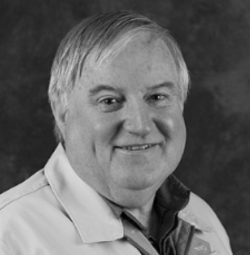
Joining me for Episode #334, all the way from
We were able to spend a lot of time talking when I participated in Honsha's Executive Development Mission trip to Japan late last year.
One thing we talked about quite a bit was Barry's experience with Toyota being “a development company,” as I blogged about here.
In our discussion, Barry talks about why he was “skeptical” about Lean before he joined Toyota. But, he evolved as Toyota continues to evolve. Why is Barry afraid that Lean (outside of Toyota) might get stuck in the past? We'll talk about all of that and more.
Streaming Player:
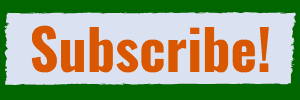
For a link to this episode, refer people to www.leanblog.org/334.
For earlier episodes of my podcast, visit the main Podcast page, which includes information on how to subscribe via RSS, through Android apps, or via Apple Podcasts. You can also subscribe and listen via Stitcher or Spotify.
New! Subscribe and listen with Spotify.
Questions, Topics, and Links:
Q: Can you please introduce yourself… before Toyota, what you did at Toyota, and how that came to an end…
A brief work history before Toyota
Outline of what I did at Toyota
The closure of Automotive and some of what I am working on now
Q: Can you elaborate on being skeptical about Lean at first? Was it going to be “extra work” for him at the company before Toyota?
Q: “many of the listeners will have people in their
Another good point to discuss. Here I will talk about what I think lean is in its most basic. “There's a risk that Lean becomes stuck in the past… Toyota is always changing.” Toyota restructured last year and the TPS group was moved out of manufacturing since TPS is about more than manufacturing.
Q: Point #1 of The Toyota Way is about making decisions with the long-term perspective, even at the expense of the short-term… but organizations that say they are copying Toyota via “Lean” rarely ask about how they can combine more long-term focused…
“Toyota's very good at managing paradox.”
Barry McCarthy
Next theme that will be an easy segue into the philosophy of lean and the heart of long term thinking – I am going to talk to some key points from Sakichi Toyoda and how what he said and did is still very relevant today and into the future.
Are there parallels between Sakichi Toyoda and Steve Jobs?
Q: What are some of the differences that you see between Toyota and other companies? – Here I will identify Organising – one of the points I spoke about in Japan.
I am going to follow with Developing and HRD and integration patterns that help developing – I will give an example of FMDS or Floor Management Development Systems.
“Eiji Toyoda” was good at balancing hard-liners and soft-liners.”
In the 1990s, Toyota shifted more toward soft-liners.
Quality Circles are a development system.
Are “hundreds of KPIs” too many?
Q: Can you talk more about the Australia plant closures and your transition?
Q: What are you doing now?
Thanks for listening!
What do you think? Please scroll down (or click) to post a comment. Or please share the post with your thoughts on LinkedIn – and follow me or connect with me there.
Did you like this post? Make sure you don't miss a post or podcast — Subscribe to get notified about posts via email daily or weekly.
Check out my latest book, The Mistakes That Make Us: Cultivating a Culture of Learning and Innovation:
This is an excellent podcast. Very informative.
Thanks, Bob.