There's a meme going around — maybe you've seen it — where a kid on a bike jams a stick into his own front wheel, crashes, then blames something else entirely.
It's funny… until you realize how often organizations do something similar with their Lean initiatives.
I was recently reminded of this image when reflecting on a familiar pattern I've seen — and sadly, still see — especially in healthcare settings:
Organizations say they want to embrace Lean. Lean is supposed to be about improving Safety, Quality, Delivery, and Cost — in that order. Hopefully the executives read that or were taught that. Or the consultant they hired got the job by promising big cost savings.
So, instead of a balanced approach, the focus quickly narrows to just one thing: Cost.
So I created this version of the meme (which is also on my LeanMemes.com site):
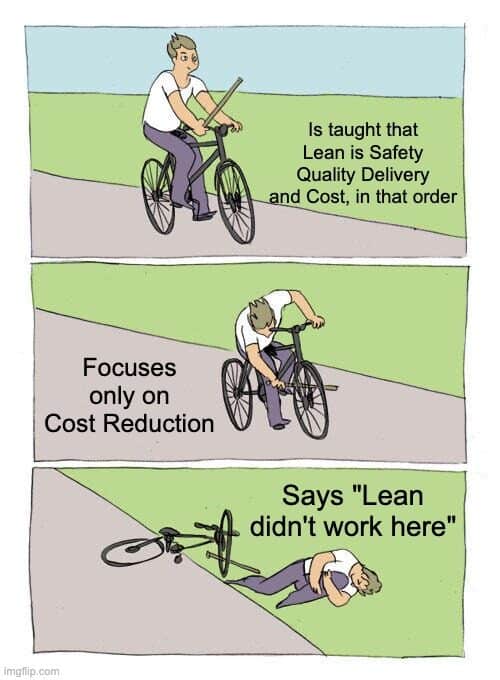
Why Cost-First Lean Fails
Let's step back and consider what Lean is supposed to be. In a truly Lean organization — like Toyota at its best — the emphasis is first and foremost on people and process. That means creating an environment where employees are respected, heard, and empowered to solve problems — a culture of Psychological Safety. Where quality and safety aren't just boxes to check, but deeply embedded values.
Cost improvement happens, yes — but as a result of doing the right things well. Improving safety, quality, and on-time delivery leads to lower cost. Cost is a lagging indicator, not the primary target.
Yet I've seen too many healthcare organizations that talk Lean but walk something different:
- Frontline staff are told to “find waste” — but only if it reduces spending.
- Improvement boards go up — but ideas are only pursued if they save money.
- Executives talk about respect for people — but then cut jobs in the name of efficiency.
It's like getting a new bike, telling everyone how great it's going to be, and then jamming a stick into the wheel before the first ride.
Related Post on the Failed Cost Focus:
What Actually Motivates People
Let's be honest: Nurses, medical techs, housekeepers, and other frontline healthcare workers don't come to work fired up to “hit the budget target.”
What inspires them is delivering better patient care. Reducing frustration. Improving safety. Being part of a team that learns and grows together.
When you align improvement efforts with what people already care about — and give them the time, tools, and psychological safety to experiment — amazing things happen. Engagement goes up. Ideas flow. Costs improve, organically.
But when leaders lead with cost, it creates fear and skepticism. People shut down. Improvement stalls–or never begins.
A Better Way: SQDC, in That Order
There's a reason Toyota and many other Lean organizations prioritize their metrics in this order:
Safety –> Quality –> Delivery –> Cost
That sequence is a philosophical commitment.
- If we don't protect safety, we fail.
- If we don't deliver quality, we fail.
- If we can't deliver reliably and on time, we fail.
- If we do all those things well, that leads to lower cost.
Start with cost and you've already lost.
Related Posts on SQDC:
The Mistakes That Make Us… or Break Us
In my book The Mistakes That Make Us, I talk about how learning organizations aren't just good at solving problems — they're great at learning from why they failed in the first place.
If your Lean initiative didn't take off, or fizzled out after a promising start, ask yourself:
- Did we prioritize cost over everything else?
- Did we cultivate Psychological Safety for people to speak up?
- Did we align improvement efforts with mission and purpose of frontline staff?
If not — well, there's your stick in the spokes.
