistakes and in fact, they made some very big mistakes, among other things, you know, abandoning the respect for people principle and blaming people for errors. Going from 16 or 18 of an inventory turns back to three or four inventory turns cost a lot of money, which of course impacts shareholders and negatively impacts customers. The collaborative relationship with suppliers gave way to arm's length, zero-sum power-based bargaining relationships that emphasize price. And as you might imagine, there were plant closings and outsourcing to lower wage countries, basically the usual stuff. Now, it's very important for people to clearly understand that Legrand is not a bad company and its leaders are not bad people.
Bob Emiliani:
The actions that Legrand executives took after they bought Wiremold were sensible from their point of view. They did what they were trained to do and they did it very well. They did what they thought was best for Legrand and its shareholders. It's just that what they did happens to be the exact opposite of what lean people would have done. This outcome, it highlights a significant problem inherent to lean management antecedents dating back to the late 18 hundreds and early 19 hundreds scientific management area, which very few people seem to appreciate, and I'd like to bring more attention to this.
Mark Graban:
Yeah, sure.
Bob Emiliani:
That is, managers who do not understand what waste is and the benefits of process improvements miss great opportunities and may even inadvertently end up hurting the business. It's a common problem. It has a name. It's the merger and acquisition culture clash. It's nothing new.
Bob Emiliani:
People are repeating the same errors. Sure.
Mark Graban:
Yeah. It certainly sounds like they were kind of going off of the mass production playbook. Yep. Well, so kind of identifying what happened and the situation, as you said, whether it was ugly or not, what do you think the rest of us can learn or should learn from what happened at Wiremold?
Bob Emiliani:
Well, one of the lessons learned is that we should prepare for high probability events, such as changes in company ownership or changes in top leadership. We know for certain that this will happen at some time in the future. So lean leaders need to plan for that. Art and his team did plan for these changes. In fact, they put a whole lot of effort into that.
Bob Emiliani:
But in hindsight, it still wasn't enough. Lean leaders should install countermeasures to prevent outcomes they wish to avoid. I talk about this in a chapter in my new book called Real Lean, Volume Two. It's called Lean estate planning. It's similar to how we might personally plan for our own estates when our day comes.
Bob Emiliani:
It's a new idea that I think people need to pay some attention to to prevent these kind of things from happening. Another lesson learned is that lean doesn't stick by itself, even after ten or 20 years of effort. If new executives one day come into the company with other interests, just look at Toyota. Their executives have long been worried about complacency. Even after seven decades of practicing their management system, they know that they can slip away quickly and that they have to remain forever, forever vigilant and ensure that the top leaders understand the people who are promoted to the top, that they understand and practice the management system, and further, that they continue to learn the management system, no matter how long they work at Toyota.
Mark Graban:
Sure.
Bob Emiliani:
I'll say it again. Lean requires constant attention, maintenance, an improvement to keep it alive and healthy. It's people that keep lean alive through the daily practice of lean principles, prophecies, and tools. And, you know, when the top leaders who have the interest in keeping lean aligned leave and are replaced by leaders who don't have the same interest, and lean dies very quickly, you know, the long view of history shows this happening over and over again. And in order for it not to happen, we need to be aware of what has happened in the past, and this has been my main interest in the past few years and is the principal subject of the book I mentioned earlier.
Bob Emiliani:
For a lousy $10, you can learn how to avoid a lot of traps and errors. And I think people will be utterly amazed the extent to which the lean movement today is faithfully reliving the past and runs a very high risk of realizing the same marginal or unfavorable outcomes as what people have achieved in the past.
Mark Graban:
Sure.
Bob Emiliani:
You know, the good news is there's a lot of practical countermeasures that can be applied, but basically only if we want to confront, see that reality, confront it head on and take action.
Mark Graban:
Yeah. Well, yeah. I appreciate you sharing that story, not only in the new edition of the book, which I've had a chance to and was familiar with the story from reading the original edition a couple years back. If listeners want to go to website leanpodcast.org, I'll make sure that there's links to Bob's website and both of those, both the second edition of Better Thinking, Better Results and the two volumes of the other book he mentioned, real Lean, to make sure people can find that. I was wondering if you could share some thoughts, maybe what kind of reactions that you've gotten from the updated story, the new second edition, and what's been happening in Wiremold?
Bob Emiliani:
Well, the reaction has been favorable in the sense that people are getting some insight into what can happen, how lean can backslide, how things can unravel despite tremendous long term effort. And that helps them plan for the future better. It makes them more aware of pitfalls and problems. One thing people absolutely dislike is for their good efforts to just fall by the wayside. And in going through the history of this earlier management system called scientific management, you read these, the leaders of that movement were very dismayed that their hard efforts eventually just didn't amount to much.
Bob Emiliani:
And nobody likes to see that happen to their efforts, of course. So this is starting to give an insight into the ways in which things can unravel and that we need to be aware of that and bring it more to the front, front and center, directly address it. There's a lot of good news stories about companies doing lean, and that's great and so forth, but we don't spend enough time looking at the failures and understanding what's going on there. And there's just tremendous amount to be learned from that. And if we really expect this to move forward, then we have to get into understanding the failures or where the outcomes were much less than expected?
Mark Graban:
Yeah, I think that's a healthy thing. I mean, one of the books on my shelf is this book how to prevent lean implementation failures by a different author who kind of highlights here are some of the things that can go wrong. And I think it's helpful to, I guess the same way you might use failure mode effects analysis to look at a physical process, maybe to anticipate what are the things that could go wrong with our management system? What's the risk? What would the impact be?
Bob Emiliani:
That's right. And that, you know, to go through formal failure analysis is not something that is normally found in the business world. And for example, in business schools, they rely extensively on the case study method. And the vast majority of case studies report something positive. And it's not so familiar to look at something negative and it's very unfamiliar in a business school setting to apply formal root cause analysis to the errors that occurred.
Bob Emiliani:
And we need to start doing that.
Mark Graban:
Yeah. And I think if we're talking through maybe to looking at at least root cause or root causes of what happened with Wiremold, you strongly hinted at one of those root causes, maybe being the educational system, business school in particular, efforts underway. Or what thoughts do you have about how can we try to make sure lean ideas are starting to get taught in business schools? Or that if lean practices are good business, which I assume a lot of us listening through self selection, that we're lean people listening to a lean podcast would believe lean is good for business, what can we do to influence it? So it seems less like a foreign program or an alternative approach to business and try to get it taught as maybe a more, how can we turn it into a more conventional way of doing business?
Bob Emiliani:
Well, that's a good question. The Lean Enterprise Institute has sponsored something called Teachinglean.org that is trying to establish a group of people that are interested in bringing lean into the classroom. And then MIT's Lean Aerospace Initiative has an effort as well. There was a joint meeting of these two groups last October to discuss ways to bring lean into the classroom. But what ends up happening is it's on an individual professor by professor basis.
Bob Emiliani:
It's really not engaging the deans or the provost of business or engineering schools to establish lean management as a major pedagogical approach to management and leadership and so forth in those settings.
Mark Graban:
So it sounds like the same company trap if the leadership leaves, or in this case, if the professor moves on, someone else comes in and suddenly you're not teaching lean anymore.
Bob Emiliani:
That's basically the same thing. Yes. You're absolutely right.
Mark Graban:
Yeah. Well, hopefully we'll make progress in that area over the coming years and decades. Do you have any final thoughts that you'd want to leave with the podcast listeners here?
Bob Emiliani:
Well, I guess I just want to reemphasize the point that I think is very important is that looking back in the history of people trying to advocate a different system of management than the conventional batch and Q approach, it shows these kinds of failures and so forth happening over and over again. And I'm really trying to bring an awareness of what happened in the past so that people can gain an appreciation for how faithfully we're reliving that past. And things are different today, to be sure, in a lot of ways. But there still is, in my view, a significant risk of having marginal or unfavorable outcomes occur. And just by awareness of this, that will help us or engage us into some root cause analysis and identifying countermeasures.
Bob Emiliani:
And that should be a very different activity and effort than what has happened in the past. In the old days, the people didn't do formal root cause analysis. They just, you know, they attributed the problems to various things through reasoning. And, you know, maybe they did a five whys in their head, but they didn't really lay it out on paper and or the five whose. Yeah, right.
Bob Emiliani:
That's right. That's right. There was a bit of blame, and particularly towards senior management. But if we can engage that process and get a better understanding of what's going on, then I think that serves everyone very well, all the stakeholders, customers, suppliers, investors, employees, communities, etcetera.
Mark Graban:
Yeah. Okay. Well, I'll make sure again that there are links to you and your website and the books. I really did enjoy volume one of the real lean series and looking forward to going through volume two. Hopefully we can get together again sometime and talk about some of the topics there that are in those two books.
Bob Emiliani:
Okay, great.
Mark Graban:
Okay. Well, Bob, thanks again for being here on the podcast. Really enjoyed it.
Bob Emiliani:
Thank you. I hope it's been helpful.
Article Based on the Interview
The Crucial Lessons from Wiremold's Lean Transformation Journey
Lean management principles have significantly impacted the manufacturing sector, promising operational efficiency, waste reduction, and a culture of continuous improvement. The case of Wiremold's lean transformation and subsequent challenges under new ownership provides insightful lessons for organizations and lean practitioners. This examination explores the impetus for revisiting the Wiremold story, the consequences of leadership transitions on lean practices, and the enduring need for alignment between lean principles and executive management.
Revisiting the Wiremold Story: A Second Look at Lean's Sustainability
The story of Wiremold's lean transformation is widely recognized in the lean management community for its initial success and the profound challenges it encountered following a change in ownership. The acquisition of Wiremold by Legrand in 2000 marked a significant shift in the company's management philosophy and practices. This transition raised questions about the sustainability of lean transformations in the face of ownership and leadership changes. Critics and supporters of lean methodologies alike have looked to Wiremold as a case study in the persistence of lean principles under new management, especially when the incoming leadership does not prioritize or understand lean management's value.
The Impact of Leadership Changes on Lean Practices
Bob Emiliani's decision to update the Wiremold story highlights the critical role of leadership in sustaining lean practices. The departure of Wiremold's senior management, including Art Byrne, and their replacement with Legrand's executives, symbolized a broader shift away from a lean-centric culture. This leadership transition underscores a common challenge in maintaining lean transformations: the dependency on the commitment and understanding of top managers. Lean management is not just a set of tools and processes but a holistic management philosophy that requires continuous engagement, learning, and adaptation from all levels of an organization, especially its leaders.
Lean's Vulnerability to Conventional Management Practices
The Wiremold experience illustrates the vulnerability of lean transformations to conventional management practices, particularly in the context of mergers and acquisitions. Despite the achievements under its lean management system, Wiremold's practices were gradually dismantled in favor of Legrand's batch and queue methodologies. This shift reveals a fundamental tension between lean management's emphasis on flow, value creation, and waste elimination, and traditional management's focus on scale, efficiency, and control. The challenges faced by Wiremold also highlight the necessity of aligning company culture, leadership, and management practices to sustain lean principles over the long term.
The Importance of Continuous Improvement and Respect for People
One of the foundational pillars of lean management is the principle of continuous improvement, complemented by a deep-seated respect for people. Wiremold's journey reflects the importance of these principles not just in achieving operational efficiency but in fostering a culture that can adapt to and thrive through changes. The failure to maintain lean practices at Wiremold post-acquisition serves as a powerful reminder that lean transformations require more than just surface-level engagement with lean tools and techniques. They necessitate a profound commitment from leadership to sustain a culture of improvement, respect, and learning.
Confronting the Reality of Lean Transformations
The unraveling of lean at Wiremold conveys a critical lesson: the need to confront the reality of lean transformations, including their challenges and failures. Understanding and learning from these experiences are essential for the lean community and organizations aspiring to undertake lean transformations. By acknowledging the difficulties, organizations can better prepare for the hurdles of maintaining lean principles amidst leadership transitions and changing business environments. This acknowledgment also reinforces the importance of fostering a culture where lean principles are deeply ingrained and practiced by everyone in the organization, not just the lean team or senior management.
Lean Management's Continuous Journey
Wiremold's story is a testament to the ongoing journey of lean management. The implications of leadership changes on lean practices, the tensions between lean and conventional management philosophies, and the paramount importance of continuous improvement and respect for people are lessons that resonate beyond Wiremold. These insights underscore the necessity for persistent effort, strategic alignment, and cultural commitment to keep lean alive and thriving. For organizations embarking on or sustaining a lean transformation, Wiremold's experiences offer invaluable lessons on the critical factors that influence the success and longevity of lean initiatives.
Building a Sustainable Lean Culture Amidst Change
The challenges encountered by Wiremold after its acquisition by Legrand spotlight a critical aspect of lean management not often discussed: sustainability. Despite a strong start, Wiremold's lean journey faced significant roadblocks, chiefly due to a culture clash and a shift in leadership priorities. This scenario is not unique to Wiremold but is a common pitfall for many organizations attempting to embed lean into their fabric. The question then arises: How can a company build a sustainable lean culture that withstands changes in leadership and ownership?
Embedding Lean Principles at All Levels
A key lesson from Wiremold's story is the absolute necessity of embedding lean principles at all levels of the organization. Lean cannot be the purview of the executive team alone; it must become part of the DNA of the company. This requires comprehensive training programs, ongoing education, and opportunities for all employees to engage in continuous improvement initiatives. By doing so, the organization creates a robust structure that is less likely to collapse when key leaders leave or when the company undergoes significant changes.
Fostering a Culture of Learning and Adaptability
Another critical element is fostering a culture of learning and adaptability. The initial success of Wiremold under lean management was due in part to a collective willingness to learn and adapt — qualities that were compromised after the acquisition. Organizations need to cultivate an environment where learning is continuous and change is embraced, not feared. This includes learning from failures and viewing them as opportunities for growth. Encouraging curiosity and openness at all levels can help in building resilience against the disruptive effects of leadership changes.
Planning for Leadership Transitions
Leadership transitions are inevitable, but their impact on lean practices does not have to be detrimental. Succession planning and leadership development are essential to ensure the continuation of lean principles. This should involve identifying and nurturing future leaders who are committed to lean methodologies and equipping them with the skills and knowledge needed to sustain these practices. Furthermore, current leaders should foster strong relationships with all stakeholders to build a coalition of lean advocates within the organization. This creates a buffer that can help protect lean initiatives from unfavorable executive decisions.
Lean as a Strategy for Long-Term Success
Rather than viewing lean as a set of tools or processes to be implemented, organizations need to conceptualize lean as a strategic framework for long-term success. This strategic orientation towards lean necessitates alignment between lean principles and the organization's long-term goals and objectives. It means looking beyond immediate financial gains to how lean can foster innovation, enhance customer satisfaction, and build a more agile and responsive organization.
Creating a Legacy of Lean Management
The idea of “Lean Estate Planning,” as indicated, is a novel but critical perspective on ensuring the longevity of lean principles within an organization. By treating lean management as a legacy to be preserved and passed on, leaders can instigate measures to protect this legacy against the inevitable changes the future holds. This might include establishing lean principles in company charters or bylaws, integrating lean metrics into performance evaluations, and creating lean ambassador roles tasked with upholding lean values.
Conclusion
The merger and acquisition culture clash witnessed in the Wiremold-Legrand case is a reminder of the robustness required in lean management practices. For lean to flourish, it must be deeply rooted within the organizational culture, championed by leaders at all levels, and aligned with the strategic objectives of the company. Learning from Wiremold's journey, companies can navigate the complexities of leadership transitions and ownership changes, ensuring that the lean legacy endures and continues to deliver value.
Navigating the Complexities of Lean Failure: A Deeper Understanding
The dynamics of lean management and its susceptibilities, revealed through cases like Wiremold and illuminated by experts like Bob Emiliani, underscore the multifaceted challenges organizations face in sustaining lean transformations. To navigate these complexities successfully, scrutinizing and learning from failures becomes as important as celebrating wins. Organizations aiming for long-lasting lean integration must adopt a proactive stance toward identifying and analyzing potential setbacks.
The Role of Education in Lean Management
One often overlooked aspect of embedding and sustaining lean principles within organizations is the role of formal education. As highlighted by the conversation on bringing lean management into academic curricula, there's a glaring gap in how management and leadership are traditionally taught. Business and engineering schools, predominantly showcasing success stories, seldom delve into lean management principles or dissect the failures and challenges associated with lean implementations. This creates a disconnect between academic preparations and real-world management challenges.
- Integrating Lean into Academic Curricula: Initiatives by the Lean Enterprise Institute and MIT's Lean Aerospace Initiative mark the beginning of efforts to bridge this gap. However, as noted, the engagement remains sporadic and highly dependent on individual faculty members. A more systematic approach involving deans and provosts could establish lean management as a foundational pedagogy within business and engineering schools.
Systemic Changes for Sustainable Lean Practices
For lean management to transcend the boundaries of being viewed as an “alternative” business strategy and become a mainstream approach, systemic changes in both organizational and educational structures are essential.
- Enhancing Organizational Resilience: Beyond the immediate organizational landscape, engaging in root cause analysis and understanding the multifaceted reasons behind lean backsliding or failures play a crucial role. This approach mandates a shift from attributing failures to broad, often superficial reasons towards a more nuanced, analytical understanding that can pave the way for effective countermeasures.
- Leadership and Continuity: The discussion accentuates the importance of leadership in sustaining lean initiatives. Just as the departure of a key professor can halt the teaching of lean principles in academic settings, so too can changes in organizational leadership disrupt lean practices. Ensuring the continuity of lean initiatives requires cultivating a broad base of lean advocates within organizations and incorporating lean principles into leadership development programs.
The Path Forward: Education and Practice
The challenge of embedding lean principles into the fabric of both educational institutions and organizations calls for a collaborative effort. Business schools and organizations need to work hand in hand to develop curriculums that not only teach lean management as a core subject but also prepare future leaders to deal with the complexities and challenges of sustaining lean practices in a dynamic business environment.
- Collaboration Between Academia and Industry: Strengthening the linkages between academic institutions and the industry can provide practical insights and a more nuanced understanding of the challenges involved in lean implementations. This could involve joint research initiatives, case studies focused on both successes and failures, and industry placements for students to gain hands-on experience.
- Continuous Learning and Adaptation: The key to sustaining lean initiatives lies not just in initial education but in fostering an environment of continuous learning and adaptation within organizations. Encouraging employees at all levels to engage in ongoing education, experimentation, and reflection can help organizations adapt to changes and overcome obstacles more effectively.
Conclusion
Understanding and learning from lean management failures, as elucidated by discussions with experts like Bob Emiliani, are crucial steps toward building more resilient and adaptable organizations. By integrating lean principles into the core of both management education and organizational practices, the goal of achieving sustainable lean transformations becomes increasingly attainable.
