As a Lean practitioner, I found the Wall Street Journal article about Ryan DeLand, the 39-year-old leader of Whirlpool's washing machine plant in Clyde, Ohio, to be fascinating. Here's a free link:
A Day in the Life of the 39-Year-Old Factory Boss Managing 3,000 Workers
DeLand's day-to-day activities and leadership style offer valuable insights for anyone interested in operational excellence, leadership, and Lean thinking. Here are some key takeaways and reflections:
1. “Stable and Predictable” as a North Star
DeLand starts each day with the motto “stable and predictable.” In Lean terms, this reflects the pursuit of standardization and reliability as foundational elements of operational excellence. The challenge of managing a plant with 25 miles of conveyors and over 2,000 parts underscores the importance of minimizing variability and fostering flow. This philosophy aligns with Toyota's principle of creating a stable foundation before tackling higher-level improvements.
2. Leadership Through Support and Empowerment
DeLand's approach to morning meetings stood out. He observes and provides support rather than micromanaging or second-guessing his team. This behavior embodies the Lean concept of “respect for people,” enabling team members to take ownership of problems and solutions. Leaders who act as coaches rather than taskmasters create environments where employees feel valued and empowered.
3. Gemba Walks: Leadership in Action
DeLand practices “gemba walks” twice a week, a cornerstone of Lean management. He stays connected to real issues by visiting the factory floor. These interactions not only highlight the importance of problem-solving but also reinforce the value of leaders being present and engaged where value is created (the “gemba“).
A takeaway for all of us: gemba walks aren't just about observation–they're about learning, connecting, and fostering a culture of continuous improvement.
He also practices the good habit of stopping to pick up a piece of trash (something I've seen other Lean leaders do):
“He arrives and heads to a room in the center of the plant known as the hub to review the previous day's numbers, picking up stray bits of litter as he goes. A company that makes cleaning appliances should have a clean factory, he says.”
4. Prioritizing Safety and Ergonomics – “A hill to die on”
The story about the troublesome plastic sleeve exemplifies DeLand's commitment to worker safety. By experiencing the problem firsthand, he gained the perspective needed to champion change. His decision to take a stand against potential injuries demonstrates the power of servant leadership. This kind of advocacy not only prevents harm but also builds trust and morale among employees.
This reminds me of the concept of “fixing the broken systems” for frontline workers, a theme often discussed in Lean healthcare.
5. Tackling Complexity with Teamwork
DeLand's ability to manage the factory's inherent complexity–balancing assembly lines, logistics, and back shop operations–requires a systemic approach. His acknowledgment that harmony is a “team-wide effort” highlights the importance of collaboration and cross-functional problem-solving.
For Lean practitioners, this resonates with W. Edwards Deming's emphasis on systems thinking. Leaders must see the interconnectedness of processes to drive sustainable improvements.
6. Driving Innovation and Cost Savings
DeLand encourages and celebrates innovation, as seen in the tool room's cost-cutting solution for die maintenance. This reflects Lean's focus on engaging employees in identifying and solving problems, leading to both operational and financial benefits.
7. Balancing Productivity and Humanity
DeLand's focus on offering work-life balance–avoiding mandatory Sunday shifts and respecting workers' time–demonstrates thoughtful leadership in a labor-tight market (and the “respect for people” principle). This approach likely contributes to the plant's ability to attract and retain talent, even in a challenging hiring environment.
DeLand's boss, vice president of U.S. manufacturing Kristin Day, says thoughtfulness for the workforce is one mark of an effective factory leader. “It really isn't just driving business performance, but it's also understanding the people aspect of the job,” she says.
Reflections for Lean Leaders
Reading about Ryan DeLand's leadership reminds us that great Lean leaders are not just process-driven–they are people-focused. They lead by example, build trust, and create an environment where employees can thrive. Whether in a factory, a hospital, or any other industry, the principles he demonstrates–stability, empowerment, safety, teamwork, and innovation–are universally applicable.
For those of us in the Lean community, DeLand's story is a call to action: How can we better connect with our teams, foster innovation, and ensure that our systems support both people and performance?
What are your thoughts on DeLand's leadership style? Have you seen similar examples of Lean principles in action in your organization? Share your insights in the comments below.
Please scroll down (or click) to post a comment. Connect with me on LinkedIn.
Let’s work together to build a culture of continuous improvement and psychological safety. If you're a leader looking to create lasting change—not just projects—I help organizations:
- Engage people at all levels in sustainable improvement
- Shift from fear of mistakes to learning from them
- Apply Lean thinking in practical, people-centered ways
Interested in coaching or a keynote talk? Let’s start a conversation.
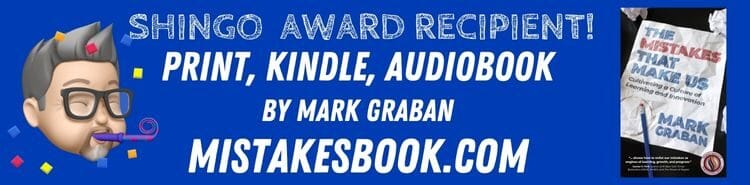
[…] WSJ Exhibits Us a Day within the Lifetime of a Plant Supervisor — Together with Lean Practices – Mark Graban discusses fascinating article about Whirlpool Plant Handle Day within the Life providing useful insights for anybody excited about operational excellence, management, and Lean pondering. […]