Scroll down for how to subscribe, transcript, and more
My guest for Episode #504 of the Lean Blog Interviews Podcast is Katie Anderson, author of the book Learning to Lead, Leading to Learn.
In this episode, Katie takes the reins along with me, Mark Graban, to discuss the transformative journey of Japan Study Trips. Recognized globally for its rich contributions to modern business practices, Japan has long been a beacon for leadership and continuous improvement. But how can one experience this powerful journey?
Strong leadership is integral to sustaining a culture of improvement. During these trips, participants get to hear from individuals like Katie Anderson, known for her insightful book Learning to Lead, Leading to Learn. Engaging with thought leaders deepens their understanding of the continuous learning process while expanding their networks. Not only do they learn about the principles, but they also meet and engage with their pioneers, reflecting the deep connection between leadership and continuous learning.
This discussion illuminates the importance of a culture where mistakes are seen as stepping stones to innovation. Personal engagements with companies recognized for their Lean practices reaffirm the significance of ‘being over doing,' making these trips a true journey of transformation and discovery.
Katie also recently hosted me as her guest on her podcast, Chain of Learning:
16 | Leveraging Analytical Systems Thinking to Drive Improvement with Mark Graban
Questions, Links, Notes, and Highlights:
- Learn more about Katie's November trip that I'm a part of
- Mark's website about Japan Tours
- How can we shift focus from doing to being in order to create a culture where better results and output are achieved?
- What role does continuous learning play in creating and fostering cultures of improvement and growth?
- How do leaders in organizations prioritize being over doing to cultivate a mindset and culture of learning and improvement?
- What are some common production principles and tools observed on shop floors, and how do they align with overall cultural objectives?
- What are the behaviors that need to become standard across an organization to create a culture of kindness, constructive response, and continuous improvement?
- How can leaders in various organizations and industries cultivate a mindset and culture of learning and improvement similar to those seen at Toyota?
- What role does sharing knowledge, stories, and experiences play in enhancing learning and strengthening connections within an organization or across industries?
- How do mistakes and constructive responses to them contribute to shaping a culture focused on learning and growth?
The podcast is brought to you by Stiles Associates, the premier executive search firm specializing in the placement of Lean Transformation executives. With a track record of success spanning over 30 years, it's been the trusted partner for the manufacturing, private equity, and healthcare sectors. Learn more.
This podcast is part of the #LeanCommunicators network.
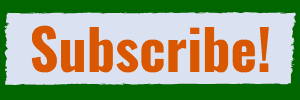
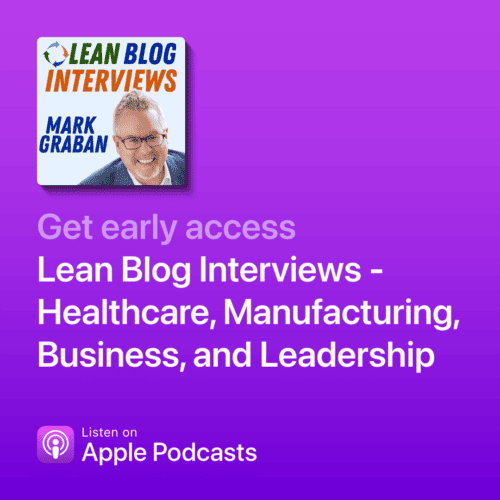
Full Video of the Episode:
Thanks for listening or watching!
This podcast is part of the Lean Communicators network — check it out!

Automated Transcript (Not Guaranteed to be Defect Free)
Katie Anderson:
I think we're live. Yay. Hi everyone. Katie Anderson here with Mark Graban and we are really excited to be talking today about our upcoming Japan study trip, which Mark is joining me in November 4. I have another trip that's happening in just a month in May, which is sold out.
Katie Anderson:
And so we're actively pulling together an amazing cohort and wanted to talk with you about the program and why Mark is so excited to be coming as well. So we hope you'll be joining us as well just to learn about Japan and Japan study trip. And if you're intrigued about the program, please reach out to me and go to kbjanderson.com Japantrip to learn more about the trip as well. So welcome, Mark. Thanks for being here with me.
Mark Graban:
It's good to do another livestream with you, Katie. People might note we're doing this on April 2. There are no April Fools jokes involved. Katie is planning another trip, as she's been doing, and we're going to talk about it today. I am part of that trip, which is not an April Fool, either.
Mark Graban:
So lot to talk about today. We're going to be able to take your questions before we talk about the trip. Katie, I'm assuming people are tuning in because they follow you, but there's maybe some of my followers who don't know. You want to introduce yourself?
Katie Anderson:
Oh, great. Well, Mark and I have known each other for going on two decades now. I was trying to think about that not quite two decades, but back when we both were working in healthcare operations, which is where I had started my lean journey. I had a first career, but my passion became lean and continuous improvement in healthcare and hospital systems. And then I started my own consulting practice and I worked over a decade ago and I work with organizations all around the world of all different industries to really deepen their leadership practices about how you create these cultures of continuous improvement of learning and high performance.
Katie Anderson:
And serendipity would have it that I had the opportunity to move to Japan with my family nine years ago, which was an incredible experience, not just for me personally, but has really transformed how I have been, the impact that I've been able to have with organizations and now bring people, leaders from around the world, have hosted over 100 people to Japan to go really have an enriched, immersive learning experience, cohorts from the same company, individuals like Mark, to really have some of that same experience that I feel like I was so fortunate to have by living in Japan for almost two years. Oh, and I'm also the author of the book Learning to Lead, Leading to Learn. One of the amazing special things that came out of my time in Japan was a friendship and deep professional connection with Toyota leader, 40-year Toyota leader Isao Yoshino. And after years of us talking, we realized we should write a book together. And I wanted to bring his, you know, decades of Toyota wisdom to the world as well.
Katie Anderson:
So that book has been awarded the Shingo Award, publication award. And, yeah, he's, he's gonna be part of the trip, too, which is so wonderful and amazing. So, yeah, that was the long version of me.
Mark Graban:
But, yes, well, we'll come back and I'm sure bring up the Mr. Yoshino connection that we discovered we had going back to my first trip there. Yes. And congratulations on the Shingo prize for the book, Katie. It's a great book. I hope people will check it out.
Mark Graban:
My name is Mark Graban. I am an author, speaker consultant. I'm going to hold up my most recent book, the mistakes that make us. Cultivating a culture of learning and innovation hasn't won any major awards like a Shingo Prize. But reviews are positive and people check out the book.
Katie Anderson:
It took a few years, Mark. It wasn't the first. You know, your book just came out. But also there are stories from me and Mr. Yoshino in the book about some of our favorite mistakes. And, and one of the key things about learning from mistakes and how do you embrace and create this culture where learning is the attitude?
Katie Anderson:
And that's a real key part of the whole Japan study trip program, too, of where we go. It's not just Toyota. It's like, how are other organizations, other leaders really creating this, cultivating this mindset and culture in their organizations as well?
Mark Graban:
Yeah. When we and you and Mister Yoshino so graciously shared those stories, not only in your book learning to lead, leading to learn, but in an episode of my favorite mistake. And then, you know, I summarize synopsis version of the story in my book, but there were also other stories from other Toyota leaders that I was able to sort of connect dots to and draw some through lines around, you know, culture. I don't think it was just a coincidence that Mister Yoshino had the same response from local leaders when he was involved in a mistake of loading the wrong chemical into a paint machine. David Meyer, my friend and guest on the podcast, had a similar experience in Kentucky.
Mark Graban:
It was some sort of plastic molding machine, but again, it was wrong. Chemical wasn't even supposed to have been there. And, you know, I think the leadership response was, was kind and constructive and not blaming that stands out in those different stories.
Katie Anderson:
Well, and that's really what creating a culture is all about. Right? So it's not one offs. It's about the, this is the behavior that just becomes the standard and the norm across an organization environment. And it can be expanded beyond, like, the physical confines of a country or a, you know, a factory, because it's all about how do we, whatever the norms that we create, and it's possible to make change as well.
Katie Anderson:
Right?
Mark Graban:
Yeah. So one other connection between podcasts and not change, but chains, chains, chain of learning, Katie's new podcast. Tell us about that.
Katie Anderson:
Yeah, so it was exciting. I've, you know, I've been doing videos and audio for years, but decided to leap into, I was inspired by Mark's prolific podcasting to leap into a more formal podcast. And I've called it Chain of Learning, which actually comes from a phrase that Mr. Yoshino said to me when he was talking and reflecting about his time at Toyota, that it was really, that he was really grateful for this, what I call this chain of learning about sharing knowledge and helping each other grow and get better. And to me, that's what a podcast can help do or what we're doing here. It's like we're sharing knowledge, and it's through that connection between us that we create the strength.
Katie Anderson:
And just yesterday, Mark and I recorded a podcast episode for Chain of Learning, which will be dropping on May 1. So be sure to go in and subscribe now and go listen to some of the past episodes. I've had Carol Dweck on the show, the author of Mindset, and some GE leaders and some, you know, Karen Martin and others just really talking about how do we create and foster these cultures of continuous learning. So, Chainoflearning.com and you can go to your favorite podcast player and subscribe. And we also talk.
Katie Anderson:
I share a lot of stories on the podcast, too, about things that have inspired me in Japan, particularly this one leader who, it's not at a Toyota supplier, is a totally different industry. And someone said, how do you create this culture where people are happy and contributing their ideas, and the company considers happiness as their purpose? And we're actually going there both in May and in November. And he said, you have to focus more on being than on doing. It's so easy to get distracted by all the things we have to do, but it's about how we be.
Katie Anderson:
And to me, that's a really profound takeaway about how do we really not get, especially in the west, we get really focused on the doing and the outcomes and the results, but it's really the being that allows us to create the environment and the culture where we do get better results and output. So that's another key learning as well.
Mark Graban:
Yeah. And it's about learning and learning. In my experience with past trips, it's learning from the host companies, it's learning from the guides, it's learning from the other people who are part of the tour. So we were going to address this question. Yeah.
Mark Graban:
So I'm going to go a little last sequence, but Harvey Leach is on watching the live stream and he commented that he's excited to be going on the trip with us. I'm excited he's going and I'm going to pull up a different book here. Harvey Leach from the UK contributed a chapter to this anthology book that I edited and published called Practicing Lean and so really excited to be part of each other's chains of learning in Japan. And he asks for me, you've been to Japan before and I think you could answer the same question, Katie, what are you looking forward to on this trip compared to what you've learned previously? So let me address that.
Mark Graban:
This will be my 6th trip. I went first off in 2012 and then I went four more times up to mid December 2019. So like pandemic COVID was, I think, probably already spreading at that point, but we didn't really know what was coming. And so I haven't been able to go back to Japan in five years. So there's a couple elements to it.
Mark Graban:
I've gone on different trips organized by and led by different people through two different organizations. And each time there's either a deepening of the lessons you think you've already learned, new lessons, new organizations to visit. And Katie, as you were talking about, I'm going to call it the happiness company, for lack of a better way of putting it. That's not an organization I've had the chance to meet. Your network, your connections, your perspectives from having lived there are different than the perspectives, good perspectives of people I've gone with previously.
Mark Graban:
The final thing I'll add is just the connection back to Mister Yoshino when you started collaborating with him. And I'll have to admit it took me a while and I think it was pandemic brain or I maybe, but anyway, I forgotten some important details from that very first trip in 2012. And I went back through pictures and notes. I'm like, oh my God, Mr. Yoshino, was that Toyota executive who came and taught a lesson in that first trip. So at some point, the trips all blurred together, and I'm embarrassed that I forgot that detail.
Mark Graban:
But I still had the printout of his slides and the lessons, and I shared it with you, Katie. So I'm excited to reconnect with him in person, too.
