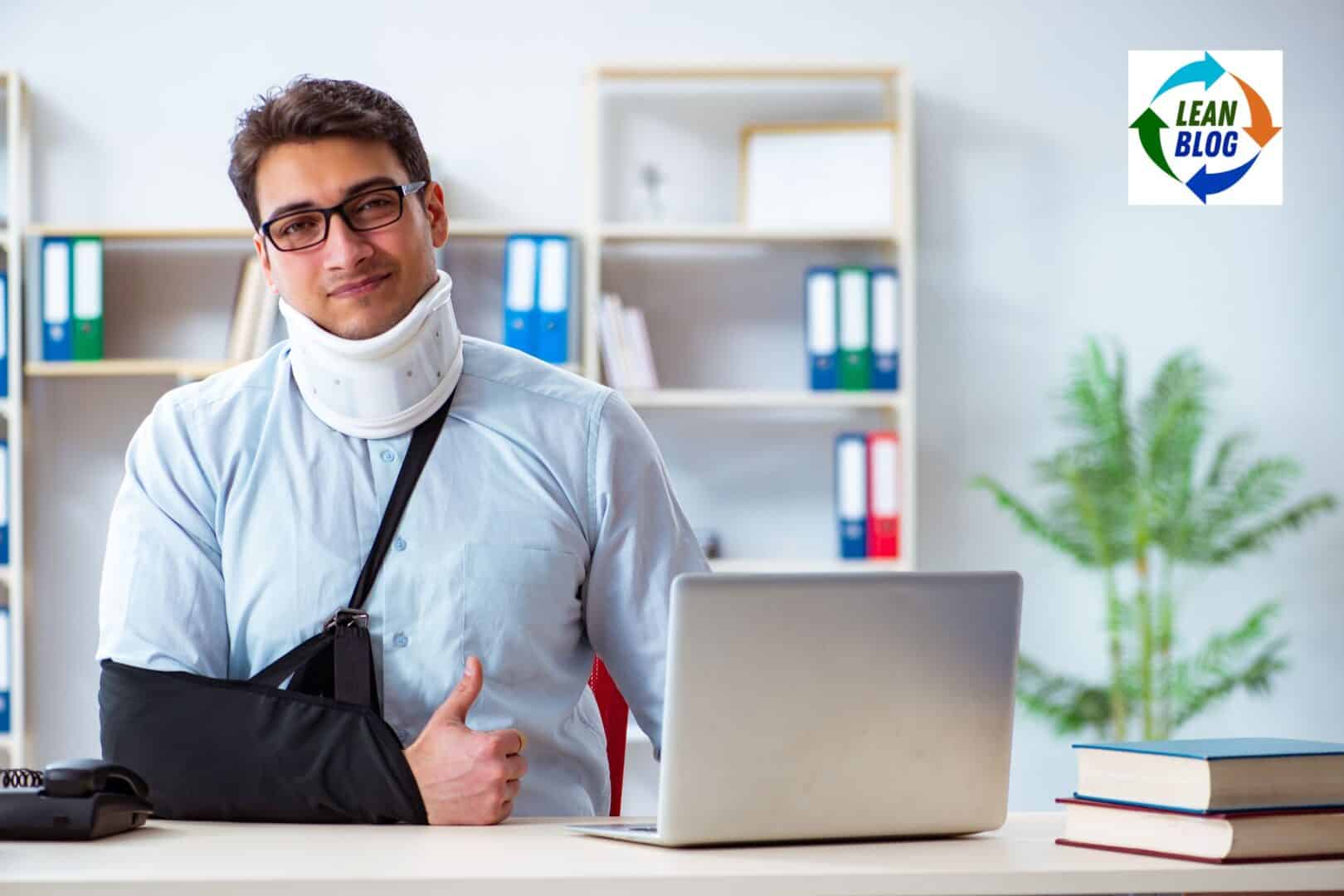
I was talking recently with a trusted friend in the Lean community. He told me a story. It's certainly believable, even if it's second or third-hand to me.
He had no reason to make up a story like this.
A relative of his works in a U.S. factory. Yes, we still have factories here.
I'll call this relative of my friend “Guy,” which is pronounced the American way, not the French way.
Guy's factory would claim to use Lean methods and might even claim a “Toyota Production System” label as its inspiration.
Guy's factory leaders say safety is important. That's great. SQDC — or Safety, Quality, Delivery, and Cost — is the common Lean mantra. It was at my GM plant in 1996, as I blogged about, and it's Larry Culp's mantra as CEO of GE Aerospace in 2024, as I've also blogged about.
Guy's factory leaders are, to their credit, trying to share performance-based gains with the frontline workers. They set up a monthly incentive program that pays a bonus each month when targets are hit. That sounds good.
It's a “balanced scorecard” of metrics, including safety — again, sounds good, right?
Here's the Catch
What's the rub? My friend said that if there's a month with a reported injury or safety problem, the team doesn't get the bonus.
I've shared this story, verbally, with a few people recently — people with varying ranges of Lean experience. And varying levels of human experience.
THEY ALL STARTED LAUGHING BEFORE I COULD SHARE THE PUNCHLINE.
Are you laughing? You might get it too. This isn't that complicated.
What Happened?
PEOPLE. STOPPED. REPORTING. SAFETY. PROBLEMS.
If they could get away with it.
Some injuries are easy to hide. I mean, if you're not bleeding and a bone isn't sticking through your skin, and nobody saw it, you could hide the injury. Hell, even if others saw it, they might readily conspire with you to keep quiet.
For the bonus.
This is, of course, so dysfunctional and counterproductive. A factory can't improve safety if they don't know about safety incidents.
Safety incidents are more likely systemic problems than they are “bad worker” problems.
Moral of the story: Don't punish people for getting injured. They don't want to get hurt. Don't punish people for speaking up.
Do better.
What Did Deming Say?
What would the late Dr. W. Edwards Deming, famed management guru, say about this?
I can't find the reference, but I vividly remember something Deming wrote about a factory that was incentivizing “zero injuries.” As a result, peopie stopped reporting injuries even when they were walking around with visible injuries, like splints and casts.
“Problem solved”?
The wild thing is that, in schemes like these, workers get what they want (a bonus) and management gets what they want (fewer injuries — wait, it's actually just “fewer reported injuries). Management might… get a bonus for this.
The conspiracy widens.
This is a good read:
Applying Deming to workplace safety
“Incentives should only be used to reward active participation in safety, not to reward an absence of reported injuries. Frankly, why isn't coming home in one piece reward enough?
Most workers I've talked to find safety incentives condescending and somewhat insulting. As one put it, “They give us a pizza party at the end of the month if we don't kill anyone. It's as if they think the only reason we will ever work safe is for the pizza”.
Do you have a similar story? I'm sure some reader does. Remember, you can comment anonymously and use “anon@anon.com” as an email address…
What do you think? Please scroll down (or click) to post a comment. Or please share the post with your thoughts on LinkedIn – and follow me or connect with me there.
Did you like this post? Make sure you don't miss a post or podcast — Subscribe to get notified about posts via email daily or weekly.
Check out my latest book, The Mistakes That Make Us: Cultivating a Culture of Learning and Innovation: