Scroll down for how to subscribe, transcript, and more
My guest for Episode #453 of the Lean Blog Interviews Podcast is Sarah Boisvert. She is the founder of New Collar Network and Fab Lab Hub.
Her career spans advanced “smart” manufacturing, art and music, and innovative workforce training.
Her mission as part of the Fab Lab Network is to create pathways that often do not require college degrees to well-paying, engaging “New Collar” careers, utilizing disruptive technologies like 3D printing, laser machining, robotics, VR and AI/machine learning.
She's joining us on the podcast from Albuquerque.
She is the author of the books The New Collar Workforce and People of the New Collar Workforce.
In collaboration with Santa Fe Community College, Boisvert also founded the New Collar Innovation Center at the Santa Fe Higher Education Center in 2021 to foster innovation in lifelong learning, New Collar workforce training, and the creation of 21st-century startups.
Sarah is going to be part of a main stage keynote panel at the AME annual conference, being held in Dallas, October 17 to 20.
Joining Sarah on the panel are Deondra Wardelle, who was my guest in Episode 405, and also Amy Gowder, President and CEO of GE Aviation Military Systems Operations. I'm going to be moderating the panel.
Today, we discuss topics and questions including:
- You've done many fascinating things in your career… but to ground the conversation, for this podcast, what was your first exposure to Lean manufacturing?
- Deming?
- Lean in your kitchen?– her choice, reducing frustration
- “Lean is people centric”
- You said in 2018: “U.S. manufacturing companies are expected to face a shortage of 2 million skilled workers by the year 2020.” — assume this came true? Made worse by the pandemic?
- It's worse, much worse than predicted?
- A problem beyond manufacturing
- For these new technologies…Which of those skills are most in short supply?
- What are the skills that “new collar” employees need to have… coming out of high school?
- Problem solving — it CAN be taught
- As you shared on LinkedIn… “General Motors is expanding hiring requirements to skills, not just degrees!
- Give an example of how “degree creep” causes problems?
- Working with Los Alamos National Laboratories to also change hiring policies?
- As an expert in 3D printing, how do you help companies decide when 3D printing isn't just “cool” but is actually more effective and the preferred choice?
- Are your earrings 3D printed? YES
- What are the benefits of 3D printing??
- There are people in Dallas working on a 3D-printed house. Made of Concrete?
The podcast is sponsored by Stiles Associates, now in their 30th year of business. They are the go-to Lean recruiting firm serving the manufacturing, private equity, and healthcare industries. Learn more.
This podcast is part of the #LeanCommunicators network.
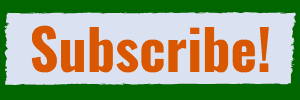
Video of the Episode:
Thanks for listening or watching!
This podcast is part of the Lean Communicators network — check it out!

Automated Transcript (Not Guaranteed to be Defect Free)
Announcer (2s):
Welcome to the Lean Blog Podcast. Visit our website www.leanblog.org. Now here's your host, mark graven.
Mark Graban (13s):
Hi, it's Mark Graban here. Welcome to Episode 453 of the podcast. It is August 10th, 2022. My guess today is Sarah Boisvert. You're gonna learn more about her in a minute. She is going to be a panelist on the main stage at this year's AME or Association for Manufacturing Excellence annual conference. So we're gonna talk a little bit about that panel, give a preview, but we're gonna talk about all kinds of interesting things from her career involving technologies like 3D printing. When should we use that? Because it makes sense as opposed to just seeming new and cool. We're gonna talk about some of the new workforce requirements that modern companies are going to face with the, all of these new technologies and what you call is 21st century apprenticeships to give people the skills that don't require college degrees.
Mark Graban (1m 4s):
So Sarah's got a great background, a really interesting background. We'll talk about lean and how that fits in to these technologies that she's been involved with as a entrepreneur and as a leader. So for links and show notes and more go to lean blog.org/ 4 53. Well, hi everybody. Welcome back to the podcast. My guest today is Sarah Boisvert. She is the founder of the New Collar Network and the FabLab Hub, her career spans advanced smart manufacturing. And we'll learn about that a lot today. She's also done a lot in the realms of art and music and innovative workforce training.