Katie Anderson:
It's so great. Well, you met Mister Yoshino before I did. I met him in 2014, right before I moved to Japan. And Harvey, we are so thrilled that you're going to be part of this cohort as well. In November.
Katie Anderson:
I want to get back to what Mark said, too. For me, I lived in Japan for almost two years, and what an incredible gift for a lean practitioner and a continuous improvement zealot to go and have this opportunity to be there and be living there, not just on a trip. And I really saw it as one of my key missions in life, to not only learn as much as that I could for myself, but also share that with others. And I really feel that chain of learning has always been part of me. I started writing my blog, and I have to say thank you to Mark.
Katie Anderson:
He was so incredibly helpful in me, like, figuring out how to blog a decade ago, and that was the beginning of what became the book. But going back to, you know, I've gone to so many companies and talked to so many leaders and cultivated, like, deep personal relationships with them. And actually, the happiness company came out of a relationship with another manufacturing company. And this female executive has taken her team to Gemba to go learn at other companies in Japan. And so she made that connection for me.
Katie Anderson:
But the people who come from around the world are also these great lean thinkers, these great continuous improvement practitioners or executives leading positive change in their organizations. And so I sort of hold that space for the collective learning and bring my facilitation skills to help foster that dialogue and the learning that happens, it's unique for each program. And, you know, I've gone to some of these companies, and now I'm going back. It's been about every six months since the world opened up again. But even if I'm going to and I don't go, my program's not the same every time.
Katie Anderson:
But there's some, you know, the themes are key, the same, and some of the companies are the same. But even if you go back to the same place six months later, you see something new, a leader says something different. That's, like, sparked by a question or a reflection of what's going on currently. And so it's actually, it's kind of, it's interesting to see both new places as well as go back and see what's changed or what hasn't changed or what's evolved. And it's been really interesting to see how Japanese companies also have been handling the pandemic.
Katie Anderson:
You know, they've encountered the same challenges that we have globally as well. So there's so much value in either going, you know, as Mark's going back some new places, maybe there'll be some similar places as well, or hearing Mister Yoshino, but you just get an enriched, deepen understanding of what this really is all about.
Mark Graban:
So. Yeah, well, and I think one thing that's different, and I'm excited about with your trip is I think it seems like you're very intentional about building that cohort before the trip. It's not just the six days of the trip. And previous trips I've gone on have made some attempts at post trip reflections and having some sort of online forum or meetings. But can you tell us a little bit more about the process of how you really try to help establish that cohort so that we can kind of prep together, learn together, reflect and apply afterwards?
Katie Anderson:
Yeah, so I'm in the thick of that right now with my May study trip cohort of 18 people. It's a full program right now and sort of about three, four months before each trip, we start an active learning process together where I have several times where we come together to have conversation, not only just learn about each other, but some train, I don't want to say training, but talking about the experience, some of the companies, I have a lot of online resources of recordings with Mister Yoshino and myself, some other leaders and resources. And we have some discussion around that because tilling the soil, the NEma washi, for your experience, will help enrich and make you have your eyes more open and asking better questions. And also the cohorts already come together for some shared learning as well. And then learning happens through reflection and through application.
Katie Anderson:
Right. And so we have, of course, an amazing six days in Japan and have many times for a reflection throughout the week. But I have times for us to come together and have discussion about how are you applying, what you're learning, what does this mean at your back? And then we always have a discussion forum that's still available for each cohort to be sharing their learnings and both an online platform to share materials and then a WhatsApp group as well. So it's friendships are made that last a lifetime.
Katie Anderson:
I mean, I love seeing the collaboration that continues to happen through each cohort, you know, as they continue to go back and continue into their work and making an impact from what they've learned.
Mark Graban:
Yeah. And I've maintained some of those connections with individuals from previous trips. People, you know, becomes your own personal, global lean network.
Katie Anderson:
Yeah.
Mark Graban:
Even. Even more so now. One thing I wanted to share, and we're going to talk more about the value of a trip like this. It's great to be able to do it. You know, I look at going back as a learning opportunity and a personal opportunity.
Mark Graban:
I mean, I love going back to Japan, so I won't hide that, like, to be able to go back and just, again experience the country, the food, the sites, cultural experiences. But, you know, I think going back to my very first visit, reflecting on what some of the key takeaways were like, you expect to go see some world-class organizations. And when I've gone before, we would go see some really top Japanese hospitals that were utilizing lean on top of decades of TQM practices. So, you know, TQM wasn't a fad in Japan. There are companies that have practiced that very diligently for decades, probably more so.
Mark Graban:
There are some companies in the US, I'm sure, but you don't hear about TQM in quality circles. But then, you know, go see companies like Toyota suppliers or other manufacturers. If you ever heard about, let's say, a U shaped cell, but you've never seen one. Well, you will. I mean, I've seen other U shaped cells back, especially when I worked in manufacturing.
Mark Graban:
But the best manufacturing, the most impressive choreography, was a U-shaped cell in a part supplier. I just saw how the work flowed and was designed in a way that was graceful, not taxing. And there's that element of it–work and design. But then think about continuous improvement and management systems. And so that one key takeaway I had from that first trip was that Toyota is not.
Mark Graban:
Well, I could say it the other way around. Every Japanese company is not like Japan.
Katie Anderson:
No. Or Toyota, again, make a mistake. Well, no one's the same, right? Yeah.
Mark Graban:
Not every… slowdown, not every Japanese company is like Toyota. And I think for anybody around the world who says things like, well, lean would be, TPS would be a lot easier if you're Japanese. And, like, that's diminishing what Toyota has really worked at and accomplished and what other companies, and there are hospitals that have learned directly from Japan, it's not easier or automatically because they're in Japan or because they're a Japanese company. And I think that's an important lesson. It should hopefully strengthen people's commitment, say, well, we can put in that work and we can try to build something of our own.
Mark Graban:
What do you think?
Katie Anderson:
Yeah, that's really important to highlight and is actually part of the framework that I set us up for on the first day on Sunday about thinking about looking at everything. It's like, what do you think is Japanese culture? What is something? Maybe it's more as Toyota specific culture or maybe something that sort of general human humanity. And, you know, where does this sort of lean thinking in practice, what we call lean thinking in practice lie?
Katie Anderson:
Because that is not actually a construct in Japan. Like, that is our foreign attempt to try and describe what was happening at Toyota and some other companies. And so you can't actually go to another company and say, are you practicing the Toyota production system? They'll be like, no, we're doing the Agora production system, or this is just Kaizen. Or there's not as many labels and words, but they're doing it.
Katie Anderson:
They're doing it from a mindset and from a philosophical standpoint and then also applying the principles and tools. But you're right. I mean, it was shocking to me. I kind of had a, I knew this wasn't going to be the case, but I did have a little bit of a shock when I moved to Japan to realize, wow, like, not all of Japan is how we are taught that Toyota is. And so there are really some special things that Toyota and some other companies have done in Japan to take.
Katie Anderson:
They definitely leverage some strengths of the Japanese culture, but there are some things they've had to overcome. I think it's really important for us to remember is there are different challenges for us, maybe from more of our western cultures, to do some of this. But there's some challenges that overcome that, like countermeasures that Toyota had to put in place for this hierarchical culture where people expect the top down, just wait for the answer or don't think outside the box because you got to conform to certain things. It's not necessarily there's different things that are easy and different things that are hard, depending on both your personal style, your country culture, and your company culture.
Mark Graban:
And things I've seen and things I've talked to you about and seen you write about. There does seem to be, I'm going to generalize cultural norm around standard practice routine, going into some sort of shop and the way they'll rap what you got, like structure and consistency to that. But then I've also heard people talk about something you experienced of maybe the unwillingness or inability to customize. Was it a gelato?
Katie Anderson:
It was a gelato store. And I was so sad that the gelato store was closed. My kids were looking forward to it. It was open still in May, and then it was closed by the time I'd taken them back last October. But, yeah, so kata, which is now, a lot of us think of kata as this routine that was coined by Mike Rother around the Toyota kata, which is actually just something, again, foreign words that.
Katie Anderson:
Trying to describe a pattern and routines that happen at Toyota around problem-solving and coaching for problem-solving. But the word kata itself came from martial arts. It's a japanese word meaning form or pattern. And so there are kata forms and patterns that are expected throughout, you know, around society. How do you hand out business cards?
Katie Anderson:
I mean, you turn it around, you bow. You have to make sure you slip your business card underneath to show deference and like this. So there's all these sort of things you have to do. Now, don't worry. As a foreigner, you're given a pass on a lot of the kata, but the Japanese are expected to know this because they're taught and trained at an early age.
Katie Anderson:
This allows society to function, this density of population in these cities, to function in a way that's so. I mean, it's amazing, right, Mark? It's clean. It's. Things run on time.
Katie Anderson:
You're not, like, it's not aggressive. You can walk through places that are so densely packed but so smooth. But it's because everyone follows these sort of katas of society and norms. However, the flip side of that is that if you're all following the constraints of a certain pattern or routine, it can be harder then to break out when you're trying to have innovation or. Or to speak up or other things as well.
Katie Anderson:
So it doesn't always come easy. And something I really thought was fascinating, and we should have talked about this on the podcast yesterday around the concept of pulling the and on was not something that came naturally to the original Toyota workers. There's a video at the Toyota museum which I take people to talking about. When Taiichi Ono started to introduce the and on system, which was the pull originally pull, the cords show a signal, Andon's a signal that there was a problem on the line. People were resistant.
Katie Anderson:
They didn't want to do that. And so he had to change the culture to make that okay, because people didn't like something new. This was different. And so, again, I really like that example because it shows that that's something we think is like just part of the Japanese toy it away. It is now, but they had to put intention to shifting that mindset and that culture to make it happen.
Mark Graban:
And I've got a kind of a pet theory that the cord and the chimes and everything, that's useful because there is noise in a factory. But I've got a hypothesis. I haven't been able to get the real detailed origin story of, let's say, y accord, and it could be as simple as that. Like, well, you don't want people to have to shout, but I've got this theory that maybe the physical motion of reaching up and pulling a cord in some ways might be less intimidating than speaking up verbally about something. And again, it could be totally a practical matter.
Mark Graban:
I'm reading too much into it. But I think it goes to show we should give credit to Toyota for cultivating that culture instead of saying like, oh, well, it was easy and automatic. It's not going to be easy and automatic in our organization or american companies. Let me give a shout out, because today's the day GE was in the news. GE Aerospace is now completely independent.
Mark Graban:
GE Vernova has been spun off. But as Katie and I both heard and actually came from the section at the AME conference where you were interviewing, having conversation with Larry Culp on stage, where Larry was sharing reflections of coming in as an outsider and detecting and realizing that he was inheriting a culture that tended to shoot the messenger related to bad news. And Larry articulated he had to not just tell people to speak up, he had to demonstrate that it was actually okay when people did start speaking up. That's the type of process I think any company can go through with committed leadership to saying, we are going to change the culture, not just lecturing people, well, you should pull the andon cord or you should speak up, like making sure that people feel, using a different phrase that Larry didn't use in that talk, psychological safety. But any company can do that.
Katie Anderson:
Yes, for sure. And so it's great to see that a big learning point is that it's not just easy in Japan, and you get to also see how some japanese companies are really doing something about this in a different way. And I feel like there's something very inspirational about people come back from these trips saying, I understand the heart side of this so much more. We're so focused on the outcomes and the doing. But like, wow, just like the profound heart centered leadership and going through hard times.
Katie Anderson:
I mean, we're going to still manufacturing companies. And it's not like everyone's like going around singing Kumbaya, but there's this real passion you'll see behind me. There's this sign here. This is all the same word. Actually, it's the word intention in Japanese, and it comes from two sub symbols.
Katie Anderson:
The first one actually has, is made of two symbols meaning samurai and heart. And so the top symbol here actually is a Japanese word that means pronounced kokoro zashi, which means the strength of your heart. And it's meant for around a leadership perspective of like, what's your energy to inspire change and positive inspiration for the people who work with you. What's the thing that gets you going? And you see this Kokoro Zashi throughout all the Japanese leaders that we talk with.
Katie Anderson:
And then the bottom symbol in intention behind me is direction. So I see it's like, what's your heart? What's that impact you want to make? And then the direction of your actions? And so we see that so tangibly when we go to these companies and talk to these japanese leaders.
Katie Anderson:
And that's really inspirational for people. Like kind of, it kicks, kickstarts you out of like all the process improvement, which is important. I don't want to diminish that, but really that leadership and the culture side is how we're going to do all these, all these things. So it is real. It is really like this revitalization of your passion for all this work that happens on these trips.
Mark Graban:
Yeah. And it sounds like it's not a quote unquote lean tools to finish tools, but I've been to organizations where you see the foam cutouts in the drawers of not just, I would say, the super important things like medications and supplies and a hospital, like, oh, that's really impressive, physically impressive, well organized workplace structure. But then you see some organizations like, okay, well, we've done the same thing with pens and an individual's desk drawer. I'm like, I'm probably not going to take that practice home, but I want to learn more about cultivating continuous improvement and the role of leaders and commitment to employees and those more philosophical management principles that I think can and should be kind of applied and brought home.
Katie Anderson:
Well, you're, you're joining the right, the right trip because that's the whole focus of my program. Of course, when you go see out on the shop floors of all these organizations, you'll see aspects of the production principles and, you know, 5S and other poll and Kanban and like SMED, like the single minute exchange of die and like all this, which is super exciting. And, you know, you can take a lot of pictures of that, but the real, that's sort of a secondary of what you see, the focus. And really where I design this and talk with the leaders before we go to these organizations, we really want to hear from their leadership perspective. And we're talking to senior executives, to senior directors who are really leading the change and then also frontline managers and employees as well.
Katie Anderson:
But, like, what does this mean from a culture standpoint? What do they have to do? What are the challenges they've had? How are they leading? What's their vision?
Katie Anderson:
How does that connect? And then how can we, we being you all who are joining, be bring that back and think about that from your own leadership perspective, whether you're an internal or external coach or consultant or an executive on the trip who's really responsible for your organization.
Mark Graban:
Yeah. Let's talk a little bit, Katie, about some of the logistics and getting around. I know for me, the first time I went to Japan was part of one of those groups in 2012. You know, it's just, if you've never been, you think, well, it might be intimidating, hard to navigate. And I would say as an American who only speaks maybe eight words of Japanese, it is surprisingly, it can be overwhelming, like sensory overload the first time you're there and a lot to take in, but surprisingly not easy to navigate.
Mark Graban:
You know, signage and using public transportation and being able to order food and check into your hotel, like, most of that is easily handled in English. And, you know, I think being part of a group where you have people to translate and be a guide is a perfect way to get introduced to Japan for a first time.
Katie Anderson:
Absolutely. So, you know, when you're part of my program with me, I have my partner who's also, you know, speaks translator and helps us. So once the program starts, like, you are totally guided. That being said, japan's a really great entry point because everything functions so, like, functions so smoothly. I mean, the train, they apologize when the train's running a minute late.
Katie Anderson:
Right. You know, like, so the precision things happen. It's orderly. And they're, especially since the Olympics, since the pandemic, the signage is even more so in Romanji, which is the roman characters. I don't want to say English because it's not actually English, it's just our Alphabet from the roman Alphabet.
Katie Anderson:
So it's much easier for you to see and read things. But that visual signage, I mean, just even using all these lean principles. The visualization is so easy to get around. There's like signage on the floors, on the train stations, let you know where to go, color coded. And I mean, everything runs so smoothly, so it's a really great entry point.
Katie Anderson:
And also, I mean, what's amazing, too, is like, Google Translate. We had all these things like Google Maps. It all helps getting around. And Japan's the safest place you will ever go. I mean, I, as a woman, feel totally fine walking around the middle of the night.
Katie Anderson:
You know, never feel fearful. And so it's a great place, even if you're traveling on your own beforehand, just to feel, go out and explore and walk around, open your eyes, experience other things. It's really fabulous. I mean, I lived in Japan and I still, even before the pandemic, I was going back twice a year. Last year, I spent probably seven weeks in Japan over three trips.
Katie Anderson:
And I'm so thrilled to be going back as well. It's just these contrasts of society, which are so amazing. And it's easy ZD get around. I do speak a little japanese now, but you don't need to.
Mark Graban:
And with the jet lag, if you're coming from the US or from a lot of places, you will be up in the middle of the night. And, like, I've gone out for a walk at 04:00 a.m. And yeah, crime is very low in Japan. And yeah, it's easy to navigate. I would encourage, you know, if you're able to go a few days early, do some self exploration in Tokyo, and then take the bullet train to Nagoya to meet up with the group.
Mark Graban:
That's a great experience. If you're not taking a connecting flight into Nagoya, or if you can tack on a few days afterwards when the trip ends to stay in Tokyo and go do your own exploration of cultural events or music and food. It's not all sushi all the time.
Katie Anderson:
No, well, that's, you know, sushi is only one of the one cuisine of japanese food. So there's a lot of yakiniku, which is the grilled meat yakitori, the grilled chicken, a lot of vegetarian. I had a woman who is vegan on my trip and gluten free, and she found no problem of getting wonderful food at every meal. So don't worry if you have dietary restrictions, you know, it'll work. Work around that as well.
Katie Anderson:
And I encourage people to try something different. Like, there's some textures I know I don't like. I've tried them, but, like, try things you might be surprised. Like, it's a, what you think of as japanese food is totally different when you get to Japan, and the, the quality of the, the fresh produce is just unparalleled. I see Isaac's comment.
