I wrote this piece for IndustryWeek… it starts:
“In January, passengers, crew and the public were stunned by the latest high-profile incident involving a #Boeing 737 MAX-9 jet. A door plug blew out during an Alaska Airlines at 16,000 feet. Thankfully (and perhaps luckily), nobody was killed in the incident.
In the aftermath, the general public might ask, “Who screwed up?” Better questions include, “What might be going wrong with Boeing's processes and operations?” We should also ask, “What's wrong with Boeing's culture and leadership?”
Are these new, isolated problems with new, local causes? It seems not.”

You can read the piece here or below in this post.
What do you think? What are the implications of the apparent lessons for your industry or setting?
Boeing Executives Failed to Lead, Waved Off Lean
Don't blame rank-and-file workers for systematic problems.
In January, passengers, crew and the public were stunned by the latest high-profile incident involving a Boeing 737 MAX-9 jet. A door plug blew out during an Alaska Airlines at 16,000 feet. Thankfully (and perhaps luckily), nobody was killed in the incident.
In the aftermath, the general public might ask, “Who screwed up?” Better questions include, “What might be going wrong with Boeing's processes and operations?” We should also ask, “What's wrong with Boeing's culture and leadership?”
Are these new, isolated problems with new, local causes? It seems not.
Immediately after the incident, inspections of the temporarily-grounded MAX-9s led to the discovery of loose bolts on multiple jets in the United Airlines fleet. The problem not being isolated to a single plane makes it even more clear it's a systemic problem — certainly not the fault of any individual mechanic or team.
It was first assumed that the Alaska Airlines plane also had loose bolts, but an initial NTSB report confirmed what had started as an internet rumor: The four bolts in question had not been re-installed. They were missing altogether, presumedly left on a workbench or ending up in the trash.
Why?
The door plug, originally assembled into the fuselage by supplier Spirit AeroSystems, was removed at a Boeing facility in Washington and had to be reinstalled.
Why?
Boeing and Spirit employees had to rework the fuselage due to riveting defects created during Spirit's manufacturing process in Kansas. Spirit should be asking why those defects occurred and how they can prevent them from happening again. But the responsibility for the incident doesn't end with Spirit.
Boeing CEO David Calhoun, who recently announced he is retiring by year's end, said publicly, “We caused the problem, and we understand that… Boeing is accountable for what happened.” It's a company problem, and Boeing is responsible for the work of their suppliers.
But how could mechanics forget to reattach the bolts after putting the door plug back in place? Instead of blaming and potentially punishing individuals or blaming “some idiot,” it's important to look at systemic causes and contributing factors for which Boeing should be accountable. Again, it's a company problem, not a worker problem.
The rework was being done outside of the normal process. Why? It was part of a widespread Boeing practice referred to as “traveled work,” which the company defines as tasks “delayed and/or completed in a factory location other than what was originally planned.”
This practice violates lean principles of:
- Building in quality at the source
- Not moving along defective parts or products to be fixed later down the line.
Traveled work is less likely to have formalized standardized work or the normal tools in place. Boeing says that documentation about the door-plug reinstallation is missing (or never existed). And reports say the security-camera recording from the area was overwritten and lost.
It's troubling that such important work was done out of process without documentation. But, in a way, that's good if the company doesn't know which individual (or individuals) to punish because the problem was caused by Boeing's policies and practices.
Boeing CFO Brian West said, “Starting on March 1 of this year, we will no longer travel work between Wichita and our fuselage supplier [Spirit AeroSystems] and Renton [Boeing assembly plant] … It had been going on too long. So now we will only accept a fully conforming fuselage from Spirit, which means in the near term, there might be variability of supply.”
The lean experts who taught Boeing about the Toyota Production System certainly instructed the company to put quality first, even if that means stopping the line to address defects instead of passing them on. Decades later, did Boeing forget that lesson, or did they refuse to ever implement it?
CEO Calhoun admitted that the amount of rework taking place in Boeing's so-called “shadow factory” exceeded the initial labor hours, stating, “In our shadow factories, we put more hours into those airplanes than we do to produce it in the first place…that's a metric I know everybody understands.” That metric is understandable, but it's completely flabbergasting to hear about any factory spending more time on rework than production.
So why didn't Calhoun and other leaders do anything about it?
West's “variability of supply” comment suggests that putting quality first could lead to production slowdowns and late deliveries. In a lean culture, short-term production delays should trigger root-cause problem-solving and countermeasures that drive long-term improvement. Passing defective work along is a workaround–and it's extremely counterproductive over time.
Reducing that variability of supply–and the resulting variation in aircraft assembly–must extend beyond Boeing rejecting a delivered fuselage that's not fully conforming to specifications. The company must work with suppliers to help them implement lean methods and mindsets that prevent mistakes and build in quality at the supplier sites (or sub-supplier sites). Part of the formula for Toyota's success is its collaborative relationships with suppliers. One can't just demand better quality; instead, one must work together starting during the product design and supplier selection stages of an airplane's lifecycle.
Lean organizations not only talk about putting safety and quality first; they walk the talk in the boardroom and the factory floor. Point #1 of “The Toyota Way” says the company makes decisions based on long-term, even at the expense of the short-term. That's another lesson that Boeing forgot or never embraced.
For years, Boeing employees and whistleblowers have complained about a culture where “schedule is king.” In other words, employees and frontline leaders are pressured to keep the line moving–to emphasize and prioritize quantity over quality.
CFO West also admitted, “For years, we prioritized the movement of the airplane through the factory over getting it done right, and that's got to change.”
If executives were unaware of these practices, which emphasized production quantity and throughput over safety and quality, they should be (and are) held accountable. If leaders directly pushed (or tolerated) those priorities, that's a fireable offense.
CEO Calhoun acknowledges the company “must inculcate a total commitment to safety and quality at every level of our company.” If he hasn't been doing that for the last four years, Calhoun needs to go–NOW, not at the end of 2024 as announced–if Boeing's culture is going to change.
There are too many instances of “too little, too late” admissions from Boeing leaders. In the immediate aftermath of the incident, Boeing announced “quality standdown days,” to “allow all teammates who touch the airplane to ‘pause, evaluate what we're doing, how we're doing it and make recommendations for improvement,'” said Stan Deal, president and CEO of Boeing Commercial Aviation — now forced into immediate retirement.
Why limit such reflections to frontline employees? Did the Boeing board and senior executives take a day to pause and reflect on their role in safety and quality? During the standdown day, “10,000 participating employees were encouraged to speak up about any concerns they have and offer suggestions about ways to improve the facility's processes.”
That seems like a tacit admission that Boeing had also not learned (or refused to adopt) basic lean principles and practices about engaging everybody in ongoing continuous improvement. How many of these ideas will be implemented?
Changing a broken company culture requires an influx of new leaders from the outside. To prevent future door plug blowouts, and similar manufacturing problems, Boeing executives must embrace, encourage, and reward the following behaviors:
- Every leader prioritizing safety, quality, delivery, and cost — in that order, every day
- Stopping production to fix quality problems, using rigorous problem-solving methods, instead of passing them on to another facility or a rework area
- Engaging every team member in improvement every day soliciting ideas and acting on them continuously, instead of waiting for a kaizen event or another “stand down”
It's time for Boeing to learn and embrace the lean lessons of Toyota and other world-class manufacturers.
Please scroll down (or click) to post a comment. Connect with me on LinkedIn.
Let’s work together to build a culture of continuous improvement and psychological safety. If you're a leader looking to create lasting change—not just projects—I help organizations:
- Engage people at all levels in sustainable improvement
- Shift from fear of mistakes to learning from them
- Apply Lean thinking in practical, people-centered ways
Interested in coaching or a keynote talk? Let’s start a conversation.
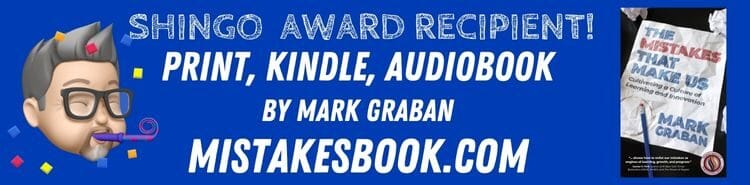
[…] Artículo anteriorMiartículo para IndustryWeek: Boeing Executives Failed to Lead, Waved Off Lean […]