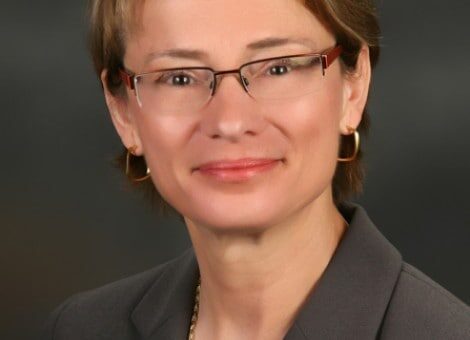
This episode is a discussion with Joan Wellman, of the consulting firm Joan Wellman & Associates.
Joan is a real pioneer in the lean healthcare arena, having started her initial work with a hospital in 1995 — I haven't found anybody who started this work earlier than her. We first met in Seattle a few months back and I'm thrilled to bring you this discussion about the early days of lean healthcare and her thoughts on the potential for the future.
Transcript
This is an automated transcript and, even after editing, some errors might remain:
Mark Graban: 00:04 Hi, this is Mark Graban. This is episode number 80 of the lean blog podcast for December 4th, 2009 my guest today is Joan Wellman of the firm, Joan Wellman and Associates. They focus on consulting for lean in healthcare. And I first met Joan a couple of months ago back in Seattle and I was really impressed with Joan, really enjoyed meeting her and I was happy to be able to have the chance to do this podcast talking about her early experiences with lean in healthcare that date back to 1995 and John's a real pioneer. I've never met somebody who has such early experience implementing and teaching lean in healthcare. So I hope you enjoy this discussion about some of those early days and some of Joan's thoughts on what there is to come with lean in healthcare.
Mark Graban: 01:06 Well Joan, I want to thank you for taking time out to join us on podcast.
Joan Wellman: 01:11 Thanks for inviting me, Mark.
Mark Graban: 01:12 Well, it's a pleasure to have you here and I'm sorry if you could start by introducing yourself to the listeners and give a little bit of background of how you first got started with Lean
Joan Wellman: 01:23 I'm Joan Wellman and I got started working in lean in the 1980s in a group here in Seattle called Delta Point Corporation. And we worked primarily with a large fortune 100 companies in particular bowling and implementing lean principles taking them to Japan to study and, and coming back and, and working on deployment of the Toyota production system principles. And I got started in health care in 1995, the head of operations at the Boeing commercial airplane group. I fell by the name of Bob Dryden. Asked me an offhanded question one day of whether I thought that the principles we were applying at Boeing would work in healthcare. And I really didn't know anything about health care and didn't know how to respond. But I went back to our office and talk with my colleagues and we reflected on the fact that we had started on the factory floor. We had moved into engineering, we'd moved into customer service and even sales and marketing areas, and we found we could make a lot of difference and that maybe this would apply in healthcare. So the next time Bob brought it up, I suggested that we have some serious conversation and we went to Overlake talk with the new CEO a fellow named Ken Graham. And the great thing about Ken was the, he was really open to trying some ideas that didn't come from healthcare. So we were really lucky that Ken and some of his colleagues were really flexible in their thinking and after to say, hey, maybe there's something that we can learn from an airplane manufacturer or a car manufacturer.
Mark Graban: 03:06 And this was in the Seattle area, is that right?
Joan Wellman: 03:09 Is was in the Seattle area. And it was a nice time because there was a lot of lean manufacturing work going on at Boeing in particular. And so there was a buzz in the community about it. So we were lucky and to have somebody, yeah, I think lucky is right to think in terms of someone being open minded. Mid nineties I mean that, that's probably as early as a, an instance of a hospital applying lean as we have in, in the modern lean healthcare era. Wouldn't you say? I mean, how, how do you Kevin Looking back and say what, what, what was it other than kind of analyze, you know, flexibility and thinking that helped inspire them to actually give it a try?
Joan Wellman: 03:58 Well, people were really stuck. They were really stuck on how to improve and it was an era of managed care and they had a lot of cost pressure and they really didn't have any way to go but up. And so I think that that sense of urgency really helped people start thinking out of the box. And yes, I, we knew of no one else at the time that was doing this work. So that was an added dimension of we didn't have other organizations to go visit or talk to or share stories with. And that made it very exciting but also extremely challenging.
Mark Graban: 04:36 And from that first instance you moved on to work with other healthcare organizations, you, you transitioned into doing that full time. Was there any for you to talk about some of the early successes that you could point to from there and in the early days in the 90s?
Joan Wellman: 04:52 Sure, sure. So what we did a number of, of workshops at, at Overlake hospital, but we're very, very successful in, in pharmacy and the laundry and discharge planning. And everything that we touch seem to work very, very well. About a year later, I got a call, this was in 96 from the chief operating officer at Seattle Children's Hospital, Pat Hagan, who is still at Children's today and still a client. And he was also feeling the pressure of the, the current healthcare environment and said, you know, we really need to learn about how to concurrently rather than separately, but concurrently address issues of quality, cost and process speed or process velocity. Would you come over? And because he knew of our bet, my background, would you come over and, and talk with us about this? So we actually went offsite with the hospital leadership and began to talk about how you could improve concurrently improve those three areas.
Joan Wellman: 06:05 And it, at first it was like, you know, I wouldn't say that they were hooked at the, at the first discussion of this, people were very suspicious about using a business model and had no idea of what a car company or an airplane manufacturer could have to do with healthcare. This was not at a time when people were looking outside so far, whereas that had been embraced. In one environment. It was very slow soaking process in another environment. But what we did was we just started doing point improvements. And one after another we had success in a laboratory and specimen collection in flow from the Ed to the nursing units in ancillary processes and support processes like receiving and shipping. We made steady progress. And so finally, in 2002 Pat Hagan went to the board at Seattle Children's and said, we really need to make this a strategic initiative and we need to make it our management system.
Joan Wellman: 07:20 And the way that we do improvement. So that began a much more intensive set of a much more intensive period both for us, for Seattle Children's. At the same time we, we had begun doing work with other clients and some of our clients wanted us to come in and do a project and some of our clients wanted us to come in and partner with them over a period of three, four or five years so that they could get their internal staff up and running and get the management system in place. So the clients we had and still have are somewhat across the board, but the ones that are, are really serious about this have, have really made this their their improvement system and their management system.
Mark Graban: 08:08 Yeah. Because it's a really positive progression to move from like you said in your early experiments point solutions to thinking in terms of of a complete management system that's, that's quite a step forward and it sounds like Seattle Children's was, was still in an experimental phase for a number of years before reaching that point. What do you think was the tipping point where they, they finally said, okay, yes, we know the, this needs to be kind of a a management system and an organizational view, not a a point solution approach.
Joan Wellman: 08:43 Good question. I think there were a couple of things. One was the engagement of key physician leaders in a rapid process improvement workshops. And one of them was with the Lynn Martin who is the, is still the head of anesthesiology at Seattle Children's and he saw a team implementing something in a week that would normally have taken, well, they'd been working on it for years. It was a problem with the introduction of technology into the o r so he, he became very interested early on. The second thing that happened, and there were others like him, the second thing that happened is in 2003 I had traditionally facilitated the annual retreats of the hospital leadership as a consultant to them. And I said to Pat Hagan were, if you really want to get serious about this, we're not going to a resort for the retreat. We need to go to the factory.
Joan Wellman: 09:41 And spend a couple of days trying to understand what is going on that is making that business successful and talk to people on the front line. But most of all talk to the leadership and find out what they've had to do to make this work. So we took the entire, about 20 people from Seattle Children's, about half physician leaders and half administrative leaders and spent two days deeply involved in discussions and observations at genie industries in Redmond, Washington. And I think that what happened on that trip and subsequent trips that we took to Boeing and eventually to Japan is people began to see that there are huge safety issues and there are huge complexities involved in other industries. When you're putting millions of parts together or thousands of parts together from suppliers all over the world, you've got a very, very complex operation and that it wasn't as far flung from the complexity and the safety issues that they face on a daily basis. Right. I remember standing on a overlooking the, the genie plant on one of these trips with the head of surgery from Seattle Children's. And he said, you know, Joan, there is not one thing I'm seeing going on here that I couldn't apply directly to the LR. So I think it was some of these experiences that really helped people break out of and started to see they change their vision of what was possible and began changing their definition of what good was because they saw it happening elsewhere.