Katie Anderson:
Isaac, it was so great to have you on the Japan trip in May last year and was so wonderful. I know you're putting, Isaac's putting together a presentation of his reflections a year later of what he's learned. So I'm looking forward to seeing that Isaac, when you pull that together.
Mark Graban:
And as Isaac added in the comment, he highly recommends the trip. Isaac had written a great blog post series on LinkedIn.
Katie Anderson:
Yeah.
Mark Graban:
Want to go read about his experiences? But he says going to Japan to see this firsthand gives you an in depth understanding of the culture, history, people, norms and leadership approach to business that is developed into what we study and practice today. So go check that out as a preview that hopefully, you know, if you're able, we can get your company to send a group or to send you, or if you're able to go individually, please do come join us. It's November 10 to 16th. You can learn more at Katie's website, kbjanderson.com.
Katie Anderson:
Japantripantrip. Yeah. And go on LinkedIn as well on the hashtag hash Japanstudytrip. You'll see, you know, Isaac's posts, other people's posts about the trip, my posts as well, my videos on my YouTube channel. So even if you're able to join us in Japan, you can experience it from afar.
Katie Anderson:
And if it's piqued your interest, please reach out. And we're actively taking applications right now, and spaces are filling up. So really excited to potentially have you join us as well.
Mark Graban:
Yeah. Is there anything else that we want to cover or.
Katie Anderson:
No, I just, we didn't have any.
Mark Graban:
Other questions come in. So.
Katie Anderson:
Yeah, no, that's great. I mean, to me, every trip is an incredible experience. I'm always sad when it ends because of the friendship and camaraderie that develops on the program. I mean, that's why it's really important to me to have not just, you know, when you apply, we have a conversation to make sure that you're the right fit for the trip and that the trip's the right fit for you. And you're learning because that's, you know, we spent an intense week together and it's, it's really exciting.
Katie Anderson:
I'm thrilled that Mark's joining me. I mean, Mark, you were so helpful, actually, in making some introductions from some of your past trips. When I was living in Japan, I had an opportunity to visit some hospitals because of your connections and met some other people. So I appreciate our chain of learning is coming full circle now that you get to come back with me, if you've helped.
Mark Graban:
Happy that you're doing this. Happy I can go?
Katie Anderson:
Yeah, it's great. Well, if anyone has any other questions, feel free to reach out to me on my website and kbjanderson.com. You can send me an email, send me a message on LinkedIn and we'll get connected there as well. So if it's been on your bucket list, I highly encourage you to go also, because Mister Yoshino is 80 years old and I hope he's around for a long time, but his energy is up and he was hospitalized for COVID last year and it was really scary. But he's so excited.
Katie Anderson:
He's planning on coming to half the program in May and wants to come to the same amount in November. Joining for the full day, going to the site visits, joining for meals on the bus so you can have like, intimate conversations with him. This is not just like a lecture and this is unparalleled access to Mr. Yoshino that he doesn't. He doesn't do this for every trip. It's because of our partnership and he knows that he wants to come in and help.
Katie Anderson:
You have a great experience as well.
Mark Graban:
That's great.
Katie Anderson:
Yeah.
Mark Graban:
Again, Katie's book. Want to hold that up to lead, leading to learn a lot of great stories in there. Her podcast is Chain of Learning. My most recent book, again, is The Mistakes That Make Us: Cultivating a Culture of Learning and Innovation.
Episode Summary and Article
Exploring the Transformational Journey: Japan Study Trips
Japan, a nation steeped in history, is also known for its contributions to modern management and business excellence. Its techniques and philosophies have become a beacon for organizations worldwide looking to enhance their practices in continuous improvement and leadership. Japan study trips serve as a conduit for leaders to immerse themselves in an environment that fosters learning and growth. But what exactly can participants expect from such a transformative experience?
The Birthplace of Lean
Understanding the origins of lean management is crucial to comprehending its nuances, and Japan is its birthplace. A study trip to Japan isn't just about visiting companies or observing the lean philosophy in action; it's about engaging with the way Japanese culture seamlessly integrates principles of continuous improvement into daily operations.
These trips are often led by experienced practitioners who have not only studied the lean methodology but have applied these principles in various industry contexts. Their extensive networks provide participants access to a range of organizations that exemplify lean thinking and its application beyond the stereotype of automotive efficiency, illuminating its potential in healthcare, service industries, and more.
Advancing Leadership: From Learning to Leading
Leadership is at the core of building sustainable cultures of improvement, and a Japan study trip often pivots around this precept. One such leader in the lean community is Katie Anderson, an author and consultant known for her work in leadership development. Anderson, through her book “Learning to Lead, Leading to Learn,” shares insights from her experience and from the perspectives of notable figures like Isao Yoshino, a 40-year veteran of Toyota, illustrating the deep connection between leadership and the ability to foster an environment of continuous learning.
Participants on these trips get to not only learn about these principles but also meet and engage with thought leaders who have shaped these practices over decades. Networking with industry peers from around the world further enriches the learning experience, creating a dynamic environment where diverse insights contribute to a more profound understanding of effective leadership.
A Culture of Learning and Innovation
Embracing mistakes and fostering a culture of innovation can lead to improved processes and better morale within an organization. Expert consultants like Mark Graban, author of “The Mistakes That Make Us,” underscore the significance of cultivating an attitude towards learning from errors as a path to innovation.
Visiting companies with exemplary records in creating such cultures provides valuable case studies for participants. Whether it's a Toyota supplier or an entirely different industry, the common thread is the focus on nurturing an environment where every team member contributes and feels valued. The concept of ‘being over doing' resonates strongly during these trips, where the emphasis lies not only on work activities but also on the behavioral norms that drive excellence.
Chain of Learning: The Podcast
Katie Anderson has extended her influence to podcasts with “Chain of Learning,” echoing a sentiment shared with her by Isao Yoshino about the importance of sharing knowledge and fostering growth. In these episodes, thought leaders from various backgrounds discuss how to create and sustain cultures that prioritize continuous learning.
Through such mediums, the chain of learning extends and strengthens, allowing these experiences and insights to reach a broader audience. The podcast complements the more tactile learnings of the study trip, enriching the pre and post-experiences of participants.
The Happiness Factor: Purpose in Practice
Among the essential discoveries that participants can expect from visiting Japanese organizations is the profound understanding that employee happiness can be central to a company's purpose. Learnings from a non-Toyota company on a Japan trip inform that focusing on the well-being of employees leads to more engaged teams and fosters an environment where people are not just more productive but happier in their endeavors.
The study trips offer perspectives into how such cultures are cultivated and sustained, providing a blueprint that leaders can adapt and apply to their respective organizational contexts. This holistic view of company health, where productivity and contentment are interwoven, is perhaps one of the most crucial takeaways from a Japan study trip.
Each section here sustains the conversation initiated by Katie Anderson and Mark Mark Graban in their dialogue, reflecting the principal topics such as the evolution of lean practices, leadership development, the value of learning from mistakes, the extension of knowledge via new platforms like podcasts, and the indispensable human aspect of creating happiness within a corporate culture. These trips are more than mere excursions; they are profound journeys of discovery and transformation.
Facilitation and Repeat Visits: Enhancing Dialogue and Discoveries
Facilitation plays a pivotal role in the success of a Japan study trip. Skilled facilitators like Katie Anderson not only bridge the cultural and linguistic gap but also curate opportunities for enhanced dialogue between the participants and the host companies. This exchange is crucial for a richer understanding of both the nuances of lean management and the leadership philosophies adopted by Japanese organizations.
Enriching these trips is the possibility of repeat visits; going back to previously visited companies can reveal the subtle transformations and evolutions in practices that occur over time. A change in leadership or the implementation of a new process might not be immediately evident but returning after a period can cast these in a more discernible light. The impact of global challenges, like the pandemic, has also formed part of this ongoing dialogue, showcasing the resilience and adaptability inherent to the continuous improvement mindset.
Pre-Trip Cohesion: Building a Foundation for Learning
Preparation before the physical journey to Japan is as much a part of the learning process as the trip itself. Establishing a cohort with its own unique dynamic is central to facilitating pre-trip learning. Through iteratively engaging with each other, participants establish a fundamental understanding of expectations, forge connections, and begin the process of shared learning.
With the use of various online resources and discussions around lean thinking and leadership, the members of the cohort have the chance to 'till the soil' – preparing themselves to absorb the maximum from their on-site experiences. The collaborative learning journey starts months in advance and helps in cultivating a fertile ground for deeper insights and more poignant questions once the actual trip commences.
Post-Trip Reflections and Integration
Learning does not cease with the end of the trip. Post-trip reflections and discussions are invaluable for the integration of new knowledge into participants' professional lives. The fostering of a learning community where ideas and experiences can continue to be exchanged is essential to the transformational journey. It's this continued dialogue that deepens the understanding and facilitates the application of lean principles and leadership insights.
Online forums and WhatsApp groups ensure a continuous exchange of ideas, successes, and challenges faced while applying the gleaned knowledge. These platforms also serve to preserve the connections formed during the trip, leading to a personal, global lean network.
Beyond the Facade of Lean: Recognizing Cultural and Operational Diversity
Understanding the diversity within Japanese companies is vital to appreciating the application of lean principles. Not every Japanese company resembles Toyota, nor can the achievements of companies like Toyota be diminished to mere cultural advantages. Realizing this helps to debunk the myth that lean is easier to implement in Japan, inspiring participants to rise to the challenge within their own cultural contexts.
Participants encounter firsthand the fact that Japanese organizations harness certain cultural strengths, but they also wrestle with unique challenges. Much like anywhere else in the world, innovating within the bounds of an existing company culture requires dedicated effort and often the deliberate disruption of established norms.
Experiencing Practical Applications: From U-shaped Cells to Andon Systems
Observing tangible examples of lean practices provides profound learning experiences. U-shaped cells in manufacturing, for instance, exemplify efficiency in practice, marrying elegance with practicality in workflow design. Such sights prove to be fertile ground for learning about work design, continuous improvement, and management systems.
Discussions around traditionally Japanese concepts, such as ‘kata' or ‘andon', deepen the understanding of how companies like Toyota have had to culturally innovate, adapting traditional practices to create systems that encourage continuous improvement and problem-solving within their specific contexts. Witnessing how such practices are implemented in their place of origin offers profound insights that are difficult to replicate through mere theoretical study.
Continuing the Journey Beyond Japan
The journey of transformation that begins with a study trip to Japan is a launchpad for continuous personal and professional growth. The cohort, facilitation methods, repeated observations, pre-trip cohesion, and post-trip reflections collectively serve as a robust framework for transformative learning. When participants return to their work environments, they bring with them not just newfound knowledge, but also the inspiration and networks required to make a lasting impact in their organizations, fostering cultures of continuous improvement, innovation, and happiness.
Cultural Transformation: Beyond the Tools of Lean
The essence of lean management and continuous improvement extends far beyond the mere adoption of tools and methodologies. GE Aerospace's independence and GM Vernova's spinoff highlight the importance of cultural transformation in organizations. Larry Culp's insights from the AME conference underscore the necessity for leaders to actively cultivate an environment where employees feel safe to report issues and contribute to the problem-solving process, demonstrating the value of psychological safety.
Transforming a corporate culture is not just about instructing employees to follow certain practices like pulling the andon cord; it's also about leaders embodying that change and showing through their actions that speaking up is not only safe but valued. This approach to leadership extends beyond language barriers and geographical boundaries, providing a source of inspiration for participants on Japan study trips.
Leadership with “Kokoro Zashi” – A Japanese Approach
The intricacy of leadership within the context of continuous improvement is vividly embodied in the Japanese concept of “Kokoro Zashi”. This term, which translates to the strength of one's heart, suggests a leadership style heavily focused on the leaders' inner drive and passion for instigating positive change and inspiring their team. The character of Kokoro Zashi is a blend of the symbols for samurai and heart, signifying the courage to lead with one's spirit and the intention to effect meaningful direction with actions.
On Japan study trips, the influence of Kokoro Zashi and the idea of leadership fueled by genuine intention and motivation becomes palpable. Participants witness this zealous approach in the daily practices of Japanese leaders, distilling the profound connection between the emotional and practical facets of management. This holistic exposure acts as a catalyst for visitors, reinvigorating their passion for lean thinking and leadership upon return to their home countries.
The Details in Lean's Practicality
While the cultural and leadership aspects of lean are crucial, the tangible applications of lean tools and principles remain a fascinating element for study trip participants. Visual management tools, efficient layout concepts like 5S, and inventory control systems such as Kanban and SMED (Single-Minute Exchange of Die) are seen in action, providing clear examples of operational excellence.
Visitors are encouraged to engage with Japan's advanced lean practices not just through observation but by understanding the underlying philosophy. This exploration enables them to discern which aspects might readily apply within their organizations and which might require adaptation, respectfully recognizing the nuance and complexity involved in their implementation.
Navigating Japan as a Foreign Visitor
The journey into lean exploration in Japan is eased by the logistical support that comes with travel programs. Japan's orderliness and the increased accessibility of signs in Romanji since the pandemic make navigation and daily activities manageable for those unfamiliar with the language. Moreover, the high degree of safety and use of technology like Google Translate further enhance the accessibility for foreign visitors.
For newcomers to Japan, being part of a guided group can mitigate the challenges of language barriers and unfamiliarity. The provision of translators and the smooth functioning of Japan's infrastructure create a supportive environment for learning and exploration, allowing participants to immerse themselves with greater ease and focus on the rich experiences offered.
The Continuous Lean Learning Process
Reflecting on learning after a Japan study trip is essential, particularly examining how seed concepts like Kokoro Zashi and logistical ease influence the continuous improvement journey back home. Participants are reminded that the lessons from Japan are part of a sustained lean learning process. As they integrate newfound cultural insights, philosophical management principles, and practical aspects of lean into their operational environments, the spirit of continuous betterment remains the thread that connects their Japanese experiences with their future endeavors.
Unparalleled Access to Lean Masters
The immersive nature of Japan study trips offers more than just an academic understanding of lean management principles–it provides distinctive access to seasoned lean masters like Mr. Yoshino who deliver irreplaceable insights from a lifetime embracing the lean mindset. This rare opportunity enables participants to engage in personal dialogue and gain a deeper understanding of the leadership qualities and operational strategies necessary for successful lean transformation.
Joining Mr. Yoshino for meals and traveling together allows for informal yet impactful learning experiences, where anecdotes and real-world experiences are shared. This intimacy with a sense of mentorship offered by such masters is a fundamental element of the learning journey, enhancing the exchange of knowledge and reinforcing the practical application of learned principles.
Interactions that Cement Learning
The dynamic of small group discussions with industry veterans during study trips translates into an engaging and memorable way to absorb and retain information. These unscripted encounters allow for the kind of one-on-one interactions that can catalyze profound professional and personal growth. Each site visit and mealtime conversation is an opportunity to unpack layers of wisdom that go well beyond what can be gleaned from traditional academic settings or books.
Entering into these conversations, participants are urged to bring their queries and challenges, establishing a dialogue that is both relevant and custom-filled to their unique circumstances. Whether discussing transformational leadership or the particulars of lean tool implementation, this exchange is tailored to bridge the gap between learning and practical application.
The Ripple Effect of Chain Learning
The concept of chain learning encapsulates the notion that every participant in these Japan study trips not only gains from the experience but also contributes to a larger knowledge pool. It is a ripple effect where insights are not just absorbed but also shared, creating an ever-expanding community of lean thinkers. After returning home, participants are often inspired to share their experiences with colleagues and networks, furthering the growth of lean principles within their own cultural context.
The Chain of Learning community, represented by experts like Katie Anderson and platforms such as her podcast, connect like-minded individuals passionate about lean philosophy. As these clusters of knowledge-seekers grow and interact, the embodiment of lean thinking becomes ever more paramount in creating cultures of continuous improvement worldwide.
Leveraging Resources for Continuous Development
In an era of interconnectedness, utilizing various resources plays a crucial role in maintaining the momentum of lean learning. Katie Anderson's book “Leading to Learn” and her podcasts offer ongoing education and insights into top-tier lean leadership practices. These resources act as tools for those who have returned from their trips and for those awaiting the chance to embark on one.
By engaging with these learning mediums, individuals can stay linked to the evolving discourse of lean management, fostering their own development and preparedness for global lean community engagement. Tapping into such resources magnifies the value of direct experiences from study trips, promoting sustained growth in lean education and leadership abilities.
Please scroll down (or click) to post a comment. Connect with me on LinkedIn.
Let’s work together to build a culture of continuous improvement and psychological safety. If you're a leader looking to create lasting change—not just projects—I help organizations:
- Engage people at all levels in sustainable improvement
- Shift from fear of mistakes to learning from them
- Apply Lean thinking in practical, people-centered ways
Interested in coaching or a keynote talk? Let’s start a conversation.
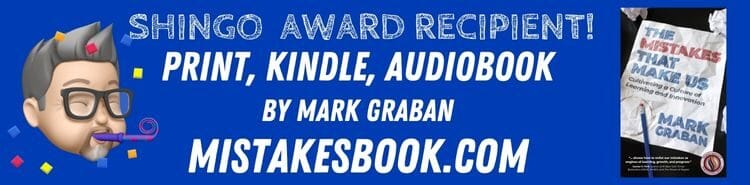
Katie’s November trip is sold out — but she’ll be doing more in 2025.
I’m also partnering with Mike Hoseus (formerly of Toyota) for his three-day Kentucky learning experience that includes a Toyota plant tour, great workshops, and more.
Learn more here and use code GRABAN for a special discount:
https://focusinleadership.com/events/