Mark Graban (1m 45s):
So Sarah's mission as part of the fab lab network is to create pathways that don't always require college degrees for people to get well paying, engaging careers, which she calls new caller careers. So we're gonna be talking about that a lot here today, careers that utilize disruptive technologies like 3D printing, laser machining, robotics, VR, and AI, or machine learning. So before I tell you a little bit more about Sarah and her background and career joining us from Santa Fe, New Mexico, welcome to the podcast. How are you?
Sarah Boisvert (2m 18s):
Oh, thank you so much for having me on your podcast.
Mark Graban (2m 22s):
I'm gonna ask you real quick for those who are watching on YouTube, you might notice why I'm asking are your earrings 3D printed?
Sarah Boisvert (2m 31s):
My earrings most certainly are 3D printed. And it's interesting because technology people always ask me, why do you always wear those same earrings? And they're fabulous branding. So everyone knows me by my neon green earrings.
Mark Graban (2m 50s):
And, and, and you said I'm afraid to cut out. They're certainly not 3D printed or they certainly are.
Sarah Boisvert (2m 56s):
Oh, they certainly
Mark Graban (2m 56s):
Are. They certainly are. Okay. Just wanted to confirm that they are a cute, cool kind of cubic open cubic shape. So maybe we can find a way to share a picture of those in the notes for those who are just listening. But Sarah is the author among other things. She's the author of two books first off the new caller workforce and the second book called people of the new caller workforce. So in collaboration with Santa Fe community college, Sarah has also founded the new caller innovation center at the Santa Fe higher learning education center in the 2021 recent project to foster innovation and lifelong learning, new caller workforce training and the creation of 21st century startups.
Mark Graban (3m 39s):
So I also wanna mention, as a couple of my previous guests here recently have been, Sarah is going to be part of the AME annual conference. She's gonna be it's being held in Dallas, October 17th through 20th, for more information or links for how to register, look in the show notes for that. And so Sarah's gonna be part of a main stage keynote panel. Joining her in that panel are going to be Deondra Wardell, who is my guest here in episode 405 of the podcast. And also Amy Gowder, the president and CEO of GE Aviation Military Systems Operations. I'm gonna be moderating that panel. So it's gonna be a good time.
Mark Graban (4m 20s):
Deondra… Listeners will know has been a good friend of mine and, and, and people may not know Amy Gowder is my wife. So I say that in the interest of full disclosure, we're still still figuring out how much that needs to be disclosed. But so Sarah, again, thank you for being part of that group and, and for joining us here today. Yeah. I, I want ask you about some of the topics you would wanna discuss in that panel. You know, you know, the AME theme is “embrace disruption,” but you know, before I do that, I wanna ask you a question that I ask most of my guests here, you know, lean manufacturing has been disruptive in different ways over, you know, the past decades.
Mark Graban (4m 60s):
What was your first exposure to new ways of manufacturing in, in particular here? Lean manufacturing?
Sarah Boisvert (5m 10s):
My first exposure was at Potomac Photonics in Maryland that had been a, an R and D company. And the founder Paul Christensen was looking for ways to develop a miniaturized eximer laser at 193 nano animators. And I joined him in the company as co-founder of the commercial division to commercialize that laser. So I helped them go from being an R and D company to implementing more codified manufacturing processes like lean.
Sarah Boisvert (5m 58s):
I had studied lean, of course, you know, the Deming work in my MBA program, which tells you I'm old. And I, I, I find that my friends joke that lean rules my life and that I use lean in my kitchen and I think that's okay. You know, I, I think that I see lean as a way to reduce stress in our lives.
Mark Graban (6m 29s):
Well, I, I think that's a, that's an amazing summary because, you know, if you're choosing to do something to improve your kitchen and that reduces stress in that setting, that's great. Think, you know, you and I are in agreement that lean is supposed to reduce stress for the people doing work, whether that's in a, a, a factory, a hospital, it should be eliminating waste, making work easier and more fulfilling, even though it seems like sometimes people get focused on tools instead of that important outcome. So I was, I was wondering if you could just tell us more about like, you know, why, why that's so important to you in terms of making work less frustrating I'm, I'm, I'm sure some of the Deming perspective that you had might have been helpful there.
Sarah Boisvert (7m 15s):
Yeah, it really was. And I think that, you know, as, as we talk about and, and was really one of the main themes, the last time I spoke at the AME conference, it was in Dallas and one of the main things there was how lean is people centric. And I find that a lot of managers don't respect the capability of people to solve problems. And so coming from the MIT fab lab world, you know, we're a meritocracy. And I think one of the reasons that MIT is such a special place is that we believe that everyone can solve problems and given the tools and, and the education and the opportunity.
Sarah Boisvert (8m 10s):
And I really think it goes beyond, it goes so beyond just having your factory floor run in an efficient way and taking, you know, those savings down to the bottom line. I think it also goes to this real sense of belonging and being a true part of a team. And I walk into so many factories where there's, you know, all this signage about the teams and, but they treat people like, like comb, you know, they teach, they treat them like they're, they're just cogs in a wheel. And in fact, when you implement lean improperly people step, most people, you know, I think want contribute and have fun and feel valued.
Sarah Boisvert (9m 1s):
And when valued, it just changes the whole dynamic in the,
Mark Graban (9m 9s):
Is that distinction as done properly or words similar to that effect, because I think one of the challenges is that anybody can do just about anything and, and put that lean label on what they're doing. And, and to your point, if a company has the mental model, that employees are a cost and employees are a problem. I mean, like when I started showing my age, when I started at general motors, that was still, that was the mental model. Employees were not viewed as a partner in a shared passion, which could have been the case, right. Building high tech engines for Cadillacs.
Mark Graban (9m 49s):
That's pretty cool stuff, but it was unfortunately like a, really the culture there was really degrading to the frontline staff. And, and yeah, that was the biggest impediment to then trying to progress and, and, and be more Toyota. Like as we got new leadership,
Sarah Boisvert (10m 6s):
You know, it, it's an interesting thing because what always struck me when I was visiting factories in Japan, which I did for many, many years, a third of my sales were in Japan at the beginning of the laser company commercialization. And in Japan, you have a small land mass with a awful lot of people and people are far more gracious to each other. And I, one time witnessed a, an accident in a parking lot, and they both jumped out of their cars and ran up to each other and started bowing and apologizing.
Sarah Boisvert (10m 54s):
And I spoke a little bit of Japanese so I could understand, but they were apologizing to each other. And I thought, good Lord, that would never happen in the US. You know, they'd be blaming each other and frustrated and, and, and after, and, you know, it was just, so I think the culture in Japan was really conducive to lean and it, it has taken us in manufacturing in the US sometime to embrace that cultural difference.
Mark Graban (11m 26s):
And I, I would propose, and I'm, I'm curious to hear your reaction, this idea, the problem is not the adaptability of workers. It's a, a problem with the adaptability of managers who have been leading a certain way for 10, 20, 30, 40 years. That often seems to be the roadblock. I'm curious your perspectives on that as someone who's been in leadership roles yourself.
Sarah Boisvert (11m 50s):
Yeah, no, I, I think you're exactly right. And, and when you coach people to work in a certain way, they, I find just step up to the plate. And so I have a really active, 3D printing, registered apprenticeship with the US Department of Labor. And it they'll invariably say to me, when they start, you mean, you're not giving me the answer, you know, what's the answer to this and I'll say, well, here's, here's how you're gonna find this. And we're gonna work on finding the answer together. And at one of them, after a while said to me, you know, at first I was really afraid that this was kind of like trick questions and you were using it to kinda weed me out.
Sarah Boisvert (12m 40s):
And, and it was like, no, we, we have to work together to find the solutions. And, you know, and particularly in this day and age, when we have, you know, YouTube and all of those wonderful resources for finding good examples and best practices is a lot easier, you know, than it was years ago when you had to go to the library. And so, you know, I really expect our people to offer solutions and they have different perspectives than I do. And they're the ones in the trenches. They are the ones who are, they're doing that, those jobs, although I've done all the jobs at that, any given moment, I'm not doing all the jobs.
Sarah Boisvert (13m 23s):
And so I think that people are still surprised when you look to them for their opinion. And I think it's because often their opinions are, are pushed aside and, and sometimes they're wrong. You know, sometimes their, their solution I've tried before. I actually, one of my, my lab manager recently said something and I said, well, you know, I've done this, this particular problem for six years and here's the data. And, and he said, oh yeah, I didn't realize you had tried all those things. And I had tried all those things he suggested.
Sarah Boisvert (14m 5s):
So then we had to really start thinking outside the box, right. Then you really, but you have to work together and you have to reinforce that you're accepting the person, you know, that, that you, you respect their ability to, to really come step up to the plate and create some good solutions.
Mark Graban (14m 27s):
Yeah. And, and, and that, that story really illustrates the difference between just somebody else might, you know, it would, would've been proud and like, well, you're wrong. I know better. And then they're discouraged from speaking up again. And, and it doesn't take, sometimes, sometimes it doesn't take more than one interaction like that for, for people to say, I've learned that speaking up is risky. Yep. And I can't be wrong. And if we wanna make sure we're not wrong, the easiest way to do that is to not take risks and not right. Speak up, whether that's in continuous improvement or as an entrepreneur, it's like, you've gotta be willing to, to take those steps and build a culture where people are willing to try things.
Mark Graban (15m 17s):
And
Sarah Boisvert (15m 18s):
Exactly. And, and sometimes, you know, ultimately I decide, right. Ultimately I, I make the final decision of whether something's gonna happen or not. But I think when you have good balance, not long ago, one of our registered apprentices decided to put a calendar to, to write a calendar on our whiteboard. And I'm not in that particular lab all the time. And I can't see that calendar. And I said to him, you know, you're welcome to keep a calendar here on the whiteboard, but you've got to duplicate it in our online calendar because I am often working at our other lab or I'm traveling, or I'm in my home office and I'm not there to see who's coming in that day or that you're gonna be off that day.
Sarah Boisvert (16m 10s):
Yeah. And I, I think that when you communicate it, and because we do a lot of peer review in our training classes, you know, I really have worked hard to get our people to move away from the you words. You know, you did this and you should, and all of that, but more, more about, well, how does that work? Or, you know, I happen to see that this failed, how can we fix this? You know, what do you, why do you think that went wrong? And then I can tell them why I think it went wrong and, and see where we meet in, in the middle.
Sarah Boisvert (16m 50s):
But I have to say that at Potomac, they got me. We very, very rarely had people leave the company. And it was because they were so respected by my partner. And I,
Mark Graban (17m 2s):
Yeah. Yeah. Well, I think that, you know, the, the story and what you're saying there illustrates that of, like you said, working together with people and, and coaching people through, whether you call it brainstorming or testing different things. There's a difference between knowing the answer and figuring it out.
Sarah Boisvert (17m 21s):
Yeah.
Mark Graban (17m 23s):
And that seems really powerful.
Sarah Boisvert (17m 24s):
And I, a problem with the education system is that teachers were trained and I have education, advanced degrees teachers were trained that they had to know the answer. And, and so we do all project based learning and it's, it's getting the teachers and that's not very different from the mentors in an apprenticeship program or managers in a plant. It's getting them to feel so comfortable with themselves to be able to say, gee, you know, I dunno the answer to that. And you know, we're gonna have to figure it out. We're gonna have to go find the answer. And maybe I know somebody who knows the answer, but why don't you start with maybe a literature search.
Mark Graban (18m 9s):
Yeah. So let's shift and, you know, I appreciate your focus on, on workforce development. And we'll, we'll talk about that, but I wanted to ask you first talking about a problem that people are trying to figure out how to solve in, in, in all sorts of settings. Let's focus on manufacturing. You, you wrote when your book was released in 2018, US manufacturing companies are expected to face a shortage of 2 million skilled workers by the year 2020 I'm I'm I'll just ask, did the, did that prediction come true? Was it worse than predicted? Has it been, how much worse has it been made by the pandemic?
Sarah Boisvert (18m 50s):
It is worse. I don't know exact numbers cause I haven't looked at it recently, but it is much worse. The manufacturing Institute and Nam are still looking at big in number of skilled workers. And I think that's, you know, as I talk about in the book, you know, that is one of the big problems is, you know, we already had this, this skills gap where, you know, and even though I wrote it, I did all the research in 20, in the last six months of 2017.
Sarah Boisvert (19m 35s):
So the information was pretty fresh, but it hasn't changed radically. What has changed is that the technologies that I talked about and I was particularly interested in manufacturing, but those technologies and now ubiquitous across industries. So now you've got robots who are the janitors in Walmart stores, and now you've got self-driving, you know, delivery vehicles and you've there, it's everywhere. You've got the dentist using 3D printing. And so the only difference that I'm seeing is that it's exacerbated beyond manufacturing and the, the great resignation, you know, did make it worse where people didn't want to go back.
Sarah Boisvert (20m 21s):
I'm hearing in the world that the pending recession, if it does happen is probably going to force a lot of people to go back to working in person. And I also read something and I can't remember where I read it in the last couple weeks that gen Z actually is missing the social interactions. It's a very social group and they're actually missing getting to see other people and other human beings. And that a lot of them are switching back to social social jobs, but it is an ongoing problem having these large numbers of, of job openings and not having a good pool, you know, of candidates.
Sarah Boisvert (21m 21s):
Yeah.
Mark Graban (21m 22s):
And so for some of these new technologies involving robotics and 3D printing and, and laser machining and things like that, what, what, when you look at the technologies, then how, how do you define the skills that are needed? Or what, what, how do you, how do you figure out which skills or most in short supply for, for that new technology environment?
Sarah Boisvert (21m 48s):
Well, as, as I talk about in the book, I had been asked by a number of fab labs in the United States to develop a two year curriculum for digital fabrication. And, and I thought, well, you know, I'd worked on this for my factory, but I knew what I needed. And so I, I looked at it and I thought, well, I'm gonna have to come up with a lowest common denominator. So I spoke with 200 manufacturers on what were the skills they needed for operators and technicians. I didn't see as much of a gap in engineers cause you know, we've convinced everybody, they have to go to college.
Sarah Boisvert (22m 33s):
So they go to college and become an engineer, which means we have no CNC machinist and we have no welders. And there's a huge gap in electricians right now. I mean, it's really serious. So I spoke to all of these companies and it turned out 95% of them were looking for people who had problem solving skills. And I'm not surprised by that because all of the new technologies that are coming on board, you haven't got the old guy in, in the back of the plant. Who's been there 30 years and can come and get, you know, the latest metal 3D printer up and running. You really have to be able to take these machines.
Sarah Boisvert (23m 15s):
And I see the 3D printing industry where the laser industry was 30 years ago where companies were just starting to understand that they needed customer service and
Mark Graban (23m 27s):
Not just technology.
Sarah Boisvert (23m 29s):
Right. Right. And I thought that HP entering the production 3D printing market around the time that I wrote the book was so fantastic, cuz they forced people to become more professional and to up their game on the customer service side, you can't depend upon the manufacturer in a new industry. And so you actually need somebody who can fix these new machines and get them up and running. But you also need people who can bring in new technologies and develop the processes that you need for your particular factory for the technologies are changing so quickly.
Sarah Boisvert (24m 12s):
And so many new technologies are coming on board that to say, you're gonna train somebody for X may not be applicable in a, in even a year. And so that was really one, the very big thing they wanted. They wanted hands on experience. They did want digital skills like CAD design and metrology because the tools of digital and many of them wanted 3D printing skills because subtractive and and additive are just so different. So it was, but that was across the board. I mean 95 of Fortune 10 down to startups.
Mark Graban (24m 57s):
So it's interesting. It sounds like, was surprised to hear that some of these new technologies, it sounds like increases demand for older trades that have been around a long time, welding and electricians or, or how much of that is increased. I might have this wrong. So lemme ask it as a question, how much of that is due to increased demand versus just reduced supply of like you said, people think I have to go to college instead of learning a trade
Sarah Boisvert (25m 27s):
On the demand side, it is that the skills have become digital. So, and I, I quote Thomas Friedman from the New York Times in the book because he had visited a welding company, I wanna say in Minnesota, you know, I haven't, I wrote the book a long time ago, so, and I think they were in Minnesota and they had been a welding company and they got a really high tech contract with a, in, in the defense space and suddenly they really needed to do welding. That was far more complex, far more advanced. It was truly advanced manufacturing. And so the old programs that just trained welders were no longer relevant and they need people who can read CAD files, who can deal with the digital side of the tools, but also understand metrology and, and more complex measurement systems.
Sarah Boisvert (26m 24s):
And so that's the demand side. So the demands have changed. And then on the supply side, you are exactly right. I mean, we've convinced everybody that, you know, you must go to college and it's just not for everyone. And so, but we end up with, I mean, when I went to high school, you, we had two tracks, you had the college prep track and you had the VO tech track and that's disappeared. Everyone is just, you know, channeled on this college track that may or may not be right for the person. And there are some wonderful jobs, you know, I can't, you know, in, in my book, the second book is behind me and it's an augmented reality book.
Sarah Boisvert (27m 14s):
And I have video that pops up, people talking about these kinds of jobs. And there's a guy from Potomac Photonics, John Ford in it who couldn't make it through community college. You know, he loved math. Didn't like anything else. He was a hands on learner, not a book learner, took a job with our company as an entry level operator of a laser system. And he in the video, that's in the book, he says, any job can have a bad day, but how bad can your day be if you get to play with lasers every day and become an engineer and run for laser labs.
Sarah Boisvert (28m 1s):
And you know, I, I look at the, particularly in the maker movement and so many of the, or the kids on the robotics teams and how fun is that. And you can make a decent living where you can support a family without all the college debt. And you shouldn't get me started on that topic. I mean, I won't give, I have to give you a chance to ask questions. No,
Mark Graban (28m 25s):
That's right. No, it's good. I mean, it's, it's an important topic. It's an interesting topic. I do wanna go back a little bit before kind of diving back into, you know, this, this idea of vocational training or, or reskilling or, or, or different types of work. We talk about, you know, the, this, this skill of problem solver or, you know, making sure everybody has that it's not a trade, it's not a job class. It's a skill everybody should have. What sorts of methodologies do you find most useful to teach? I think of, you know, a big part of lean is at least some approaches to problem solving. I'm curious if you teach people some of those methods and or other methodologies to, to, to get better at solving problems.
Sarah Boisvert (29m 15s):
Well, I think that most of the MIT graduates that I've ever met complain heavily about the problem sets, but I have never met an MIT grad who could not solve a problem. And my partner had done his master's in MIT PhD at Berkeley. And, you know, he could, he just could solve any problem and would go to visit a customer in a totally different fields, like, you know, chemical analysis and he would solve their problems for them. And I think that the methodologies that schools and, and project based learning really came out of McGill in, in their medical school.
Sarah Boisvert (30m 4s):
But that kind of teaching method is I think is key and has to start at the lower grades. And so that then when you get someone they already are, are used to problem solving, they're used to being able to do approximations. I mean, being able to do approximations is, is something that really everyone should be able to do in their everyday life and be able to get close to an answer and then refine it. So I think that there's a lot of lean things that we do that are are important, but I really think it comes back to the school systems and that we really have to get these kids young and get them into a mindset that is so different.
Sarah Boisvert (31m 8s):
And, and we also use peer review so that they learn to work in teams collectively and, and take everyone's good ideas. And I, it, it comes back to our education system really needing to be revamped.
Mark Graban (31m 26s):
Yeah. And I mean, and then back to what we were talking about earlier, some of the workplace culture being revamped, cause again, to that story that you told, it sounded like a, a process of kind, you know, team based, experimental learning. So I think like what you were sharing and, and what they were doing, you know, sound like a process of coaching them through that because one doesn't have to have a degree from MIT or a PhD from anywhere, right. Generally, you know, to solve problems related to your day to day work. So, so to that point, you know, what, what sorts of frameworks, how much of it can be taught versus just developed by having hopefully a good coach as you're trying to solve problems
Sarah Boisvert (32m 18s):
From one of the automotive companies on one time, say that problem solving could not be taught and that is wrong. I mean, that is just wrong. Problem solving can be taught and it can be taught K through 12, it can be taught in college and grad school and on the job on the factory floor. And it, it really is. And I, I use the Stanford D School Design Thinking model and it's, it's always so fascinating to me that even the people that work for me when we're in a design thinking exercise, they just want to go right to their first idea and on it.
