Listen:
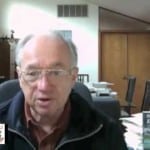
LeanBlog Podcast #36 once again features our friend and frequent guest, Norman Bodek, noted lean author, consultant, and President of PCS Press. In this episode, Norman talks about his most recent publication, a text by the legendary Shigeo Shingo, called Kaizen and the Art of Creative Thinking – The Scientific Thinking Mechanism, as well as future publications he is working on.
This was recorded back in 2007, before the book was published (it has now been out in publication for a few months, I apologize for the delay in getting this podcast released).
If you enjoy this podcast, I hope you'll check out the rest of the series by visiting the LeanBlog podcast main page.
Keywords and Main Points, Episode #36
- You can find the book here via enna.com, or amazon.com.
- Can you share the background and significance of Shigeo Shingo's new book, Kaizen and the Art of Creative Thinking, in the context of Lean and creative problem-solving?
- How does this book connect with Shingo's previous works, and what new insights does it offer?
- What is Shingo's “scientific thinking mechanism,” and why is it valuable for companies aiming to develop problem-solving skills among employees?
- Why is it important for companies to encourage all workers to participate in creative improvement activities, and what impact has this approach had in Japanese workplaces?
- How does the Japanese approach to worker suggestions differ from typical American practices, and what can companies learn from these differences?
- What are the core principles in Shingo's approach to analytical thinking, and how can they help in capturing and clarifying problems?
- How does Shingo's method address idea generation for improvement, and what steps does he outline for effective problem identification?
- Can you explain the significance of separating idea generation from judgment, and how this approach benefits creative problem-solving?
- How does Shingo describe the evolution of improvement and moving from ideas to reality, and what role does overcoming mental obstacles play in this?
- What are Shingo's “10 objections,” and how do they hinder the improvement process?
- Can you discuss Shingo's nine-point policy for promoting improvement ideas within an organization, and how it supports a culture of continuous improvement?
- How can study groups be used to maximize learning from Shingo's work, and why is this approach effective for translating theory into actionable insights?
- How does Shingo's emphasis on developing people align with the goals of Kaizen, and what challenges do organizations face in adopting this mindset?
- How can companies apply Shingo's principles of problem-solving instead of merely copying other companies' methods, like Toyota's?
- What do you hope readers will take away from Kaizen and the Art of Creative Thinking, and how should they approach this book to get the most out of it?
If you have feedback on the podcast, or any questions for me or my guests, you can email me at leanpodcast@gmail.com or you can call and leave a voicemail by calling the “Lean Line” at (817) 372-5682 or contact me via Skype id “mgraban”. Please give your location and your first name. Any comments (email or voicemail) might be used in follow ups to the podcast.
Click here for the main LeanBlog Podcast page with all previous episodes.
Automated transcript:
Mark Graban:
Are you struggling to find the right leaders to drive your Lean transformation? Stiles associates has a 30 year track record of solving those talent problems in the manufacturing, private equity and healthcare sectors. Their team of executive recruiters rigorously screens and delivers exceptional candidates, resulting in a repeat client and referral rate of over 90%. Visit leanexecs.com to discover how Stiles Associates can help your organization find the perfect leader for your team. Or if you'd like to be considered for a role, go browse the open Assignment section and send in your resume today.
Mark Graban:
Once again, that's lean execs.com.
Announcer:
Welcome to the Lean Blog Podcast. Visit our website at www.leanblog.org. now here's your host, Mark Grabin. Hi, you're listening to episode number 36 of the Lean Blog podcast. It's Febr 8th, 2008 and this is Mark Graben.
Mark Graban:
Our guest today is Norman Bodek. He's going to be talking about the new book he brought to the Lean World from Shigeo Shingo called Kaizen and the Art of Creative Thinking. I do apologize for the delay in getting this podcast out. We actually spoke about the book back in September of last year. So when you hear us talking about how the book will be coming out, the book has already been out on the market and if you'd like to buy it, there's a link to do so on leanpodcast.org if you look for the link to episode 36.
