There's a new “AI copy writing tool” that I read about called copy.ai. I decided to play around with a free trial and, of course, I tested it by asking the service to write a blog post about Lean in healthcare.
I gave it some keywords, including:
- Toyota
- Lean
- Leadership
- Culture
- Management
- Continuous improvement
It's surprisingly not terrible. The text is below and I'll interject as a human with text that's in italics and labeled “Mark:”.
October 2024 update: Scroll down to see what ChatGPT wrote more recently…
Introduction
Lean healthcare is a term that's thrown around a lot, but what does it actually mean? And most importantly: how do we improve our healthcare system using this new-age management strategy? In this article, I'll break down the basics of lean and explain why we need to implement it in our hospitals.
Mark: I don't know if I'd go with “new-age” — a modern management strategy maybe?
What is lean healthcare improvement?
Lean healthcare improvement is a continuous improvement process that uses the tools of the lean methodologies to solve problems. In healthcare, we use these tools to improve processes, eliminate waste and unnecessary steps in care delivery and improve patient outcomes.
The tools of lean include:
- Problem solving (kaizen)
- Visual management – using visual cues to identify areas for improvement
- 5S – organization based on efficiency and cleanliness (5S stands for sort, straighten or organize, shine or clean up, standardize so that all tools/equipment are in their place at all times; repeat this every day)
- Continuous flow – moving patients through in an orderly fashion with no bottlenecks or delays
Mark: It's interesting that the AI would focus on “tools.” Lean is more than tools of course… it's primary about the philosophy, as Toyota people say. And the Japanese word “kaizen” really means more like “continuous improvement.”
Lean is an approach. Lean came from Toyota.
Lean manufacturing was invented by Toyota in the 1950s, and it's all about eliminating waste.
Mark: It's not really “all” about eliminating waste… Toyota might say it's about continuous improvement and respect for people. Eliminating waste by respecting people and engaging them in continuous improvement… maybe the AI wasn't far off. But there's indeed more to say.
That's pretty much the only thing that you need to know about lean as a concept. But just in case you're interested in learning more:
Lean is an approach that focuses on solving problems by eliminating waste (or “muda,” as it's called in Japanese). Lean principles are derived from Toyota's manufacturing system, which has been used for decades to make millions of cars every year with very high quality standards and low costs. The goal of lean is not just to reduce costs but also improve customer value by delivering products faster than competitors can do so.
Mark: I do appreciate that the AI focused on quality and flow (lead time), not just cost. Good bot.
Lean is a journey, not a destination
Lean is a journey, not a destination.
A journey of continuous improvement. A journey of problem solving. A journey of leadership.
The lean methodology is about the long term.
The lean methodology is not just a one-time event, it's a continuous process. This can be hard to grasp when you're new to the concept of lean because of all the buzzwords surrounding it–streamline, eliminate waste and optimize are all common phrases in any lean project plan. But these terms have specific definitions when it comes to actual implementation:
Lean isn't just about cost reduction. It's also about improving the customer experience and employee experience by making sure everyone understands how their job contributes to overall goals. It takes time for people on a team or departmental level to learn how each person's role fits into the bigger picture–and that learning curve has nothing to do with being “slow” or “inefficient.”
Mark: Whoa, and not the AI is emphasizing that it's not just cost — but also about the customers and employees having better experiences.
The lean methodology is all about continuous improvement.
The key to lean is continuous improvement. That's right, I said continuous improvement. And that's exactly what it means: improving things every day, making small improvements every day, and having a problem-solving culture. It takes the concept of kaizen–a Japanese word meaning “change for better” or “improvement”–and applies it to every aspect of your organization so that you're always working toward better outcomes for patients and employees alike. In this way, lean healthcare is not just about making one big improvement (like installing brand new equipment), but rather creating a culture where everyone in the organization looks at problems they see on a daily basis as opportunities for improvement.
How to do Lean
Mark: We might want to “be Lean” or “act Lean” more so than “do Lean.”
We know you're busy, and we don't want to waste your time. So let's get right to it:
Identify a problem that needs solving. This is the only way to start a Lean journey.
- Take action! After all, if nothing changes, nothing changes. Don't wait for someone else to do something about it–that's not Lean thinking at work. If there are people in your organization who are working on improving efficiency, ask them for advice or help with identifying areas where improvement could be made; if nobody has any ideas yet (or if nobody wants anything changed), then go ahead and make one yourself!
- Learn from the results of this change–this could mean looking into how much time was saved thanks to making improvements (if any), or whether employees were satisfied with their jobs after receiving training on new processes they'd use every day at work (another example).
This step is especially important because it allows us all learn from mistakes before moving forward again with another solution – so make sure that everyone involved knows how much money/time/effort went into making these adjustments before deciding whether or not they should continue down this path toward increased efficiency within their organization.”
Mark: The AI is repeating the classic Taiichi Ohno advice of “start from need.” As John Shook asks, “What problem are you trying to solve?” And I love how the AI emphasizes the importance of learning from mistakes. Has it been listening to my podcast??
Implementing lean requires leadership at every level.
Now, you may be thinking, “But I'm a manager! I don't have time to lead!”
Don't worry: leadership and management are not the same thing. Leadership is about setting an example; it's about creating a vision and inspiring people to follow it. Management is more tactical in nature–it involves making sure things happen in the right order, at the right time, using the right resources.
Management is also different from supervision, which involves supervising others' work–and sometimes overseeing their performance evaluations as well.
Mark: Is the AI just padding for word count? Is this leadership vs. management detour helpful?
The organization must have a problem-solving culture.
Problem-solving culture is a key part of lean. Lean healthcare improvement isn't just about identifying problems and solving them; it's about continuous improvement, learning from mistakes, and transforming your organization into one that is able to adapt quickly to changing conditions (such as those brought on by new technology).
One way this can be achieved is through a problem-solving culture. You may have heard of “OKR” or “Objectives & Key Results.” This approach focuses on setting clear goals for your team and then measuring progress towards those goals in order to measure performance and identify areas where improvements need be made. The problem with this method is that it doesn't encourage any sort of reflection or introspection at all–you're just checking off items on your list as they get done. By contrast, the concept behind problem-solving cultures encourages employees within an organization to reflect deeply on their challenges; once they've reflected deeply enough, they come up with solutions that are tailored specifically for their environment (and not necessarily applicable everywhere else).
Mark: OK, the AI got off track with a discussion of OKRs… it would be more on-track to reference Strategy Deployment (a.k.a. “Hoshin Kanri”) as the method for creating alignment across the organization for goals and breakthrough improvements.
Implementing lean requires cross-functional teams.
In order to truly implement lean, you need cross-functional teams. Not just functional teams, or organizational teams–but cross-organizational and cross-cultural ones.
Just like how the Japanese use kanban cards to signal a need for something from another department, your healthcare organization needs measurable ways of letting people know that they should be working together to improve processes. On the other hand, having separate departments that don't communicate with each other can lead to inefficiencies and poor quality care.
Mark: The AI is running out of steam? That's an odd connection to kanban signals. Cross-functional teams are important and we might more likely use Value Stream Mapping or Process Mapping as a way to better understand the cross-functional and cross-departmental flows of work.
When we say “cross-functional” here at Healthy Healthcare Solutions (HHS), we really mean it: you should have not only different types of specialists working together but also specialists from different parts of your organization. For example, just imagine what a team made up purely of IT professionals would accomplish if they didn't have any medical professionals on board!
Mark: Whoa, bot. You just made up a consulting firm (HHS?) that you're pitching?
Implementing lean requires management that leads by example.
Many people think that lean management is just about leadership. However, it's not just about leadership–it's also about management. Leadership and management are two sides of the same coin: one cannot exist without the other. Management leads by example and sets a good example for others to follow. When they see their manager making efforts to improve their processes, employees will also try harder at their jobs and become more motivated overall.
Mark: This paragraph doesn't add much…
Organizing around a problem-solving culture and creating cross-functional teams can go a long way toward making your organization more efficient.
If you're looking to take your healthcare organization from an inefficient mess of separate silos to a lean, mean, problem-solving machine, here are three things that will help:
- Leadership. As with most projects, leadership is key. It's not enough for your C-suite to say “make it happen.” They have to get involved and make sure everyone in the chain of command is working together toward a common goal. That means keeping their eyes on the ball at all times–not just when something goes wrong but also when everything's going right. A leader should be able to clearly articulate where they want their organization to go and what they need from each department in order for them to get there.
- Cross functional teams are good too! Alongside this kind of leadership structure, organizing around cross functional teams can go a long way toward making things efficient within an organization–and as an added bonus–it makes everyone feel like they're doing something important!
Mark: Silly bot, that was only two things?? It's really running out of steam for sure…
Conclusion
We've all heard the phrase, “If you can't beat 'em, join 'em.” We think that this is just as true when it comes to implementing lean healthcare improvement. If you're not ready to fully embrace lean, start by adopting some of its principles. You'll be surprised how much your organization will benefit from them!
Mark: The intent and use case of the AI writing tool is to write a “good” first draft. I think it did surprisingly well at that task. What do you think?
Here's what the latest version of ChatGPT wrote using the same prompt in October 2024:
Lean in Healthcare: Transforming Care with a Focus on Culture, Leadership, and Continuous Improvement
Lean is a powerful approach for transforming organizations, and its application in healthcare has gained significant traction over the past few decades. Originating from Toyota's production system, Lean focuses on eliminating waste, improving efficiency, and delivering greater value to customers. In healthcare, this translates to delivering better patient care, optimizing processes, and fostering a culture of continuous improvement. In this post, we'll explore how Lean principles can reshape healthcare, the role of leadership in driving change, and the importance of cultivating a culture that sustains these improvements over time.
Understanding Lean in Healthcare
Lean in healthcare is often associated with the Toyota Production System (TPS), a management philosophy that emphasizes the identification and elimination of waste, continuous improvement, and respect for people. In the context of healthcare, waste can be anything that doesn't add value to the patient experience, such as long waiting times, redundant paperwork, or inefficiencies in patient flow. By applying Lean principles, healthcare organizations can streamline these processes, reduce delays, and focus more on patient-centered care.
At its core, Lean is about maximizing value while minimizing waste. This resonates deeply in healthcare, where improving patient outcomes, reducing costs, and enhancing staff satisfaction are critical goals. But it's not just about tools and methods–it's about creating a culture of continuous improvement where every staff member feels empowered to make changes and improve their daily work.
Leadership's Role in Lean Healthcare
Successful Lean transformations in healthcare begin with leadership. Leaders play a critical role in fostering a culture that embraces Lean principles and practices. In healthcare organizations that have successfully implemented Lean, leaders act as coaches and mentors, guiding their teams through the journey of improvement rather than dictating solutions.
For example, a Lean leader in a hospital setting might spend time on the floor, engaging directly with nurses, doctors, and other staff to understand their challenges and encourage them to voice their ideas for improvement. This practice, known as Gemba walks in Lean terminology (where “Gemba” means “the real place”), allows leaders to observe processes firsthand and engage with employees who know the work best.
In Lean organizations, leaders are not just managers–they are servant leaders who prioritize the needs of their teams and create an environment where psychological safety allows for open discussions about mistakes and opportunities for improvement. This shift from traditional command-and-control management to collaborative leadership is crucial in healthcare, where high-stakes environments and complex processes require constant learning and adaptation.
Building a Culture of Continuous Improvement
Culture is the backbone of any successful Lean transformation. In healthcare, where the stakes are high, creating a culture of continuous improvement is essential. This culture is built on the idea that small, incremental changes, made consistently over time, can lead to significant improvements in patient care and operational efficiency.
A continuous improvement mindset requires everyone in the organization–from frontline staff to executives–to see problems as opportunities. For example, when a nurse encounters an issue with medication delivery, a Lean-oriented culture encourages them to bring it up, suggest improvements, and work with a team to solve it. This shift from problem-hiding to problem-solving is a critical change in mindset.
One way to foster this culture is through the use of Kaizen, a Lean practice focused on small, incremental improvements. Kaizen events in healthcare might focus on reducing the time patients wait for surgery, improving the discharge process, or streamlining patient flow in the emergency department. The goal is to create a work environment where every employee feels they have the tools and support to make changes, no matter how small.
Lean Tools and Methods in Healthcare
Lean brings with it a suite of tools and methods that can be adapted to healthcare settings, such as 5S, Value Stream Mapping (VSM), and Standardized Work. While these tools are valuable, it's important to remember that they are just that–tools. They are not the goal but rather a means to create a more efficient and patient-centered healthcare organization.
- 5S helps organize the workplace by eliminating unnecessary items and ensuring everything is in its place, which can reduce time spent looking for supplies and improve safety in clinical areas.
- Value Stream Mapping (VSM) enables healthcare teams to visualize processes and identify waste, such as unnecessary steps or delays, to streamline patient flow and reduce waiting times.
- Standardized Work ensures that best practices are consistently applied, reducing variation in care delivery and improving outcomes for patients.
While these tools are helpful, they must be applied within a framework of continuous improvement and respect for people. Simply implementing Lean tools without focusing on culture will not lead to sustainable results.
Real-World Examples of Lean in Healthcare
Many healthcare organizations have successfully implemented Lean principles, achieving impressive results in patient care and operational efficiency. For example, Virginia Mason Medical Center in Seattle is a well-known Lean healthcare pioneer. By using Lean to eliminate waste and focus on patient safety, Virginia Mason has dramatically reduced medical errors, improved patient satisfaction, and cut costs.
Another example is ThedaCare in Wisconsin, which has embraced Lean management to empower its staff and eliminate inefficiencies. Through initiatives like Daily Huddles, frontline staff and leaders come together to identify problems and collaborate on solutions, fostering a culture where everyone is involved in improvement efforts.
Mark: Oops, that's outdated information about ThedaCare – what's going on?
These examples demonstrate that Lean is not a one-size-fits-all solution. Each organization must adapt Lean to its unique needs, focusing on both process improvement and cultural change.
Challenges and Opportunities in Lean Healthcare
Implementing Lean in healthcare is not without its challenges. Cultural resistance, a lack of understanding of Lean principles, and the time required to train staff can be significant barriers. However, the opportunities for improvement are vast. Lean can help healthcare organizations address pressing issues like reducing patient wait times, improving quality, reducing costs, and creating a work environment where staff feel valued and engaged.
The journey toward Lean in healthcare is a long-term commitment that requires perseverance and patience. It's not about quick fixes but about creating an organization that can continuously adapt and improve. Leadership must set the vision and create the conditions for sustainable cultural change, where every team member understands that their role is crucial to the organization's success.
Conclusion: Lean as a Pathway to Better Healthcare
In a time when healthcare systems around the world face mounting pressures to improve care while controlling costs, Lean offers a promising pathway forward. By focusing on continuous improvement, engaging leadership, and cultivating a culture that empowers every team member to contribute, healthcare organizations can transform their processes and deliver better care to patients. The lessons from Toyota and other Lean pioneers remind us that the journey is just as important as the destination. Through a shared commitment to learning and improvement, the future of healthcare can be brighter for patients, providers, and leaders alike.
By embracing Lean, healthcare organizations can move beyond traditional methods and build a system that is truly patient-centered, resilient, and continuously improving. This transformation, though challenging, holds the promise of a healthier and more efficient future for all.
Please scroll down (or click) to post a comment. Connect with me on LinkedIn.
Let’s work together to build a culture of continuous improvement and psychological safety. If you're a leader looking to create lasting change—not just projects—I help organizations:
- Engage people at all levels in sustainable improvement
- Shift from fear of mistakes to learning from them
- Apply Lean thinking in practical, people-centered ways
Interested in coaching or a keynote talk? Let’s start a conversation.
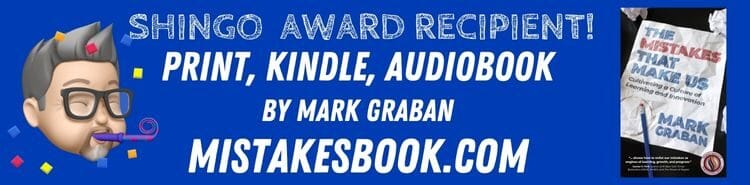