Fostering Stakeholder Engagement in Lean Environments
The philosophy of lean management, heavily underscored by continuous improvement and respect for people, inherently involves various stakeholders in its operational orbit. Engaging customers, suppliers, investors, employees, and communities in the lean process not only enriches the ecosystem but also ensures that lean principles are sustainably integrated and practiced. The dialogue between Mark Graban and Bob Emiliani emphasizes the importance of inclusivity in lean endeavors–highlighting how well-rounded understanding and cooperative efforts can propel organizations toward success.
Engaging Customers and Suppliers
- Customers form the cornerstone of any business's lean journey. By focusing on value from the customer's perspective, organizations can streamline operations, reduce waste, and enhance product quality. This customer-centric approach necessitates open communication channels and continuous feedback mechanisms to adapt to changing needs and expectations.
- Suppliers play a critical role in the lean supply chain, where collaboration and synchronized workflows contribute to the elimination of waste and the stabilization of production schedules. Developing partnerships based on mutual respect and shared lean values can lead to innovations in product development and process improvements.
Involving Investors, Employees, and Communities
- Investors are key stakeholders who benefit from the organization's lean successes through sustainable growth and profitability. Keeping investors informed about lean initiatives and their impact on long-term value creation is essential for garnering their support and understanding.
- Employees are at the heart of lean transformations. Empowering employees with lean education and involving them in problem-solving and improvement activities fosters a culture of continuous improvement. This empowerment elevates morale and productivity by making every employee a stakeholder in the organization's success.
- Communities benefit from organizations that practice lean principles by creating more sustainable business practices, reducing environmental impact, and contributing to local economies. Engaging with communities by sharing lean successes and practices can enhance an organization's social responsibility footprint.
The Importance of Communication and Continuous Improvement
The synergy between lean management and stakeholder engagement is amplified through effective communication and a commitment to continuous improvement. Open dialogue about goals, challenges, and progress helps align stakeholders' expectations and contributions. Furthermore, actively involving stakeholders in the lean improvement cycles–Plan, Do, Check, Act (PDCA)–not only maximizes the collective intelligence but also ensures that improvements are meaningful and sustained over time.
Building a Lean Culture Together
The journey towards a comprehensive lean transformation is a collaborative endeavor. By embracing the insights and perspectives of various stakeholders, organizations can overcome the complexities of lean failures and turn challenges into opportunities for growth. The conversation between Mark Graban and Bob Emiliani, with its emphasis on engagement and understanding, serves as a reminder that the success of lean initiatives is a shared responsibility. Cultivating a culture that values stakeholder input and leverages it for continuous improvement is paramount for organizations aspiring to achieve and sustain lean excellence.
Please scroll down (or click) to post a comment. Connect with me on LinkedIn.
Let’s work together to build a culture of continuous improvement and psychological safety. If you're a leader looking to create lasting change—not just projects—I help organizations:
- Engage people at all levels in sustainable improvement
- Shift from fear of mistakes to learning from them
- Apply Lean thinking in practical, people-centered ways
Interested in coaching or a keynote talk? Let’s start a conversation.
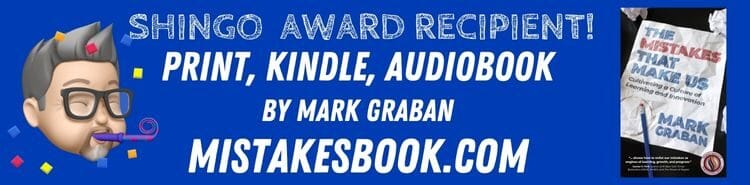
excellent podcast, Mark, thanks for tracking Bob down. There is much to learn from Wiremold, yet it is a sad story for the employees who had such pride in competing with low-cost foreign imports, successfully.
[…] can also read Bob’s thoughtful review of Art’s book. Also, listen to my podcast with Bob (who documented the Wiremold story in the book Better Thinking, Better Results: Case Study and […]
[…] equipment. Legrand was firmly committed to batch production and standard cost accounting, and the lean transformation unwound in a few […]