During Katie Anderson‘s #JapanStudyTrip this past November, a participant shared an observation with me that resonated deeply:
“The biggest challenge is our blame culture. It's easier for people to do nothing because they don't get in trouble.
But if they make a mistake, they get punished.
And our company is successful enough that there's not a compelling reason for top leaders to change the culture.”
This isn't a story from the U.S., but the feeling is universal.
A workplace culture where individuals are punished for mistakes–especially when those mistakes have systemic causes–is a significant barrier to progress.
It's a global challenge, and addressing it requires rethinking how we approach leadership and learning.
The Cost of Blame and the Need for Safety
Organizations that cling to blame-based cultures face hidden costs:
- missed opportunities for innovation,
- disengaged employees, and
- the perpetuation of systemic issues.
When people fear punishment, they play it safe. Silence becomes their shield–but at the cost of continuous improvement.
If we aim to build a Lean culture, it must rest on a foundation of Psychological Safety. In an environment with high enough levels of Psychological Safety, people generally feel safe speaking up about problems, sharing ideas, and experimenting without fear of retribution.
Without this safety, even the best Lean tools and techniques will fall flat.
Lessons from Japan: A Different Approach
The companies we visited in Japan provided a stark contrast. Across the board, we saw leaders embracing these principles:
- Encouraging Open Communication: Leaders aimed to cultivate environments where everybody felt safe to speak up about problems and ideas without fear of being blamed, punished, or ignored.
- Focusing on Systemic Causes: Instead of blaming individuals for errors, the emphasis was on understanding and addressing systemic causes.
The result? A culture of learning and improvement that's deeply embedded in their organizations.
A Leadership Resolution for the New Year
As we enter a new year, let's reflect on how we lead and support our teams. Here are two resolutions for leaders aspiring to foster continuous improvement:
- Help people feel safe speaking up. Cultivate an environment where team members are empowered to share concerns, ideas, and mistakes openly. Don't just tell people they should feel safe.
- Avoid blame. When things go wrong, focus on understanding and addressing the system rather than finding someone to punish.
These are not just abstract principles; they are practical, actionable steps. They require a shift in mindset but offer the potential for profound transformation.
Follow the examples that former Toyota leaders Isao Yoshino and David Meier shared in their episodes of the “My Favorite Mistake” podcast.
Isao Yoshino's Story: A Lesson in Learning and Reflection
Isao Yoshino spent four decades in leadership roles at Toyota, where he witnessed and lived the company's deep commitment to learning from mistakes. Early in his career, Yoshino made a mistake while overseeing part of the painting process, putting the wrong chemical into a machine. The error resulted in flawed paint jobs for 100 cars, which required rework and additional costs. In many organizations, such a mistake might lead to blame, reprimand, or even termination. However, Toyota's response was fundamentally different.
Rather than blaming him, Yoshino's supervisors apologized for putting him in that position… and encouraged him to help examine the root causes of the mistake and identify ways to prevent it from happening again. This experience reinforced a core Toyota principle: problems are opportunities for improvement. Instead of assigning personal fault, the company viewed errors as systemic issues, creating space for reflection and learning. Throughout his career, Yoshino was encouraged to experiment, reflect on his methods, and continuously refine his approach.
Yoshino came to understand that Toyota's culture was built on the foundation of Psychological Safety and iterative learning. Managers didn't expect perfection from their employees but demanded an honest effort to reflect and improve. This approach taught Yoshino to embrace vulnerability and view mistakes not as personal failures but as critical learning opportunities. Over the years, he internalized Toyota's commitment to learning, making it a cornerstone of his leadership style.
David Meier's Story: Transforming Mistakes into Growth
David Meier joined Toyota as a production manager in Kentucky, where he experienced firsthand the company's unique approach to mistakes. During his tenure, he also oversaw an operation (molding) where the wrong chemical was added to a machine, leading to dust and powder instead of properly formed parts. Like Yoshino, David expected punitive repercussions. However, his leaders surprised him by responding differently.
Rather than reprimanding him, his supervisors treated the incident as a valuable learning opportunity. David was asked to investigate why the error had occurred and to think critically about the broader systemic issues that might have contributed to the mistake. With the guidance of his leaders, he analyzed the processes that allowed the defective parts to be made and proposed improvements to prevent similar mistakes in the future.
This experience became a defining moment in David's career. He saw how Toyota's culture emphasized blame-free problem-solving, where the focus was on understanding and fixing processes rather than assigning fault to individuals. His supervisors recognized that the mistake stemmed not from negligence but from flaws in the system–a lesson that David carried forward as he became an advocate for Lean principles.
David later transitioned into consulting and teaching Lean methodologies, helping other organizations adopt Toyota's systems-thinking mindset. His personal experience of turning a mistake into a growth opportunity became a key part of his teachings. By sharing his story, David highlighted the importance of creating environments where employees feel safe to admit errors and focus on improvement.
Parallels and Connections:
- Systemic Thinking: Both Yoshino and David encountered mistakes that revealed underlying process flaws. Toyota's culture directed them to investigate process-based root causes rather than focus on individual error, emphasizing the importance of systems thinking in problem-solving.
- Psychological Safety: Toyota's leadership created an environment where admitting mistakes was not only safe but encouraged. This empowered both individuals to take ownership of their actions, fostering a proactive learning culture.
- Iterative Learning: Their stories illustrate Toyota's iterative approach–experimenting, learning from mistakes, and continuously improving. This iterative mindset drives both personal and organizational growth.
- Global Impact: These lessons extend beyond Toyota, shaping how leaders in other industries view and handle mistakes, highlighting the universal applicability of learning-focused cultures.
By embracing mistakes as learning opportunities, both Mr. Yoshino and David demonstrate the transformative power of Psychological Safety and systemic thinking in fostering a culture of improvement. These principles encourage organizations to treat mistakes as catalysts for innovation rather than setbacks.
Read my blog posts from all of my Japan tours
Both Mr. Yoshino and David's experiences reflect Toyota's commitment to fostering a culture of Psychological Safety, where mistakes are seen as critical tools for learning. While Yoshino's story emphasizes leadership development over decades, David's account shows how Toyota's principles transcend cultures and geographies, influencing individuals and industries worldwide. Their experiences illustrate that embracing mistakes leads to greater innovation, stronger systems, and more engaged employees–transforming organizations into engines of continuous improvement.
Moving Forward
Creating a blame-free, psychologically safe workplace is a journey. It requires consistent effort and a willingness to challenge entrenched norms. But the rewards–a more engaged team, better outcomes, and a culture of innovation–are well worth the effort.
Let's make this the year we lead with curiosity, compassion, and a commitment to continuous improvement–with Psychological Safety as the foundation. Let me know if you'd like me to help you on that journey.
What are your leadership resolutions for the year? Share your thoughts in the comments below.
Please scroll down (or click) to post a comment. Connect with me on LinkedIn.
Let’s work together to build a culture of continuous improvement and psychological safety. If you're a leader looking to create lasting change—not just projects—I help organizations:
- Engage people at all levels in sustainable improvement
- Shift from fear of mistakes to learning from them
- Apply Lean thinking in practical, people-centered ways
Interested in coaching or a keynote talk? Let’s start a conversation.
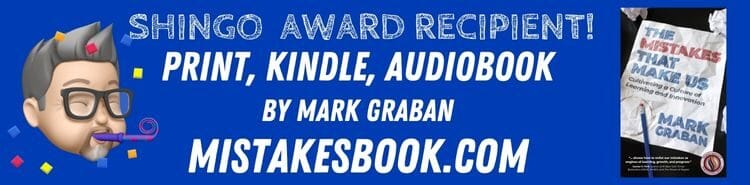
[…] Beginning the New 12 months with World Management Resolutions: Constructing a Basis of Psychological… – Mark Graban says if we purpose to construct a Lean tradition, it should relaxation on a basis of Psychological Security the place folks usually really feel secure talking up about issues, sharing concepts, and experimenting with out worry of retribution. […]