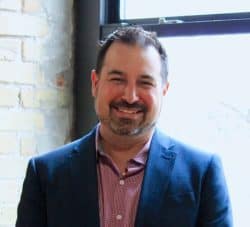
Joining me today for Episode #332 is Jason Burt, owner of EHIP Consulting. Jason is a Lean consultant and business coach with an extensive and diverse background, including a manufacturing career where he has led and coached organizations to increased levels of efficiency and performance. Using the Toyota Production System (TPS) approach has allowed him to positively change cultures to achieve sustainable improvements.
During his time at Herman Miller, Jason spent 18 months learning TPS directly from Toyota as a Toyota Lean Consultant. Toyota and Herman Miller were in a partnership during his time with the company, which allowed him to receive direct coaching from Toyota Senseis for the entire 16 years.
I was interested in talking with Jason about what it was like learning from Toyota's TSSC organization (a group that has done great work with a UCLA eye clinic and a food bank, to name two that I've featured on the blog). We talk about a wide range of topics, including common misunderstandings about TPS and Lean, the Toyota goals of developing people and their clients (knowing results will follow), and how he sometimes has to adapt to work with clients and their expectations. I hope you enjoy the conversation!
Streaming Player:
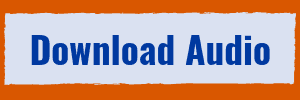
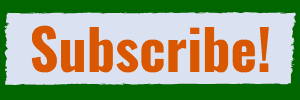
For a link to this episode, refer people to www.leanblog.org/332.
For earlier episodes of my podcast, visit the main Podcast page, which includes information on how to subscribe via RSS, through Android apps, or via Apple Podcasts. You can also subscribe and listen via Stitcher or Spotify.
New! Subscribe and listen with Spotify:
Questions, Topics, and Links:
- Find Jason on LinkedIn
- Find Jason on Twitter
- Jason's blog
- How did you first get introduced to Lean and TPS?
- Do you see Lean and TPS as being synonyms or are there differences out there?
- Why Lean?
- Tell us about the Herman Miller Production System… what was it like to be an internal consultant / coach?
- What were some of the successes and benefits of Lean at Herman Miller?
- What were some of the struggles and challenges?
- Mistakes and lessons learned, in the spirit of “Practicing Lean?“
- Why were there “two factions” where one facility was being coached by Toyota and another had a consultant who used “kaizen workshops” primarily?
- What are some misunderstandings that you've seen about Lean?
- Different styles vs. misunderstandings?
- “Lean and Six Sigma are two separate things”
- What was it like being coached by TSSC? – “Getting in the trenches”
- What was your opportunity to work directly for TSSC for a period?
- “One of only three HMI (Herman Miller) employees (out of 6000) commissioned to spend time with Toyota in order to strengthen Herman Miller's TPS learning”
- A TSSC employee was on site for 18 months, paid for by Herman Miller
- Goals: Developing people and their clients… results will follow
- Different than focusing on “ROI & results” first
- What was your opportunity to work directly for TSSC for a period?
- How did the culture and management system change at Herman Miller?
- What have you done since Herman Miller?
- What is it like introducing Lean / TPS to different companies?
- “Unfortunately, I have to adjust my style sometimes… try to find the right clients.”
- What's the difference or opportunity in being an interim executive?
- How can companies help keep manufacturing in the USA by using the Lean approach
- Why is this important?
- How can people learn more about your work and contact you online?
Another Podcast with Jason Burt:
Thanks for listening!
What do you think? Please scroll down (or click) to post a comment. Or please share the post with your thoughts on LinkedIn – and follow me or connect with me there.
Did you like this post? Make sure you don't miss a post or podcast — Subscribe to get notified about posts via email daily or weekly.
Check out my latest book, The Mistakes That Make Us: Cultivating a Culture of Learning and Innovation: