Scroll down for how to subscribe, transcript, and more
My guest for Episode #450 of the Lean Blog Interviews Podcast is Professor Torbjorn Netland, Ph.D.
Tor is the chair of production and operations management in the department of management, technology and economics at ETH Zurich in Switzerland.
He is a member of the World Economic Forum's Global Future Council on Advanced Manufacturing and Value Chains and a Fellow of the European Academy for Industrial Management.
His award-winning research on managing performance improvement appears in leading scientific journals such as Management Science, MIT Sloan Management Review, Journal of Operations Management, and more.
Tor is a recognized thought-leader in operational excellence (including lean) and is the recipient of two Shingo Research Awards and numerous teaching awards.
His blogs at www.better-operations.com.
Like my recent guest, Dr. Lisa Yerian (ep 449), Tor is going to be one of the keynote speakers at the 2022 AME Conference, being held in Dallas — Oct 17 to 20. I'll be there and I hope you will be too.
Today, we discuss topics and questions including:
- Tor, what is the topic of your keynote talk on the AME theme of “Embrace Disruption”?
- Tell us your thoughts on the role of new technologies in Lean?
- Not just emulating Toyota of the 1960s
- Lessons learned about bringing new ideas to people?
- The dream of the lights-out factory has been haunting us for a while now – GM CEO Roger Smith in the 1980s and in more recent years Elon Musk at Tesla… is that still a dream? Is it a dystopian nightmare? Or something in between?
- How did you first get interested in Lean and Operational Excellence?
- Dogma vs practical realities – Buffers? Inspection?
- Last year, you blogged about the confusion around “what is Lean?” How do you define Lean and what's the most common confusion?
- Different views of researchers?
- How do you describe the role of company-specific production systems?
- Difference in having YOUR production system vs. just a name?
- “If you like heated debates, start a discussion thread on the definition of lean on LinkedIn.”
- Another heated debate — Lean is not TPS? Goes beyond TPS?
- Tell us why it's wrong to blame JIT for pandemic-era supply chain problems…
- You have a textbook, written with Michel Baudin, coming out — tell us about that?
The podcast is sponsored by Stiles Associates, now in their 30th year of business. They are the go-to Lean recruiting firm serving the manufacturing, private equity, and healthcare industries. Learn more.
This podcast is part of the #LeanCommunicators network.
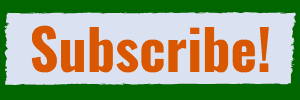
Video of the Episode:
Thanks for listening or watching!
This podcast is part of the Lean Communicators network — check it out!

Automated Transcript (Not Guaranteed to be Defect Free)
Announcer (2s):
Welcome to the lean blog podcast. Visit our website www.leanblog.org. Now here's your host Mark Graban.
Mark Graban (13s):
Hi, it's Mark Graban here. Welcome to episode 450 of the podcast. It's July 13th, 2022. My guest today joining us from Switzerland is Professor Tor Netland. You're going to learn more about him in a minute, but for links to his blog and articles, he's written more information about him and the AME annual conference 2022. Look for links in the show notes, or you can go to leanblog.org/450 as always. Thanks for listening. Well hi everybody welcome back to the podcast. My guest today is professor Torbjorn Netland. He is the chair of production and operations management and the department of management technology and economics at ETH Zurich in Switzerland.
Mark Graban (59s):
He is member of the World Economic Forum's global future council on advanced manufacturing and value chains. And he's a fellow of the European Academy for Industrial Management Tors. Award-winning research on managing performance improvement has appeared in leading scientific journals, including just to name a few Management Science, MIT Sloan Management Review, and the journal of operations management Tor is a recognized thought leader in operational excellence and methods, including lean. He is the recipient of two Shingo research awards and numerous teaching awards. So you can find his blog and I'll link to this in the show notes, www.better-operations.com.
Mark Graban (1m 41s):
So Tor, welcome to the podcast. How are you today?
Torbjorn Netland, PhD (1m 44s):
Thanks Mark. It's great honor. To be invited by you to speak with you today about lean and whatever else you have in mind.
Mark Graban (1m 52s):
Yeah, exactly. We'll talk about lean and whatever else, mostly lean, but I think there's a lot of interesting manufacturing topics to discuss. And before we get into that, I just want to mention that Tor, like another recent guest, Dr. Lisa Yerian who joined me again in episode 449 Tor is going to be one of the keynote speakers at the upcoming AME annual conference. It's being held in Dallas, October 17th to 20th. So I hope to see you there I'll be there. Tor will be there on stage you're you're speaking in person, right?
Torbjorn Netland, PhD (2m 25s):
That's true. I look forward to go to Dallas, never been there before, meet the community. Sure.
Mark Graban (2m 31s):
Yeah, because, and part of why I asked her to just confirm that it's, it's a bit of a hybrid event. There'll be a lot of people there in person and some speakers are appearing virtually. So I'm glad you'll be able to make the trip from, from Zurich. So you can learn more about the conference ame.org, or you can look for a link in the show notes. So, you know, the theme for the event this year is embrace disruption. So a Tor, maybe, maybe my first question for you is to share a little bit about the topic, the themes of your keynote talk and how it fits into the idea of embrace disruption.
Torbjorn Netland, PhD (3m 6s):
I thought that we'll talk a little bit about the role of new technologists in lean transformation, which is maybe shaking up a little bit, the lean community, at least all those pen and papers, a pen and paper consultants, and a lot of us out there we've gone to try to see if there is a role for technology in lean. And, and clearly there is. And, and then gave me a few examples of where technologies can help us close the gap and increase productivity beyond what lean can do alone.
Mark Graban (3m 37s):
Yeah. And, and, and you're right. That will discussion of that will fire the neurons of, you know, people in the audience in different ways. There are some, I'm trying to think of old guard. I don't know if that I, up there, I said it, you know, there, there are some who really hold to the idea. I think, as you alluded to that, oh, you must do everything with paper and pencil, whether that's an, a three or a Kaizen card for documenting an improvement or a value stream map or, or things like that. But, you know, th you know, let's say Jeffrey likers book, the Toyota way he emphasizes how Toyota doesn't completely shy away from technology.
Mark Graban (4m 21s):
Maybe they just don't take it to an extreme of using technology for technology's sake. Do you, do you think that's fair to say
Torbjorn Netland, PhD (4m 28s):
That's, that's exactly what it is. If you look at Toyota, all these tools that we're worshiping the lean community are really nothing else than tools. They can be replaced with other tools. It's, it's the thing we're trying to achieve that matters, right? Which is increased productivity, better work environment, customers that are happier with our products and want to buy more. So I I'm trying to stay on outcome focused transformation rather than the tools and practices. And then suddenly technology can actually do things we could never do with pen and paper. So we should be having an open eye for these things, I believe.
Mark Graban (5m 9s):
Yeah. I mean, I think one simple example that, that I even saw over 20 years ago would be the idea of taking a simple Kanban card, right? So maybe in its origin piece of paper, maybe it's laminated, maybe it has some plastic technology to help protect the card, but, you know, traditionally that Kanban card or container might physically travel back to a supplier as the signal. But even, you know, 20 years ago, we saw companies using using fax, which seems like an outdated technology now, or internet technologies to, to communicate. What, what, what seems important is that, that information that you're sending to the supplier, not how you do it, right?
Torbjorn Netland, PhD (5m 51s):
Absolutely. No, you come by and we had in the 90s you're right. Then we have to look at this thing. So when people were skeptical towards the new digital technologies, just asking them if they use email,
Mark Graban (6m 4s):
So some of them might say, no,
Torbjorn Netland, PhD (6m 8s):
Sure. Maybe
Mark Graban (6m 9s):
Those people do.
Torbjorn Netland, PhD (6m 11s):
Yeah. So, and that's a bubble, of course, we're going to start to give a few, I'm going to start to give a few more practical examples as well. It's not just about the assured technologies can help. Hopefully I get into one of the examples or plan to talk about is quality management. You know, for years, we've used polka Yorkers to try to avoid mistakes happening. Still mistakes happen 400 years. We use statistical process control, still taught widely in schools, completely outdated in some sense, at least in some type of manufacturing environments, but it's still the go-to tool for many lean consultants and, and practitioners.
Torbjorn Netland, PhD (6m 51s):
And here, for example, the latest machine learning algorithms can, can do wonders if they're applied correctly to systems where data exists in a form that can be used. So, I mean, I'm not saying it's easy, whether it is possible to do things better than it was a hundred years ago.
Mark Graban (7m 7s):
Yeah. Or even better than 10 years ago in a lot of cases. And I I'd love to hear more if you can kind of elaborate on this idea of, you know, in, in some cases, is there something better than SPC for, let's say, looking at manufacturing dimensions on some sort of part that you're cutting. This is what I was involved in. You know, over 25 years ago, you, you have specifications, you have a center line target, and you're monitoring the SPC chart to decide when you might shut down a process to investigate. Not because it's gone out of spec, but you see some sort of signal that says, okay, that, that whole it's getting to be too small.
Mark Graban (7m 49s):
The variation is too high. Let let's stop and adjust. Can you talk about how AI or machine learning might monitor a process in a way that's better?
Torbjorn Netland, PhD (7m 58s):
So SPC works in many of these environments, it's a tool that is still not used enough if you'd like, but in manufacturing environments where one para meter setting can affect another one, which you may probably have in the, in the tooling industry. And, you know, you, you change a tool to another one and suddenly the heat and friction between the tool changes as well. I mean, there are dependencies. So as long as you only use SPC and you're focusing on one-on-one variable, you may improve that. You may optimize the process for a variable that overall hurts the system, the industry where we've been working in this is extreme in that regards, the semiconductor industry.
Torbjorn Netland, PhD (8m 44s):
It's one way you actually would not necessarily like to go into with an SPC tool in the first place, because there's so many variables that affect the outcome of, of, of the process. And maybe the one, the most difficult things there is that you don't really learn the outcome of the process before it's gone through two to three, 400 processes that may be different than a, in a tool shop where you, after you grinded it, mailed it, you can actually inspect the product and see is it within specs in electronics, manufacturing, and semiconductor in particular, this is much harder because the, the, the, the parts and they affect each other, and maybe you need to do this process before you can test it and so on. And then suddenly you will have more complex production systems with many variables that effect each others, then SPC is which basically just picks up one-on-one variable.
Torbjorn Netland, PhD (9m 34s):
It's not bad. It's better than nothing, but it, it doesn't, it doesn't really solve the problem. So with machine learning, you just throw all of these things into a neural network, as long as you have a outcome variable, that makes sense in semiconductor industry it's yield, right? So number of defects produce a good products to the facts. And then you just look at all the parameters you have in your production process. And, and the algorithm can provide advice to the engineer or operated where the likely mistakes are happening. What we should change impossible with SPC, unless you have a lot of, this is just one example. And of course, in a very high tech industry, which is mature, which have a lot of data, highly automated.
Torbjorn Netland, PhD (10m 19s):
And then as we move towards the less automated more manual assembly work and this type of things well, it's in within this fan and we will try to figure out what technology works best. So I'm not saying it's always machine learning. No SPC is a wonderful tool in the right circumstances, but it's not all that there is.
Mark Graban (10m 40s):
Yeah. So yeah, when I, when I hear about these new technologies, I personally feel a little bit disruptive… Disrupted. There are times when I'm disruptive, but here I feel disrupted because I feel like I understand SPC. I know how and where to apply it. And so, you know, it's, it's, it's a little bit frightening to learn about some of the, or to, to think, how do we learn about these new technologies? How do we bring them in, into our organization in a way that's not too scary or not too threatening for people? Like, what do, I'd be curious if you can kind of share an example, whether that's what the company in Europe, or, you know, just even broader question of like, you know, introducing new what methods, whether it's lean methods or whether it's technologies, what are some things you've learned about introducing new things to people
Torbjorn Netland, PhD (11m 30s):
The first admire your reaction? I mean, you open you say, I don't know all the thing about this. I need to learn more or, you know, you get frightened. Your, my lean foundation is shaking a little bit and that's that's of course that's the right reaction because then, okay, I'm open to try to figure out what can this be? First realization, nobody in the world knows everything. You need to improve manufacturing today. There's not one single person who knows everything about machine learning, 3d printing IOT, and all of these things. So first utilization is, and we need to work together, right? We need to be a team. We need to listen to each other, need to be open for ideas. We need to work with other type of companies, startups, maybe universities take in students.
Torbjorn Netland, PhD (12m 17s):
And, and, and here's the advantage for lean companies. They are, they have this attitude, right? The okay. We want to learn. We want to improve. We're open for not being the best. And that was my experience visiting companies in Japan. Well, I, back in that time, I was only a student. I came to the factory and there's like 20 senior managers lined up in front of the factory to miss a visit or to welcome a student from, you know, what, I never had that in the U S in, in Scandinavia and Europe, nowhere, but they have this attitude of, Hmm. Maybe we can learn something today. Okay. I guess your question was more what's what's how, how do we start to engage with this new technologies?
Torbjorn Netland, PhD (13m 2s):
How do we overcome the resistance?
Mark Graban (13m 4s):
Yeah. Or, you know, w what have you learned about introducing? I mean, you know, as a professor, you're, you're introducing new concepts to people all the time, you know, maybe it's, you know, students have this expectation of I'm a student I'm here to learn. You, you, you raise, I think an instrument point of, you know, sometimes people who are further along in their career don't have that same learning mindset or growth mindset to say, well, I've learned it, I've been doing it. I know things. So I, I, there's a couple of different ways of framing the question maybe, but, you know, as, as somebody who introduces new concepts to people, what are some things you've learned about how to do that? Most effectively,
Torbjorn Netland, PhD (13m 46s):
My, in my experience, first of all, it's worth listening to those have done these things forever. You need them, that's going, gonna continue to do this as a, I take my strategy to this from a Mudi Mura Muda… From classically. Why do I say that when I was working with Volvo back in the days, studying how they tried to just employ kind of deploy, to say, I'll do a lean transformation. You have the same issue. I mean, they can be technology, but can also be a soft technology, like lean new processes, new ways of doing things it's frightening anyway, right? You need to change a little bit.
Torbjorn Netland, PhD (14m 26s):
And the best way to go about that is to start with a reducing overload for those who are supposed to do this right. Mudi. And, and that basically mean helping the operator. The first thing you should do is to make sure you introduce technology or lean principles and practices that actually makes life easier on the shop floor. That's the best way. Then you'll win them and you can move on pure companies, get this, and they start with waste, right. Start with Muda. Okay. Let's reduce waste. Let's take away this time, thieves way with that coffee break, you lost them immediately. It's, it's, it's, it's from one of the learning from the wall.
Torbjorn Netland, PhD (15m 6s):
When I think of the effect, it's exactly the same for new technologies need to look at for technologists that augment and help the operators succeed in their jobs, rather than just saying let's automate them away. So I think that's, that's my answer to that one classic Mudi Mura Muda.
Mark Graban (15m 23s):
Yeah. And like you said, make sure you're being helpful, throwing a solution at people that doesn't address something that they think is a problem. People will ignore that solution. If we don't get agreement that there's a problem. Or even if they would say, there's not a problem. If we can make people's work easier, less frustrating that at least helps, you know, people are complicated. We could say rationally. Yeah. I know that new way of doing it is better, but I'm comfortable doing it the old way. Right. So we still have to work people through it. But I agree with you, like making sure that there's benefit to people is, is absolutely necessary.
Torbjorn Netland, PhD (16m 4s):
Yeah, I agree. And there are still many, you know, we call dull, dirty and dangerous jobs in manufacturing and automating these jobs or Samuel automating these jobs. So it's get less of this and more of all the jobs that is also a good place to start. So there's plenty of opportunity for new technology, which lean canceled everything. It's right. This space for many types of solutions. Yes.
Mark Graban (16m 31s):
So on, on the topic of automation, I wanted to ask you your, your thoughts and, and, you know, instead of looking at replacing a tool or making incremental change, sometimes people have this vision of mine call it total automation, or, you know, back to the 1980s, Roger Smith famously was the CEO of General Motors. And he had this vision of a lights out factory. And, you know, they spent billions and billions of dollars pursuing this vision. That just didn't really go very far. And in more recent years, Elon Musk, as CEO of Tesla has pursued, you know, the similar idea of, you know, the machine that builds the machine.
Mark Graban (17m 14s):
And so I think is how they called it. So, you know, this, this, this dream of a lights out factory, is that still a dream? Is it a nightmare? Is it somewhere in between?
Torbjorn Netland, PhD (17m 25s):
It's still a dream. It's still a dream. It's a wet dream, even bore some people and some people, I mean, engineers and we have to of course give them engineers respect. They're the guys who build this world in many, many, many ways, right? At least the things we use and that, that the vision is still very much alive. And in itself, I don't have a problem with the vision. I mean, if we can make technology work for, for humans, make things we need is a good vision. Of course, there's a very strong capitalistic motive motive there as well. If you can make a factory that just produce things and solid, it's a wonderful thing. So it's also a wet dream for many, for many business people.
Torbjorn Netland, PhD (18m 8s):
And now of course, reality hits in when you try to do this things, and then suddenly modern nature has its requirements, physics, acids requirement. Then most importantly, human behaviors, markets, disruptions, all of these things just makes it very, very difficult. And it's not new. I mean, I think the book one book called automation or was published in 1950, it was about how the factories will be fully automated within a few years, coaches a few years later, of course, we also got the computer integrated manufacturing revolution in the seventies and eighties, lots of good thoughts stay in vision.
Torbjorn Netland, PhD (18m 50s):
And you mind, you mentioned the General Motors story with robots started to painting all the robots and wiling the door shots. It's not easy, right? You need such a control, which is almost out of the world and maybe, maybe not necessary. What I'd say is the vision is still alive. And I don't think it is a bad vision to have, but expecting that it will be just around the corner. Maybe now it's probably for someone who hasn't studied history. So I would say at least towards that vision, let's rather see how we can augment humans to do work better.
Torbjorn Netland, PhD (19m 35s):
And then at the end of the day, if we can automate some of these tasks that that may actually be progress for the world.
Mark Graban (19m 43s):
Yeah. And you know, there there's a difference. I mean, you know, general motors have this long history of a combative relationship with its workforce and the, in the union, you know, when I was working there in the mid 90s, you could definitely sense that you were part of, you know, kind of the, the aftermath, you know, that, that wasn't history, that was still very much the case. And, you know, it seemed like the mindset of general motors was one of looking at well, you know, people are a problem. So let's try to get rid of them, which is different than the Toyota mindset that you've mentioned of. Well, if a job is dangerous, unsafe, boring, too repetitive, or if it could be done better by a robot, let's automate it.
Torbjorn Netland, PhD (20m 25s):
Sure.
Mark Graban (20m 26s):
As opposed to, you know, just, I, I don't know, Elon Musk's mindset. I think he's a technologist who falls in love with technology, but, you know, as he commented publicly after they struggled, you know, automating some things that maybe were a bit of an overreach, you know, he famously said he learned people are, people are underrated. Yes. There are some jobs people still can do better.
Torbjorn Netland, PhD (20m 52s):
No, this is true. It's because, so I said, accessive automation was a mistake. My mistake. Cause I'm in, in the, in that famous tweet. But of course its factories are still quite automated. And also when they open new factories, now they do, they do seek out automation where it's possible. So it just, maybe he went too far and this it's not just Tesla. It's also, the other car manufacturers are worse at Mercedez in Stuttgart and they had the same. They had even for the final assembly, of course, assembling seats in these things is a very difficult thing, which humans still do. And they had the robots for that. But then suddenly markets demands, changes, more variation, more different types of products, perhaps on the same line.
Torbjorn Netland, PhD (21m 37s):
And then they realized this for a while, human is the most flexible cost efficient trouble. There is on the world kind of. So, so they changed it this well back and forth, but the every time maybe it's two steps ahead than once that back. Yeah.
Mark Graban (21m 53s):
Well we, we, we learn and adjust hopefully, so that there's evidence to that. You know, so Tori, I want to step back a little bit. This is a question I like to ask my guests and I often do it at the beginning of the podcast, but I'll go ahead and throw the question in here. Like what, what sparks your interest in topics like lean and operational excellence?
Torbjorn Netland, PhD (22m 14s):
It's a good quite, let me maybe answer that question with how I got to start to study and do research on, on, on lean and lean programs. I was working with a worldwide era at that point in time. Today's part of GKN, British multinational, the producing part for engines, aerospace aircraft engines. I was visiting this factory, working with them on a project and suddenly kind of the door went up and it was the pallet was just pulled into the factory full of books. And then the book, it said mobile production system. That was the delivery from the headquarters in Sweden. And they, and the message that came with the pallet of books was clear, go implement.
Torbjorn Netland, PhD (23m 0s):
Here you are. Here's our system. Good luck. And that was of course an interesting observation and obviously also not how, how you should do it, but it, it sparked my interest for these things. Having already worked in manufacturing and research for some years at that point in time, I found that to be particularly interesting.
Mark Graban (23m 23s):
And so then how did you decide to pursue this then, you know, more deeply as a research focus as a career focus?
Torbjorn Netland, PhD (23m 32s):
So of course, what I observed was what I have later kind of learned to call it a phenomenon. I mean, it's an observation is that there's something that is happening here. Okay. There's this a lean transformation under the label of Volvo production system, something I call the company specific production systems on the something that most many companies have, even as you, you would know for sure, hospitals with Virginia Mason production system and all this variance for production system. And so they started to study this phenomenon off and basically with two, two angles first, does this make sense? It means, it means does it improve operational performance?
Torbjorn Netland, PhD (24m 14s):
And second, if it does, how do you do it most efficiently? So you actually can achieve those performance benefits as fast as possible. The answer to the first question is, yes, it does improve operational performance. If you do a dry right. Particularly in the industry that I studied, which was automobile industry. And yeah, basically then how do you study? This is the next question for a researcher. And what I knew is that I can't sit in my office and this was back in the days it was in Trondheim, Norway. I can't just sit there in an office and try to figure this thing out. You need to go invest it. So I started to travel together with my, with a mentor from Georgetown university in Washington, DC.
Torbjorn Netland, PhD (24m 55s):
I started to travel the world and visit all factories. And he said that the 54 Volvo factories at the end of the day in all, on all continents met with people on the shop floor on the management positions, then interviewed them and then parallel to that collecting like, you know, a Volvo production system assessment data, which would be familiar, I would assume to many of your listeners is type of audits that companies often run in, in lean transformations in addition to KPI data and the survey data. So, and while from this, I did my doctoral studies back in the day. So, which was for me, tremendous learning opportunity, just going, traveling the world and learning from Volvo a very good company.
Mark Graban (25m 40s):
Yeah. So as Linda from Volvo, and you mentioned going to Japan, tell us a little bit more about that trip or trips and the value of doing that.
Torbjorn Netland, PhD (25m 52s):
So I did that point in time. I visited mostly of course, some Scandinavian factories in the Volvo group, but also mostly American factories, which are good in their own way. Okay. Interesting. In their own way. And the cultures are different than these things, but then I went to us, I didn't know what the, oh, sorry to Japan. I didn't know what to expect them. As I said, the, the, the level of formality and, but also preparations that came from their sidewalks at the Northern level, absolutely different level. And then when I first came there, they stood 10 senior managers outside the factory lined up to welcome me at that point in time, a doctoral student to the factory to show me around. And in the end of the day they asked me, so what have you seen?
Torbjorn Netland, PhD (26m 35s):
What can we learn? First of all, at that point in time, I couldn't teach them anything, but I definitely learned a lot. So it was just a remarkable experience. And then the, what else should I say? I worked with, of course a it's called UDI trucks. It's a owned by a Volvo group. Now what's part of Nissan diesel before. And I saw truck manufacturing in Japan, whether or not this can be compared to Toyota, I dunno, but it was clearly impressive this first time you see this in a, in a Japanese automobile factory, maybe I was just standing floor above the shop floor.
Torbjorn Netland, PhD (27m 21s):
And it was like observing a dance. It was, It was, it was different. I never seen that in any other assembly factory in Europe or us, it was, it was a coordinated dance of moments just in time to the line flying carpets. Yeah. I don't know how to describe it. It was.
Mark Graban (27m 42s):
I know that I, I think I I've used that same language that the work is. So well-designed, it seems choreographed the interaction between individuals in the work between different individuals. I love a factory Tor, like when I've been able to go to Japan and you can walk up on that catwalk level and really both stand and look down to see the work that's different than a Tor where they drive you through on a, a tram, you know, and you don't really ever stop and like to watch cycles of work on whether it's the on an assembly line at Toyota of seeing how things are synchronized, or I think even more rare and more exciting to see is like a U shaped cell where the work is, is again like, so well-designed, it's, it's, it's really, it's beautiful to see.
Torbjorn Netland, PhD (28m 37s):
Absolutely. So that, that was my experience as well. On the mezzanine there, you could see that you could see the dance and then afterwards you go to the engine factory right next door and you learn it's a two hour buffer between them. And you understand also the fragility or the robustness of the system. There's not much, it's not much to play with. This has to work or everything stops.
Mark Graban (29m 1s):
Well, then, you know, you see even something like a two hour buffer, or even if you go to, let's say a Toyota plant in the United States, the assembly line is in segments that they and the, and there are buffers in between those segments were, were assembly kind of moves back and forth. And, you know, they're, they, I guess a question for you is helping people see past dogma of like, oh zero inventory. Well, Toyota doesn't have zero inventory or dogma of like, oh, inspection is waste, get rid of inspection. Well, Toyota still has final and final inspection.
Mark Graban (29m 42s):
Just, I'm curious to hear your thoughts on like some of these things that might be directional, but sometimes maybe people take it to an extreme before they're really capable of that.
Torbjorn Netland, PhD (29m 53s):
These are very interesting observations. And the clearly also where we've gone wrong to some extent, but I would first maybe start to say that, well, we say these things men, or it's often repeated in the Lynn community that we should have stopped less production and no inspection. The fact is that there are very, very few companies in the world that have ever had that. So you can't blame that for things doesn't work because companies actually don't have it. And w absolutely. When you look at inspection, this is where I I'm thinking about it, that you have to tailor this thing. We call lean to the context you're talking about. So if you go into an electronics manufacturer today, every second step is either a testing or inspection and you won't make waves of it because the customer is actually interested in paying a fixed exactly that the inspection is the service.
Torbjorn Netland, PhD (30m 44s):
You could also do this at home and don't have it tested and inspected, but then you have no guaranteed would work. So there's, there's actually value add to inspection testing, same with inventory, to some extent, because you're, of course, you're, there's a value add to having the product available when you want it. It's the value of availability. So, and these buffer inventory is actually may help reduce the lead time to your door or availability when you need it. This is, this is a discussion we really never had in the lean community. And it's misunderstood. And we're talking about the seven wasters stock, less production, and we're stuck there.
Mark Graban (31m 27s):
Yeah. I mean, I think things like, you know, the inspection inventory, like to me that some of that facilitates an outcome, like what the customer I think is paying for is, you know, the, the, the right quality product and the white, the right quantity delivered at the right
Torbjorn Netland, PhD (31m 44s):
Time.
Mark Graban (31m 45s):
And there might be ways of delivering that, that are least wasteful than others. Right. So having some inventory might be less wasteful than not being able to make delivery to your customer because you have an imperfect, unreliable process or inspection. I, I, you know, it seems like if, like you said, if somebody could guarantee that they were building a perfect product as complex as a car, I'm sure they would gladly do away with the inspection, but it seems like having the inspection again, like to me as least wasteful than delivering bad products that have to be fixed later.
Torbjorn Netland, PhD (32m 23s):
No, that's absolutely correct. Yeah. We, we call it these things, by the way, you know, coming textbook marks.
Mark Graban (32m 31s):
Well, well, we'll, we'll, we'll talk about the textbook. Yeah.
Torbjorn Netland, PhD (32m 35s):
But particularly the inspection, the inspection thing is something that is undervalued in manufacturing, and there are ways to, to, to, to go about it that that are better than others, but the idea that they should be completely removed is probably not feasible.
Mark Graban (32m 53s):
Yeah. But, you know, so you talk about, you know, the, like these different views. So I want to dig a little deeper into like, some people would say, well, lean means zero inventory. Like, well, okay. We might define it differently. You you've blogged about this. And I'll link to the blog posts that, that points to a journal article around, you know, confusion on, you know, what is lean. And, and, and I kind of want to explore two parts to this. Like one is different views amongst academics and researchers, and then maybe, you know, out in industry or in healthcare, but like what you want move very diluted to a couple of them. But what, but what's the most common confusion, or at least another common thing that people are maybe confused about, or, or maybe we might even use the word wrong.
Torbjorn Netland, PhD (33m 42s):
Okay. So this what's lean depends on, on your own way. You are kind of, and what you've seen. And there's so many different opinions right now, maybe you and I, we would like to think we've studied this for a long time. We know what it is. At least we know maybe more than average what it is, and maybe that's true. But then at the same time, we have our views and others have other views. That's the first realization we have to make. So when I was traveling the factories, sometimes I, I met many people on the shop floor that may not have heard the lien, maybe heard it, but forgot it.
Torbjorn Netland, PhD (34m 22s):
And, and it can also be of course, the company specific production systems. They heard it or seen it, but I don't know what it is. And often they would even define it as yellow tape on the floor, five assets that's we lean is cleaning. Okay. That's the mint for some people. That's the, how they see it. Now that's not whole, maybe more students than engineers would have said, because at least they had some class on this in school or something, they read a book and they will maybe see it as waste reduction. And that's maybe the most common way of looking at lean. And then this may be a common denominator across all these areas where we apply lean, because there's always waste.
Torbjorn Netland, PhD (35m 6s):
And it's a good thing to reduce it. This is fine. It's, it's correct. It just that there is more to it. And if you, only thing you do is to reduce waste. You actually hurt other areas that are important for performance. That's what I often come back to this mood and mood, our mood, which is fully, almost like a theory of lean, because it contains an understanding of, of reducing, reducing overload, reducing variability, and then reducing waste. So that that's a better approach. High level thinking.
Mark Graban (35m 38s):
Yeah. And yeah, I mean, it's, it's, I think sometimes it's important to try to separate different experiences, different opinions versus, you know, correct and incorrect. And there, there, and there, and there might be degrees of correctness. So it's not just a yes, no right. Wrong thing. But you know, you, you, you often read, there are some academics and, and there are publications. These often come from fields in the social sciences or labor relations articles that will go on and on about how lean is bad for workers. And it's based on some people's lived experiences, but the trouble I have is then when they generalize and say, well, these people had bad experiences in this organization, therefore lean is bad.
Mark Graban (36m 27s):
I'm like, well, that's fine. That's not that, that, that, that, that causes some difficulties or confusion.
Torbjorn Netland, PhD (36m 34s):
Absolutely. But this is, again, this is also a little bit understanding about how research works, right. Then there's limitations to research as well. And in many of these studies and also in many consulting practices, lean is a label you use to sell a service, whatever you can sell within this, that at least theoretically, you'd like to increase productivity or something in the factory, but you may end up just doing something under the label of lean because people want that. It, of course, we do have that in research as well, because you need to tie your, your research, finding something to, you know, to something that has practical value that people are actually interested in and, and lean this helpful in the sense, because it is a phenomenon of great interest in industry in research is also like this.
Torbjorn Netland, PhD (37m 23s):
If you can tie to something that the other side is working and you can prove it doesn't work, then suddenly it sounds more interesting than it may actually be because your observation is of course. Correct. So,
Mark Graban (37m 35s):
Yeah, there's a difference between saying, I mean, we could come at it either way that an organization tried to quote unquote, implement lean, whatever that meant to them, didn't really lead the business benefit. The employees were all upset. The company gave up on it and to say, you know, lean didn't work there. It's, it's hard to extrapolate just as it would be hard to extrapolate. Let's say, look at a company like Danaher like, well, you know, Danaher's a manufacturer, acquires companies put some through lean transformation, creates a lot of value, creates a lot of benefit to, to all their stakeholders. That doesn't mean everyone's going to be a Danaher either.