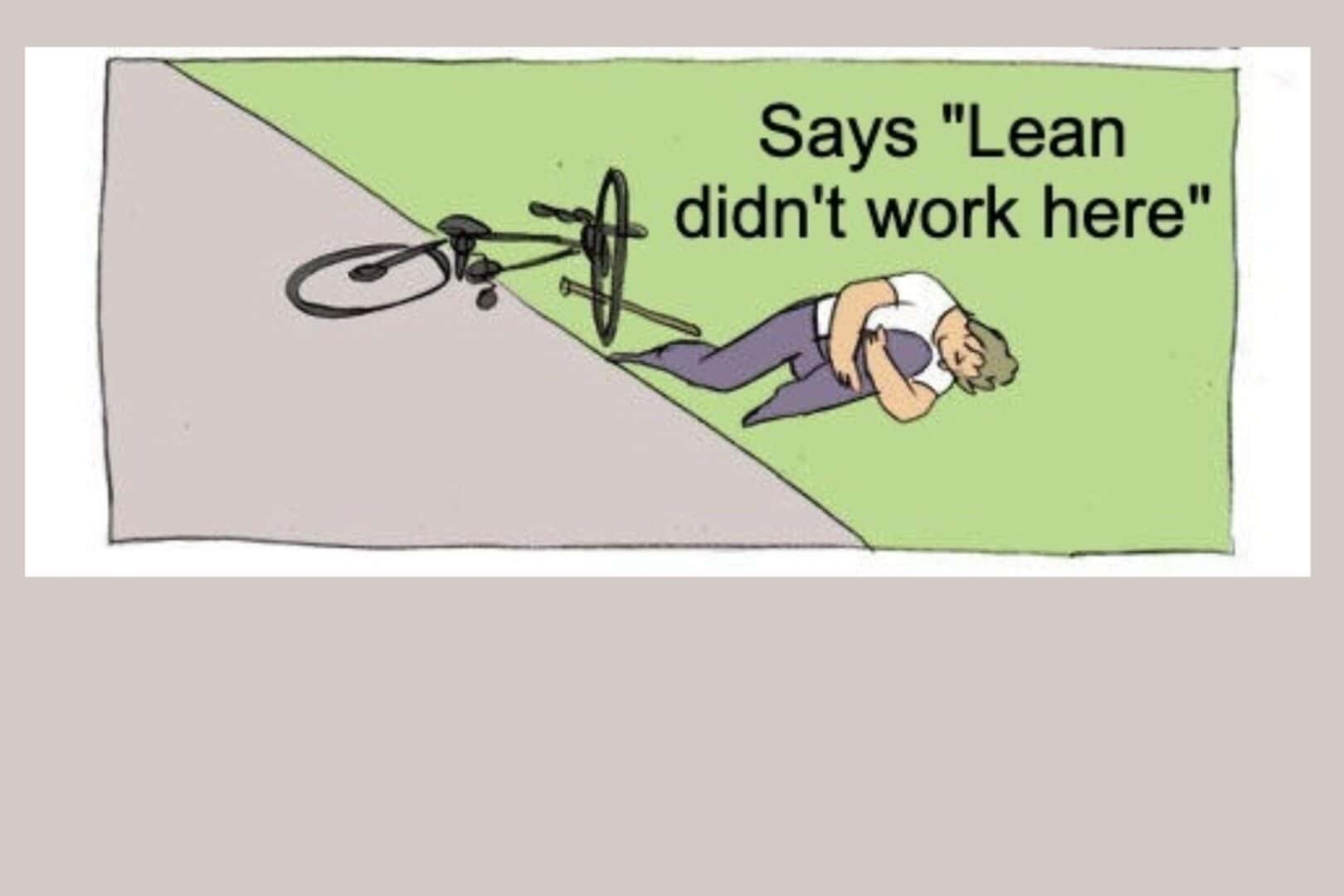
The good news? That mistake can become a turning point. A moment to realign, refocus, and re-commit to a Lean approach that respects people and builds sustainable results.
Let's not sabotage our own efforts. Let's take the stick out of the wheel — and keep moving forward, together.
Have you seen organizations make this mistake — or recover from it?
What do you think? Please scroll down (or click) to post a comment. Or please share the post with your thoughts on LinkedIn – and follow me or connect with me there.
Did you like this post? Make sure you don't miss a post or podcast — Subscribe to get notified about posts via email daily or weekly.
Check out my latest book, The Mistakes That Make Us: Cultivating a Culture of Learning and Innovation: