Scroll down for how to subscribe, transcript, and more
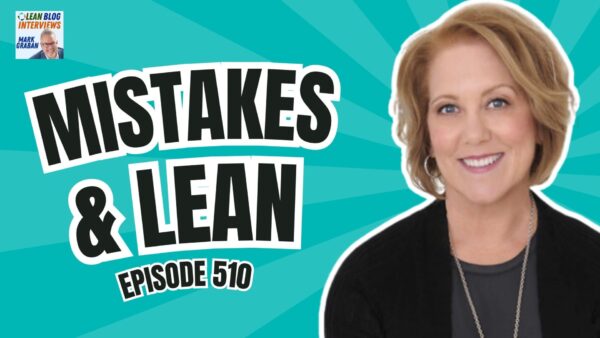
My guest for Episode #510 of the Lean Blog Interviews Podcast is Karen Martin, Founder and CEO of TKMG and TKMG Academy, appearing for the fifth time.
She is the author of books including The Outstanding Organization, Clarity First, and Value Stream Mapping.
In this episode, we discuss mistake-proofing in lean practices, exploring its significance in various industries. The conversation begins with a light-hearted discussion about the “five-timers club” and Mark's “ZERO hat” from the Patient Safety Movement Foundation, which symbolizes the goal of zero harm in healthcare.
Karen shares her extensive background in quality improvement and lean management systems, emphasizing the importance of building quality at the source. Drawing on the teachings of Dr. W. Edwards Deming and the Toyota Production System, Karen and Mark discuss the psychological impact of striving for zero harm, debating whether it is an inspiring goal or potentially demotivating.
The episode also explores real-world examples of organizations achieving zero harm and the cultural shifts required to reduce errors. Karen introduces the TKMG Academy and its comprehensive courses designed to enhance lean practices, including the new mistake-proofing course co-developed with Mark. Her passion for quality improvement and continuous learning shines through, offering listeners valuable insights into achieving operational excellence.
Questions, Notes, and Highlights:
- Why is quality such a passion for you?
- Why did you want to add the mistake-proofing course to the TKMG Academy catalog?
- What are some common barriers to achieving zero harm in healthcare?
- How do you differentiate between mistakes and errors?
- How do you handle situations where the work system isn't at fault, but the individual continues to make mistakes?
- Can you tell us more about the “slow work” movement?
- What are your thoughts on final inspection versus quality at the source?
- How do you address the challenge of maintaining standards in training and process design?
- Could you elaborate on the spectrum of mistake-proofing from 100% prevention to error reduction?
- How does the TKMG Academy help organizations with continuous improvement?
The podcast is brought to you by Stiles Associates, the premier executive search firm specializing in the placement of Lean Transformation executives. With a track record of success spanning over 30 years, it's been the trusted partner for the manufacturing, private equity, and healthcare sectors. Learn more.
This podcast is part of the #LeanCommunicators network.
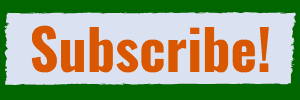
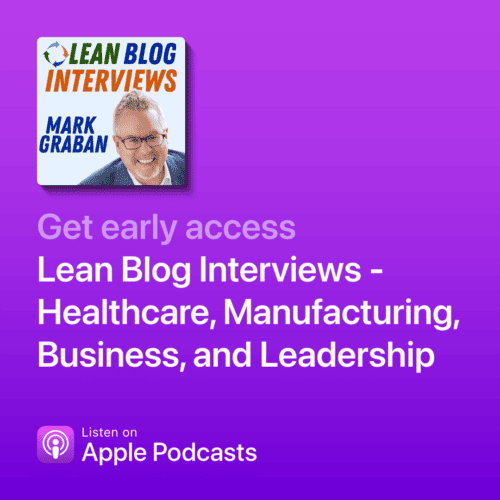
Full Video of the Episode:
Thanks for listening or watching!
This podcast is part of the Lean Communicators network — check it out!

Quotes
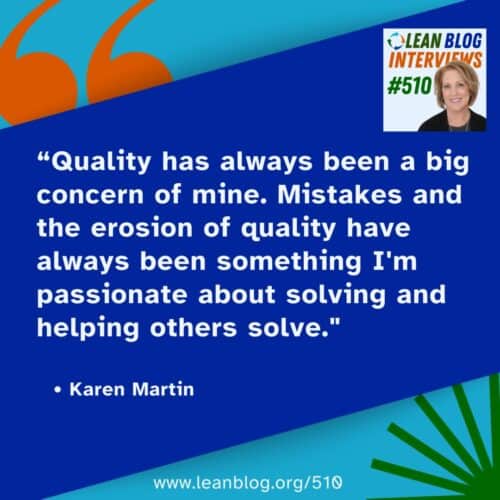
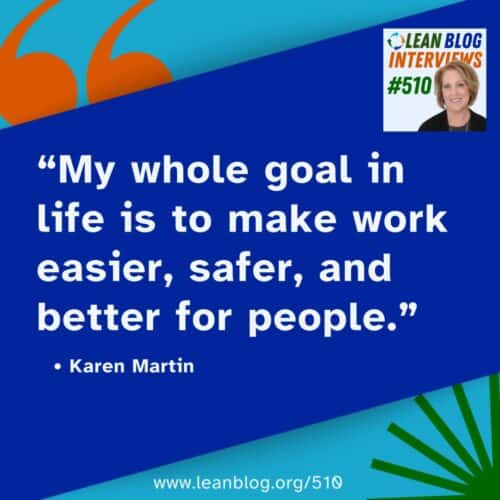
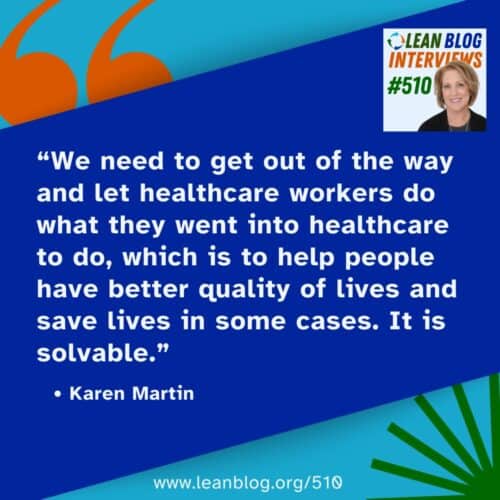
Episode Summary
Embracing Zero Harm in Healthcare: A Journey Towards Excellence
The concept of zero harm is increasingly gaining traction in various sectors, notably within healthcare. This ambitious goal aims to significantly reduce, if not entirely eliminate, mistakes and errors in healthcare delivery, leading to improved patient safety and overall service quality. Such a vision is both inspiring and daunting. Critics often question its feasibility, fearing it might set an unrealistic benchmark that demotivates rather than encourages improvement efforts. However, the journey towards zero harm is not just about the elimination of errors but fostering a culture that relentlessly pursues quality and safety.
The Pillars of Quality in Healthcare
At the core of achieving zero harm are two fundamental principles: built-in quality and systemic mistake proofing. Built-in quality, or quality at the source, signifies the integration of quality checks and balances within healthcare processes, ensuring that errors are caught and corrected early. This approach is deeply rooted in lean management and the Toyota Production System, highlighting the critical role of quality in enhancing flow and efficiency. Contrary to the misconception that lean principles primarily focus on speed, the essence of lean is deeply intertwined with maintaining high standards of quality. Emphasizing quality at the source aids in minimizing rework and waste, thereby enhancing operational efficiency and patient care outcomes.
The Role of Technology and Process Design in Zero Harm
The journey towards zero harm is multifaceted, involving a blend of technology, process design, and cultural change. In recent discussions, the spotlight has been on leveraging technology and innovative process designs to mistake-proof healthcare environments. For instance, high-tech solutions such as barcode scanning for medication administration have shown promise in minimizing errors. However, the foundation of mistake proofing lies in robust process design and optimization. By structuring processes in a way that inherently reduces the likelihood of errors, healthcare institutions can make significant strides towards the zero harm goal. This approach requires a commitment to continuous improvement and the willingness to rigorously analyze and redesign workflows for enhanced safety and quality.
Cultural Transformation: The Bedrock of Sustainable Improvement
Achieving and sustaining zero harm transcends technological solutions and process adjustments. At its heart, it requires a profound cultural transformation within healthcare organizations. This cultural shift involves fostering an environment of psychological safety, where staff feel empowered to speak up about mistakes and learn from them without fear of reprisal. Shifting from a culture of blame and punishment to one of open communication and collaborative problem-solving is crucial. Such an environment encourages the identification, reporting, and addressing of errors, paving the way for systemic improvements. Furthermore, embracing a culture that prioritizes patient safety and quality care above all aligns the collective efforts of healthcare professionals towards the shared goal of zero harm.
Learning and Collaboration: Key Drivers of Change
The path to zero harm is both a collective and continuous journey, underscored by the need for ongoing learning and collaboration. Healthcare leaders and professionals are increasingly recognizing the value of sharing insights and best practices in pursuit of this goal. Platforms for online learning, such as the TKMG Academy, play a pivotal role in disseminating knowledge on effective mistake proofing strategies and quality improvement methodologies. Collaborative initiatives, whether in the form of courses, workshops, or cross-institutional partnerships, serve as catalysts for innovation and improvement across the healthcare industry.
In conclusion, the pursuit of zero harm in healthcare is a noble yet challenging endeavor. It requires an unwavering commitment to quality, patient safety, and continual improvement. By emphasizing built-in quality, leveraging technology, redesigning processes, and cultivating a culture of safety and learning, healthcare organizations can make significant strides towards achieving zero harm. This journey, while complex, is vital for enhancing patient care and building health systems that are not only efficient and error-free but also compassionate and patient-centered.
Empathy and Training: Cultivating a Strong Healthcare Community
In the continued effort to achieve zero harm in healthcare, empathy and proper training emerge as pivotal elements. Empathy towards healthcare professionals is not just about understanding and sharing their feelings; it's about recognizing their dedication and the emotional toll of their work. The depth of impact when errors occur can be profound, affecting not just the physical well-being of patients but also the emotional health of caregivers. This calls for a supportive environment that acknowledges these burdens and provides the necessary resources to help professionals cope and recover, thereby ensuring their well-being as well as that of their patients.
Training for Excellence and Respect
Proper training stands as a cornerstone in preventing errors and fostering a culture of respect and dignity within healthcare settings. It goes beyond the basic onboarding processes to include continuous professional development and mentorship. Training is an acknowledgment of the complexity of healthcare tasks and the variability of human performance. By prioritizing comprehensive and ongoing training programs, healthcare organizations can mitigate errors stemming from a lack of knowledge or procedural uncertainties.
Ensuring that all members of a healthcare team are adequately prepared for their roles not only improves the quality of care but also bolishes the morale of the workforce. When healthcare professionals are confident in their abilities and resources, the workplace atmosphere is inevitably more positive, which, in turn, reduces stress levels and the likelihood of burnout.
Integrating Empathy in Patient-Centered Care
The focus on empathy extends beyond the internal operations of healthcare facilities to the very core of patient-centered care. Empathy in healthcare is about recognizing the individual needs and concerns of patients, understanding their journey, and providing care that addresses not just their medical but also their emotional and psychological needs. This holistic approach to care is essential for building trust between patients and healthcare providers, thus enhancing patient satisfaction and outcomes.
Collaborative Efforts for Systematic Change
Collaboration plays a critical role in the journey towards zero harm, as it breaks down silos and encourages the sharing of knowledge and experiences across different domains. Healthcare professionals, administrators, and patients must work together to identify vulnerabilities within the healthcare system and develop innovative solutions to address them. This includes leveraging technology not as a standalone solution but as part of a comprehensive strategy that considers the human factors in healthcare delivery.
For instance, incorporating user-friendly electronic health records (EHRs) can reduce documentation errors, whereas implementing advanced simulation training for clinical staff can enhance preparedness and decision-making skills in critical situations. Likewise, patient engagement tools can facilitate better communication and empower patients to be active participants in their care.
Moving Forward with Humility and Determination
The pursuit of zero harm in healthcare is an ongoing challenge that requires humility, dedication, and a collective effort. It's about continually learning from experiences, both positive and negative, and being open to change. Recognizing that the path to zero harm is a marathon, not a sprint, healthcare organizations must remain committed to the principles of empathy, quality, and continuous improvement.
By fostering an environment that values transparency, accountability, and mutual respect, the healthcare sector can forge a path toward not only minimizing harm but also enhancing the overall well-being of both patients and providers. In doing so, the vision of zero harm becomes not just an aspirational goal but a tangible reality that shapes the future of healthcare.
Embedding Quality and Safety in Healthcare Culture
A robust healthcare system thrives on a culture that prioritizes quality and safety at its core. The understanding and implementation of safety as a fundamental aspect of healthcare delivery prevent detrimental impacts on both patients and healthcare providers. Establishing a strong foundation that embeds quality control and safety mechanisms into the daily operations of healthcare services is essential. This involves a proactive approach to identifying potential hazards, implementing preventive strategies, and fostering a culture where safety and quality are ingrained in every action and procedure.
Emphasizing Continuous Learning and Improvement
Continuous learning is critical in the healthcare sector, given the rapid advancements in medical knowledge and technology. Healthcare professionals must be committed to lifelong learning to keep abreast of the latest developments in their fields. This continuous improvement extends beyond individual competencies into the realm of systemic improvements. Learning from mistakes and near misses is a pivotal aspect of this culture. Instead of attributing blame, the focus should be on understanding the root causes and making the necessary adjustments to prevent recurrence. This learning-oriented environment encourages open communication and shared responsibility for improvements.
- Encouraging Open Communication and Reporting
Creating a transparent atmosphere where healthcare workers feel safe to report errors and near misses without fear of punishment is crucial. Open communication channels enhance the team's ability to identify and address vulnerabilities within the healthcare system promptly. Encouraging such practices helps in developing trust and accountability among team members. It fosters a positive working environment where every member feels valued and responsible for contributing to the well-being of patients and their colleagues.
- Integrating Technology and Human Factors
In the quest for zero harm, the integration of technology plays a significant role. Innovations in healthcare IT, such as advanced EHRs, predictive analytics, and telehealth, offer significant opportunities to enhance patient care and safety. However, it's imperative that these technological advancements are implemented with an understanding of human factors engineering. This approach ensures that technology supports healthcare professionals in their work, rather than adding complexity or new challenges. It is about creating user-centered designs that align with the workflows and the real-world contexts in which healthcare delivery occurs.
Prioritizing Worker Well-being
The well-being of healthcare workers is integral to the provision of high-quality care. Ensuring that healthcare professionals have access to mental health resources, work-life balance, and supportive work environments is fundamental. Addressing the issue of burnout and stress among healthcare workers not only benefits the individual but also improves patient care and safety. A healthy, motivated workforce is more capable of delivering compassionate, empathetic, and high-quality care to patients.
Conclusion
In conclusion, cultivating a strong healthcare community where empathy, training, quality, and safety are interwoven into the fabric of healthcare delivery is crucial. It requires a collective effort from all stakeholders, including healthcare professionals, administrators, patients, and policymakers. By embracing a culture of continuous learning, open communication, technological integration with a human touch, and prioritizing worker well-being, the healthcare sector can move closer to achieving the visionary goal of zero harm. This journey is not without its challenges, but with humility, determination, and collaborative efforts, it is indeed a achievable aspiration.
Leveraging Microlearning for Professional Development in Healthcare
The concept of microlearning has emerged as a transformative approach in healthcare education and professional development. By breaking down complex information into digestible, bite-sized modules, healthcare professionals can enhance their knowledge and skills efficiently without the need to disrupt their busy schedules. This methodology aligns perfectly with the healthcare industry's goal of continuous improvement and safety, offering a practical solution for learning that fits into the demanding lives of healthcare workers.
- The Power of Accessibility in Learning
One of the most significant advantages of microlearning is its accessibility. Healthcare professionals can engage with educational content during short breaks, over a morning cup of coffee, or in between patient appointments. This ease of access ensures that learning becomes a daily habit rather than an occasional activity, fostering a culture of constant growth and development within the healthcare setting.
- Tailored Learning Experiences
With microlearning, content can be tailored to address specific areas of interest or need. This personalized approach not only increases engagement but also ensures that the learning is relevant and actionable. Healthcare providers can focus on modules that address the current challenges they face, enabling them to apply new knowledge and techniques immediately to their practice.
- Subscription Models and Team Learning
Embracing a subscription model for accessing a comprehensive library of microlearning modules offers continuous learning opportunities for individuals and teams. This model supports the notion that learning and development are ongoing processes, rather than one-time events. For healthcare organizations committed to fostering a culture of safety and quality, investing in such subscriptions can be a cost-effective way to keep their teams updated with the latest practices and innovations.
- Enhancing Team Performance through Shared Learning
Microlearning offers an excellent opportunity for teams to engage in shared learning experiences. Bulk licenses or subscription options allow entire teams or even organizations to access the same content, encouraging discussions and collaborations around best practices, mistake proofing, and continuous improvement strategies. This collective learning approach not only enhances the team's knowledge but also strengthens the bonds among members, leading to improved teamwork and patient care outcomes.
- Continuous Improvement Tools
Specific courses, such as those on mistake proofing and value stream mapping, equip healthcare professionals with the tools and methodologies to identify areas for improvement within their practices and systems. Strategy deployment courses further support healthcare leaders in aligning their teams and resources with the broader goals of enhancing patient safety and care quality. These tools are essential in navigating the complexities of healthcare delivery and in achieving the aim of zero harm.
In Conclusion
The integration of microlearning into healthcare professional development strategies represents a forward-thinking approach to ensuring that healthcare workers remain at the forefront of their field. By making learning accessible, relevant, and engaging, healthcare organizations can foster an environment of continuous improvement, driving advancements in patient care and safety. This commitment to lifelong learning is a cornerstone of a healthcare culture that values quality, safety, and excellence.
Automated Transcript (Not Guaranteed to be Defect Free)
Mark Graban:
Hi, welcome to lean blog interviews. I'm Mark Graban. We are joined today for the fifth time in this podcast series by my good friend and colleague Karen Martin. Karen, how are you?
Karen Martin:
I am well. How are you doing?
Mark Graban:
Doing well. You know, on Saturday Night Live, they give five time hosts like a special jacket. There's a five timers club. I don't have a jacket, but I.
Karen Martin:
Want your zero hat.
Mark Graban:
Welcome to the club. Yeah, my zero hat. For those who aren't watching on YouTube. I'm not wearing it because I think I'm a zero. It's a hat. From the exact name is the Patient Safety Movement foundation, an organization, a nonprofit that is really focused on trying to move healthcare towards zero harm. Maybe we can talk about that here today because that's a controversial concept. Sometimes to think about. Zero defects, zero harm. Is that possible? Is that inspiring? Is it demotivating? But I like to wear the hat as a conversation starter. Like, hey, actually someone did ask me earlier, what's that zero mean?
Karen Martin:
Yeah, it's a great conversation starter. Zero has some charge to it.
Mark Graban:
It does. So I think we'll make a note. We're going to come back to a related topic later on in the episode. But if you don't know Karen, and I'm sure a lot of you do, among other things, Karen is the founder and CEO of TKMG. She's also founder and CEO of TKMG Academy, a great online learning platform. We're going to talk about that today. She's author of books including the outstanding organization clarity, first value stream mapping. Just among those, is there anything else you would add kind of about your background and bio? Karen?
Karen Martin:
No. Other than maybe yes. The one thing that I think drives me toward this topic of mistake proofing is that I started with in operations design, but specifically the quality improvement side of it. So, you know, I was kind of very, very quality focused long before I fell into lean thinking and lean management systems. And so, you know, quality has always been a big concern of mine. So therefore, mistakes and erosion of quality have always been, you know, something I'm passionate about solving and helping others solve.
Mark Graban:
Yeah. And I mean, for me it's so core in Lean or the Toyota production system of trying to build in quality at the source. Like, I'm a deming geek going back to before learning about Toyota and doctor. Deming would certainly talk about the need to eliminate inspection and not just getting rid of inspection, but by building in quality through different kind of rigorous methods and culture. As we'll chat about here today, the two pillars of the Toyota way. Just in time. Think about flow and on time delivery and small batches and things like that. The other pillar, of course, is built in quality, or quality at the source, as we. I think a lot. Some, some people overlook that. They say, well, lean is all about speed and flow and efficiency. I'm like, no. Karen's rolling her eyes and shaking her.
Karen Martin:
Head, yeah, you can't go fast if you have poor quality. You know, you have to do rework or scrap, which is wasteful, and blah, blah, blah. You know, so it's, it's. I don't know where that ever started from, but it's. It's not true.
Mark Graban:
No, it's a mistake. I think it's factually incorrect. That's one type of mistake. It's just being factually wrong about something. But one reason Karen and I are doing the podcast, and we always, we chat a lot. What did you call it, Karen? Just an ongoing podcast.
Karen Martin:
An ongoing podcast. A life of podcasts between us.
Mark Graban:
There's times, though, I'm glad. I mean, we can speak candidly. It's good. I mean, when we're not recording, I mean, we'll try to be candid here. Life would be different if you were constantly being recorded and filmed. But we do have a lot of great conversations over time, and I'm glad we could do another podcast together here. But one reason we're doing that is that Karen invited me to work with her on a course for TKMG Academy. It's called mistake proofing. We wrote it together. I'm the one on camera. Whether that's whether you like watching or listening to me or not, I'm the one on the camera.
Karen Martin:
Excellent on camera, excellent, excellent partner all the way around.
Mark Graban:
That was a new experience. So I'm trying to get more comfortable with that. But that course is available now, tkMgacademy.com, and we'll put links in the show notes. So I'll stop. I probably crossed that line from being self effacing into being too self critical. So I will put that behind me. I mean, I think the course turned out great. It was great collaboration. But, Karen, I was going to ask you, you've already touched on a little bit why quality is such a passion of yours. But, you know, why was this topic something that you wanted to add into the TKMG Academy catalog?
Karen Martin:
You know, there were several reasons. One is that my whole goal in life is to make work easier, safer, I better for people. And I believe and have certainly experienced over and over and over that you can get that. And companies can also profit greatly, and customers can have just incredible loyalty toward an organization because of how they're being treated and feel about the product or service that's being used, they're using. And so there's just all this muck that can happen when you have a mistake oriented, error prone organization. And much of it is very solvable. Not marginally solvable, but incredibly solvable. And yes, I know we're going to get to the zero concept at some point, and so I just would, you know, I have a passion for getting people to understand not only what it's doing to them, really what it's doing to the organization, to have high degrees of errors or mistakes, and also that there's so much you can do about it. And it's. Some of it is actually remarkably simple if you just learn that, you know, develop the way to see what's really going on and then do something about it.
Mark Graban:
Yeah. And I. That that's a key mindset of just thinking or believing that the problem is solvable, because I hear a lot of self defeating, self fulfilling prophecy. There's a lot of this in healthcare where people, you know, people look at things like medical errors, hospital acquired infections, and people will throw their hands up and say things like, well, it's unfortunate, it's sad, I wish it wasn't there, but it's always been. And our patients are really sick. And I think people kind of convince themselves it helps them feel better of like, well, we're all smart, we're caring. If it was solvable, we would have solved it by now. But then I think the, the rub is you can point to organizations that have solved some of these problems, surgical site infections, hospital acquired infections of different types, different errors. So, I mean, I think people have got to look to see if it's possible somewhere. I'd like to think it's possible more places. And we got to get past that. Right?
Karen Martin:
Yeah, it's. The healthcare paradigm is just so dangerous on so many levels and so unfortunate, because it's not only the people that are the subject or the victims of mistakes and errors that are happening, it's the workers themselves. I mean, I don't know one soul that has gone into healthcare that just doesn't care passionately for what their calling is, and they want to do a good job, and they want to be able to do what they went into healthcare to do. And so, you know, we need to get out of the way and let them do what they went into health care to do, which is to, you know, help people have better quality of lives and save lives in some cases. And, you know, so it's just, it unfortunate and it is solvable. And hopefully people will either read your book, the mistakes that make us, or they'll take the course, or they'll Google or whatever they do to get reinvigorated and get restored. Hope that, yes, you can do something about this. You really can. Most errors are solvable. So it's, you know, if nothing else, I hope that this podcast generates a little bit of excitement about that.
Mark Graban:
Yeah, well, and I hope people do both of reading the book and doing the course. There's some overlap between the two, but it's different topics delivered in different formats. Hope people will check that out. But a couple other thoughts come to mind. People wondering, is it solvable? People will refer to human error. And that doesn't mean to me that the human is the root cause. There's root causes, or to me, human factors or our human nature is that we get distracted, fatigued, we get bored sometimes with work, or there's all these different factors. We could point back and say, well, those are maybe primarily systemic factors. They can be addressed systemically. I've heard people say things like, I don't know if you've heard this, Karen, you'll say, well, it's human error. We're all human. We're all going to make mistakes. So what can you do?
Karen Martin:
I'm like, yeah, I hear it a lot.
Mark Graban:
I mean, do something. Don't just throw your hands up and say, it's not solvable. Companies that really embrace systemic mistake proofing make great strides in that. Like, what can you do? Figure that out. Run some experiments, use, you know, some methods and some mindsets.
Karen Martin:
Yeah, and I'm sure we're going to touch on this as the, you know, the cultural element of that. What can you do is critical. It's not only the mechanics of how do you actually prevent the errors from happening, which is oftentimes process design related work, system design, work environment design. You know, there's all kinds of reasons. There's a human factor that may play a factor as well, like if someone's fatigued or hungry or, you know, any number of things that can play a role too, but the culture has to support the interest in and ability to do something about them, you know, and so, and you do a great job in both the book and the course explaining that whole psychological safety need that we have in order to have mistakes come to the surface. And so back to your comment about healthcare and medication error reduction. The reporting of those errors needs to actually go up initially so that you can get to common root causes for the errors and do something about them and go through scientific problem solving, discipline problem solving. So the culture has to support the discovery of and then the resolution of these mistakes.
Mark Graban:
Yeah. Another way of saying it is shifting from discipline and punishment to disciplined problem solving.
Karen Martin:
Yes, yes. I like that. That's good.
Mark Graban:
Different way of saying that. But think about mistakes. The probably non physically harmful or deadly category. I don't know if you saw in the news, I'm just throwing this at you here, that there's an airport in Japan. This was in the news and a couple of places recently, Kansai International Airport near Osaka has been open for like 30 years. And they claim, and this sounds unbelievable, but they're really putting the stake in the ground and talking about it and, okay. That they've never lost a bag in 30 years.
Karen Martin:
Wow.
Mark Graban:
And, you know, they probably use a lot of the same technology us carriers use barcode scanning on the bags, and I think they've thrown technology at it. But what I remember from, like, the NPR piece was somebody from the airport talking about things like process and purpose and, like, it sounds like, you know, this culture that, you know, some of it they framed as, okay, yeah, that's japanese hospitality of, like, really, really, really caring for a customer and tourists. And, you know, they have a lot of pride in thinking about their role. It's not just the physical movement of the bag. It's supporting somebody who's traveling maybe into the country or around the country, and they, it contributes to their experience and, like, wow. Like, just, it sounds like, you know, a matter of culture and process. It wasn't something that they bought and installed.
Karen Martin:
Yeah. And I think, you know, the danger of talking about having that human element as core and the whole mistake proofing arena is that I've heard several leaders say, well, that's going to cost too much. It's going to cost too much to put the people in place to handle problems at their core. And usually when I hear that, and I'm usually somewhat aware of the problem and the mistakes and the root causes for them when we're having these conversations, it doesn't take really all that much extra money. It really doesn't. Sometimes it's usually technology if you're going to bring technology that costs anything at all, but sometimes it's just process design or the lack thereof. And often. And so when leaders say that, I'm like, no. Do you know that? Have you actually gone through root cause analysis and gotten to the core of what's going on? And have you explored all the potential countermeasures you can put in place to at least reduce, if not eliminate? And the answer is usually no. And I was like, well, then, come on, give it a chance.
Mark Graban:
Yeah. And I mean, you know, there's these complicated dynamics when, you know, you were talking about quality. And I think even with safety, we're focusing on that and making great strides and engaging people in the process, you know, strengthens their commitment to the team, to the organization. It's not just a simple cost benefit analysis. I think it's more complex than that, you know, and back to the zero hat for a minute. The late Paul O'Neill, as CEO of Akoa and later in his work, was such an advocate and a leader for working towards zero harm. And he, I remember things that he would talk about where he would tell people at Alcoa, don't let budget become an excuse for not implementing something for safety. I don't think they were. I don't think it was a complete full blank check. But I do remember him saying that he told his safety people or finance people, if you start calculating ROI on this, I will fire you. Because to him, it was really based on principles and I think commitment to the employees and how that gets repaid through people's participation in improvement. And Alcoa was wildly successful during those years. It wasn't a trade off between safety and financial performance and the customers of.
Karen Martin:
Whatever that good or service is that's being produced. You know, that the safety of those folks also, it gets back to respect for people the fundamental element of what makes lean when it's done well. And it's core so powerful that that drives decisions much of the time. And it's a more humanistic way to get really good work done at a decent price point that people will pay for and gain market share.
Mark Graban:
Yeah, yeah. And you and I have talked a lot offline about mistakes, and you've shared with me how you're even more focused on this and you notice opportunities or a lack of mistake proofing, or you can sometimes see mistake proofing. But I think, like going to Starbucks, and I think the level of process depends partly on the impact of the mistake. So I've been waiting in line for a Starbucks, and I've called out Mark. And I thought this, no, no, it was actually for another mark or a different mark, came up and grabbed and took a sip of my drink and like, oh, that's not right. Like, it's probably not worth doing. Like a hospital saying, well, you need to use two identifiers. Like Mark, born in October 24.
Karen Martin:
You can't get your coffee until you show your driver's license.
Mark Graban:
Yeah, we're not checking id. They're nothing. Scanning our app as we pick up the scan is just for the payment, you know, I mean, I think there are processes in hospitals, like medication administration need to have so much more attention. When you think of what. What's the worst that could happen? I mean, somebody who really doesn't want caffeine might get a caffeinated drink instead of uncaffeinated. Like, hopefully there's not, like, any medical risk or somebody had that level of risk, they might want to see the person pouring it directly, you know, to try to check for that. But for most customers, you know, it probably doesn't merit that level of mistake proofing, because I think with Starbucks margins, they'll dump a drink and remake it.
Karen Martin:
Right.
Mark Graban:
Without giving it too much thought. But that's cost, right? I mean, so there's financial impact, right?
Karen Martin:
Yeah, but I don't get the sense that Starbucks does that willy nilly. You know, they're not just, like, dumping drinks, you know, every 2 seconds. I mean, it's. There's purpose behind their movements and their decisions and their actions and all that stuff. So, yeah, you know, I get obsessed with it. So, first of all, I think that just generally speaking, anyone who's interested in improvement and process design and all of that, it's a career hazard that you can't not see it. Once you learn how to see waste, you can't unsee waste. And so what's. What's sometimes challenging is having patience with the situation and not just like, wanting to get my mapping paper out and post it and start fixing it.
Mark Graban:
Send them a consulting proposal.
Karen Martin:
Yeah. You know, it's very tempting when you see waste so rampant, but, you know, quality as well. You know, it's to know what we know and what others hopefully will learn if they don't already know it, is that it is solvable, you know, and so it's. It's hard to see it continue when, you know it can be solved. And one more thing that you just kind of touched on that I want to go into a little more deeply is this thing about respect for people. You know, when people have a frustrating day at work that has all kinds of, you know, ripple effects into their families, into society, I mean, it's. It's it can be a really big deal to come home from work drained, and people think, ah, you know, it's a job. You're drained. No, no, no. Coming home from work drained and not having your tank filled up instead of having it depleted has all kinds of ripple effects inside families and communities and friendships and all kinds of things.
Mark Graban:
And physical health.
Karen Martin:
Yeah, and physical health. And so every time someone makes a mistake, unless they're a sociopath, and there are a couple of those in companies, not in every company, thankfully, but there are a few running around there. People care passionately about doing a good job, and doing a poor job feels terrible, and so. And it's even more terrible when they didn't have anything to do with the mistake in the first place. You know, they either weren't properly trained, or there's no standard work saying what they should do, or the equipment's not working, or what. You name it. They're forced to make a substitution. Whatever it is, you know, that feels crappy. People want to do a good job, and, you know, we're obligated to make that environment so that that can happen.
Mark Graban:
Yeah. Yeah. And one thing I've kind of experienced and, you know, discovered in recent years is it's one thing to not get upset when somebody makes a mistake, but sometimes you have to go beyond that and, like, recognize and have empathy for that person feeling bad, even when you've said, well, that wasn't your fault, or they're still feeling bad, or they're wondering, well, yeah, no, I'm putting this on myself. I feel like it's my fault. And giving someone the space to get past being upset about it, even when that's, like, kind of self imposed, as opposed to situations where they got yelled at or they got in trouble.
Karen Martin:
Right.
Mark Graban:
Yeah.
Karen Martin:
And I think that there are times when it's pretty impossible to get past it quickly, in other times, when it calls for passing quickly. I mean, if you do harm to someone else because of something that your hands touched or your mind made a decision about, you know, it's. I think it's okay to feel bad about it. It's not okay to stew on it, and it's not okay to blame oneself when the organization's, you know, processes or the work systems maybe didn't support the opposite outcome. You know, the good. The good outcome. But, you know, it's okay to feel bad for a little while, but only a little while, and then. And then I, you know, gonna move on and put that energy toward actually solving the problem.
Mark Graban:
Yeah, sometimes it takes a couple of minutes. Sometimes it takes an hour. In some situations in healthcare, when a healthcare professional is involved in a systematic mistake that harms somebody or almost harms somebody that they're sometimes referred to as the second victim.
Karen Martin:
Right.
Mark Graban:
And sometimes you need counseling, resources, or EAP program to help somebody process and get past something kind of traumatic.
Karen Martin:
Yeah, absolutely. I mean, it's a whole spectrum of, you know, little effect versus, you know, life ending effects.
Mark Graban:
Yeah, yeah. But you mentioned training, and to me, that's totally a systemic factor. When we look at process design, staffing levels, equipment design, all these different things. I'm going to bring it back to the more lighthearted topic around Starbucks again. Like, I think of one time, or I love the nitro cold brew beverage, which is always served without ice because it's nitrogenated, it's foamy, and it's cold enough as it's being poured. And I ordered it once, and the barista working there poured it over ice, and I said, oh, this isn't supposed to have ice. And then I overheard the interaction between that barista and someone else of, like, clearly this woman was new on the job, and she hadn't been trained to know that. And it's almost like they were training her by correcting different mistakes. I'm like, well, that's. I don't. That. I mean, how is that making her feel? They could have more proactively kind of laid that out for her or been supervising and coaching. Okay, you're gonna make this. Now, this doesn't have ice. The regular cold brew does. You know, don't. Don't make that mistake. I felt bad for the barista more than I wasn't upset because they'll dump it out and give you the right drink the right way.
Karen Martin:
Well, again, respect for people. I mean, that's not fair to do that to an employee. You know, Starbucks is such an interesting case study to. And I am in Starbucks a fair amount, like you. And I listen a lot, and I ask a lot of questions, too. I'm a nosy customer. And so I remember back in the day when Starbucks was relatively new, I used to see the training. I used to see it being done in the lobby during quiet periods. I used to overhear it. I used to see their materials, and it was stellar, and it was consistent. And I happen to love a tall soy mista with two raw sugars. It's off menu. It's off menu. It's like Olay, basically. It's steamed milk coffee, nothing, not espresso. And that used to be precise, beyond, beyond precise at any Starbucks in the world, not just us in the world, because their one standard was you fill the coffee up to the sirens eye on the siren that was on the cup. And because of that, no matter what size cup it was, the milk proportion was exactly right and the same everywhere. And then, you know, over the years, I started tasting these wickedly different, you know, flavors to my soy misto. And I finally started asking people, do you know about the siren's eye? No one.
Mark Graban:
Yeah.
Karen Martin:
Do you know about the siren's eye? No one. You know, and so, you know, it may be for a different reason. Maybe they changed the width, the width of the cup and no longer, no longer was a siren's eye.
Mark Graban:
The plane, they changed the logo. They got rid of the old siren in the Starbucks.
Karen Martin:
That's why. But it's really interesting to me that the, I have observed, served, and I have more than just a few data points on this, that their standards of training and documented work and all that stuff have slipped tremendously, in my opinion.
Mark Graban:
Well, no, I mean, they, I think, have moved away from. There was a period 15 years ago, roughly when Starbucks was really into lean and they were using twi training within industry job instruction. They were coming to conferences and demonstrating how they teach job instruction. And, yeah, I think, I think something has slipped. There's been executive changes, and I think one of the key people who was a vice president, who I'd met, who was one of the leaders of that whole initiative, left the company. And it, it's a story we've heard so many times. These things, these things can fade when leaders really aren't.
Karen Martin:
Yeah.
Mark Graban:
Focusing on it anymore.
Karen Martin:
Exactly, exactly.
Mark Graban:
But, you know, we were going to talk about kind of a spectrum of mistake proofing, like, you know, ideal and, you know, would be 100% prevention. Sometimes that happens through mechanical devices, electronic sensors, and sometimes we can only come up with something that reduces errors. So I think of like the Starbucks cup, and I did see something. They've redesigned their cold beverage cups again to have some of these lines and, you know, visual indicators. I'm sure that helps to have that standard, but somebody could still over pour or under pour. They could overpour and they're in a rush and like, well, I know standard might be to dump it out and start again, but we're really behind and the customer probably won't notice or, you know, then there's like, cultural elements involved. But I mean, you know, I think instead of throwing our hands up and saying, well, people are sloppy poorers. I mean, I guess I'm not trying to push for automation, but an automated dispenser can be really precise. I've seen at a whiskey distillery, there's a machine that will put precisely 750 milliliter milliliters of liquid. That's hard to say. Sober after a little long. If I'd had a bourbon, maybe it's easier to say 750 ML, because for tax reasons, that has to be very legally precise. They wouldn't have somebody hand funneling into the bottle. So then there's that question of like, well, what do you automate because of quality? And then how do you treat people respectfully in that process?
