I don't think I ever shared this article that I co-authored and had published in 2014… so it's time for another “Throwback Thursday.”
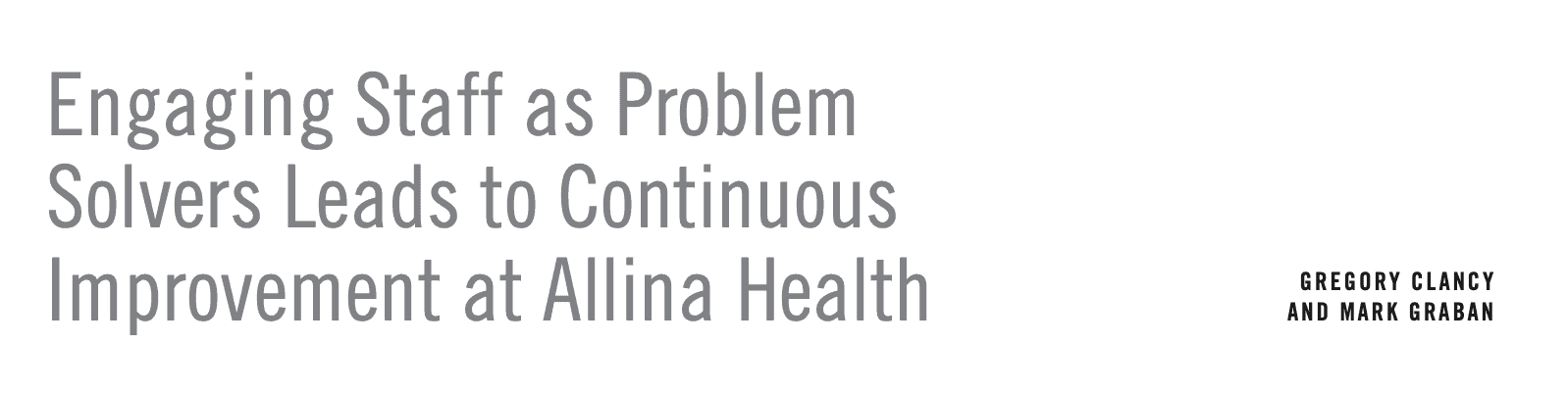
I'll share a summary of it here in this post. I think this still applies here in 2024.
In the evolving healthcare landscape, fostering a culture of continuous improvement is essential for enhancing patient care, safety, and operational efficiency. Allina Health, a nonprofit health system with over 26,000 employees in the Midwestern United States, has demonstrated the profound impact of engaging staff as problem solvers through the implementation of the Kaizen methodology.
What is Kaizen?
Kaizen, a Japanese term meaning “good change,” is rooted in the principles of continuous improvement and staff empowerment. This approach, famously adopted by Toyota, encourages all employees to contribute ideas for improving their work environment. At Allina Health, the adoption of Kaizen has transformed traditional workflows into a culture of ongoing process improvement driven by staff at all levels.
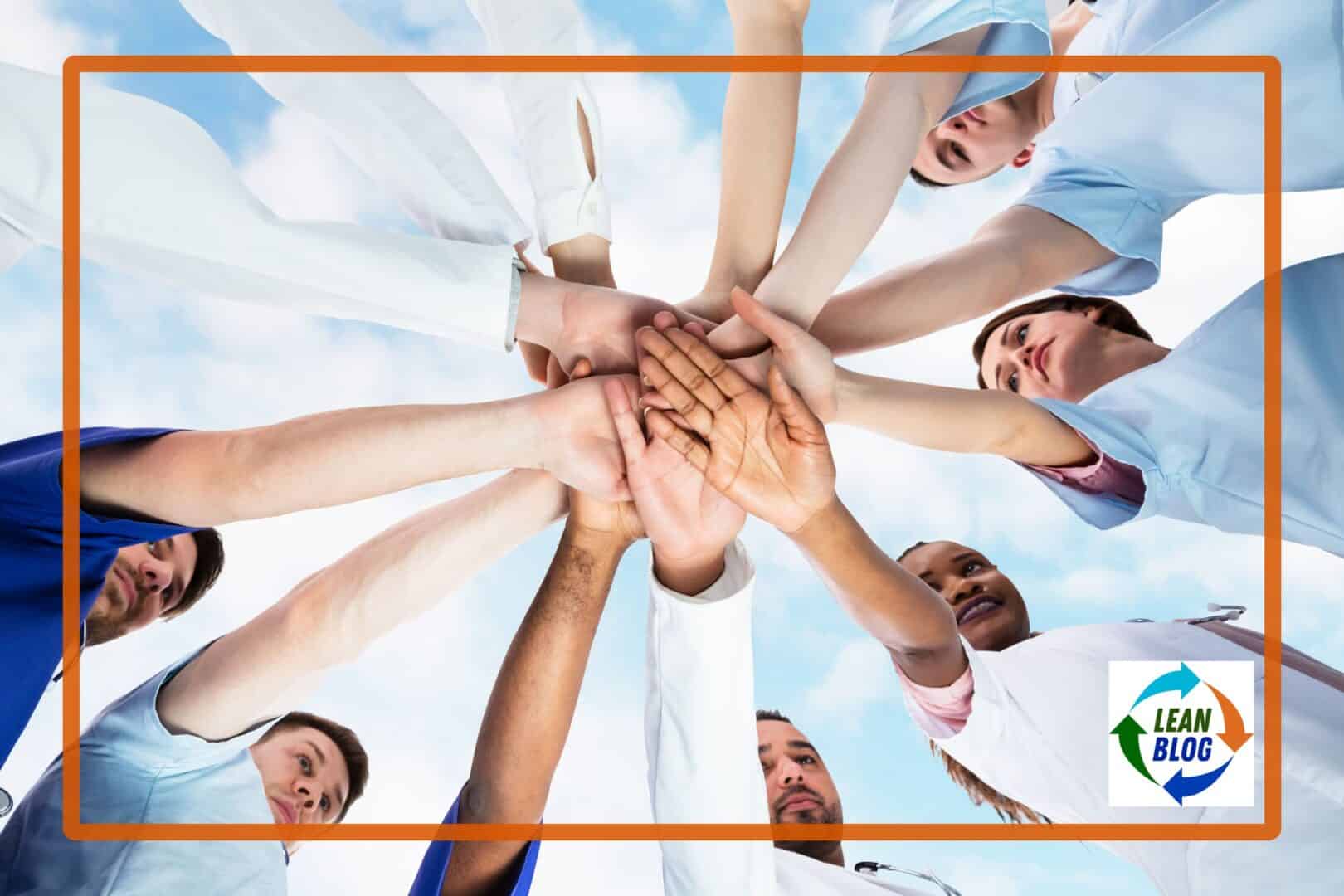
The Implementation at Allina Health
In 2013, Allina Health's Performance Improvement Department, supported by the Nurse Executive Committee, initiated Kaizen projects across four pilot sites:
- Adult/Pediatrics Unit in a rural community north of Minneapolis
- Cardiovascular Unit in suburban Minneapolis
- Emergency Department at a large hospital in Minneapolis
- Cardiovascular Unit at a hospital in downtown St. Paul
These projects began with a daylong conference (led by me) where managers and selected staff learned about the Kaizen process and the importance of engaging and empowering staff.
Visual Idea Boards: A Key Tool
Central to the Kaizen implementation were Visual Idea Boards, installed in highly visible locations within each pilot unit. These boards, divided into sections labeled “New Ideas,” “To Do,” “Doing,” and “Done,” facilitated daily huddles where staff and managers reviewed new ideas, discussed progress, and delegated tasks. This visual and interactive approach ensured continuous engagement and transparent communication.
Here's an example of such a board from another organization I've helped (see more examples here).

Examples of Kaizen in Action
- Numbing Spray for IV Insertion: Staff suggested using numbing spray to reduce patient pain during IV needle insertion. The idea required pharmacy approval, but the status updates on the Idea Board kept all staff informed, showcasing the collaborative effort and transparency of the process.
and
- Improved Supply Management: To address the lack of suitable supplies for finger sticks used to check blood sugar levels, a staff member suggested adding non-sterile pads to the supply box. This simple yet effective change improved quality and reduced costs.
Overcoming Challenges
The implementation faced two main obstacles:
- time constraints and
- the need for managers to develop effective coaching skills.
Some units formed committees to manage Kaizen activities, ensuring that staff had the necessary support and time to work on improvement ideas. Managers learned to act as coaches, fostering an environment where staff felt empowered to suggest and implement changes.
Results and Next Steps
The initial success of the Kaizen projects was evident.
Within six months, over 275 ideas were submitted, with 70% completed.
Notably, staff engagement and patient satisfaction scores improved significantly in the pilot units. For example, in the Adult/Pediatrics Unit, employee engagement scores increased in key areas, and patient satisfaction improved in communication with nurses and staff responsiveness.
Allina Health plans to expand the Kaizen methodology system-wide, leveraging the lessons learned from the pilot units. The organization is also exploring software solutions to enhance the tracking and feedback mechanisms for continuous improvement efforts.
Conclusion
The Kaizen methodology has proven to be a powerful tool for engaging staff in continuous improvement at Allina Health. By fostering a culture where every staff member feels empowered to contribute ideas and make changes, Allina Health has enhanced patient care, operational efficiency, and staff morale. The success of these initiatives underscores the importance of leadership in creating an environment that supports and values staff-driven innovation.
For more insights into the implementation and impact of Kaizen at Allina Health, you can refer to the full article titled “Engaging Staff as Problem Solvers Leads to Continuous Improvement at Allina Health” by Gregory Clancy and Mark Graban, published in Global Business and Organizational Excellence.
What do you think? Please scroll down (or click) to post a comment. Or please share the post with your thoughts on LinkedIn – and follow me or connect with me there.
Did you like this post? Make sure you don't miss a post or podcast — Subscribe to get notified about posts via email daily or weekly.
Check out my latest book, The Mistakes That Make Us: Cultivating a Culture of Learning and Innovation:
[…] Throwback Thursday: Participating Workers as Downside Solvers Results in Steady Enchancment at Allin… – Mark Graban revisits an article about participating employees as drawback solvers by the implementation of the Kaizen methodology. […]