Update: I've written a longer piece about inspection that's now at the bottom of this post.
I'm frustrated that the official Boeing response to their high-profile quality problems (and safety risks) is more… INSPECTIONS!
Boeing will inspect Boeing's work more.
Boeing will inspect Sprit AeroSystems' work more.
Airlines will be invited to come inspect the work.
The F.A.A. will come to audit the work.
I'm picturing a variation of the famous Oprah moment that turned into a meme… “You get an inspection! You get an inspection! Everybody gets an inspection!!!”
But you can't inspect your way to quality.
I hope that Boeing is also using Lean methods and mindsets, including mistake-proofing to truly build-in quality.
There's nobody better to learn mistake-proofing from than today's webinar presenter, John Grout.
Join us at 1 pm ET today or register to have us send you the recording.
Here was the preview that John and I recorded:
Boeing Cannot Inspect Their Way to Quality; Nobody Can
Following the January 5th incident where a door plug suddenly blew out of the side of a Boeing 737 MAX-9 jet operated by Alaska Airlines, one word has dominated the news about what Boeing and their suppliers are doing next: inspection.
The enormous success of Toyota's vaunted production system, known widely as “Lean Manufacturing,” prompted virtually every aspiring world-class manufacturer to adopt the essential principle of “building it” quality rather than “inspecting in” quality by finding defects after they're made.
Boeing has claimed to be implementing Lean methods since 1996, what they call the “Boeing Production System.” A 2003 article on Boeing's website says, “Mistake-proofing and built-in quality are throughout the entire factory and part of every process.”
Mistake-proofing is a core Toyota strategy dating back almost a century, using electro-mechanical devices to prevent mistakes or immediately find defects using automated methods. The key is being willing to stop the line to fix quality problems in ways that prevent them from happening again. Prioritizing quality over production numbers in the short team leads to better quality and schedule attainment over time. Boeing seems to still be learning this lesson.
In a memo dated January 15th, Boeing Commercial Airplanes President and CEO Stan Deal announced “immediate actions to strengthen quality” but only promised more inspections–a dubious strategy. Boeing will conduct more inspections at Spirit AeroSystems, the supplier that builds the fuselage and initially installs the door plugs. Spirit will most certainly also increase their own inspections. The airlines will be invited to inspect Boeing's work. The FAA will be on-site to audit all of this work, on top of a review of Boeing's practices by an outside company.
Deal said Boeing will add “additional” inspections. And this is on top of previously increasing the number of quality inspector positions by 20% since 2019. With all of its history building planes, one would think that Boeing would already know how many inspectors and inspections would be necessary. Adding more inspectors is a tacit admission that they weren't doing enough of this previously.
Boeing is adding inspectors but previously slashed staffing in this function. Senator Maria Cantwell (D-WA) recently criticized Boeing, and the FAA's oversight, for a “Verification Optimization” program that cut 900 quality inspector positions a few years back. So the same company that said it was OK to cut inspector positions now says adding more inspectors is the solution? Will these companies ensure that every supervisor (and that every leader up through the CEO) rewards people for speaking up about quality instead of punishing them?
Boeing Supplier Ignored Warnings Of “Excessive Amount Of Defects,” Former Employees Allege
When a company hasn't figured out how to completely mistake-proof the work, inspections might the best alternative for trying to protect the customer from receiving defective products. Visit any Toyota assembly plant around the world, and you'll see a long final inspection bay that every car travels through before being shipped. A factory must combine vast mistake-proofing efforts and some level of inspection, at least until the mistake-proofing is so effective that it's impossible for an imperfect product to be built in the first place. Then, inspections can be reduced or eliminated without the customer being put at risk.
However, 100% inspection is never 100% reliable, especially when it's done by humans. Different forms of human frailty creep in, as inspectors get fatigued and they miss problems. Or mismanagement takes over when inspectors are pressured to be good team players and to let quality slide to keep production moving.
The best companies work diligently to prevent mistakes or detect them in real time. These companies also have a culture of “psychological safety,” where every employee feels safe to point out problems and admit mistakes when they do occur. Admitting mistakes leads to effective problem-solving, which prevents the recurrence of mistakes by focusing on work processes and systems instead of blaming individual workers.
Has Boeing forgotten the core lessons about how to build in quality that they stated 20 years ago, as the result of employee turnover and multiple CEO changes? Or do they limit their promises to “more inspections” because of optics and the public's willingness to accept that as a solution?
While these inspectors are potentially tripping over each other to inspect these bolts (and other critical safety and quality items on the plane), I hope that mechanics, engineers, and Lean Manufacturing facilitators are working doubly hard to install better mistake-proofing methods. That's the best way to ensure safety, and that's a method I'd trust my life to when flying — not more inspections.
Please scroll down (or click) to post a comment. Connect with me on LinkedIn.
Let’s work together to build a culture of continuous improvement and psychological safety. If you're a leader looking to create lasting change—not just projects—I help organizations:
- Engage people at all levels in sustainable improvement
- Shift from fear of mistakes to learning from them
- Apply Lean thinking in practical, people-centered ways
Interested in coaching or a keynote talk? Let’s start a conversation.
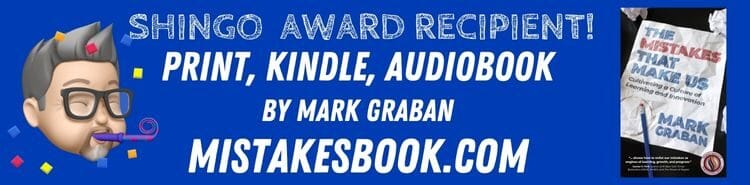
You are exactly right! As I learned during my time at Toyota, quality cannot be ‘inspected in’, it has to be BUILT in, using processes that deliver consistent results every time, regardless of who is executing it. There does not seem to be much of a Lean or quality mindset at Boeing currently as I have yet to hear mention of ‘mistake-proofing’, a Lean concept fundamental to flawless quality output for critical processes.
Thanks for your comment, Andre. I hope Boeing might be willing to learn from Toyota and I wonder if TSSC would provide some direct support to Boeing, as a member of the American manufacturing commmunity.
The best way to ensure quality and safe products? Hire inspectors! Said nobody ever, except Boeing, who is essentially dodging Lean concepts of mistake-proofing before the product in use, and trying to fix these issues after. It’s rather surprising and unsettling that even Boeing, one of the largest manufacturers of aircrafts in the world is more focused on inspecting their quality than having engineers build it in from the start.
Thanks for commenting, Jacob.
I hope the employee ideas that are being solicited include things like mistake proofing and other cultural changes that reduce the pressure to prioritize schedule attainment over safety and quality.
Now that the preliminary NTSB report says that the four bolts were indeed MISSING (not just loose), the one news reporter said something like, “It’s not clear WHO is responsible for that.”
I hope the news media, the public, and Boeing leaders don’t fall into the “blame game” trap.
In a complex manufacturing environment like Boeing’s, it’s impossible to say a single person at fault. This was a systemic failure. If you had to say ONE person was responsible, it’s the CEO, Dave Calhoun.