Mark Graban: 11:20 Yeah. And I think that's interesting though to think of you know, like yourself. I, I started in manufacturing and you have a different context when you come into a hospital and you're right, it's probably good to remember sometimes the folks in the hospitals haven't been to a factory. A lot of times I think there's a general perception of, Oh, you know, manufacturing is simple, but you know, to go see the complexity of a Boeing factory. I'm sure it would be very eyeopening. As, as a point and you know, it makes me think of, have moved into, you know, final question about where health care has come over the 14 years or so. You've been involved in healthcare where it needs to go. This whole issue of quality and cost and speed is something that the manufacturing industry has also struggled with. And you know the automotive industry learned from Toyota that you can have high quality at lower cost and with faster speed. And, and we're, we're still trying to educate people about that today in health care. Just ready if you could reflect a bit on, you know, where you've been, where the industry has been and where things still need to go. What do you think is the future the next couple of years of the impact lean could have or should have in healthcare?
Joan Wellman: 12:44 I think, first of all, we've, we've got a lot of beachheads. We have several organizations in the u s that are really having success and have full scale lean initiatives underway. And so I think that's, that's the good news. We've passed over some of the, the hurdles of things like, you know, getting it 50% better today than waiting for perfection or thinking about improvement is episodic versus continuous. Or resistance to doing multi-day events to make a breakthroughs versus having ongoing, I call them book clubs of, you know, meeting every week and never really getting to where we want to go. So I think we have some early signs that we're, we're able to apply this and that we are not changing people's views of how they have traditionally done improvement in healthcare. So that's, that's the good news. Where I think we're going from here is that I think there's a lot of activity and leading is getting to be there.
Joan Wellman: 13:53 Very hot item in healthcare. And whenever that happens, I start getting nervous because I think that the danger that we face is that lean, we'll we'll do a lot of lean light that organizations will see this as a set of methods or tools and techniques and not as Jeffrey liker would put it, a system and not certainly not as a management system. So my prediction is that for organizations that are serious about using this as a philosophy and a management system and realize that if it's hard, this is about a cultural transformation, that their prognosis is great, they will continue to take cost out and have higher reliability and all the good things that we need to happen in, in health care. I think for those organizations who think this is a, another tool with the expertise residing primarily in the performance improvement department rather than in the executive conference room and elsewhere or on the, on the front line that that they'll move on to something else when they find that in spite of their good intentions are not getting the results that they want. And if we look at other industries that the parallel, there's a parallel here. So I think it depends on how organizations are going about the work. But I think there's a very rosy prognosis for those who are beginning to really see results from their efforts. And I'm hoping that they will continue to tell their stories so others can learn
Mark Graban: 15:34 I'm sure it must be gratifying for you. It's not quite as lonely as it must've been in the mid and late nineties. And so I, I admire the role that you played and you know, if you will, the early days of lean health care and, and, and you're still at it and still doing great work. So I want to thank you for sharing your perspectives with us. Tell us more about your consulting group:
Joan Wellman: 16:09 Our group is 100% focused on healthcare. We are training and consulting in the both the technologies of lean but also the management systems required to set priorities and manage both cross-functionally and to do daily management to sustain gains. We have very deep experience in training and coaching internal staff and managers and physicians to lead improvement events. And our bottom line is, and our success is based on whether our clients become improvement engines and are continuing to do this work 10, 15, 20 years after we have left or finished our work with them. And that's a pretty high bar, but I think it's really the only legitimate bar we have a lot of work to do in healthcare and we think that's the best way to go about it.
Mark Graban: 17:08 Well, again, I want to really thank you for taking time out from the important work you're doing to share some of your perspectives here on the podcast. I always enjoy talking with you and maybe we can do this again some time. Great. Thanks so much.
For earlier episodes, visit the main Podcast page, which includes information on how to subscribe via RSS or via Apple Podcasts.
If you have feedback on the podcast, or any questions for me or my guests, you can email me at leanpodcast@gmail.com or you can call and leave a voicemail by calling the “Lean Line” at (817) 372-5682 or contact me via Skype id “mgraban”. Please give your location and your first name. Any comments (email or voicemail) might be used in follow ups to the podcast.
What do you think? Please scroll down (or click) to post a comment. Or please share the post with your thoughts on LinkedIn – and follow me or connect with me there.
Did you like this post? Make sure you don't miss a post or podcast — Subscribe to get notified about posts via email daily or weekly.
Check out my latest book, The Mistakes That Make Us: Cultivating a Culture of Learning and Innovation:
Joan Wellman is one of the best consultants I've ever worked with. She is tireless in her pursuit of healthcare transformation using lean principles. Shine on Joan! You rock so hard!
[…] In this case, the collaboration included my friends at Joan Wellman & Associates (listen to my podcast with Joan here). […]