Mark Graban (38m 17s):
So what do we learn from the problems? And what do we learn from the successes that that's what we have to figure out for. Let's say, as you, as you frame it, our company's production system, right?
Torbjorn Netland, PhD (38m 28s):
I think it's a much better approach. The, because of, for numerous reasons, the lean lean is many things to many different people. And it depends on your experience. And this is a, when we say, when you present, we'll talk about that company that some, maybe organizational behavior research studied and they find they were doing lean, a served, right? That's a phenomenon. Somebody tried to do some 5S and daily shop floor meetings and stuff, and whether or not it worked and it was implemented or used as, as it should be. It's of less interest. It's a phenomenon lean under this.
Torbjorn Netland, PhD (39m 10s):
Certain things happen, cost relationship and so on, and then go. So it's from their perspective, it's not wrong, right. But if we look at this from the, maybe that's the one, it becomes tricky. When we look at it from the Toyota lean as TPS angle. And we look at the respect for people and using daily shopflor, meaning properly in this, that's absolutely not lean. Then the question is, okay, so is lean Toyota production system. And some people would say, some people say lean is TPS applied outside of Toyota. It's a fair definition. But I would, I think it has many problems because I don't think for example, and you're the expert, but when you apply lean in a hospital, it's not TPS outside of a car factory.
Torbjorn Netland, PhD (40m 3s):
It has completely different settings. It's the customer is not the customer that the patient is not the customer and so on and so on. So that's where I think the company specific production system tailoring the lean, if you'd like, or even if you want to go there Six Sigma and Total Quality Management, whatever works for you to achieve the purpose you want to do, which is often improving productivity, hack it into your own system, just like Toyota did. That's what, that's what they did. Yeah.
Mark Graban (40m 36s):
Yeah. I mean, I think, you know, we, we, we, in, in healthcare we can certainly learn principles and mindsets and practices from Toyota. I, you know, did we call it TPS with, you know, we probably wouldn't call it TPS. We, we, we, we probably wouldn't call it. I wouldn't call it production. Right. So you mentioned earlier this one label, Virginia Mason Production System, like as successful as Virginia Mason has been over 15 plus years, I've always found that a bit curious that they didn't call it. Let's say the Virginia Mason Care System, or, you know, there are other organizations that might say, well, we've adapted lean and TPS.
Mark Graban (41m 19s):
And we call it the Cleveland Clinic Improvement Model, or we call it continuous improvement or some other label, or we, so Cleveland clinic Improvement Model is Cleveland Clinic's description of their system. And I think there is benefit to that, right? I mean, General Motors didn't want to say we're implementing Toyota Production System. They want to call it, you know, global, competitive manufacturing or something. They give it their own label.
Torbjorn Netland, PhD (41m 46s):
No, I think that, of course there's a value because of the ownership you get to the model that you're, of course, nobody in the automobile industry want to implement the compact that this model. This is maybe also partly why they call it lean back in the days, but that's too generic. Right? So labeling, labeling it by your own name, maybe even using your logo, your colors, it creates some ownership. There's no doubt that this belongs to you. And that comes with a few benefits. First. It makes it clear. That mean this is not optional. This is a system that we have developed and want to use. And second, it should also create a little bit more longterm commitment to the model. So, you know, when the CEO change, okay.
Torbjorn Netland, PhD (42m 27s):
New model it. But if you particularly, if you use Six Sigma for a long time, okay, then we'll try lean and you get all this, the consultants cross firing at you and trying to win you over for the next big thing, industry 4.0, industry 5.0. If this, these things happen in any case, if you can say fine, but let's build it into our company's specific production system, business system or whatever you want to call it. I think it's a stronger, more sustainable approach. Yeah.
Mark Graban (42m 56s):
Yeah. There, there there's that, that ownership when there's the ability to evolve. So like, just to use another example of a organization in their label, duke university health system has what they call the duke quality system. When you call it something like, you know, kind of broad like that you can fold in and incorporate different methodologies where it doesn't seem like, you know, we're, we're, we're, we're, we're giving up on this and now this is our thing. Like you, you can, you can fold in maybe a little bit of six Sigma with, with lean and, and other safety and quality practices, you know, it's, Duke's, you know, quality system and, and, and, and one other benefit maybe in you, you wrote about this, I wanted to ask you about, you know, lean versus TPS.
Mark Graban (43m 47s):
It's funny you wrote in the blog post, if you like heated debate, started discussions, thread on the definition of lean on LinkedIn.
Torbjorn Netland, PhD (43m 56s):
I think
Mark Graban (43m 59s):
I've, I've seen I've, I've seen enough of that, but I think the other heated debate is one that I see a lot of people back to this question of lean is just a label for TPS versus lean is a low definition, low fidelity qual copy. Let me start say that again, a low fidelity copy of TPS, or it could be better than TPS where we've taken it. You know, you know, I think you or somebody in the article said, you know, are we trying to copy Toyota of the 1960s? Or are we trying to evolve our own company operating system?
Torbjorn Netland, PhD (44m 39s):
Absolutely. I mean, this is, I, you know, when I go to conferences, you still see this Taiichi Ohno on the shop floor, right? Maybe we are also guilty in using it at some point in time. And you See on the set, the Nissan, the shop, plus on the sentence, come on, this isn't state of the art. And we know, and whatever he said back then was probably truth in all of these things, but it isn't, it isn't a universal truth and the world change. So when the world evolves also Toyota evolves, right. It develops that the auto production system, which we talked about that day, we saw in France now in the Toyota factory, they have a look, they have an industry 4.0 manager in Toyota factory.
Torbjorn Netland, PhD (45m 26s):
That's it, that's an interesting observation. So there's something that happens and basically just shows that Toyota at least is willing to learn and, and, and develop there. Maybe anyway, maybe we should try to ask someone to define what is the Toyota production system on the 2022. And if what they still show is, you know, the TPS house, which is a very good description of how it was, if, if that's what we still are. We losing out on a lot of opportunities with new technologies, with new world, with Gail political tensions and all kinds of things that we have.
Mark Graban (46m 5s):
Yeah. Yeah. And we can look and see how Toyota, you know, on their corporate Japan website in English, how they define the Toyota production system today. Right. W what,
Torbjorn Netland, PhD (46m 16s):
That's two, that's two things they have on that page is Jidoka. And just in time, right. I mean, at least
Mark Graban (46m 24s):
That's it. Yeah. And then there's, there's a lot more to it, but let's say if you visit, you know, one of the visitor centers in, let's say San Antonio, or in Japan, when they have, you know, displays explaining, here's what we mean by respect for people. Here's what we mean by continuous improvement. Like, you know, there are those other dimensions to it. We can look at how, you know, TSSC teaches TPS to different types of organizations here in 2022. How they, how do they explain it? And, you know, I, I think, you know, I, you, you raised a good point. There are some notions that might be outdated and Toyota has evolved.
Mark Graban (47m 4s):
Like the one I've heard from Toyota people is like kind of the classic image of Taiichi Ohno, and people would jokingly say, oh, no, here comes Mr. Mr. Oh No. Cause he would, you know, he would yell and scream. And there are lots of stories about behavior like that. But Toyota seems to evolve sort of, you know, from that, that behavior, like that might not be acceptable today that you know, that they've tried to evolve into what, what I've heard them described as a more humanistic approach to, to how they improve and how they lead. So I think there would be danger in somebody saying, well, here's how Taiichi Ohno did or here's how Shingo Jitsu people did it lean means yelling and screaming and insulting people like that.
Mark Graban (47m 48s):
That I wouldn't, I wouldn't recommend that,
Torbjorn Netland, PhD (47m 53s):
But the, yeah, like the us army approach, I try to break them down and then build them up again. It may work in some settings, but absolutely not in all. We also have to remember that when a, of course, Womack Jones and Roos in the end of the whole IMV study in the, in the eighties, seventies, eighties, and nineties then studied this thing. They, they described the Toyota production system as of that day in 1998, 1999, in the Machine That Changed the World. Right. And that's when we started to use the word lean and that's a good study and all of that is good. But at the second after that, I mean, 99, we started to populate the lean term with a lot of things that were never used in Toyota.
Torbjorn Netland, PhD (48m 36s):
Prime example is the value stream map. It's a good tool. It's a fantastic tool in many settings for consultant doesn't work in all settings, but it isn't a Toyota tool, right? It's,
Mark Graban (48m 48s):
It's an adaptation of what they called, what material and information flow diagram.
Torbjorn Netland, PhD (48m 53s):
Right? Absolutely. And that place in another role, in a minor role in Toyota. And so maybe that's an improvement of the Toyota production system, at least for some settings, but not for all. That's why I say lean isn't Toyota Production System. It was lean, a production system. And you know, when Krafcik in 1998, he put all the study there on, on, on, on lean that's when lean was TPS, since then, it has evolved in slightly different directions. And a lean of course is a much broader term than TPS. And we use lean in healthcare in hospitals, in governance, governance in police. And nobody should tell us that it's exactly the same in all these settings, because it isn't true.
Mark Graban (49m 36s):
Yeah. And, you know, there are things that evolve and, and then there's some things that are old. There may be timeless principles that don't change things like, you know, a principle like respect for people, respect for humanity. Some of the manifestation of that may change over time, but the principle probably doesn't become outdated.
Torbjorn Netland, PhD (49m 58s):
No, we all agree at that level. And then of course also this principle means different things in different cultures slightly. Right. And so it's, it might be, I would like to make that point about if you have a company specific production system as Wally, it's just a guide. I mean, it's, it's not, not a system you should rigorously implement because some of, sometimes these systems and programs that are adaptations of TPS to whatever, do your setting tends to take on a live life on their own, right. They are followed with lots of assessments and a, and there's 2030 people working in the group, just implementing and making PowerPoint slides and all kinds of things to make these things look nice and shiny, eh, part of that is needed, but it shifts the objective from improving work itself to running these programs.
Torbjorn Netland, PhD (50m 51s):
And that's where we sometimes go wrong as well. But we try to structure too much the deployment of lean if we want to use that as a overarching
Mark Graban (51m 3s):
Yeah. There's deployments. And you've written about how, and I would agree with you on this implement or implementation is probably not the right word either.
Torbjorn Netland, PhD (51m 12s):
Oh yeah. I use this word. I think it was back in, was it deaf liker? I think I was in a call conference with Jeff liker and I talked to about them like informally about this. And I used the word implementation and he stopped me and say that that's not, that's not appropriate. But so he's thinking kind of the idea is simple lean isn't the it system. I mean, it's not a digital that you can't implement it. You don't anything. Okay. That was nevermind tension obviously, but using this word, but reflecting on it further, I'm not, I'm very relaxed about it because sure. Okay. Then what's your, we call it deployment. Is it better?
Torbjorn Netland, PhD (51m 52s):
What does it mean
Mark Graban (51m 53s):
Adoption? I don't, I don't, I, yeah,
Torbjorn Netland, PhD (51m 57s):
Never ants. I mean, particularly for a researcher, the world word implement is almost needed because we, we have to say something for sure. Whether or not you use it or not. I mean, we can say, oh yeah, we're in there somewhere on the process, but we don't know exactly where we need to be able to try to, to pin down approximately where you are, maybe even with a number or otherwise we can't do objective research on it that has its limitations. We all understand it's not that easy. And then there is things, but it's also what companies do with our assessments. So I'm a relaxed about the world, but I've been arrested before for using it
Mark Graban (52m 41s):
Back to that point of different researchers, you know, maybe having a different view or different word. And yeah. I mean, hopefully, you know, some of that difference, sparks people to think and reflect and, you know, create their own experiences. But, you know, before we wrap up here, I do again, want to point people to your blog, better-operations.com and you can find links to journal articles that, that, that Tor is written. There's one. And maybe at some point we could do, we could do a whole episode around something you wrote about and I've written and talked about why it's wrong to blame Justin time, quote unquote, just in time for pandemic era supply chain problems.
Mark Graban (53m 24s):
Like could, could you give maybe just a real quick a synopsis, if, if an executive or if you were talking to an executive on an elevator and they said, you know, Tor use you say lean is good, but just in time has killed this during the pandemic. How would you try to explain?
Torbjorn Netland, PhD (53m 41s):
Well, first I would also, you are not using just in time because you probably don't know exactly what it is. I mean, if you have a global supply chain and these things, you already value evaluating a little bit, the principle of, of, you know, next door supply and this. So that's one thing. And even if they have global, they usually tend to have tons of inventory in their supply chain. I know it was stocked somewhere and that's it. They don't know where it is. I mean, so they can use digital technologies and all kinds of things to improve that performance. But so I would, it's globalization, which I think is a beautiful thing, is more to blame for the crisis that, that we got. And then just in time, and, and by the way, I hope people go back to a time where we see globalization blossom again, right now it's a little bit of a dark time.
Torbjorn Netland, PhD (54m 31s):
I wanted to say one more thing. What was that? Just forgot it. Yeah.
Mark Graban (54m 38s):
That you're probably not really practicing just in time because you have big, long slow supply chains.
Torbjorn Netland, PhD (54m 44s):
Yes. I was one more thing I want to say, if we want this to be a good planet to live on in the future, there is no other option than just in time. There's no, I mean, especially with the fragmented long global supply chains that we have, and we have them for a reason, it's because the economic activity, you know, always takes the shortest path, just like water. It finds it way. And it's a good thing. It's, it's why the world has developed, you know, we are prosperous in these things. Not saying we should not have manufacturing PMPs in Western culture, we should absolutely will always find its way, but cooperation and trade is a good thing in general. And if you're going to stop this world up with inventory everywhere, it's just not gonna gonna go on and be a good thing instead of inventory focus on shortening lead times.
Torbjorn Netland, PhD (55m 34s):
And that this is just very good. Your thinking. So we're back to lean is saving the world.
Mark Graban (55m 41s):
Well, there there's shortened lead times, which means, you know, more agility, lower inventory at the same time, but then there's the environmental impact and the carbon footprint, right? So I've seen Toyota at factories. I don't know, off hand if they've achieved this, I know they certainly aim to be zero landfill facility. So that's a, that's a pretty local way of looking at things. I wonder if, if you know, the, the next step might be to aim to be carbon neutral through your supply chain,
Torbjorn Netland, PhD (56m 11s):
They all would be fantastic. Unfortunately, it's been free to pollute up to today, but again, here is an area where we should also embrace technology and not just say let's, you know, we are because technology can do wonders. If we are able to do things that reduce emissions, it can be anything from continuous improvement of engines to just make them more energy efficient than the, there they are. It's not like they're not working on this. And then we also need to shift the new technologies. So there's, there's a business opportunity that can actually be good for the world as well.
Mark Graban (56m 47s):
Yeah, well, so, so I, again, our guests has been Tor net land Tor. I'm really looking forward to meeting you in person and to, to seeing you, to hearing you speak at the AME conference in Dallas. So again, to remind people, go to ame.org, look for a link in the show notes and any final, final question. And maybe we can talk about this again in the future that you have a textbook that you've written with Michel Baudin, who I know he's a, a Frenchman who's lived in California for, for many decades, and I've crossed paths with him and, you know, re respect his work. T tell us about, tell us about that textbook and what the focus is when it's going to be available.
Torbjorn Netland, PhD (57m 32s):
That has been a long project, or if I knew when we started this thing, I don't know if we would have a start, but we're getting to an end, the five or six years after we started, which is much longer than what we had intended, but it is a, an 800 page textbook on introduction to manufacturing. You start to write about manufacturing. You realize there's quite a few things that you need to cover and manufacturing is so diverse. So there's so many different arguments you need to make. There's some boiler plate arguments about the, you know, using some principles that everywhere just doesn't work.
Torbjorn Netland, PhD (58m 12s):
So that's what has taken us quite a bit of time. It's a book with an industrial engineering and management perspective. And what it really does is that I think it fills the gap because there's tons of textbook on operations management and supply chain management. They're taking the process perspective and explaining operations strategy. And then these things, they have tend to be generic, good books to learn about this. And then many of them, at the other hand, there's all the machining process technology textbooks that go into grinding, melding automation and all of these things in the middle there, how you manage actually design and improve a factory. There's been almost nothing. And that's exactly where we target the book.
Torbjorn Netland, PhD (58m 56s):
So I look forward to have that, see that we've sent it to production. So now, now we're waiting for Rockledge to Welsey hall or lean. They are so
Mark Graban (59m 6s):
Well, there are even in the best of times, publishing supply chains can be slow and global. There's a, another author I talked to recently whose book was Alan Robinson, who I'm going to have on the podcast again here. Soon new book was the release was delayed for a couple of months because what he was, he was told there were paper shortages, at least, and at head at his publisher. So I hope you don't. I hope you don't hit delays in that.
Torbjorn Netland, PhD (59m 36s):
Maybe not, but there's also the ebook. So there's always some technologies that we can't ignore.
Mark Graban (59m 44s):
Well, it'd be a, you know, an 800 page book is a lot to carry around. So there's a benefit to an ebook first.
Torbjorn Netland, PhD (59m 51s):
Maybe of course, it's something with holding a textbook in that.
Mark Graban (59m 56s):
Yeah, there are pros and cons as, as with any of these new technologies. So we'll look forward to that book being available. Maybe when the book comes out, maybe you and Michel and I can do an episode together to talk about. That
Torbjorn Netland, PhD (1h 0m 10s):
Could be fun. That could be fun.
Mark Graban (1h 0m 12s):
I have no good reason why I haven't invited Michelle to be, to be on the podcast. So maybe we can do that at some point. So again, Tor Netland joining us from Switzerland and he will again be at the AME annual conferences. One of the keynoters a website again is better-operations.com. Tor. This has been a lot of fun and really thank you for being here today.
Torbjorn Netland, PhD (1h 0m 38s):
Thank you. See you soon.
Announcer (1h 0m 41s):
Thanks for listening. This has been the lean blog podcast for leading news and commentary updated daily, visit www.leanblog.org. If you have any questions or comments about this podcast, email Mark leanpodcast@gmail.com.
Please scroll down (or click) to post a comment. Connect with me on LinkedIn.
Letās build a culture of continuous improvement and psychological safetyātogether. If you're a leader aiming for lasting change (not just more projects), I help organizations:
- Engage people at all levels in sustainable improvement
- Shift from fear of mistakes to learning from them
- Apply Lean thinking in practical, people-centered ways
Interested in coaching or a keynote talk? Letās talk.
Join me for a Lean Healthcare Accelerator Trip to Japan! Learn More
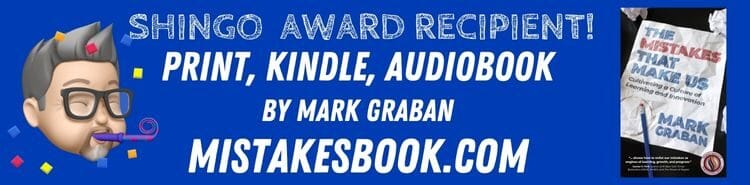