I'm currently working on a Mistake Proofing class for Karen Martin and TKMG Academy. Coming soon!! UPDATE — AVAILABLE NOW.
In the process of writing the course and its script, I've gone back to some older source material that has been on my bookshelf for a long time. In this case, it's a book I've owned, reading it many years ago (20 years ago?): Zero Quality Control by Shigeo Shingo.
It was published by Norman Bodek during the heyday of Productivity Press when he still owned it.
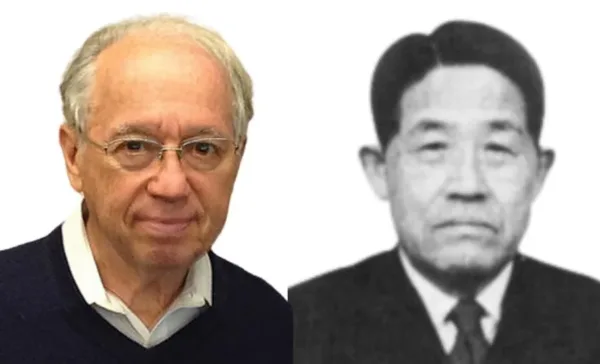
Norman Bodek's Words
In the publisher's foreword, Norman wrote, in part:
“One of the great things about ZQC is that it focuses on correcting the conditions for processing, not on blaming people for making mistakes. Shigeo Shingo, the developer of ZQC, recognized that it is human nature to make mistakes or forget things. People should not be punished for mistakes. Punishment only makes people feel bad –it doesn't eliminate defects.”
My thoughts: There's so much wisdom in just one paragraph:
- Focus on the process instead of blaming people
- It's very human of us to make mistakes and forget things (we are fallible)
- Don't punish people for mistakes
- Punishment only makes people feel bad
As I've learned, people already feel bad about their mistakes. Getting upset and yelling doesn't help. The punitive approach is counterproductive because it teaches people to hide and cover up mistakes when they can get away with it. And if that's happening, we're doomed to repeat those mistakes as an organization. And we can't improve or prevent mistakes if they (or their causes) are hidden.
Hear Mark read this post — subscribe to Lean Blog Audio
Shigeo Shingo's Words
On page 45, Shingo writes about an operation that was mistake-proofed so that the product no longer missing any springs, which had led to customer complaints.
“Whenever I hear supervisors warning workers to pay more attention or to be sure not to forget anything, I cannot help thinking that the workers are being asked to carry out operations as if they possessed divine infallibility.”
We're all fallible. Telling people to “be more careful” through the spoke word or signs and posters just isn't effective (as I've documented on this mini site).
Instead, we need mistake-proofing. As Shingo writes:
“Rather than that [being careful] approach, we should recognize that people are, after all, only human and as such, they will, on rare occasions, inadvertently forget things. It is more effective to incorporate a checklist — i.e., a poka-yoke — into the operation so that if a worker forgets something, the device will signal that fact, thereby preventing defects from occurring. This, I think, is the quickest road leading to attainment of zero defects.”
This was many decades before the excellent book The Checklist Manifesto was a huge hit for Dr. Atul Gawande.
At the bottom of this post, you can find two episodes of the “My Favorite Mistake” podcast that illustrate the point vividly about Toyota not blaming individuals for mistakes.
The Baka Yoke / Poka Yoke Story
Over time, I've heard many versions of the story about why Toyota shifted away from “baka yoke” (in Japanese), which means “foolproof,” to “poka yoke,” which means “mistake-proof” or “error-proof.”
In the book, I found what might be the definitive version of that story. I could never remember if this was attributed to Ohno or Shingo. Maybe Ohno's books had his own version of this tale. But Shingo wrote:
“This poka-yoke concept is actually based on the same idea as “foolproofing,” an approach devised mainly for preserving the safety of operations. In the early days, I used the term “foolproofing” (in Japanese, bakayoke), but around 1963, when Arakawa Auto Body adopted a “foolproofing” device to prevent seat parts from being spot-welded backwards, one of the company's part-time employees burst into tears when her department head explained that a “fool-proofing” mechanism had been installed because workers sometimes mixed up left- and right-hand parts.
“Have I really been such a fool?” she sobbed.
She ended up staying home the following day and the department head went to see her there.
He tried all sorts of explanations. “It's not that you're a fool” he told her. “We put the device in because anybody can make inadvertent mistakes.” Finally, he managed to persuade her.
When the department head told me this story, it was clear to me that “foolproofing” was a poorly chosen term. But what name would be suitable? After some thought, I gave the name poka-yoke (mistake-proofing) to these devices because they serve to prevent (or “proof;” in Japanese, yoke) the sort of inadvertent mistakes (poka in Japanese) that anyone can make.“
It's nice that Shingo would admit his mistake in using the foolproofing term. Instead of telling people things like, “Don't be so sensitive!” it's better to adjust the language so that it's:
- More accurate (you're not fools)
- Less upsetting
Do you hear this language at work? Terms like:
- Foolproofing
- Dummy-proofing
- Idiot-proofing
If so, can we admit that mistake and adjust accordingly, as Shingo did?
Episodes About Toyota and Mistakes:
What do you think? Please scroll down (or click) to post a comment. Or please share the post with your thoughts on LinkedIn – and follow me or connect with me there.
Did you like this post? Make sure you don't miss a post or podcast — Subscribe to get notified about posts via email daily or weekly.
Check out my latest book, The Mistakes That Make Us: Cultivating a Culture of Learning and Innovation: