You don't find the root cause of a problem in a conference room.
OK, so we've gotten away from the whiteboard. Now what?
You might not even KNOW the root cause by thinking and talking out where the work is actually being done.
That's one of the most powerful lessons I've learned from former Toyota people I've been able to work with.
“We found the root cause,” somebody might say.
“How do you know?”
“Well, we talked through it,” they might respond.
My Toyota mentors would say that, at best, the team has a “suspected root cause.” It's a hypothesis. A supposition. It's not knowledge.
How do we confirm our suspicion about the root cause or causes? We need to TEST a countermeasure. If we remove the suspected root cause and the problem goes away (or gets significantly better), we might have proven something.
Root cause analysis doesn't end with talking. It starts with talking and must lead to action, which means experiments.
And sometimes those experiments don't work out… we didn't KNOW the root cause after all. So the process continues…
What's your experience with this approach? Have you ever been tripped up by stubbornly “knowing the root cause” and staying on the wrong path too long?
Please add your comment below and/or join the discussion on LinkedIn about this.
Please scroll down (or click) to post a comment. Connect with me on LinkedIn.
Let’s work together to build a culture of continuous improvement and psychological safety. If you're a leader looking to create lasting change—not just projects—I help organizations:
- Engage people at all levels in sustainable improvement
- Shift from fear of mistakes to learning from them
- Apply Lean thinking in practical, people-centered ways
Interested in coaching or a keynote talk? Let’s start a conversation.
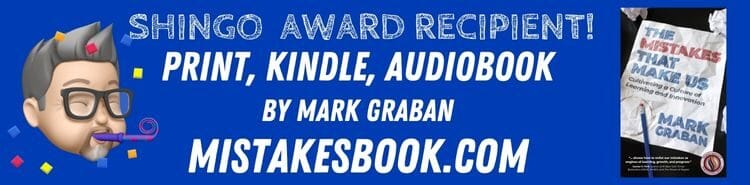
This Root cause analysis seems to really fall into the improve phase of the DMAIC where we are actually performing tests and confirming our hypothesis. This also seems like a very trial and error technique. With the your conclusion of “So the process continues…” Is this process applicable if you are not sure of the Root Cause? Or is it better suited to test root causes that have a high probability of being true.
If we are unsure of the root cause but are just going through many tests this would be hard to fully implement. I think using this after further research would be more applicable.
Thanks for reading and commenting, Dane. I guess I was writing in shorthand, sorry about that.
Yeah, I think the process continues if our initial experiments show that we either 1) don’t really understand the root cause the way we did or 2) if our countermeasures weren’t as effective as we had expected.