It was a real treat to hear Larry Culp, the CEO of General Electric and CEO of GE Aerospace, speak at the AME 2022 annual conference in Dallas. He recently reached the four-year mark of his tenure as GE's first-ever outsider CEO (read the 4-year update that Larry posted on LinkedIn).
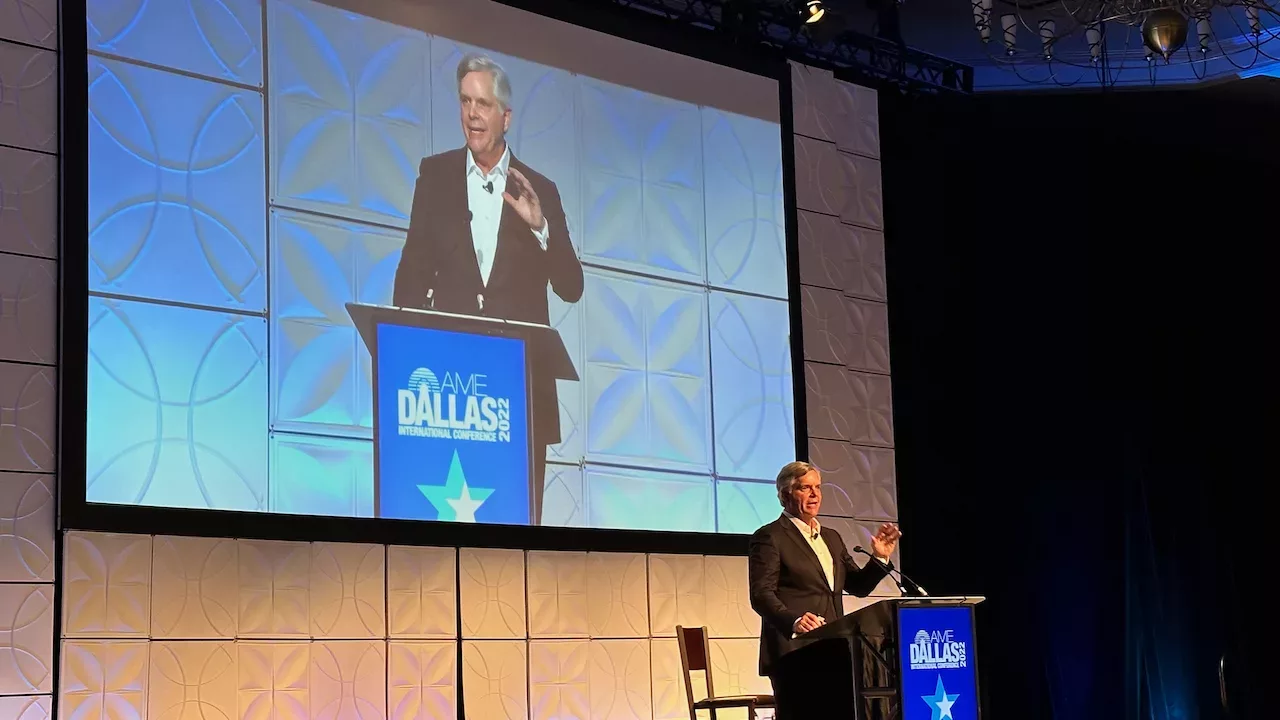
Larry previously became CEO and Chairman of Danaher in 2001 (the same year Jack Welch retired from GE), and he retired from Danaher in 2015.
Below are some highlights and quotes from his 15-minute remarks, along with some of my commentary and thoughts.
If you attended AME, the recording of Larry's session is now available through the conference website (your login is required).
After speaking, Larry had a longer “fireside chat” with our friend Katie Anderson on stage. Katie and I will discuss his remarks and their discussion in Episode #464 of the Lean Blog Interviews Podcast.
Hear Mark read this post — subscribe to Lean Blog Audio
The Goals That Matter
Larry is probably amongst a small percentage of CEOs who explicitly talk about safety (the late Paul O'Neill of Alcoa was another).
The goals, as Larry stated:
“…safety, quality, delivery, cost – in that order, every day.”
SQDC. See a blog post that I've written about that:
Safety first — there is no other way. Or, we'd like to think that would be the norm, not just in manufacturing but also in healthcare.
Not Knowing Any Other Way
In referring to his own “Lean journey” as a leader, he wanted to focus on the journey at GE more so than talking about his past at Danaher, although that time there certainly made him the leader that he is today at GE.
When Larry was brought into GE as CEO, he recalled that people asked him, “Are you going to bring the Danaher Business System (DBS) to GE?”
“I don't think I have used that acronym at all in the last four years at GE, but I do admit I'm a product of 25 years of that environment. If you want me to manage and lead in a different way, I do not know how. What you see is what you get.”
I've heard that same sentiment from other leaders who were deeply influenced by Toyota (or, in Larry's case, Shingijutsu, the famed Japanese consulting firm made up of Toyota retirees). Being a “Lean leader” isn't just a coat that you put on — if you're doing it well and doing it sincerely, it's who you are.
A Passion for Manufacturing
When he graduated from Harvard Business School in 1990, going into manufacturing wasn't the cool thing to do. But he viewed manufacturing as an important calling, just as I did in the late 1990s when I chose the “Leaders for Global Operations” program (then called “Leaders for Manufacturing”) at MIT that, at the time, had a stated mission of rescuing American manufacturing.
“Many of you will remember that the consensus at that point within the US was ‘manufacturing was dead,' or at least dying. That was really all the contrarian in me needed to hear… sparked my interest in American manufacturing renaissance.”
So Larry took a job at Danaher and worked his way up to the CEO role just 11 years later.
Within Danaher, he says he was fortunate to learn the word “Kaizen,” having opportunities to travel to Japan because “Danaher was one of the first, if not the first, company in the US to bring the Toyota masters, Shingijutsu, into our facilities.”
“I spent a week building air conditioners [in Japan], being pushed, probably cursed at, in Japanese. A week I will never forget.
It really was a formative experience for me in terms of the principles around daily management, around standard work, around Kaizen. The concepts were not necessarily alien to me, but the way we were taught that week to really operationalize those ideas has stayed with me to this very day.”
Toyota is well known for sending leaders to work in manufacturing as part of their orientation to the company — not just being there, but doing front-line jobs (as Isao Yoshino has described… and Steve Spear had the same opportunity when he started studying Toyota as an academic).
Lean Transformation at GE
Larry spoke of the “Lean transformation of GE,” as he called it. He's aiming for a “true Lean culture.”
When he joined in 2018, “the company was obviously not enjoying its finest days.” Larry noticed they had great people and great technology, but the “operational foundation of the company wasn't nearly as strong as it could be given the talent.”
Where did he start? In an “old school” way, with shopfloor Kaizen Events led by the famed Shingijutsu firm out of Japan. What does Larry think about these?
“There's nothing more fun.”
How great is that to have a CEO who thinks that a shopfloor Kaizen Event is “fun”??? Or that nothing is more fun?
He added about the importance of leaders coming to participate in the events:
“It's not strictly about manufacturing, particularly at GE. But I've long been of the view that if you are not running these events, if you are not actively participating in these events, put aside the improvements that you will forego, you really can't internalize the core Lean principles.”
That reminds me of what Toyota people say about improvement (recognizing they don't rely heavily on formal week-long events) — it's not just about the improvement results, it's also focused (if not primarily focused) on developing people in the process.
Larry says that he should be involved in more events and he wants more events to happen in 2023.
“This really is the bottoms up effort that is underway at GE.”
There's also the “top down” effort of “Hoshin Kanri,” which we'll get back to later. That's what the former Toyota people always say, that Lean / TPS is BOTH top-down and bottom-up.
Larry stated:
“We're in the early innings of the Lean transformation at GE. COVID didn't help, but we all have worked our way through that. I couldn't be more excited, more confident about what GE is going to do going forward.”
The Impact of Kaizen Events
Done properly, improvement work doesn't just develop people — it engages them. Lean should benefit all stakeholders and Larry told a story to illustrate that. Larry was in Evendale, Ohio for the report out of an event and, in a company with a history of some contentious labor / management relations…
“It was just so gratifying to hear Garret Farson, the UAW committee man, go on and on about the impact that the events and the principles are having, not only on our performance — we're reducing cycle time, improving our on time delivery — but in turn, the culture.
If we've got Garret on our side, and so many of his colleagues and others in management positions, it's easy to be optimistic about the future at GE.”
Kaizen, the recognition that everything can always be better, requires humility, as Larry talks about in this short video. “Leading with humility” is one of the core leadership values that Larry promotes at GE (along with transparency and focus).
Top Down and Bottom Up
Again, Larry emphasized the need for top-down AND bottom-up, showing a diagram on screen. It was familiar to me (it's similar to a diagram that's been used by Masaaki Imai for a long time), but the name “Nemoto diagram” was new to me. It “hangs in my office,” Larry said.
I apologize that the angle makes it hard to read. You can see a similar diagram on this website.
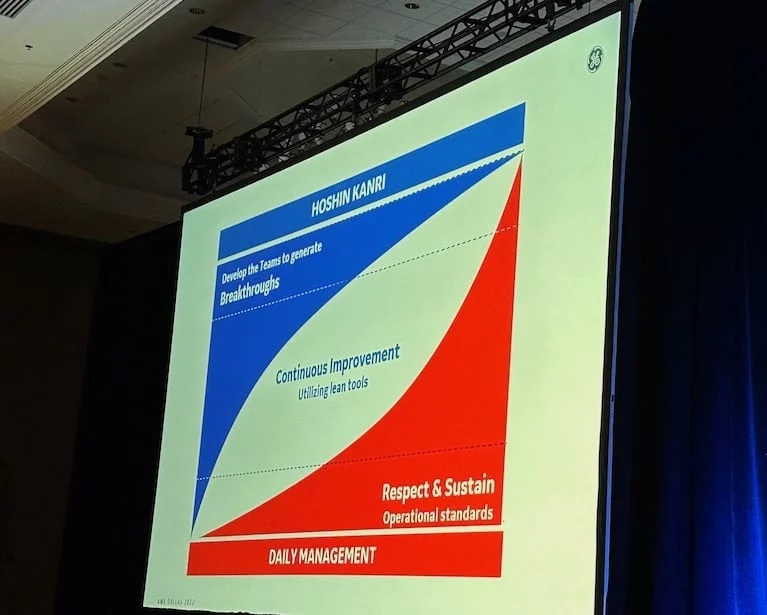
The diagram shows that top leadership should be spending most of their time on “develop the teams to generate breakthroughs” (note it doesn't say “have the breakthrough ideas”) and some time on “continuous improvement utilizing lean tools.”
Middle management spends less time on “breakthrough” and more time on C.I., while spending some time on “respect and sustain operational standards.”
People at or closer to the front line might participate a bit in breakthrough and more on C.I. — but they're spending more of their time on “respect and sustain.”
Daily Management
Larry also spoke about the engagement that comes with a focus on “daily management” instead of just rushing at the end of the quarter to hit your numbers.
“I was so thrilled that one of [our team members] said, “Daily management? I'm into hourly management now. Because if I don't jump on a problem and get to root cause in 24 hours, I'll lose my week.
He said this in the second week of the quarter. A company that been very much geared over time for the last two weeks of the quarter. To have somebody talk about hourly management the second week of the quarter, I was pretty happy in that moment.”
Bottom-up management is combined with top-down management, which to him is “Hoshin Kanri” (a.k.a. strategy deployment).
Hoshin Kanri
Larry described “HK” as a way to “operationalize” the ambitions of a company, as a way of:
“…systematically channeling and harnessing that ambition toward real breakthroughs.”
And on that note…
The Books That Larry Recommends
Larry is clearly a reader and he recommends a number of books to his team so they can get a better grounding in Lean and related topics.
The classic, “The Machine That Changed the World is a really great place to start.”
As pictured below in a slide he used, Larry also recommends other books. You'll notice that they're not all “Lean” books and, to me, that's not a surprise, and I think that's good. They are:
- Good to Great by Jim Collins
- Principles by Ray Dalio
- Topgrading by Brad Smart
- The Carolina Way by Dean Smith
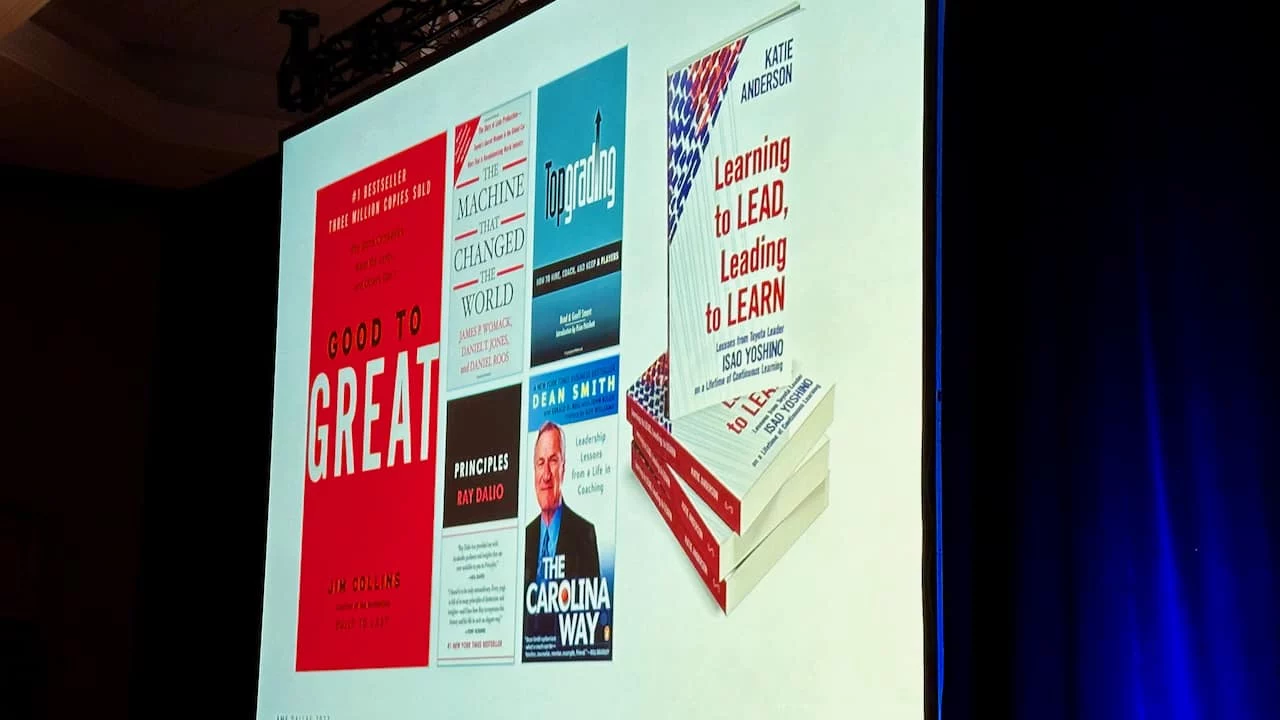
Larry also highly recommends the book by our friend Katie Anderson: Learning to Lead, Leading to Learn. We talk about that more during our podcast episode that will be released Wednesday.
“It was another book that had caught my attention earlier this year, ended up in my summer reading book bag, and has been something that has really helped me think about leading in a Lean principled way.”
As they discussed in the fireside chat, Larry was impressed with how well Katie articulated some thoughts about Hoshin Kanri — and he learned from that.
His Lean journey continues, as does GE's. I'm impressed that Larry still seems eager to learn, that he doesn't claim to know it all, and he doesn't make it all about him.
Larry's Conclusion
“There's a lot happening here. There's a lot that you'll read about in newspapers, but what you won't read about is very much what is near and dear to so many of us. That is what happens day in, day out in our factories and our service depots, and increasingly in our office locations, and our boardrooms as we drive the Lean transformation…
Not only with an eye for better results, but a true Lean culture at all three GE businesses in the future.”
It's not just about manufacturing. It's about the business — which means the people and the culture, not just the results.
The media gave a lot of attention to Jack Welch (including his Six Sigma approach) — they were a much bigger company back then, and Jack seemed to love being on the covers of magazines and books.
Will the media give a fraction of that attention to GE's Lean transformation under Larry? Will they write about what's happening in the factories or just fixate on the stock price and other numbers? Time will tell.
Thanks again to AME for having Larry speak at the conference!
Here is the podcast with Katie:
I'll also post various highlights from the fireside chat between Larry and Katie.
Here's the first post:
Please scroll down (or click) to post a comment. Connect with me on LinkedIn.
Let’s work together to build a culture of continuous improvement and psychological safety. If you're a leader looking to create lasting change—not just projects—I help organizations:
- Engage people at all levels in sustainable improvement
- Shift from fear of mistakes to learning from them
- Apply Lean thinking in practical, people-centered ways
Interested in coaching or a keynote talk? Let’s start a conversation.
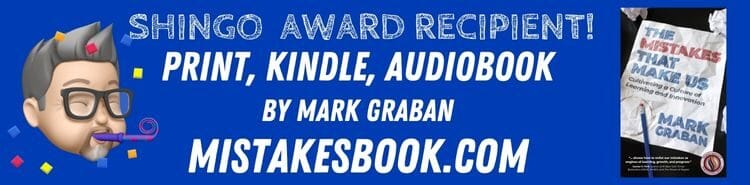
[…] And be sure to visit Mark’s website to read his reflections about our interview here and his summary of Larry Culp’s keynote here. […]