Mark Graban:
So I hope you enjoy the podcast, belated as it may be. I hope you'll also come back for future episodes, including one in about a week with Jeffrey Leiker, when we'll be talking about his new book, Toyota Culture. So as always, thanks for listening. Well, it's my pleasure to welcome a frequent guest here on the Lean Blog Podcast back again today, Norman Bodek. Thanks for being here.
Norman Bodek:
Hi, thank you, Mark.
Mark Graban:
Today we're going to talk about a new book from Shigeo Shingo that you are going to help introduce us to. Can you tell us kind of the background and what that book is going to be about?
Norman Bodek:
Yeah, I go to Japan probably twice a year over the last 30 years, been there 67 times and lately I go to visit Mrs. Shingo, Dr. Shingo's wife. I see her at least once a year or once every other year, and a couple of years ago I visited her house and she showed me a number of Shingo's old books that I did not translate. I've translated and published maybe five or six of Dr.
Norman Bodek:
Shingo's books, and there's a lot of old ones. And I went and selected three of them specifically. And I took the first one. Dr. Shingle called it the scientific thinking mechanism.
Norman Bodek:
And I went to the publisher and negotiated the rights to reprint it in English. And then with a company called Enna E N N A in the state of Washington, we agreed to become partners on producing this book of Shingo's in English. Had no idea what was in it because I don't read Japanese. So it's always big gamble for me when I do this. When I owned productivity, I would translate maybe five books.
Norman Bodek:
And I was very lucky because four of them were good, very good, and one of them I couldn't use. But this one turned out to be an incredible jewel. I teach quick and Easy Kaiser.
Mark Graban:
Right.
Norman Bodek:
And this is a very simple process to get all workers involved in creative improvement activities. It's really the Japanese suggestion system. And when you really challenge people to identify problems and solve them, it's amazing what they'll do. I mean, in America, the average worker comes up with one suggestion every seven years. In Japan, it's 24 in writing.
Norman Bodek:
At Toyota, at one time it was 70 ideas. Now I teach people this system and it works. It's miraculously miraculous how my clients are able to go from hardly any to like GulfStream. They got 16 ideas from 1,000 workers in February 2005, and now they're up to 27,000.
Mark Graban:
Yeah, it's not a problem that people can't come up with the ideas, but they're not being asked or there aren't mechanisms for them to communicate those ideas. Right?
Norman Bodek:
Absolutely right, Mark. Yeah, but we don't have the mechanism. We don't answer them. We don't go out and say to the worker and challenge them, you got problems. Look, people are solving problems.
Norman Bodek:
Of course they are. But we don't have. Most companies don't have the system to draw this out. So instead of just getting a handful, here we're getting thousands of them. And we're looking for very small ideas because we want people to be excited at work.
Norman Bodek:
Well, so I teach people the system, but I don't teach them how to identify or I haven't taught them how to identify and solve them. And Shingo's come up with this marvelous book, just marvelous, filled with beautiful charts and graphs and wonderful stories because Dr. Singer was a great storyteller. And this is a really step by step process of how you can identify problems and solve them. And I'm so proud of it.
Norman Bodek:
I Mean, I'm so lucky in my life. My life is always filled with miracles. And this is such a beautiful book. And even Jeffrey Leiker wrote the foe to it, which is very exciting for me. Single taught in the book.
Norman Bodek:
I'm just looking at the table of contents and first part is on the Principles of Analytical Thinking. And the second chapter is Capturing Problems. How do you find problems? Never accept the status Quo. How do you clarify problems?
Norman Bodek:
What's the five elements of problems? He talks about Gilbraith's work. His 18 serve leagues. Thinking analytically for purposes of improvement. Then the third chapter is Idea Generation for Improvement.
Norman Bodek:
Many Paths to a single summit. Mental activities for improvement and what he calls his scientific thinking mechanism, which is brilliant. This is a flow chart and this is a process of how you get people to think scientifically about solving problems.
Mark Graban:
Right.
Norman Bodek:
And he gives us 12 steps. 12 steps eliminate looking, opposing viewpoints, etc. Next chapter is the Evolution of Improvement and he gives us a little bit of a history and brings us up to automation. And then the fifth chapter is From Ideas to Reality. Overcoming Mental Obstacles.
