As I recently shared on LinkedIn, I really appreciated the annual shareholder letter that was published and shared by Larry Culp, who has been CEO of General Electric for just over five years now (the first-ever outsider CEO in their 125+ year history).
Read the full letter here. I've also archived it here as a PDF.
First off, I can't help but notice that the photo shared at the end of the letter is not a corporate headshot of Larry in a power suit and tie. It's a photo from a “gemba” (or factory floor) with him wearing safety glasses, a casual shirt, and a high-visibility vest.
He certainly looks to be in his element and enjoying it. How rare is that amongst CEOs of manufacturing companies of any size? How much better off would other manufacturers (or healthcare organizations) be if they had CEOs who don't just sponsor or support Lean, but are instead leading and driving the culture change? How many hospital CEOs truly enjoy donning PPE to be at the frontlines of patient care?
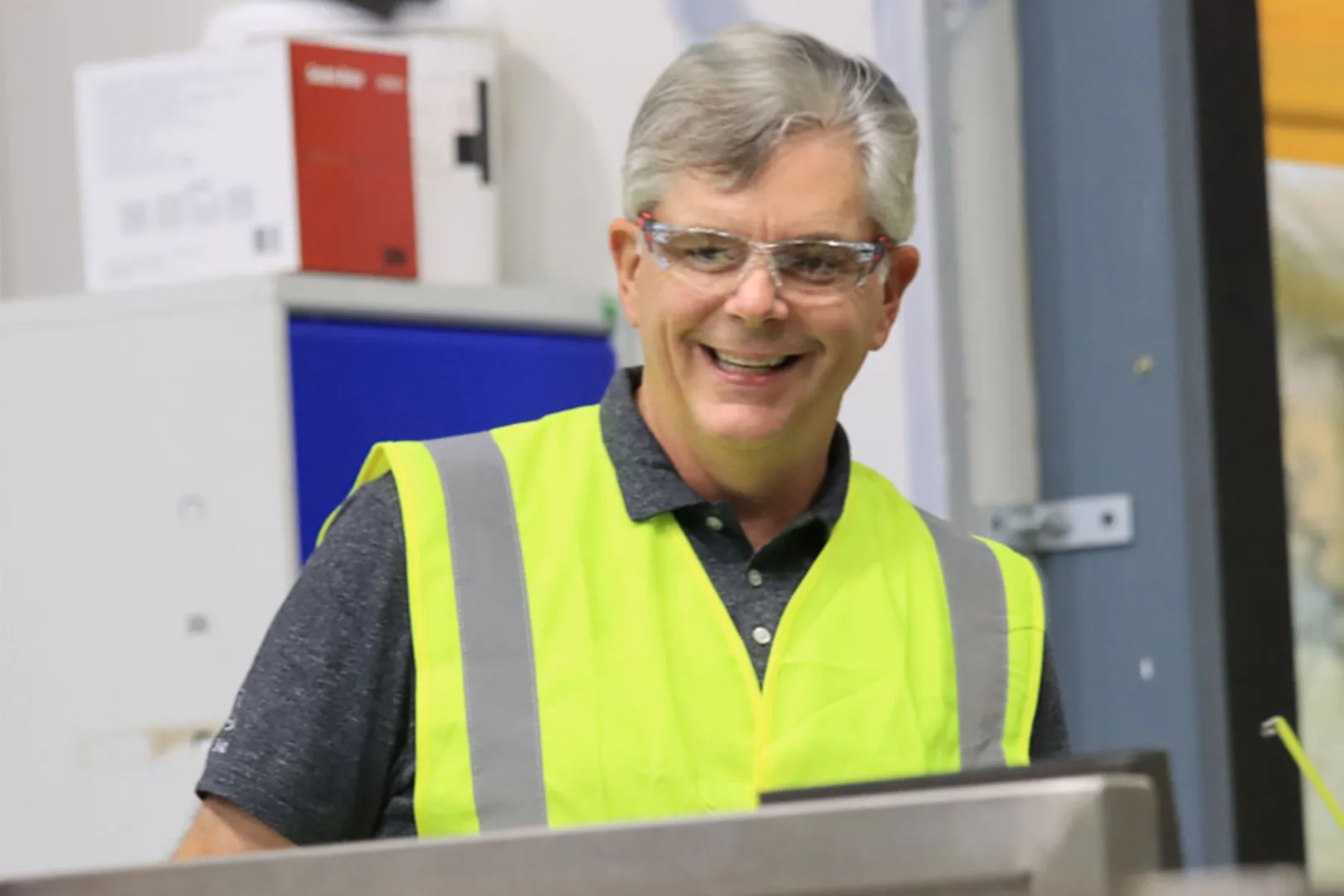
Hear Mark read this post — subscribe to Lean Blog Audio
In part of the letter, Larry wrote:
Today, in an ever-challenging environment, GE employees are embracing a lean philosophy rooted in kaizen, “change to make it better.” They are delivering for our customers by listening, learning, and executing. Step-by-step, one process at a time, they are advancing safety, quality, delivery, and cost, in that order, serving our customers and each other with deep respect.”
Larry participates in kaizen events (as described in this recent FORTUNE article), which sets a great example for other leaders. But that doesn't mean he's the one with all of the answers. GE is also working beyond events, to engage people in Lean and continuous improvement through a daily management system and a culture of continuous improvement.
“We're laying in our lean operating model for GE Aerospace, which we'll call FLIGHT DECK, so that we can perform at much higher levels in ways that I think will serve us well going forward.”
The mantra of “safety, quality, delivery, and cost, IN THAT ORDER” is one I've heard for almost 30 years, going back to my days at General Motors. Read more about that here:
Those words can't just be lip service. Leaders must be willing to let everybody take actions that put safety and quality first, even at the short-term expense of slower production. But safety, quality, and production quantities can go hand in hand, with good processes and continuous improvement mindsets. Quality and quantity are not really a tradeoff… in the old thinking yes, but with Lean thinking — no.
Boeing has been struggling with this greatly in recent years, with all of the complaints about management pushing speed and schedule over safety and quality.
In the letter, Larry shares the results from one kaizen event:
“Enter lean. The GE T408 engine, for example, powers the fast-growing CH-53K King Stallion, and volume on the engine is growing 300 percent year-over-year. With such an intense ramp, any delay or bottleneck matters a lot. That's why last November, business leader Alex Stone, lean leader Camille Latour, and advanced engine mechanics Frank Stewart and Vinnie Falls led a cross-functional team through a kaizen event at our Lynn, Massachusetts, plant.
Coming into the event, our build time on the T408 was around 75 hours with two mechanics working simultaneously on two separate engines to meet demand. Our goal: Take that 75 hours down to under 32, with one mechanic working at a time.
By the end of the week, engineers and operators working together on the floor identified opportunities both big and small; saving hours of prep time by using a heat gun instead of an oven to treat a compressor rotor, for example. The result was reducing build time to just 11 hours with one operator, all the while enhancing safety and quality.
75 to 11 is the kind of change that takes your breath away. But to me, the best part was the fact that on Thursday of that week, the team was already talking about how they were going to do better than 11; what they could do next.
That is the spirit of lean and kaizen. Always getting better. Your mindset shifts to look for opportunities at the most granular levels, day in and day out, to enhance performance and eliminate waste.”
That's not uncommon with Lean thinking and the action of kaizen events. They set an aggressive goal of more than 50% improvement, only to see something more like a 85% reduction. Very impressive! And the kaizen mindset of “what they could do next” is impressive and it's a great sign of employee engagement.
It's great to see the example that GE is setting for other organizations that are willing to learn and follow. I hope Boeing starts learning from the “new GE” instead of doubling down on the “old GE” approach of Jack Welch and his acolytes.
Again, the letter is linked here.
What do you think? Please scroll down (or click) to post a comment. Or please share the post with your thoughts on LinkedIn – and follow me or connect with me there.
Did you like this post? Make sure you don't miss a post or podcast — Subscribe to get notified about posts via email daily or weekly.
Check out my latest book, The Mistakes That Make Us: Cultivating a Culture of Learning and Innovation:
The leadership in action displayed by Larry Culp should be something other leader strive to achieve. It is very impressive to see an 85% reduction in assembly time over the course of just a few days!
Thanks for reading, Alex. Those results are indeed impressive!