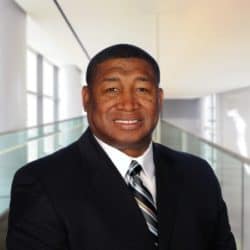
My guest for Episode #293 of the podcast is a dynamic speaker and manufacturing leader, Billy R. Taylor. I saw him speak a few years ago at a Shingo Prize Conference and I've wanted to get him on the podcast ever since.
He's currently the Director of Commercial, Off Highway, and Support Manufacturing North America for The Goodyear Tire & Rubber Company. Over the past 20 years, he has risen from “the lowest level of the organization,” up through the manufacturing leadership ranks at Goodyear, including time as a Plant Director at facilities in Oklahoma and North Carolina.
He's been “engaged in Lean” for over 15 years and he is a Six Sigma Master Black Belt. Billy has a BS in in Electrical Engineering from Prairie View A&M University and an MBA from Baker University.
Billy was very giving of his time and we talked for over 75 minutes, so I'm breaking this up into two parts, with Part 2 available now. Today, we talk about how he got started with Lean, the shift from tools- and event-based Lean to a culture focus, how to build a sense of ownership, servant leadership, strategy deployment, employee recognition and more.
'In the absence of ownership and clarity comes blame.' -- Billy Taylor Share on XStreaming Player (Run Time 34:01)
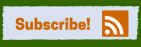
For a link to use for this episode, refer people to www.leanblog.org/293
For earlier episodes of my podcast, visit the main Podcast page, which includes information on how to subscribe via RSS, through Android apps, or via Apple Podcasts. You can also subscribe and listen via Stitcher.
Links, Topics, Questions, and Quotes:
- How did you get started with Lean?
- How did you move beyond a “tool-based” and an “event-based” approach to Lean?
- “The culture piece is what really intrigued me”
- Learning from AME and Shingo
- How did thinking about Lean more as a culture help?
- “Instead of DMAIC, we had DI — we went from Define right to Improve.”
- How better “governance” leads to better sustainment
- “Once you change the guard, how do you guard the change?”
- How do you use strategy deployment to create a sense of ownership?
- Why managers should embrace the idea that “I work for you” rather than “you work for me.”
- “Some managers look for facts that justify their opinions” and that will “demoralize their team.”
- “Not everything that counts can be counted, however what should be counted must be.”
- “Where are the gaps in the process vs. where are the gaps in the numbers?”
- “I'm recognizing the process, but embracing the individual.”
- How do you create and reinforce a Lean culture in an organization? How has your role changed and evolved?
- “The core process has not changed for me” — define winning, align to win (helping people understand what they own), execution (how do we know if we're winning or not?)
- Do we celebrate the “red?” — use the red as a way to improve instead of “a hammer”
- “In the absence of ownership and clarity comes blame.”
- How do you work to create trust?
- How do you help employees know what the strategy is?
- Moving from getting “the shrug” to 90% of employees understanding the boards
- How do you find the “gold mine” in “the hidden factory?”
- The cartoon of mine that Billy found and talked about
- How do you create an environment where it's safe to change?
- Billy's story about being exposed to a different type of culture visiting a hospital…
- How do you help people through the discomfort of change?
- “You can't teach what you don't know and you can't lead where you won't go.”
- Their “formula for success: Strategy + Execution = Results”
- Why do so many companies fail to execute? Because people don't know what they have ownership of.
- Goodyear's CEO: “You can't manage a secret.”
Video of Billy Taylor:
What do you think? Please scroll down (or click) to post a comment. Or please share the post with your thoughts on LinkedIn – and follow me or connect with me there.
Did you like this post? Make sure you don't miss a post or podcast — Subscribe to get notified about posts via email daily or weekly.
Check out my latest book, The Mistakes That Make Us: Cultivating a Culture of Learning and Innovation:
Very interesting interview and looking forward to the second part. Tools are the easy part (and not always that easy to implement) but we sometimes really struggle to dive into the cultural aspects of lean and understanding that’s what you need to do to have a successful lean enterprise.