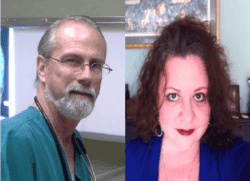
Episode #254 is interesting to me for a number of reasons.
For one, I have a “guest co-host” joining me for the first time. He's Chip Ponsford, DVM, a doctor of veterinary medicine and former practice owner who I've gotten to know here in Texas over the past few years.
Chip has been a great student of Lean, following a path similar to that of Sami Bahri, DDS (“The World's First Lean Dentist”) in reading the “classic” Lean books from industry because there had been nothing written about Lean in VetMed. I've been helping Chip with his “Lean Vets” blog and we've collaborated in a few other ways to promote Lean in veterinary medicine.
Our guest is Samantha (Sam) Parrett, the Director of Business & Administrative Services at North Carolina State University Veterinary Health Complex. Chip and I ran across Sam's name in one of the few articles we've found on Lean in VetMed:
NC Vet College Dives Into Lean Training
In the podcast, we'll discuss their story at NC State and the potential for Lean to make the jump into veterinary medicine more broadly. We hope you enjoy the discussion.
Streaming Player (Run Time 39:45)
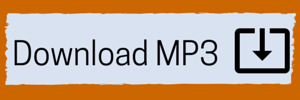
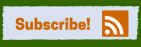
For a link to this episode, refer people to www.leanblog.org/254.
New! Read the transcript
Topics covered and links related to the podcast:
- About North Carolina State Veterinary Hospital. Size, # of doctors/staff, case load?
- North Carolina State Vet Hospital recently experimented with Lean. As Taiichi Ohno wrote, “Start from need.” What “need” prompted y'all to consider Lean?
- How did you learn about Lean as a possible solution to your issues?
- What attracted you to Lean?
- What Lean methodologies did you utilize?
- Wow did you document the value stream? Software, paper/pencil, Post-it notes?
- How long did it take to work out the issues between anesthesiology and surgery? How did you facilitate this? Who all was involved?
- Have you considered implementing a complete Lean initiative and transformation; teaching Lean to the entire staff and creating a culture of continuous improvement and organizational learning?
- NC State Veterinary Hospital is a large teaching hospital. It is easy to understand how communications and coordinating might pose some difficulties, but what about the typical private veterinary practice? Do you think the same kinds of kinds of gains are possible for them? What would you tell veterinarians that may or may not have contemplated Lean for their own practices?
For earlier episodes of my podcast, visit the main Podcast page, which includes information on how to subscribe via RSS, through Android apps, or via Apple Podcasts. You can also subscribe and listen via Stitcher.
Thanks for listening!
What do you think? Please scroll down (or click) to post a comment. Or please share the post with your thoughts on LinkedIn – and follow me or connect with me there.
Did you like this post? Make sure you don't miss a post or podcast — Subscribe to get notified about posts via email daily or weekly.
Check out my latest book, The Mistakes That Make Us: Cultivating a Culture of Learning and Innovation:
[…] Lean Vets Transcript – Podcast #254 – Lean in Veterinary Medicine […]