Scroll down for how to subscribe, transcript, and more
My guest for Episode #517 of the Lean Blog Interviews Podcast is Jacob Stoller, a journalist, speaker, facilitator, and Shingo-Prize-winning author of The Lean CEO. We talked about that in Episode 221.
His latest book, Productivity Reimagined: Shattering Performance Myths to Achieve Sustainable Growth, was just released by Wiley on October 8th, 2024.
Jacob has published hundreds of articles on technology and business management methods, and is known for demystifying complex topics for general business audiences. Jacob has delivered a variety of keynote speeches and learning events workshops in Canada, Europe, and the US, and authored reports, created training materials, and strategic corporate documents for clients such as Microsoft, Dell Computer, Staples, Pitney Bowes, International Data Corporation (IDC), CMA Canada, and the Conference Board of Canada.
In this episode, the discussion focuses on debunking common myths about productivity and exploring how sustainable growth can be achieved by improving operational efficiency without sacrificing quality. Jacob emphasizes the importance of lean thinking and continuous improvement, noting that productivity gains should come from enhancing processes, not just relying on technology or financial measures. We also highlight the critical role of people and culture in driving lasting improvements and discuss how true productivity involves creating more value with the same or fewer resources, aligning with lean principles.
Questions, Notes, and Highlights:
- What have you been up to since The Lean CEO?
- If you were to do a new edition of The Lean CEO, what would you add?
- How do you define productivity?
- What are productivity myths, and how are they affecting organizations?
- What are some examples of productivity gaps you've observed in industries like manufacturing?
- What misconceptions exist about improving productivity with lean methodologies?
- How important is the people side of lean, and how does it impact productivity?
- What strategies have you found most effective for real employee engagement?
- What are the pitfalls or misconceptions around leveraging technology for productivity gains?
- Can you share examples of companies successfully using lean thinking to improve productivity?
- What are some success stories or inspiring examples of organizations improving productivity outside traditional lean environments?
Key Topics:
- Productivity myths and misconceptions
- The relationship between productivity, quality, and resource efficiency
- The importance of the people-first approach in lean
- Challenges in sustaining lean improvements
- The role of technology and automation in productivity
- Leadership's role in driving cultural change and continuous improvement
- The evolving landscape of productivity in various sectors, including manufacturing, healthcare, and sustainability.
The podcast is brought to you by Stiles Associates, the premier executive search firm specializing in the placement of Lean Transformation executives. With a track record of success spanning over 30 years, it's been the trusted partner for the manufacturing, private equity, and healthcare sectors. Learn more.
This podcast is part of the #LeanCommunicators network.
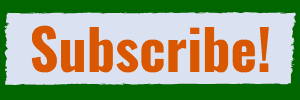
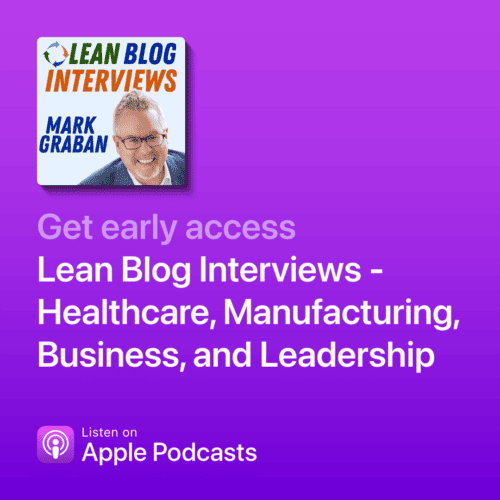
Full Video of the Episode:
Thanks for listening or watching!
This podcast is part of the Lean Communicators network — check it out!

Episode Summary
Productivity Myths and Sustainable Growth
Introduction to Jacob Stoller and His Work
Jacob Stoller is a journalist, speaker, and facilitator known for demystifying complex topics in technology and business management for general audiences. He has published hundreds of articles and delivered numerous keynote speeches globally. Stoller is a Shingo prize-winning author and recently released his new book, Productivity: Shattering Performance Myths to Achieve Sustainable Growth. His previous work, The Lean CEO, delved into how senior management approaches lean methodology within their organizations.
Understanding Productivity
Productivity is often misunderstood and misdefined. According to Stoller, renowned institutions like the Bureau of Labor Statistics define productivity as the ratio of output over inputs. True productivity growth is about achieving more output with the same or fewer resources without compromising quality. Productivity isn't merely about increasing volume; quality plays a crucial role. The International Monetary Fund (IMF) describes productivity as the foundation of prosperity, noting that raising the standard of living sustainably requires producing more with existing or fewer resources. This notion underscores that productivity improvement should enhance value without sacrificing quality.
The Importance of Lean Thinking in Productivity
Stoller's research revealed that lean thinking, typically associated with reducing waste and improving operational excellence, aligns perfectly with productivity growth. Lean thinking emphasizes continuous improvement and maximizing value from available resources. Unfortunately, macroeconomic discussions often miss the operational excellence aspect, focusing instead on broader economic factors like industry concentration and business dynamism. This gap presents an opportunity for the lean community to showcase its expertise in enhancing productivity.
The Myth of Productivity Segmentation
In large organizations, management tends to aggregate data into financial metrics, which often fails to reflect the nuances of operational productivity. Stoller refers to this as the “myth of segmented success”, where companies assume that productivity can be improved by optimizing independent components of the organization, such as departments or divisions, through key performance indicators (KPIs). However, this fragmented approach rarely leads to overall productivity improvement. Instead, lean principles advocate for a holistic view of the organization, recognizing that the sum of individual efficiencies does not necessarily equate to total organizational improvement. Dr. W. Edwards Deming, a key figure in quality management, criticized this segmented approach, emphasizing the importance of understanding the interdependencies within an organization.
Revisiting the Human Element in Productivity
Stoller emphasizes the importance of people and culture in productivity. One reason lean transformations fail is the neglect of the human aspects. Leadership changes often disrupt productivity gains because new executives may not share the same lean mindset. This underscores the need for a deep, organizational culture shift towards lean principles. By valuing employees and fostering a culture of continuous improvement, organizations can achieve sustainable productivity growth.
Productivity in the Broader Economic Context
Productivity impacts the standard of living by determining the availability and quality of essential goods and services. Economic growth should reflect improvements in living standards by ensuring access to quality products and services like nutrition, shelter, and transportation. Despite significant economic growth, not all increases in productivity translate into better living conditions. Thus, operations play a critical role in ensuring that productivity gains benefit society at large.
Challenges and Opportunities in Lean Implementation
The implementation of lean principles faces several challenges, notably the resistance to change and a lack of understanding at the executive level. Stoller notes that often, success in lean initiatives is hindered by leadership that relies too heavily on aggregated financial reports, missing the operational nuances critical for productivity improvements. Companies that fail to integrate lean thinking into their culture and operations risk backsliding into unproductive practices.
Conclusion
Jacob Stoller's insights into productivity and lean thinking offer valuable lessons for organizations seeking sustainable growth. By redefining productivity to include quality, emphasizing the human element, and recognizing the limitations of segmented success, businesses can achieve meaningful improvements. Lean thinking provides a powerful framework for these efforts, and its principles remain crucial for enhancing productivity in today's complex economic landscape.
Breaking Down the Mental Prison: Rethinking Organizational Structures
Jacob Stoller dives deep into examining the self-imposed constraints that shape organizational behavior. These structures aren't rooted in natural laws but are rather artificial constructs that influence our perceptions and actions. From childhood, we are conditioned to accept hierarchical norms, which embed deeply into our professional identities. Stoller recounts a poignant story from Rich Sheridan, who illustrated this societal expectation through his granddaughter's innocent query about his workspace aesthetics as a CEO. This highlights how entrenched these ideas can become over decades.
Financial Metrics and Productivity Myths
A significant myth in management is the reliance on the bottom line as a comprehensive indicator of success. Ori Fiume's work emphasizes the need to decouple productivity from profitability, advocating for a focus on elements within the organization's control, like operational productivity. Fiume's analyses reveal that numerous metrics critical to productivity are non-financial, often hidden within the “black box” of operations. This disconnect between financial logic and operational reality is a barrier to genuine productivity improvement.
Lean Accounting: Getting the Real Numbers
Stoller points out the nuances of lean accounting, a concept that aims to present the actual cost structures within operations. Traditional accounting methods fail to capture the iterative benefits of investments in quality and safety, which, contrary to conventional wisdom, can reduce costs. This mirrors Deming's chain reaction, where high-quality processes decrease overall expenses and enhance productivity.
The Short-Termism Challenge
Short-term thinking is prevalent in large corporations, often at the expense of long-term productivity gains. This contrasts starkly with lean principles, which emphasize sustainable growth over quarterly financial targets. As Toyota practices have shown, long-term decision-making is vital, yet many organizations still grapple with this old-world view that prioritizes immediate financial returns.
The Pitfalls of Siloed Thinking
Interviewing over 60 leaders from diverse sectors, Stoller encountered a common challenge: organizational silos. The separation of disciplines often leads to suboptimal solutions, as illustrated by Bruce Taylor's story. Taylor demonstrated that eliminating siloed approaches and adopting a holistic view led to innovative solutions such as transforming exhaust fumes into marketable solvents, thus eliminating the need for energy-intensive fans.
Lean Thinking Beyond Manufacturing
Lean principles aren't restricted to manufacturing; their applicability spans across various sectors. Stoller provides an example of an environmental engineer who utilizes lean thinking on a macro scale, tackling global issues like food waste. Despite not being officially labeled as “lean,” his methodologies exemplify lean principles by targeting waste reduction at its source.
Engaging Non-Lean Thinkers
Interestingly, Stoller's interviews also encompassed practitioners outside the traditional lean community, such as those in environmental engineering. These professionals, though not identifying as lean thinkers, inherently apply lean principles in their quest to create sustainable solutions. Their projects often succeed due to a lean-like focus on eliminating waste rather than pursuing superficial green initiatives.
Sustaining Excellence: Lessons from the Shingo Prize
The Shingo Institute discovered a troubling trend: many Shingo Prize-winning organizations could not maintain their excellence over time. This is attributed to a failure in embedding the principles deeply within their organizational culture. True lean transformation requires an enduring commitment to people and processes, ensuring that productivity gains are not only achieved but also sustained.
Final Thoughts on Lean Implementation
Jacob Stoller's exploration of productivity myths unearths profound insights into the intersection of financial metrics and operational realities. By debunking conventional wisdom and promoting a people-first approach, he provides a compelling roadmap for achieving sustainable productivity improvements. Bridging the gap between traditional financial logic and operational excellence is key to unlocking long-term organizational growth.
I hope this expands on the topics and themes already mentioned, integrating the points from the transcription seamlessly. Let me know if there's any specific direction or additional content you'd like to explore further!
Practical Steps for People-First Lean Implementation
Revamping the Shingo principles to emphasize a people-first approach has been a groundbreaking move. It underscores the importance of building trust and fostering a culture where improvements are more than just technical tweaks–they involve comprehensive engagement with people at all levels. Before diving into lean methodologies, it's crucial to cultivate an atmosphere of mutual respect and open communication.
Building Trust and Culture
The journey toward lean transformation should start with creating a trusted environment. This involves:
- Encouraging transparent communication across all tiers.
- Establishing forums for employees to voice concerns and suggestions.
- Initiating team-building activities to break down hierarchical barriers.
As Stoller suggests, engagement isn't just about making people feel heard; it's about actively involving them in the decision-making process. Organizations need to be prepared to support managers and employees alike through this cultural shift.
Effective Leadership and Unlearning
Implementing a people-first strategy also demands a transformation in leadership. Leaders must not only learn new skills but also unlearn traditional management practices that emphasize control over collaboration. This unlearning process can be tough, as it challenges long-held beliefs and practices ingrained since early education and professional training.
- Compassionate Leadership: Managers should approach unlearning with empathy, recognizing the challenge it poses.
- Support Systems: Providing resources such as coaching and mentoring can help leaders transition into their new roles smoothly.
Role of Technology in Lean Transformation
While technology holds immense potential for improving productivity, it's not a panacea. Companies like Toyota emphasize that technology should serve to enhance processes, not replace human agency. The integration of collaborative robots (cobots) showcases a shift towards technology that works alongside employees, not independently of them.
Practical Approach to Technology Implementation
To make the most out of technological advancements:
- Assess the Necessity: Before resorting to automation, evaluate if the process can be improved without it.
- Collaborative Robots: Cobots are increasingly used in manufacturing settings for their flexibility and ability to work with humans.
- Internet of Things (IoT): Using sensors and AI, companies can gain detailed insights into processes, leading to predictive maintenance and enhanced decision-making.
It's essential, however, to involve people in these technological transitions to ensure they are stakeholders in the change rather than passive recipients.
Case Study: Parker Hannafin's Technology Justification
A notable example is Parker Hannafin, where the deployment of robots undergoes strict justification processes. Proposed technological implementations must demonstrate improvement over manual processes. This approach not only saves costs but also ensures that technology becomes a tool for genuine enhancement, not an unnecessary complexity.
Inspiring Examples of Lean and People-Centric Practices
Several companies have successfully combined lean principles with a people-first approach:
- OC Tanner: This organization stresses the importance of engaging everyone in improvements, setting an example of people-driven lean transformation.
- Anti-Poverty Initiatives: By focusing on giving individuals the agency to create small enterprises, significant strides are made in eradicating poverty using lean-like thinking, even outside traditional manufacturing sectors.
- Kerry Siggins' Ownership Mindset: Emphasizing employee ownership, this approach ensures that workers are not just participants but co-owners of the organization, aligning their interests directly with organizational success.
Younger CEOs: A New Perspective
Interestingly, younger CEOs are leading the way in revising conventional management paradigms. Their focus on finding purpose in work and fostering a more inclusive and flexible environment is reshaping how productivity and engagement are perceived. Their management style often aligns with lean principles, even if they don't explicitly use lean terminology.
Empathy and System Thinking
Emphasizing Dr. Deming's principles, it's essential to recognize that leaders are also part of a system that requires understanding and empathy. Reengineering management roles involves honoring the legitimacy of past experiences while encouraging a shift towards a more collaborative and inclusive mindset.
In conclusion, reshaping organizational structures to prioritize people, integrating flexible and supportive technology, and understanding the need for compassionate leadership and systemic thinking are crucial for sustainable lean transformation. This comprehensive approach not only paves the way for operational excellence but also fosters a workplace culture where employees feel valued and engaged.
Expanding the Lean Tent
Mark Graban and Jacob Stoller highlight a crucial point: the lean community has historically focused on manufacturing and industrial sectors, but its principles can be applied more broadly. This expansion of lean principles to various sectors offers an opportunity to leverage unique talents to enhance productivity across the economy. This widened perspective embraces a holistic view of lean, one that can be integrated into education, healthcare, startups, and even government operations.
Productivity in Context
It's important to understand that productivity is not an isolated metric but a culmination of various factors: Safety, Quality, Delivery, and Cost (SQDC). This interconnection means improvements in these areas will naturally lead to better productivity. Emphasizing one without considering the others can yield subpar results and lead to inefficiencies.
- Safety: A safe work environment reduces downtime and fosters a culture where employees feel valued.
- Quality: Consistent quality enhances customer satisfaction and reduces waste.
- Delivery: Timely delivery builds customer trust and streamlines operations.
- Cost: Reducing unnecessary expenses allows reinvestment into more productive initiatives.
Integration of Lean in Broader Sectors
Healthcare
Lean principles have proven effective in healthcare by streamlining processes, reducing wait times, and improving patient outcomes. For instance, Virginia Mason Medical Center in Seattle adopted lean to create patient-centered care, significantly cutting down waste and enhancing quality.
Education
Educational institutions like San Diego State University have adopted lean methodologies to improve administrative processes and classroom management. This results in better resource allocation and enhanced student experiences.
Startups and Small Businesses
Lean isn't just for large corporations. Startups and small businesses can benefit by implementing lean startup methodologies, which encourage validated learning, iterative product releases, and measuring progress through actionable metrics.
Reimagining Productivity
Jacob Stoller's insights in his new book, Productivity Reimagined: Shattering Performance Myths to Achieve Sustainable Growth, challenge traditional notions about productivity. The book argues that true productivity comes from a systemic and holistic approach, rather than quick fixes or short-term gains.
- Lean CEO: This book remains a staple in many executive reading lists, providing a blueprint for integrating lean into core business strategies. Its influence continues as new leaders find value in its principles.
Leveraging Leadership
The role of leadership in lean transformation can't be overstated. Effective leaders must act as facilitators rather than authoritarian figures. They need to cultivate an environment where continuous improvement is part of the organizational DNA.
- Encouraging Innovation: Leaders should create safe spaces for experimentation, where failures are seen as learning opportunities.
- Building Skills: Continuous learning and development opportunities for employees ensure that the workforce remains adaptable and innovative.
- Empowering Teams: Providing teams with the autonomy to make decisions fosters ownership and accountability.
A Collaborative Future
Incorporating lean principles across various sectors requires a collaborative effort. As Mark Graban notes, it's not just about making isolated improvements but crafting a coherent strategy that interlinks all facets of productivity.
Community and Knowledge Sharing
Building a community of practice where different sectors share their lean experiences can drive innovation. Forums, seminars, and collaborative projects can help spread lean thinking and practices beyond traditional boundaries.
Technological Integration
The marriage of lean principles with advanced technologies like AI, IoT, and machine learning offers new avenues for productivity. These technologies can provide real-time data and insights, helping organizations make informed decisions quickly.
Conclusion
As we continue to apply lean principles to diverse sectors, it becomes evident that the core of lean–respect for people, continuous improvement, and a holistic view of productivity–resonates universally. Expanding the lean tent to include various industries and leveraging modern technologies ensures that organizations not only survive but thrive in today's dynamic and competitive landscape.
By cultivating a culture that values safety, quality, delivery, and cost, leaders can craft strategies that are not just efficient but also sustainable. Ultimately, this collective effort will drive a more productive and engaged economy, benefiting everyone involved.
Automated Transcript (Not Guaranteed to be Defect Free)
Here is the full transcript, cleaned up for clarity and flow, while maintaining the original content:
Mark Graban:
Hi, welcome back to Lean Blog Interviews. I'm your host, Mark Graban, and today we are joined by Jacob Stoller. He's a returning guest–he was with us on episode 221, back in 2015. Jacob is the author of a new book just released, titled Productivity Reimagined: Shattering Performance Myths to Achieve Sustainable Growth. Jacob is a journalist, speaker, facilitator, and a Shingo Prize-winning author of The Lean CEO, which was the topic of our last episode. You can find that episode at leanblog.org/221. Jacob has published hundreds of articles on technology and business management methods. He's known for demystifying complex topics for general business audiences and has delivered a variety of keynote speeches, learning events, and workshops across Canada, Europe, and the US. His clients have included Microsoft, Dell, Staples, and more. Jacob, welcome back to the podcast!
Jacob Stoller:
Thank you, Mark, glad to be here.
Mark Graban:
It's good to see you again! You were also part of a webinar in the Kinexis series a few years ago, which I remember well. Congrats on the release of your new book. I noticed it was endorsed by several people, including some past guests of this podcast and my My Favorite Mistake podcast–like John Shook, Michael Ballé, Kerry Siggins, and Rich Sheridan. A lot of great endorsements! So, what have you been up to since The Lean CEO?
Jacob Stoller:
I've continued writing and talking to people, and as you remember, The Lean CEO was a study to understand senior management's perspective on Lean–what goes on in the boardroom and what CEOs are telling shareholders and the press. I concluded that there wasn't a single playbook for Lean CEOs; they had many different approaches. Since then, I've discovered a lot of people displaying what I'd call “Lean-like thinking” in areas like technology, anti-poverty initiatives, and sustainability projects. The common thread is productivity–doing more with the resources available.
Mark Graban:
You've talked with so many CEOs and Lean leaders. If you were to do a new edition of The Lean CEO, are there any lessons or updates you'd include?
Jacob Stoller:
I think I'd dig deeper into the people side of Lean because I've learned more about the importance of people and culture. Some case studies from the book have changed over time, often due to leadership changes, which is disappointing, but the overall lessons still hold up.
Mark Graban:
I completely understand! I've felt the same way about all three editions of my Lean Hospitals book. Changes in leadership often disrupt continuity in Lean efforts. Let's talk about the new book. Productivity is a word we hear a lot, but there are different definitions in people's minds. How do you define productivity?
Jacob Stoller:
Productivity, at its core, is output over input. Productivity growth is what we really want–getting more output with the same inputs. It's important to emphasize that improving productivity also means maintaining or improving quality. For example, making more ballpoint pens but with lower quality is not true productivity. Real productivity growth means increasing value with the same or fewer resources.
Mark Graban:
That makes sense. I was curious about your thoughts on how productivity influences societal factors like the standard of living.
Jacob Stoller:
Absolutely. Productivity growth is critical for improving the standard of living. It's not just about financial growth; it's about having better and more accessible services and products–food, shelter, transportation, and entertainment. When these things aren't readily available, people feel worse off, regardless of GDP growth.
Mark Graban:
That's a great point. I remember when I was working at General Motors, we were measured on things like hours per engine. But when poor quality was produced, those metrics didn't capture the real story. It's not just about cranking out more; it's about good quality output.
Jacob Stoller:
Exactly. Too often, companies focus on aggregate financials without really understanding what's happening on the ground level. That's one of the myths I discuss in the book: the myth that financial metrics alone tell you everything you need to know about operations. They don't.
Mark Graban:
One of the things you discuss in the book is productivity myths. What are some of the biggest myths you've encountered?
Jacob Stoller:
One major myth is that the bottom line tells you everything about how well an organization is doing. People think that financial metrics are enough, but many of the indicators of true productivity–like quality or operational improvements–are non-financial. Another myth is that technology alone will drive productivity improvements. The reality is, technology can't fix broken processes. You need strong process thinking to make technology work for you.
Mark Graban:
I've seen that a lot in healthcare, where automation is implemented without improving the underlying processes first. It can lead to even worse outcomes. What are some misconceptions companies have about using Lean to improve productivity?
Jacob Stoller:
One of the biggest misconceptions is underestimating the people side of Lean. Many companies jump into tools and processes without first building a culture of trust and engagement. Without that foundation, Lean efforts are unlikely to be sustainable.
Mark Graban:
Speaking of engagement, what strategies have you found most effective for fostering real employee engagement, not just making people feel like they're involved?
Jacob Stoller:
Leadership needs to be truly committed to changing the role of managers. It's not just about learning new leadership skills–it's about unlearning old habits. Managers have been taught that their knowledge and authority make them leaders, but in Lean, leadership is about listening and supporting your team. Helping managers feel safe during this transition is key.
Mark Graban:
That's such a tough shift. I've struggled with reminding myself that ineffective leaders often operate within systems they've been part of for decades. How do you see technology fitting into the productivity equation, especially as companies rush to adopt AI and automation?
Jacob Stoller:
Technology can be incredibly helpful, but it shouldn't be seen as the be-all, end-all solution. It needs to support processes, not replace them. For example, collaborative robots, or cobots, that work alongside people are a growing area because they provide flexibility without replacing human problem-solving. But before automating, companies should always ask: Can we improve this process without technology first?
Mark Graban:
I love that example. If automation doesn't solve the root problem, it just automates waste. Are there any companies or sectors that you've found particularly inspiring in how they're approaching productivity?
Jacob Stoller:
Yes, some younger CEOs are approaching things differently. They talk about purpose and agency in ways that align with Lean principles, even if they don't use that terminology. I'm also inspired by non-traditional Lean thinkers, like environmental engineers working on sustainability projects. They're applying Lean thinking to eliminate waste on a massive scale, like reducing food waste, which has a significant impact on the carbon footprint.
Mark Graban:
That's fascinating. Are there misconceptions or myths you see in Lean-focused organizations when it comes to improving productivity?
Jacob Stoller:
Yes, one is that many organizations think they can just throw Lean tools at a problem without addressing the people and culture first. The Shingo Institute found this out the hard way when they realized that many of their Shingo Prize-winning companies weren't sustaining their improvements. They revamped their principles to focus much more on people and culture, which is essential for long-term success.
Mark Graban:
That's a strong point to end on–people first, always. Thanks for joining us again on the podcast, Jacob. Be sure to check out Jacob's new book, Productivity Reimagined, and his previous work, The Lean CEO.
Please scroll down (or click) to post a comment. Connect with me on LinkedIn.
Let’s build a culture of continuous improvement and psychological safety—together. If you're a leader aiming for lasting change (not just more projects), I help organizations:
- Engage people at all levels in sustainable improvement
- Shift from fear of mistakes to learning from them
- Apply Lean thinking in practical, people-centered ways
Interested in coaching or a keynote talk? Let’s talk.
Join me for a Lean Healthcare Accelerator Trip to Japan! Learn More
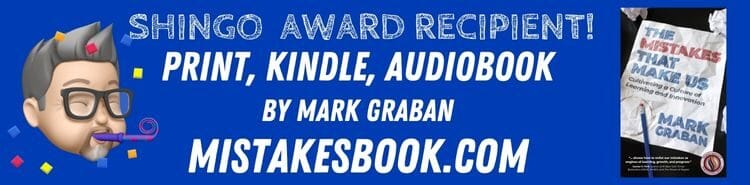