For a long time, I've heard the phrase “the hidden factory” used to describe various forms of waste in a factory, including rework operations and activity.
I was surprised to hear Boeing CEO Dave Calhoun refer to this in a news story using a similar phrase, “shadow factory.”
Boeing Wants to Close Its ‘Shadow Factories.' It Would Be a Positive Step.
The article is paywalled, but I was able to read it via Apple News+.
Calhoun admitted:
“In our shadow factories, we put more hours into those airplanes than we do to produce it in the first place…that's a metric I know everybody understands.”
That's wild. Spending more hours on planes being “reworked, upgraded, and checked before final delivery. That happens in a shadow factory.”
The Barrons headline refers to “closing” said factories, but that's more metaphorical than literal.
Boeing would need to improve their initial production and assembly processes to ensure “built-in quality” instead of relying on inspection and rework.
Hear Mark read this post — subscribe to Lean Blog Audio
Being able to eliminate repairs and rework requires better process controls and mistake-proofing, among other Lean tactics. It requires better training and supervision, better tool calibration, etc.
I've seen the “hidden factory” in automotive manufacturing. There's Lean automotive lore, with stories that I think go back to Jim Womack, where vehicles coming off the line at a General Motors plant went to “one of two places: minor repair or major repair.”
That's certainly not the Lean ideal, where built-in quality and “doing it right the first time” is what we aspire to. Instead of getting better at reworking planes (or any product) more efficiently, the goal, of course, is to reduce the need for rework through better production processes.
And that plan can't be “hopes and dreams” or “putting pressure on the workers.”
Join the discussion on LinkedIn:
As Jonathon Andell commented, “Cutting out the detection and containment is not the “cause” of improved quality, it's the RESULT. Calhoun is asking the tail to wag the dog.”
That's very well said.
Please scroll down (or click) to post a comment. Connect with me on LinkedIn.
Let’s build a culture of continuous improvement and psychological safety—together. If you're a leader aiming for lasting change (not just more projects), I help organizations:
- Engage people at all levels in sustainable improvement
- Shift from fear of mistakes to learning from them
- Apply Lean thinking in practical, people-centered ways
Interested in coaching or a keynote talk? Let’s talk.
Join me for a Lean Healthcare Accelerator Trip to Japan! Learn More
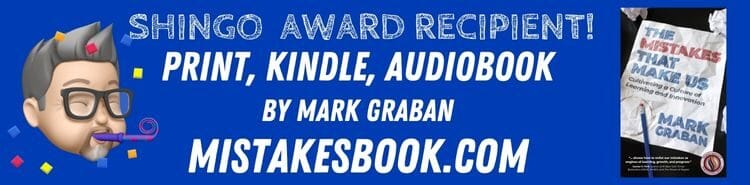
It’s a well known fact to those of us that have and do work in the industry that inspection is not something to be cut from a process because mechanics and technicians can be trained and depended upon to eliminate escapes from manufacturing. I have been on both sides of that coin. I have experienced that eliminating defects are not a matter of skill, education and great performance as it is a matter of perspective. Inspections done correctly, and practically integrated into the process is money well spent. Those two worlds clearly need to remain a part of the process. it’s not a matter of eyesight, as was originally thought. It’s how the work is observed from a quality perspective. This has been proved over and over, so senior managers need to stop trying to get by with fewer inspections. A technician or mechanic has their job to do, and they (believe it or not) have a different perspective than the inspector.
The answer clearly isn’t to cut out “detection and containment” from the process. However, if the items in the “shadow factory” are spending more time in processing than they are serving their purpose, then many its the process that is incorrect. If the process can be reworked to fit the proper steps while also doing so efficiently, the problem would be solved.