Thanks, as always, to Ryan McCormack for this. He always shares so much good reading, listening, and viewing here! Subscribe to get these directly from Ryan via email.
News, articles, books, podcasts, and videos about how to make the workplace better.
Operational Excellence, Improvement, and Innovation
Mario Kart Meets Pareto
Most readers are likely familiar with Pareto, ubiquitous in quality for his Pareto chart, and the Pareto principle (or “80/20” rule), and in optimization science for the Pareto front and Pareto efficiency. Pareto fronts and efficiency can be very helpful when faced with finding optimal configurations from many choices or selecting optimal portfolios.
Antoine Mayerowitz demonstrates how to use Pareto fronts and Pareto efficiency to identify the optimal build of player, cart, tires, and gliders for Mario Kart from 703 560 potential choices.
Quality at The Source
The Federal Aviation Administration has opened an investigation into Boeing to determine whether “Boeing completed the inspections and whether company employees may have falsified aircraft records” for the manufacture of the 787 Dreamliner.
Boeing's quality crisis highlights age-old debates and solution approaches deployed by organizations when defects leave the building. Most resort to adding rigorous training, auditing, and end-of-line inspection to prevent defects from escaping their business. John Shook asks, “What if…each of the 12,000 operators in the factory could be an inspector…what if each engineer (software or hardware) were responsible for ensuring that quality is built in at each step?” Shook shares insights on the conditions required to ensure quality can be built-in at the source.
The Many Uses of the Shewhart Chart
The proliferation of PowerBI and the democratization of data is meant to put more data-driven insights into the hands of managers and employees. Alas, a lot of this pursuit has led to dashboard overload, chartjunk, and unnecessary noise, rather than actionable insights.
Don Wheeler continues to make the case for the Shewhart chart as a method to create context and actionable insights.
Creating a Culture of Improvement
The Only Constant is Change
Employees are tired of change. The bad news? It's not likely to slow down. Leaders need to get to grips with change management.
Building a Lean Culture at GE Aerospace
“Culture can't be declared,” says Farah Borges, who oversees GE Aerospace's assembly, test and maintenance operations. “You have to build it.”
Larry Culp continues to walk the walk at GE Aerospace, and it's delivering results.Â
Get Off My Territory
Imagine what can be accomplished if managers spent less time protecting their turf and more time collaborating to solve problems. Why Territorial Managers Stifle Innovation — and What to Do About It.
Coaching – Developing Self & Others
Self-Handicapping
How often do we hear we need to get out of our comfort zone and embrace challenges in order to grow? Many people develop an esteem-preserving response to hold back when faced with a challenge, which, unchecked, can become a barrier to trying anything. Learn to recognize self-handicapping behaviours in yourself and others.
Follow Ryan & Subscribe:
LinkedIn:Â https://www.linkedin.com/in/rjmccormack/
Subscribe to receive these via email
Please scroll down (or click) to post a comment. Connect with me on LinkedIn.
Let’s work together to build a culture of continuous improvement and psychological safety. If you're a leader looking to create lasting change—not just projects—I help organizations:
- Engage people at all levels in sustainable improvement
- Shift from fear of mistakes to learning from them
- Apply Lean thinking in practical, people-centered ways
Interested in coaching or a keynote talk? Let’s start a conversation.
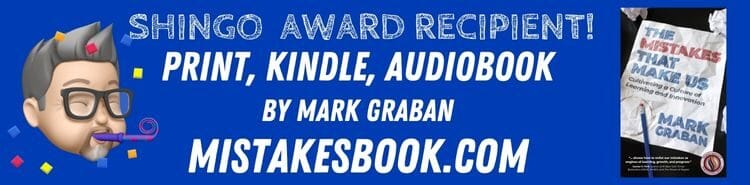