I'm thrilled to announce that I'll be presenting a 90-minute “intensive” session at the 2025 Health Systems Process Improvement (HSPI) conference, organized by the Society for Health Systems.
This year's event will take place in Atlanta, and if you're passionate about making a meaningful impact in healthcare and process improvement, I encourage you to join us!
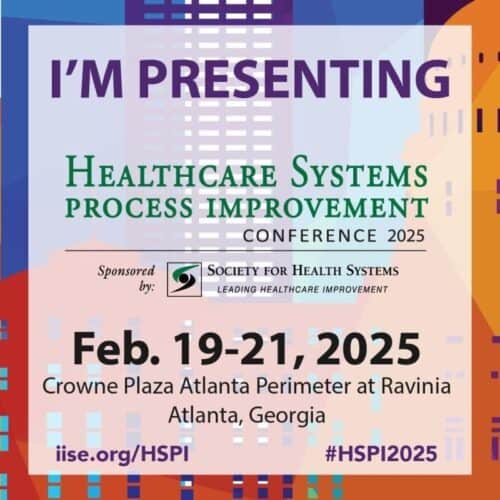
During this session, I'll revisit and expand upon the workshop I conducted two years ago, focusing on Dr. W. Edwards Deming's famous Red Bead Experiment and its profound implications for Lean management and process improvement.
Why the Red Bead Experiment?
For those unfamiliar, Deming's Red Bead Experiment is a thought-provoking and participatory exercise that vividly demonstrates how systemic issues often masquerade as individual performance problems. Workers in the experiment (acting as “willing workers”) are tasked with “producing” beads from a container using a prescribed process. The red beads are considered “defects,” and the workers are told to avoid them.
The system is inherently flawed, but despite this, the workers are praised or blamed for outcomes beyond their control.
This exercise drives home key lessons about:
- The dangers of focusing on individual blame rather than systemic improvement.
- The importance of understanding variation within a system.
- Poor management practices often exacerbate systemic issues rather than addressing their root causes.
Connecting the Experiment to Process Behavior Charts
One of the tools that dovetail perfectly with lessons from the Red Bead Experiment is Process Behavior Charts (PBCs), a concept central to my book Measures of Success: React Less, Lead Better, Improve More. PBCs help us separate “signal” from “noise” in performance metrics, enabling leaders to focus on meaningful trends rather than overreacting to normal variation.
For example, imagine a healthcare setting where patient satisfaction scores fluctuate slightly each week. Without understanding the natural variation in the system, leaders may overreact to a small drop or celebrate a minor increase, wasting time and energy that could be spent on genuine system improvements.
By combining the lessons of the Red Bead Experiment with Process Behavior Charts, leaders can better understand:
- When to react to data and when not to.
- How to identify systemic issues that require improvement.
- Why managing a system requires addressing root causes instead of assigning blame.
Don't react to noise. DO react to signals. What do signals look like? See below:
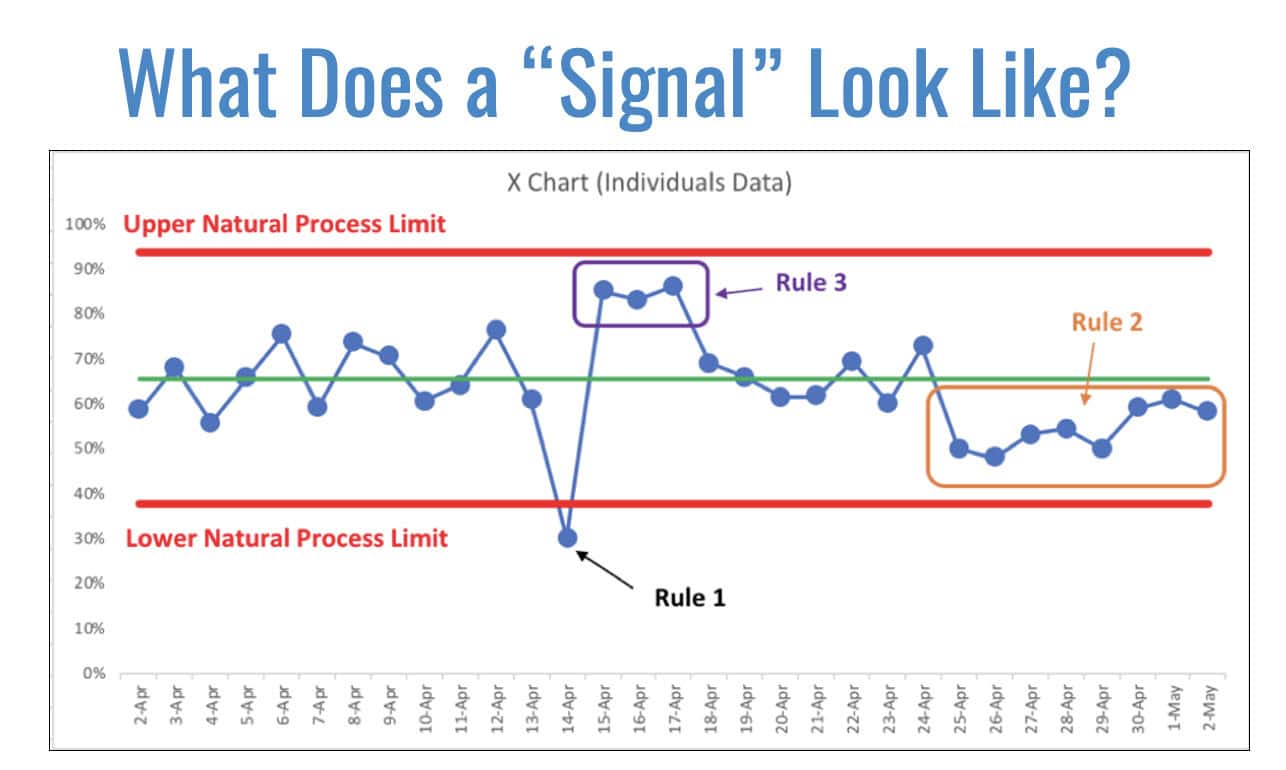
Join Me in Atlanta
This session is part of a larger conference that I've attended almost every year since 2006. It's one of the best gatherings for healthcare professionals, process improvement experts, and Lean practitioners to exchange ideas and learn from one another. Whether you're new to process improvement or have years of experience, there's something at HSPI for everyone.
Let's learn together how to react less, lead better, and improve more. I hope to see you there at #HSPI2025!
More Posts about “Red Beads”
Please scroll down (or click) to post a comment. Connect with me on LinkedIn.
Let’s work together to build a culture of continuous improvement and psychological safety. If you're a leader looking to create lasting change—not just projects—I help organizations:
- Engage people at all levels in sustainable improvement
- Shift from fear of mistakes to learning from them
- Apply Lean thinking in practical, people-centered ways
Interested in coaching or a keynote talk? Let’s start a conversation.
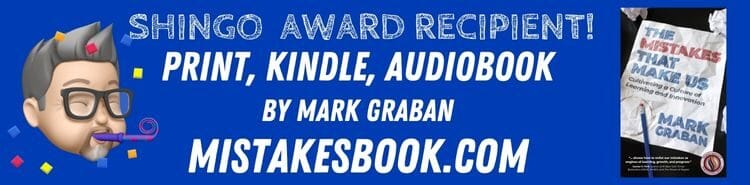
Mark, great sneak peek at your HSPI 2025 session! One of the best ways to highlight the dangers of holding people accountable for systemic problems is through the Red Bead Experiment. This lesson is much more valuable when tied to Process Behavior Charts; it’s all about concentrating on the real signals and avoiding distractions. Your method of assisting leaders in differentiating between substantial trends and natural variance is just what the healthcare industry needs to promote long-term progress. I’m eager to see how you make these ideas work together and encourage more astute, data-driven leadership.