I'm glad that I have become friends with David Meier over the past… almost 20 years, I think. He's been a podcast guest many times (on my Lean Interviews podcast, Lean Whiskey, and My Favorite Mistake).
His story and lessons learned are also featured prominently in my upcoming book The Mistakes That Make Us: Cultivating a Culture of Learning and Innovation.
Sign up to get updates about the book's release.
David's career has had three major phases:
- Toyota in Georgetown, Kentucky (TMMK) — but that wasn't his first job
- Lean / TPS consulting around the world
- Starting and operating Glenns Creek Distillery — a place I've been able to visit four or five times
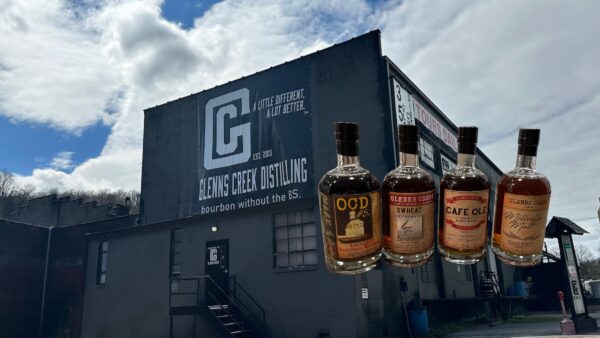
With my wife's latest career move last year, we now live about 90 minutes away from the distillery! Since Dave's now-award-winning spirits aren't widely distributed, the easiest way to buy is to visit him in person.
A few weeks back, we drove down to say hi and pick up a few bottles that I had purchased through his website, and he gifted us a bottle of “Cafe Olé” that we had helped put into a barrel, back in 2018.
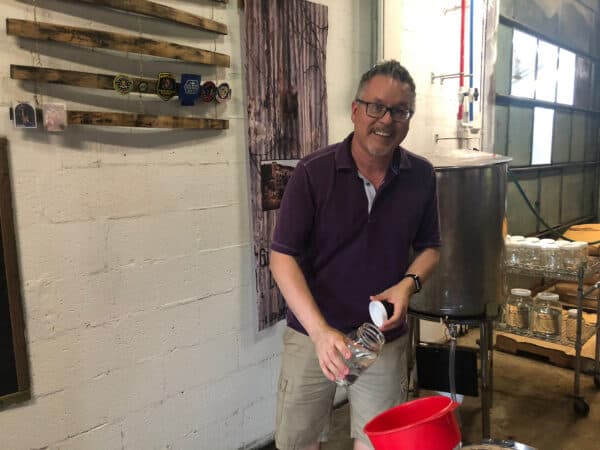
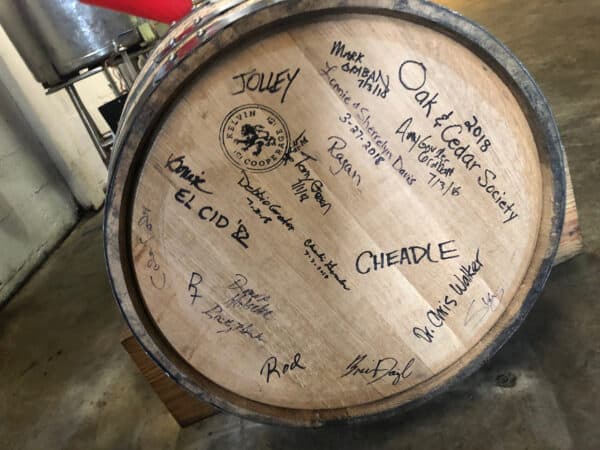
As we drove home, two of the bottles were together in a paper bag.
As we drove, the bottles clinked together quite often. It's not like this is a major life problem, but it was noticeable.
Knowing Dave — what he learned at Toyota and what he practices at the distillery — I knew it was safe and worthwhile to mention this to him.
I sent a note politely explaining the experience and, without knowing the exact countermeasure that would be best, suggested that it was a “kaizen” (continuous improvement) opportunity.
Of course, Dave responded positively and thanked me for bringing this up.
He followed up a few days later:
“I was able to improve the clanking bottles and also use recycled material to do it! I cut up some of the dividers from old boxes to put between bottles.”
Thanks for the idea!
Too many people get defensive or dismissive about ideas. They might get upset at you for pointing out a problem. They reflexively might say, “That's not a problem” or “It's no big deal.” How often do we hear these things at work? We wouldn't hear those things at Glenns Creek (unless a suspected problem truly was NOT a problem).
I'm also not surprised that Dave, as a former Toyota person and a bootstrapped entrepreneur, would take the path of “creativity over capital.” Instead of going and buying mesh bottle sleeves (at about 25 cents each), he used material that he already had and might have otherwise been trashed or recycled. I love it!
In an email exchange after sharing the draft of the post, Dave said:
“Also a side note – I find it interesting that I NEVER even considered mesh sleeves. Maybe I am just conditioned by my time at Toyota to make improvements with what is available. We were getting ready to throw out the boxes and I noticed the dividers if cut would fit in the bag and do the trick so that was the ‘answer.' I tell customers what the cardboard is for and they think it is a great idea.”
I'm not surprised! And I admire / appreciate his approach.
He also shared a few photos:
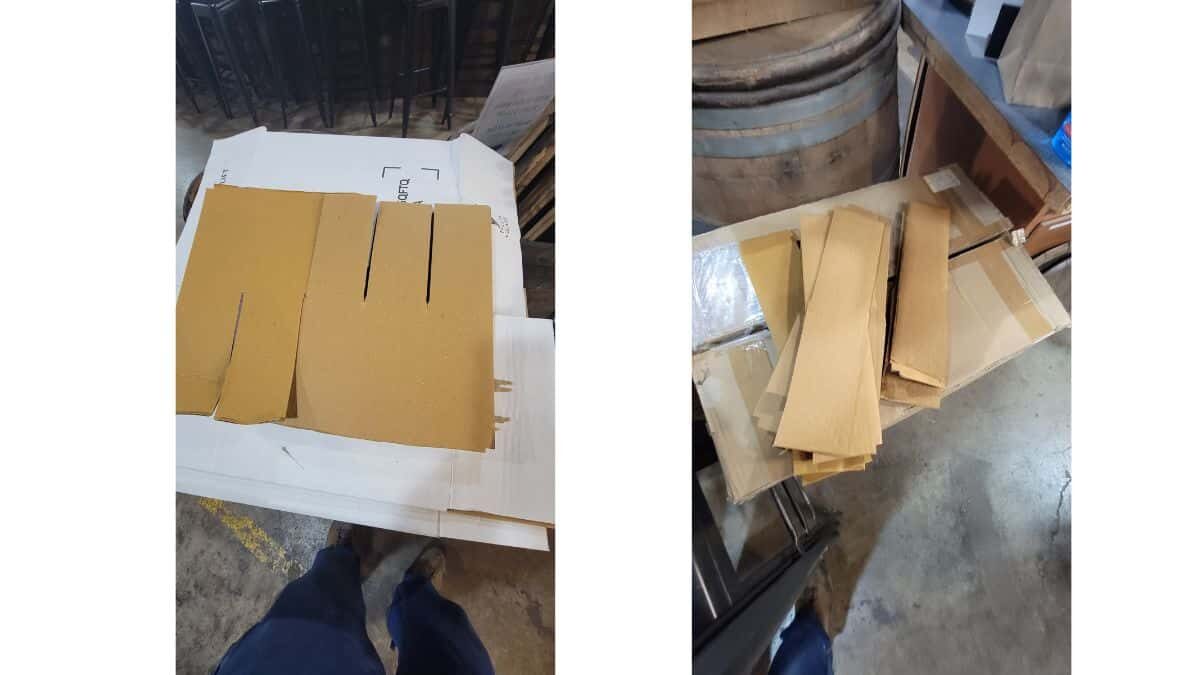
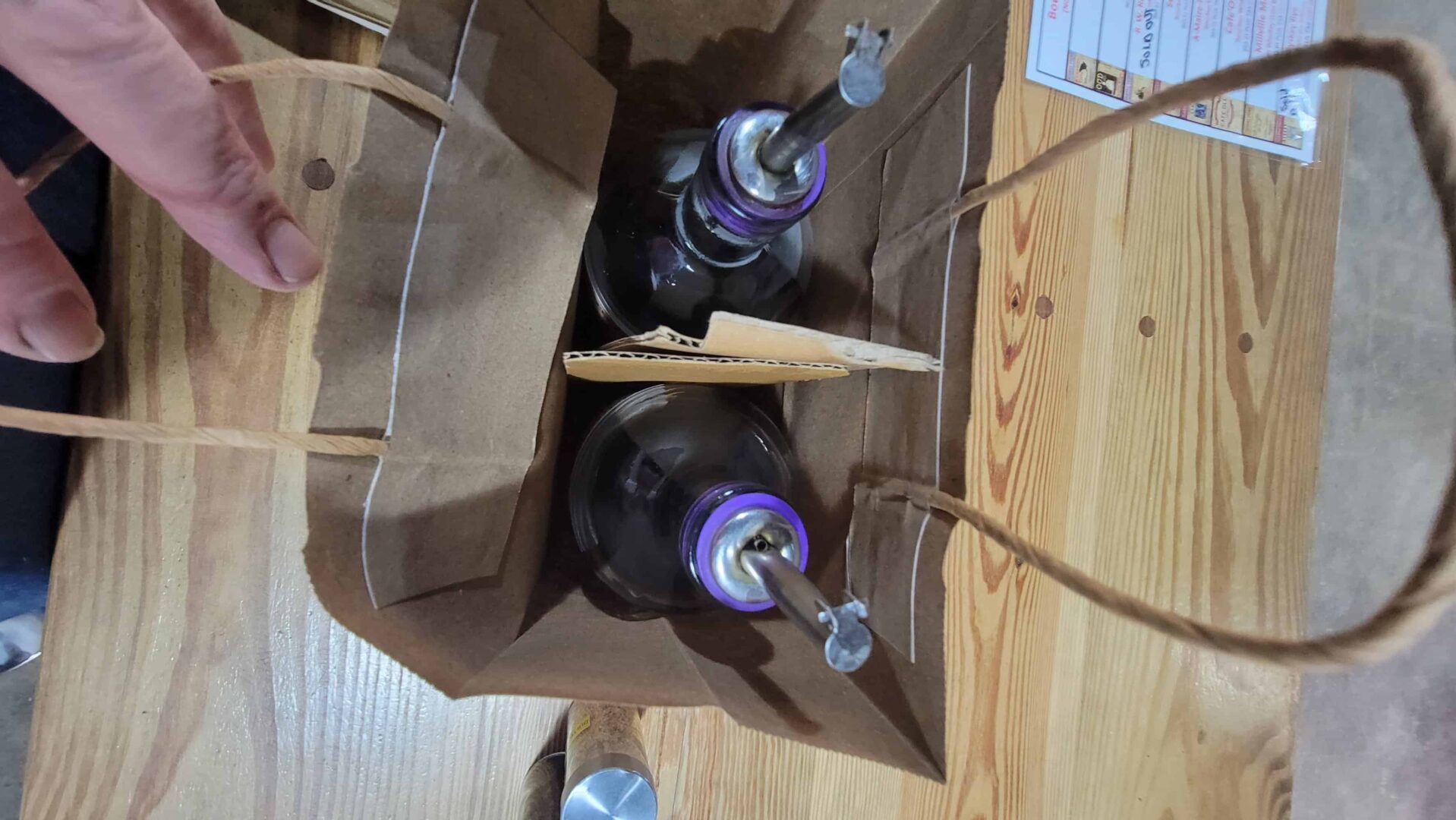
There's an inexpensive and effective countermeasure. We might even say that the problem is “solved.”
Plan, Do, Study, Adjust.
As Dave said to me during a recent visit, “It's all about solving problems.”
He isn't implementing Lean / TPS tools because he “should.” If you visit, you won't see visible 5S markings and visual controls. But he certainly has standardized work and he's practicing problem solving — focusing on the problems that matter most to his business.
Or in the case of my clinking bottles… working on problems that have simple, inexpensive countermeasures that don't take much time or money to test and implement.
There's a time and a place for us to strategically prioritize big improvement initiatives. But we can also “fix what bugs us” with small everyday Kaizen improvements. I love the example that Dave sets. Cheers!
What do you think? Please scroll down (or click) to post a comment. Or please share the post with your thoughts on LinkedIn – and follow me or connect with me there.
Did you like this post? Make sure you don't miss a post or podcast — Subscribe to get notified about posts via email daily or weekly.
Check out my latest book, The Mistakes That Make Us: Cultivating a Culture of Learning and Innovation: