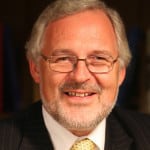
Returning to the podcast after his first appearance in Episode #188 is Daniel T. Jones, founder and chairman of the UK-based Lean Enterprise Academy. You can find him on Twitter now as @DanielJonesLean.
Dan collaborated with Jim Womack on the books The Machine That Changed the World, Lean Thinking, and Lean Solutions and published other books through the LEA. He is also a senior advisor to the relatively new website and journal “Planet Lean.”
In this episode, we talk about some of the progress being made in areas outside of manufacturing. Dan says there's “awareness everywhere” but asks if there's “real depth” in Lean progress? We'll discuss how we can reframe Lean for the public sector and healthcare as a way of going beyond mere cost cutting programs. What does Dan seeing happen in software and startup sectors with Lean in companies like Spotify in Sweden? How is interest in the core “respect for people” leading to a search for “more holistic management methods?”
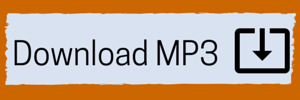
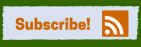
Scroll down to read a partial transcript.
For a link to this episode, refer people to www.leanblog.org/216.
For earlier episodes of my podcast, visit the main Podcast page, which includes information on how to subscribe via RSS or via Apple Podcasts. You can also subscribe and listen via Stitcher.
Some videos with Dan:
Feedback & Comments:
If you have feedback on the podcast, or any questions for me or my guests, you can email me at leanpodcast@gmail.com or you can call and leave a voicemail by calling the “Lean Line” at (817) 372-5682 or contact me via Skype id “mgraban”. Please give your location and your first name. Any comments (email or voicemail) might be used in follow ups to the podcast.
Partial Transcript:
Mark Graban: Hi, this is Mark Graban. Welcome to episode 216 of the podcast for February 20th, 2015. Returning to the podcast after his first appearance back in episode 188 is, Dan Jones. He is the founder and chairman of the Lean Enterprise Academy.
Dan, of course, collaborated with Jim Womack on the books, The Machine That Changed the World, Lean Thinking, and Lean Solutions, and helped publish many other books through the Lean Enterprise Academy. He's also a senior advisor to the relatively new website “Planet Lean.”
In this episode, we're going to talk about some of the progress being made in areas outside of manufacturing. Dan says there's awareness everywhere, but he asks if there's real depth in Lean progress outside of manufacturing.
We'll discuss how we can reframe Lean for the public sector and healthcare as a way of going beyond just cost-cutting programs. What does Dan see happening in software and startup sectors in companies like Spotify in Sweden? How is interest in the “core respect for people” principle leading to a search for more holistic management methods?
Those are some of the themes we'll explore in this episode. To find all episodes and information about subscribing, if you'd like to get notified about the great episodes that we've got coming up soon and in the future, you can go to Leancast.org.
Mark: We're sitting here more than 25 years since the term Lean Production was coined, and obviously you were part of those efforts. I'm curious though. You're here in 2015. What some of the things are there that you're seeing that interest you in areas beyond manufacturing sectors? What's going on with Lean?
Dan: Part of my destiny in the partnership with Jim early on after we coined the term into the MIT studies was that, living the UK, our manufacturing industry in the '80s and '90s was imploding. So, it was an awful lot of future for Lean beyond the few Japanese plants that came here.
I had to quite quickly go out of manufacturing and explore taking Lean to other sectors like construction, healthcare, retail and aerospace and later on public sector. I spent a lot of time trying to find pioneers with whom to experiment and see how we could translate the concept into the language and address the needs of different sectors.
That's been my destiny in life. We can claim we've spread awareness everywhere, and there're very few sectors now that haven't been touched by some form of Lean activity. That doesn't mean that we've created depth of real experience and practice with Lean. That's still to come in many sectors.
We've spread it widely and we've spent a lot of time over the last 15 years deepening our understanding of the management system necessary to support the Lean tools that we all learned about 25 years ago
Mark: You're right, awareness is a first step, but what do we do beyond people being able to use some terminology? It seems to happen in other industries, people say, “This Lean stuff seems simple. I'm sure that we've done that now.” How do you gauge that depth of real progress in different industries?
Dan: It's interesting. You could reflect on the TWI stages of learning basic job instruction. We've done the awareness steps. Quite a lot of people can do Lean with a lot of help, not too many can do Lean on their own without help, and then there are very few people who are at a point where they can teach Lean to others.
You can apply that not just to people, but also to sectors. I would say healthcare and public sector are more recent into this field, last 10, 15 years at the very most. Really, mostly over the last 10 years. And they've gone through the big consultant led programs.
We've seen and I'm sure you've seen a dozen of those. At some point you get a call saying, “We've spent the money. We've had the consultants, we did a lot of activity, and people are very energized by it.”Actually, our finance director in the end said, “Where's the result? What's all this led to?”
That's a very salutary lesson that while big programs create awareness and engage people, they don't deliver results as promised. That's where we're at in the public sector and healthcare right now.
Mark: I would think there's a risk that awareness is either partial awareness, or it creates the risk of misunderstanding, to your point about engagement. Awareness doesn't necessarily engage people. People combine old managerial habits with the Lean concept. “I'm going to use Lean to tell people they need to rearrange their work space,” as opposed to really engaging people.
Dan: Yes, that is absolutely the case. There is a danger with Lean that you learn a little and you think you know it all. Whereas, in fact, a true approach to Lean means that the more you learn the more you realize there is to learn.
This is a developmental path. I think you're right that engagement quickly fizzles when it's just tools and when it's just supported by experts from outside. Or when it is being rolled out across the organization in classic Six Sigma style as a thing that people don't think about too much. “Just listen to the training sessions and just do.”
That's a very Taylor-ist approach to managing change. People get pretty cynical when Lean is used that way.
What do you think? Please scroll down (or click) to post a comment. Or please share the post with your thoughts on LinkedIn – and follow me or connect with me there.
Did you like this post? Make sure you don't miss a post or podcast — Subscribe to get notified about posts via email daily or weekly.
Check out my latest book, The Mistakes That Make Us: Cultivating a Culture of Learning and Innovation:
Thanks for bringing this interview to us.
There were many good insights from Dr. Jones.
I like the one where he said something like leaders learn best when they’re helping (teaching, coaching?) others to learn.
I think you could turn that into a good litmus test for how engaged leaders are.
[…] Podcast #216 Dan Jones, Lean Outside of Manufacturing, listen here […]