Karen Martin:
Are you the one that told me about this machine, back to coffee again, about the machine that is an automatic dispenser, and it does everything. There's no human element in it. Was that you that told me about that, or is that someone else? There's no barista. There's just, you know, you go, it's self serve, and it's exactly. It pours exactly the right amount every time of whatever you're getting, whether it's, you know, the flavor or the coffee or the milk or whatever.
Mark Graban:
I mean, there's certain vending machines, like the Cincinnati airport has, you know, like a lavazza espresso make drink making machine that's automated. I'm sure that's engineered to be completely consistent. It'd be interesting to compare the quality. But then, you know, you think about the experience. You know, if going in and have a drink or a pizza that's made by a robot, as opposed to a person that you can interact with. There's all kinds of factors around the experience and like, okay, you don't want to spend money on the robots, and it might damage the customer experience. We can think about. How do you error proof the process and the training along the way? One other thing I was going to go to, and this is going to sound like I'm just ranting about pet peeves. Starbucks has a really good process for order taking, whether it's in person or in the app. I was at a restaurant recently where the server was taking the order for four people and was never once writing something down. And then sure enough, the server had to come back and ask, wait, was it this or was it that? Yeah, I tried to be really calm of like, gosh, pen and paper. Yeah, that's a very technology.
Karen Martin:
Was it a server in a regular restaurant, or are you referring to Starbucks?
Mark Graban:
No, it was not as Starbucks. It was a sit down restaurant.
Karen Martin:
So classic servers in high class restaurants, it was a sign of the expertise of the server to not have to write things down. And you see that still in some of the older servers, especially in some of the older establishments that have been there, like in New York City, you'll see a lot of this where they don't write anything down, but they also hardly ever get it wrong. And so I'm not quite sure how they hold all that in their head. I don't think I could do it. But it's just. It's interesting how it's almost revered to not write things down in those types.
Mark Graban:
Of restaurants, but everyone's human, and everyone's going to have a moment where they forget. Now, I'm glad that server came back to clarify instead of being wrong. Back to the kitchen. I don't know the voice of this customer. I'm not impressed doing it via memory. I'd rather see the pad of paper. And nowadays it's often it's an iPad type device.
Karen Martin:
Right.
Mark Graban:
You know, that's just me. So anyway, I had to get that off my chest. You were about to say something?
Karen Martin:
Well, I was going to say, we've been talking a lot about mechanical kinds of things, and a lot of. When I've talked with people about mistake proofing, error proofing, a lot of people say, yeah, but we only deal with information and data and creative or engineering or transactional process or whatever. So how do you do that with human error being so rampant? And I loved how you touched on things like a simple read back was one thing, where information can be more reliably conveyed if there's a read back involved. And I don't think we said this in the course, but since you and I both write, you know, the technique of reading out loud what you've written so that you can actually catch it. The ear will catch way more than the eye will, and so there's things like that. There's reading backwards, you know, through a sentence to also see typos or errors and, you know, spell check, grammar check. All that stuff's lovely and wonderful, but it's not perfect. And so, you know, there's all of those things that can happen, and then there's just getting clearer on what the standards are, you know, and making sure that everyone is operating from the same page on what qualifies as good work being passed on versus it being error prone. I love when we do mapping and we get cross functional teams. There's almost always some tension between one or two people or teams, and when we map out the current state, almost always it'll be revealed that someone isn't getting what they think they need or what they should have to do their job. And the people supplying it had no clue that that's what they needed. Right. And. And this friction gets like, it just melts away and come back. It's so cool. But it's like, wow, you know, we need to get out of our ways of success because it is that simple to solve what's otherwise seemingly a human error that can't be solved.
Mark Graban:
Yeah. So, yeah, and, you know, there's. There's the two mindsets. There's, you know, we can't solve that problem. And then at the risk of sounding a little Pollyanna, I've heard people say, well, maybe what you mean is we haven't figured it out yet. One is very definitive of, like, we can't solve that fixed mindset, I guess, versus a growth mindset of, well, let's work on it. Let's make it 50% better this year, and then let's keep at it. Toyota still has final inspection at the end of their assembly lines. As much as they focus on built in quality, and for as long as they've been focusing on the techniques and the culture, I'm sure they make this determination of, like, well, we're still not outputting perfect cars. Final inspection, technically, we want to call that waste. It's still better than nothing having the final inspection. And Toyota doesn't have a zero harm safety record. I've seen data and charts when I've gone through plants, and I'm not saying, I mean, you know, I'm not saying shame on them for not getting to zero. I think it show, goes to show it can be really difficult, but you need to keep working at it. That's why I wear the zero hat. Like, it can be an inspirational goal when leaders are working together with everybody in the organization, or it can make people roll their eyes if it's just a slogan and people are being punished for mistakes or injuries.
Karen Martin:
One of the things about final inspection that I like to remind people of when we're working with teams is that the final inspection may need to be in place, especially short term, while you're figuring out all the root causes and getting rid of the mistakes and the whole process that leads up to final inspection. But the one thing that's different at Toyota than most organizations that have final inspection is that heavy culture of that quality at the source, in process quality fixing before it gets to final inspection. So that's the rare instance of finding something at final inspection that needs to be either reworked or hopefully not scrapped at that point. And so what I find fascinating is the research has been proven over and it's been the same results over and over, that when you have final inspection, there is this relaxation that happens in the middle of the process where people go, oh, well, someone else will catch it.
Mark Graban:
Ah, that's risky.
Karen Martin:
And as an author, I wonder if you've had this. I've had this where I've had, and the next step is my own editor. Not the publisher's editor, but my own editor. And I will be. I've caught myself being a little less diligent because I know someone else that's even more skilled than me is going to be looking at it. And it's like this weird psychological thing and I have to go, no, stop it, Karen, you're the quality of the source gal. And so I think that's a difference between having final inspection where it's catching things way downstream from where they should have been caught and possibly never occurred in the first place, versus kind of responsible final inspection with a strong quality of quality at the source and don't pass anything on.
Mark Graban:
Yeah, yeah, I mean, that's a good point. And I think final inspection needs to not be just the fixer of the problem. It needs to kick off the feedback loop back to the source and that cultural backsliding that could occur. Maybe you address that by really proactively making it a sense of pride that you caught your own mistake and companies that are more on the side of rewarding the mistake. Now, if you have a reasonably functional culture, people aren't going to be intentionally creating problems so they can get rewarded for it. People want to do good work. You know, some people would be cynical and say, like, oh, well, or, you know, those software developers are going to just create bugs so they can get rewarded for fixing them. I don't, I really don't think developers work that way.
Karen Martin:
No. First of all, they hate fixing bugs.
Mark Graban:
Yeah.
Karen Martin:
So, you know, like they're not going to create their own drama and their own angst, you know, what was it going to say? There's something about the. Oh, so the thing about quality, the source, I also get really kind of high on is this notion of pacing the work so that people have time to do self inspection before they pass work on. And that, you know, rushing work pressure that a lot of the performance objectives and goals give people doesn't serve quality well at all because they don't have time to even really do their own inspection before they pass it on. So I have an image that I love using every once in a while in talks and things like that. It's a big ball of like, garbage. It's like a gigantic. And there's a person beside it, this huge ball, and it says, don't let me get the right order. Don't make junk, don't accept junk, don't pass junk on. It's like, you have three obligations as a worker in this process. Don't make it, don't take it, don't pass it.
Mark Graban:
So, and I think part of what helps make that happen is leaders realizing, okay, the commands to them, if you will, is don't punish junk. Because when you punish junk, people start hiding junk. They start passing it on. They start. And again, I've heard people say, well, we have to punish people for mistakes because if we don't, that gives them permission to make more. And I, like, you rolled your eyes. And that's my reaction of, like, I don't, again, like, I don't think it works that way. You know, the harm that comes from punishing mistakes gets, you know, so it becomes hard to see.
Karen Martin:
Yeah.
Mark Graban:
But, yeah, that's something leaders need to pay attention to. And in the podcast, my favorite mistake and the book, the mistakes that make us, I've documented some of those stories from Toyota where leaders apologized to the frontline worker because they put them in a position where a mistake was possible. Like, that's just such a different mindset than most companies that would say, you screwed up, you put the wrong chemical into the machine, you better not do it again.
Karen Martin:
Or right. You know, I think there's one exception to the rule that I've had noticed over the years that I haven't quite ever figured out exactly what to do with this reality. But I do think there are cases when the work system isn't at fault and that there's someone that for some reason just can't stop making a mistake or can't stop a behavior that leads to mistakes, or can't. Or. And when I say can't, I think kind of unwilling. And so, you know, I've seen situations I personally have been involved with where I've noticed a pattern and have raised it, and we've had a great conversation about what's behind that pattern, and it just doesn't seem to ever really improve, no matter what we try. And I think there are those rare, thankfully, cases where someone's either not well suited for the work, it's not a good job Fitzhe or something. There's something that's not quite right. It's not a bad person. They're not in a role that can help them be successful. And I think it's perfectly fine to move people out of those roles into something they can be more successful at.
Mark Graban:
Yeah. Yeah, I would agree. And some of that selection and placing somebody into a job can be part of the system. You know, are we rotating jobs so that people are staying mentally fresh? That's part of the system design, you know? You posted on LinkedIn recently an article about talking. What is it called? The slow work movement.
Karen Martin:
The slow work movement, yes.
Mark Graban:
Because I have a bad habit that I think is either innate or it was somehow imprinted on me or ingrained at a young age. I have this tendency to try to rush through my work and, like, focusing on completing the work instead of focusing on even, like, enjoying the work as I'm doing it. And that's something I've been trying to be more mindful of. And some of that comes down to, like, literally, like, I can type very quickly and I type pretty accurately. I actually. It's more effective to intentionally try to slow down my typing just a little bit.
Karen Martin:
Yeah. Auto cracking.
Mark Graban:
And a lot of mistakes get corrected automatically so I don't have to go back to fix them anymore. Some things get auto corrected into the wrong word.
Karen Martin:
Right. Well, you know, I think a lot of times when you have a propensity to rush, there's something deep in someone's background that is a little bit of a spark. Maybe not the whole reason for that behavior, but a Yde spark. Like, it could have been a very impatient parent. Come on. Go. You know, it could have been a coach, it could have been a teacher. It could have been a first boss. It could be any number of things where someone was the opposite of being methodical, intentional, you know, deliberate, you know, that measured. And the people that responded to that post of mine about slow work, a lot of them had the same phrase. That is what my phrase is. Go slow to go fast.
Mark Graban:
Right.
Karen Martin:
Their phrase was, there were like three people that said the same phrase. And it was really. It's very poignant and of course, I can't remember it. It was.
Mark Graban:
I put you on the spot by bringing.
Karen Martin:
No, no, I want to think for like ten more seconds. It was because it's a really good phrase. Oh, smooth. Let's say slow is smooth. Smooth is. No, wait. Slow is smooth. Smooth is fast. Wait. Yeah, smooth. As fast as the last part of it.
Mark Graban:
So working smooth is a good.
Karen Martin:
Smooth is fast, and that's, that's true because you're not having to jerk around and fix things and, you know, and all that interruption that can happen when things aren't going well. So I. I'm a big believer in.
Mark Graban:
Slowing down and I'm sorry.
Karen Martin:
And self inspecting.
Mark Graban:
And self inspecting. And that, that also applies, I think, to speaking, whether it's reading a bio or an introduction or even just speaking extemporaneously in a conference, sometimes trying to just slow the pace of speaking down a little bit. Not so much that it seems super noticeable, but words like milliliter become a speed bump if you try saying it too fast. That's why they say 750 ML. Right?
Karen Martin:
Yeah, it's true. Words get. It's easy to slur over them when you're going fast.
Mark Graban:
Yeah. So one other thing we're going to talk about here today is something that we kind of hashed out and talked through very early in the planning of this mistake proofing course. Back to words and terminology. And we're both writers and we think about words a lot. Mistakes versus errors are these different things. I've heard some people, including yourself, say they're different, and I was taught that they're really more of a synonym. So I'm not trying to say, hey, nah, nah. Told you. I don't know. I was right. No, but I think I influenced. We came to agreement. So now that I've framed it that way. I'm sorry. Could you share a little bit of your journey on, like, you know, thinking about those words?
Karen Martin:
Yeah. So my thought about them has historically been that error is the kinder term, and that mistake has baggage, that mistake has blame implied. But when someone raised that point on that post that you had the first post, when the course came out, the guy. Yeah. On LinkedIn, the guy that mentioned that they aren't the same, and the mistake is, you know, necessarily blaming. I pointed out to him that in the process of writing the course with you, we went to many sources for definitions to see what the dictionaries of the world said, and they were synonyms, like clearly synonyms. And then I posited back to this guy that perhaps the difference is very much about how words have been used and in what settings, and that maybe if error was given that finger wagging, that mistake, Scott, it would be the bad guy.
Mark Graban:
Yeah.
Karen Martin:
And so I've come to. Yes, I have come to believe that they're synonyms. Thank you, Mark.
Mark Graban:
You know, so, I mean, I'm being pedantic, if I'm pointing to dictionary definitions, but I mean, your point, the guy who commented on LinkedIn, and that was a Toyota retiree who's worked with a lot of other companies and other industries. I'm not doubting him that. As he said, his experience is that when he's worked with other organizations, the word mistake causes a lot of heartburn or it's seen more negatively. We've seen that with the word problem. I know Toyota people have run across that. I've run across that. I've learned from Toyota people. The language matters. It means different things in different settings. And I think that former Toyota person Pat was, of course, Toyota. No, I mean, you're not supposed to blame people for these things, but other organizations do. And that's part of the challenge when we work with different organizations. But I think of my thought process on this over time. Well, I've heard some people say error is more significant than a mistake, its degree of impact. I dont know if thats how everyone, some people look at it that way. John Grout, whos an expert in, he tends to say mistake proofing. But when weve done podcasts and discussions, to him the words are synonyms and we see the translations of pokeyoke. Sometimes people say that means error proofing. Sometimes they say it means mistake proofing. As long as we're not saying foolproofing. Right.
Karen Martin:
The old or idiot proofing.
Mark Graban:
Idiot proofing. The old dummy or dummy proofing. The original japanese phrase bake means idiot proofing, and they stopped using that because it was disrespectful and inaccurate. But I pointed to the dictionary. Forgive me for that, but dictionary.com says an error is a deviation from accuracy or correctness. Semicolon, a mistake, as in action or speech. Then when you look at its definition of mistake, it says, in error, in action, calculation, opinion, or judgment caused by poor reasoning, carelessness, insufficient knowledge, etcetera. So, like it's circular, like if you were brand new in the language, these words are pointing at each other. Maybe the dictionary, maybe other dictionaries do a better job.
Karen Martin:
But yeah, I think the one thing I do feel pretty firmly about, you know, the error mistake thing, I'm, I'm now agnostic, although I do tend to use the word error more. I think that's because I grew up thinking that mistake was bad and error was good. Now, now I, you know, I'm not going to change that one yet. But one of the things I do think is that there's a continuum. And when you look at the eight wakes, for example, or seven waist plus, plus underutilization of people or lost creativity that we've added in the west, the, you know, the waste. Sometimes I see it framed as rework. Sometimes I see it as the mistake. Sometimes I see it as a defect. And to me, it's a continuum. So there's an error or mistake that creates a defect which requires rework. So to me, it's a continuum. The. The original sin, as it were, is the error, mistake, you know, not the rework. And, I mean, I'm sorry, not the. Not the defect and not the rework. It's that original one. You know, if you want to talk about what the outcome was of it, then that's the defect. But to me, the waste is actually rework. You know, it's the. It's the result of all those. So as long as, you know, people are sure that there, and understand that there's three pieces of that puzzle that cause it all causes waste, then. Then I'm. Then I'm good.
Mark Graban:
Yeah, I'm good. If people say error, I use the word error sometimes to mix it up. I mean, them as synonyms. But, yeah, it just goes to show the complexity of language and implications of different words in. In different settings. I mean, if you had felt really strongly that the course should have been called error proofing, I could have run with that, because what we teach in the course is what matters, I think, more than the terminology, we could call them whatever we call it, gaffes, blunders, flub ups. You could call it also other ups. Yeah, I mean, some of those phrases do sound to me inherently more blamey. I would tend to avoid a those phrases, but I could see having a workplace culture where somehow it fit of like, oh, we do an award for the flub up of the month, and we celebrate when people report flub ups. And, like, they could have a completely blame free culture around a different word.
Karen Martin:
I don't like going that far with the cultural aspects of accepting that errors will occur and being respectful. I actually think that the average leader would roll his, her, their eyes at that, and I think it's justified. Yeah. Because that's like, like, oh, it's okay. It's okay. It's not okay to make mistakes or errors. Never. Okay. It's a fact that it is common and there is, and we're not going to beat people up for doing so because it's typically not the person's fault for doing it. But I don't think we also need to celebrate them either. I think that's a little too gimmicky for my.
Mark Graban:
Yeah, I hear you. I tend not to use the word celebrate errors. I use words more like acknowledge mistakes. And I've interviewed people on the podcast whose companies are doing quite well and they've been doing something like that. But I think a lot of it is situational. Like if you're on more of a innovation or scientific front and it's inevitable that some experiments won't work out of. So that's a different situation than. I would never give an award for medication error of the month. That would be completely inappropriate.
Karen Martin:
Yes.
Mark Graban:
You know, different situation.
Karen Martin:
So last night I thought of you and I almost went back and rewound. I was watching a Stephen Colbert episode on DVR and he had, I forget his nurse. Is it Tyson? Tyson? You know, the adventure, the vacuum and the hand dice. Dyson James, is it Jameson?
Mark Graban:
I think it is, yeah.
Karen Martin:
So he was a guest. I never heard him interviewed. He was delightful. And he used the, I think it was Einstein that said something about, I have failed x number of times. Oh, it might have been Edison.
Mark Graban:
Edison, Edison.
Karen Martin:
Yeah.
Mark Graban:
I haven't failed. I've found 10,000 ways that didn't work.
Karen Martin:
Right. And he was talking about his original vacuum cleaner experiment and how many. He had something, 5000 different prototypes. And he, and he said, you know, those weren't 5000 failures. Those were, you know, 5000, you know, iterations to the successful one or something like that. And I thought of you because he was talking about his mistakes in a very positive way.
Mark Graban:
Yeah. And I think regardless of the situation, whether it's an innovation mistake, that we can be a little more light hearted about a serious process problem that hurts or kills somebody. The key is acknowledging it and learning from it. Right. So these innovators, Thomas Edison wasn't repeating the same mistake 10,000 times.
Karen Martin:
Right.
Mark Graban:
Some hospitals repeat the same mistakes over and over again, which is.
Karen Martin:
And some airline manufacturer aircraft do as well. Yeah, unfortunately.
Mark Graban:
Yeah.
Karen Martin:
That's a very high stakes mistake as well as medication error.
Mark Graban:
Yeah. Okay, quick think of another Starbucks example. That's how it lighten the. Try to lighten the mood.
Karen Martin:
Yeah. I don't know.
Mark Graban:
I have to pick on Starbucks. I mentioned Starbucks because I'm a frequent customer there.
Karen Martin:
So I'm a fan.
Mark Graban:
I'm a fan. If I was a fan of another coffee shop, I'm sure I would notice that. Coffee shop mistakes. Well, Karen, let's go ahead and wrap up this segment of our long standing podcast, 50 minutes that we decided to record today. Karen, tell everyone before we wrap up about TKMG Academy, the website, and a little bit more. I mean, as much as we both like the mistake proofing courses, there's a lot of great instructors and content there. As we wrap up, tell people more broadly about TKMG Academy.
Karen Martin:
Thank you. Yes, we started this about five years ago, and it was our attempt to get more knowledge into more people's hands across the globe in a more efficient way so that companies can start reaping the benefits or continue or deepen the benefits of what happens when you perfect processes and get great work environments and build amazing cultures and all the benefits that that brings. And we have kind of started with little course here, course there, some practices, some methods, some philosophy. We're pretty how to. So it's, everything's pretty practical. There's maybe a little bit of theory to understand context, but pretty practical. We've got 25 of them right now and we launch about six a year. And we're just really passionate about, they're about an hour in durations. We have a couple that go to 2 hours, and they're broken into these little micro learning modules. So it's easy. There's no excuse for not learning. You can have it with your coffee or your juice in the morning and just watch one. And we're excited for the future and more on the way. So tkmgacademy.com is the URL for the website?
Mark Graban:
Yeah, and we'll put links in the show notes. They can go directly to the mistake proofing course and they can register for that individually. Or there's a subscription that gives you access to everything in the catalog, right. That's an annual, annual basis, right.
Karen Martin:
It is an annual subscription access to the full library. And if you want to buy it for full team, if you have a team or even the organization to get people really sensitized to mistakes and what you can do about them, then we have bulk purchases as well, bulk licenses.
Mark Graban:
Well, people will check that out. And I know some of my colleagues at Kynexus have gone through your value stream map. The value stream mapping course was you or did Mike, that was you. And they've gone through, I think, a course on strategy deployment. And I've heard really good things about those courses. And the bits and pieces I've looked at are really good too. I can go through and deepen my own learning.
Karen Martin:
So I learned too. I mean, every time we like, I learned from you as much as I, you know, contributed also. It's, it's I mean, it's just looking at things, these different lenses is always so cool. Very, very instructional.
Mark Graban:
Yeah. And I learned some things from you, so thank you for a good collaboration. Thank you on that. So I hope people will check it out. Karen, it's a lot of fun. Five times. Like, I I need to make a coffee mug or a sweatshirt or something that I can send to people who are in the five time club. There's about ten of you, I think.
Karen Martin:
Wow. Yeah, it's. Thank you. It's an honor to be in the club.
Mark Graban:
Yeah, well, thank you for being here. It's always fun, and we'll have it back again sometime.
Karen Martin:
Thank you, Mark. And we'll see you soon. We'll. We'll be podcasting probably tomorrow. Our informal podcast. All right, thank you.
Mark Graban:
Okay, thanks.
Karen Martin:
Thanks. Bye bye.
Please scroll down (or click) to post a comment. Connect with me on LinkedIn.
Let’s work together to build a culture of continuous improvement and psychological safety. If you're a leader looking to create lasting change—not just projects—I help organizations:
- Engage people at all levels in sustainable improvement
- Shift from fear of mistakes to learning from them
- Apply Lean thinking in practical, people-centered ways
Interested in coaching or a keynote talk? Let’s start a conversation.
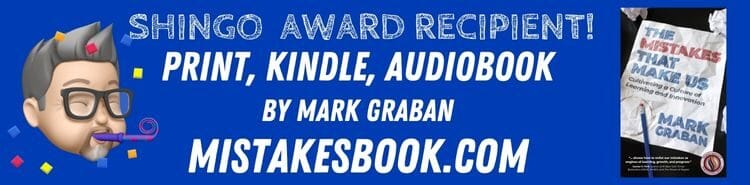