Norman Bodek:
Separating Idea Generation from Judgment. An engineer's instinct versus a manager's instinct. And what's the 10 objections? He calls these? The 10 objections?
Mark Graban:
Yeah.
Norman Bodek:
Objection. Based on exceptions. Nitpicking. Objection. Unit manipulation of.
Norman Bodek:
Objection. Chicken or egg. Objection. Tadpole. Objection.
Norman Bodek:
Cross eyed. Objection. These are just beautiful. And the last chapter, Promoting improvement ideas within the organization. Developing what he calls a nine point policy.
Norman Bodek:
The true value of improvement. And the last one he talks about Looking in the Mirror.
Mark Graban:
It sounds like some very practical material for how do you drive Kaizen?
Norman Bodek:
Oh yeah. I mean first of all, when you read this, you recognize that the only way to achieve this is comes from people. So I got to develop people, I got to work with people. And if we do, they'll go out and solve these problems. Look, what we're looking for is not complicated.
Norman Bodek:
We want to improve productivity and we want zero defects.
Mark Graban:
Right. And so then this book is going to be available somewhat soon, right?
Norman Bodek:
Yeah, it's published by November 1st. It'll be available and we did something new this time that I've done in the last recent years. It's going to be in hardcover.
Mark Graban:
Okay. So this will be available through PCSpress.com and I assume the major online booksellers, is that right?
Norman Bodek:
Yeah, I mean they can get the book from the PCs press or they can get it from Na Enna. I'm sure they'll love it.
Mark Graban:
Yeah. What's the title again?
Norman Bodek:
And it's called Kaizen and the Art of Creative Thinking.
Mark Graban:
Okay, now.
Norman Bodek:
Those of you that are familiar with my past books of Shingle, I want to tell you about one book which was this med book, you know, the white book.
Mark Graban:
Yeah.
Norman Bodek:
Single Minute Exchange Die. When I found it, then I published it, and I had the audacity to sell it for $60. Call it the Audacity. It was a lot of money, but the book cost a fortune. First of all, I didn't know what I was doing back then in publishing a book.
Norman Bodek:
I had to pay for the translation twice because the first translation was so bad. It was a real struggle to produce it. But we sold over 100,000 copies of it and revolutionized manufacturing. I mean, when you think of many companies in America, changeover is not a problem anymore. By following Dr.
Norman Bodek:
Singh's advice and now Shingles addressed this other area of creative thinking. It's the heart of what he taught. Thousands of Toyota managers have gone through this, and I hope that there will be people smart enough out there that will look at this book and develop their own training courses to teach what's in here to the workers.
Mark Graban:
Right, right. Because I see a lot of questions or people asking online about how to get training and the Toyota problem solving methodology, because you hear so much about how that's really the key to what the management system and the Toyota way is about. So it seems like there's a real kind of pressing need or there's a hunger out there for learning about that.
Norman Bodek:
Yeah. You brought up something I think is very interesting in the whole learning process. One, of course you should go to school. Everybody should go to school for life. I mean, this thing about I graduated college or high school and learning is over, has to stop, and so we have to go to school.
Norman Bodek:
The best school, of course, is the school of life. The best schools should be at each company. Each company should have their own university. And who should be the teachers? The teachers should be the workers.
Norman Bodek:
There are companies in America that are outstanding. One company where like 75% of the people in the plant were teachers. Somebody who had a really great skill would teach that skill to the other workers in the plant. Yeah. And this is the kind of book that I think the same thing should happen is companies should take it and read it in study groups.
Norman Bodek:
Right. Then as they read it together in study groups, then they challenge people to use the material there, go out on the factory floor and do it.
Mark Graban:
Yeah. So you have that book coming out. You had mentioned when we talked previously that you have some other books that you're working on as well. Can you tell us about those?
Norman Bodek:
Yeah, I'll tell you. I have quite a number that I find, especially on this trip, I found quite a number of new books I'm going to be attempting to do as quickly as I can. But these two other Shingo books that I'm going to be publishing, one is almost completely translated, and this is probably the most difficult project I've ever had in my life. First of all, it's brilliant. It's Shingo talking about the fundamentals of plant improvement.
Norman Bodek:
And he's meticulous in his description and his precision in the way he did it, but it's very difficult. And to what extent will American managers, American engineers, American workers be willing to study this? It's like going to college. It really is. It's going to college is here.
Norman Bodek:
Here I have a machine that's not operating as efficiently as can. As it can. What can I do to make it operate more efficiently? You have to really study very hard in order to do this. Well, that's the way this book is.
Norman Bodek:
And I can't envision somebody just picking up the book and reading it from beginning to end. I've been reading it, and it's very, very hard for me. And I done all these hundreds of books.
Mark Graban:
Is it just a pretty intense process or.
Norman Bodek:
This is very intense, but it's worth the effort if we can get people to do the effort together. And so I think what I'm going to ask is people like you, Mark, and a lot of the people that I know, a lot of the professors that I know, I'm going to ask them to take a few pages of the book and to tell us their understanding of it, what it means to them, and to also come up with questions that we can have at the end of every chapter.
Mark Graban:
Okay, yeah.
Norman Bodek:
Then the book could be used at a university, and the book could be used within a company where people can read the chapter, reaching those brilliance, but also listen to some other expert and their feeling about the work, and then asking each other the questions and challenging each other. Are we doing it this way? I mean, really, have we addressed the issue of transportation within a plant properly as an example? Transportation is a waste. How do we eliminate that waste?
Norman Bodek:
I mean, you go to many plants and you see people happy with their forklifts running all over the place, you know, delivering.
Mark Graban:
They've added conveyor belts.
Norman Bodek:
Well, they made a conveyor belt. Right. And, you know, they're happy with the transportation. But transportation is a waste, and it should Be eliminated. Yeah.
Norman Bodek:
And how do you. Well, turn. Just did something interesting I've noticed in my last two visits. One Georgetown last year, and this visit recently in Japan this September, which is 2007, is they're now using a kitting system. Yeah, I saw the kitting system at Canon about 15 years ago, but not at Toyota.
Mark Graban:
They're doing this down in San Antonio. It's been in the news as well.
Norman Bodek:
Yes. And this system really eliminates a tremendous amount of waste, reduces inventory to a minimum because the kit is filled with the parts, with all of the medium sized, smaller parts, and it goes with the car. And so the worker picks out of the box, out of the kit or the box, the container, the parts that they need for this specific car. Because every car is different.
Mark Graban:
Right, right, right.
Norman Bodek:
So what I saw at Prius on my visit in September is that as soon as we walk into the plant, we can see the inventory area and the worker is filling a container. And the way they do it is there's the container is they're in sort of like a rectangle. The workers in the middle and all around the sides are the parts to be picked. And a light goes off and the worker runs over to that area where the light is a green light and then pulls out the part that he needs. And I think a red light goes on to show that he did pull it out.
Norman Bodek:
Because we want to make sure that he did pull it out and not that he just went to the light and took it and then clicked the trigger. But he doesn't have the part in his hand that Shingo's Poka-yoke system. And then it goes into the. Into the container. And then the container goes and follows that specific car along the line.
Norman Bodek:
So the only parts that are there are the parts that that car needs.
Mark Graban:
Right.
Norman Bodek:
And you don't have the 20, 30 or 50 items cluttering up the whole factory floor.
Mark Graban:
So that was put into effect, I'm sure as the result of a particular problem. And by going through a problem solving process like Shingo wrote about, they decided that kitting was a good solution for that. I bet, right?
Norman Bodek:
Yeah. Because it eliminates inventory and it only puts into the box exactly what belongs to that car previously. The worker would select from the parts behind them what they would put in.
Mark Graban:
Right.
Norman Bodek:
And they could make a mistake.
Mark Graban:
Yeah. And there's a lot of. You don't have as much floor space with line side inventory. I've got to tell you a story because it's right along the line of this topic. You're talking about thought process and problem solving as opposed to just copying what other companies have done.
Mark Graban:
I was at a series of meetings a couple weeks back. I blogged about this briefly and I'm not going to mention who the company is, but it's a company that pretty big major company. They are going through a kick now where they're trying to copy the Toyota production system and they're going to do lean and they've always used kitting in their assembly because there's a high variety. A lot of the factories you had mentioned and they were getting away from the kitting and doing kanban and line side inventory. At least the way they described it was, well, that's how Toyota does it and we're going to be like Toyota now.
Mark Graban:
Then later in that same set of meetings we had a guy from Oregon at the Toyota truck customization and assembly facility there and he was telling a very similar story about how Toyota decided at least at their plant and other plants that they are going away from line side storage to kidding because of all of these benefits. I saw the guy from this other company was just scribbling furiously and I felt bad for him that they were doing this inspired by what they thought Toyota was doing rather than using a problem solving process like I'm sure the Shingo book did. Describes where think, well, gosh, if they really need to figure out for themselves what makes sense rather than just copying somebody.
Norman Bodek:
Of course that's a great key. I mean you do want to study the best, but you have to know why they're doing it and then you have to see that it applies for you that you're doing the best. So Toyota is a great system that works for building automobiles and I'm sure it can work for many things, but you have to adapt what you need for your environment. Kitting was good because it helps the precision that we have the right parts for each car and we're eliminating so much of the transportation that ran on in a factory. You don't see in the Toyota plant these forklifts going back and forth.
Norman Bodek:
You do see some, but even less, you do see robotics. You know, you see the unmanned vehicles, but you see a lot less of that because of the kitting system. So that was reduced. So what I'm hoping for, Mark, is that everybody out there buys this new Shingo book, Kaizen and the Art of Creative Thinking. And they get together in study groups and they ask people to learn from the great Dr.
Norman Bodek:
Shingo once again. And study groups are so powerful. I mean I can read a book and forget everything that I read. But if I sit in a study group and we talk about it and then I get a chance to apply it, then I remember everything that's there. And books are.
Norman Bodek:
So if you use it this way, books are the least expensive way of educating people in your company. The least expensive way.
Mark Graban:
I love study groups because it helps take what might seem like theory in the book or somebody else's examples, and it's a great way of translating that into action and discussion around. Okay, so how does that apply to us? If we're reading about Toyota, that's great, but we're a different type of business. What do we learn from that?
Norman Bodek:
Yes. So once again, I thank you very much, Mark, for the opportunity to talk with you.
Mark Graban:
Well, thank you for taking time out of your schedule to share a preview of these new books. And I think I'll speak for a lot of podcast listeners that we're looking forward to seeing the book. And we'll post review and links on the blog website for how people can go.
Norman Bodek:
Oh, thank you, Mark. And I'll send you a copy right away. Thanks an awful lot, Mark. Appreciate it.
Mark Graban:
Okay, we'll talk to you again soon, I hope.
Please scroll down (or click) to post a comment. Connect with me on LinkedIn.
Letās build a culture of continuous improvement and psychological safetyātogether. If you're a leader aiming for lasting change (not just more projects), I help organizations:
- Engage people at all levels in sustainable improvement
- Shift from fear of mistakes to learning from them
- Apply Lean thinking in practical, people-centered ways
Interested in coaching or a keynote talk? Letās talk.
Join me for a Lean Healthcare Accelerator Trip to Japan! Learn More
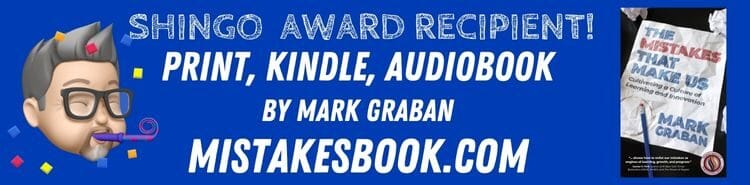
Hi Mark,
hi Norman,
thanks for the great podcast on this exceptional book:-)
@Norman, the mentioning of setting up discussion groups just makes me mention the group “Lean Thinking” at http://www.xing.com/net/lean. To get the ideas into practice I organize the 2nd meeting (Lean Thinkers Meeting) in Frankfurt (in an open space format) with people from the group in order to exchange ideas, try out certain things like lean games and alike.
Everybody -even though it is a more European focused group right now expanding slowly around the world;-)- is invited to take part of the discussion.
Just leave me a PM, if you would like to participate and I will send you an invitation.
Cheers
Ralf
PS.: Mark the podcast has pushed me a little bit towards finishing the review;-) THANKS;-))
Comments are closed.