Sarah Boisvert (33m 5s):
Yeah. And you just have to, you know, rip their little fingers off the keyboard or off the chalk and know we have to, you know, I wanna hear every idea, think about every possible way and think of the craziest idea, you know, think of, you know, that you're gonna bring some Wass down and they're gonna, you know, I wanna hear every possible idea, no matter how simple and efficient or how outlandish. And I think that when you get people, particularly in teams who start to work that way, and it, it opens up so much possibility than when they go to that first idea.
Sarah Boisvert (33m 50s):
And, and they're, they're not really thinking outside the box. And, and it's often the, the noisiest, most vocal person who, you know, brings up that idea first and, you know, you need to get everybody involved. And that, that's one of the ways that I, that I really try to develop our work and I'm actually going to be teaching problem solving for my city's managers through design thinking. And they, they they're gonna be in for a surprise cause they have, they, you know, I think they're thinking, well, it's gonna be a lecture and they have no idea how, how much fun this is gonna be.
Sarah Boisvert (34m 42s):
And I think that's the thing. I, I, I see how we teach and both on the factory floor with our workers and in our classes, and it's so much fun and people really enjoy it and they, they come to work happy to be there. Yeah. And that's what we want. Right. We want people to have good lives
Mark Graban (35m 7s):
And people's enjoyment in the workplace affects people's lives. Their studies that point to health impacts that that hating your job or being in a really dysfunctional workplace environment has all sorts of spillover effects unfortunately, to physical health, mental health home life. Yeah. Yeah,
Sarah Boisvert (35m 30s):
Exactly. And, and when I see somebody who is off kilter, you know, I give them a, you know, maybe they don't feel well that day. I mean, not by the minute, but if it goes on for more than a day or so, you know, I'll, I'll talk to them about, you know, so what's going on, you know, it seems, is it, is it us? You know, is it your, is it us? Is it something in your personal life? Is it, do you need some time off? I mean, you know, tell me what's going on that you seem not yourself. Maybe you're in pain, maybe, you know, you have something physical going on and how, how can we work with you to solve that problem?
Sarah Boisvert (36m 11s):
And cuz otherwise it just festers.
Mark Graban (36m 15s):
Right. And right. Yeah. A little bit of caring and empathy goes a long way. Yes.
Sarah Boisvert (36m 23s):
Yeah it does. And, and it's good for me because I, I, it's not fun for me to go into a cranky office or a cranky lab or people being, you know, destructive, you know, internal physically destructive, but destructive to the culture that I have built and it's not good for me and, and it's not good for the person and we, we all, it has to be win-win
Mark Graban (36m 51s):
Sure. For sure. So Sarah, you touched earlier on, you know, the idea that a lot of, you know, people have been convinced college degree is the only way to go. Seems like a lot of companies have been convinced that hiring college graduates is the only way to go. So you, you shared recently on LinkedIn about how general motors has made a change to policy. I had seen this in the news, I think even before you shared it, looking at skills, not just degrees. So I was wondering if you could, you know, kind of talk about that dynamic of, I think you framed it degree creep. How, how does that end up developing and, and what can we do about that?
Sarah Boisvert (37m 31s):
Yeah. You know, and, and you know, we're highly educated and I love that I have the opportunity to have education and it was right for me, you know, it was the right path for me and I love school. And I think all the time about going back and getting a PhD in engineering, you know, for fun because I love school, but what, and so not to be disparaging of colleges, but colleges hit upon this idea that the more people that went to college, the more money they made, right. I mean, it's a typical business decision.
Sarah Boisvert (38m 12s):
So colleges went from being kind of for the public good to being businesses. And it was all about how do we, you know, make more money. And, and the way to do that is to convince the universe that everybody needs a college degree and you're gonna make more money. Well, also in my book, I talk about a study that was done in Baltimore that compared the salaries of people who had degrees at the same level. So say an AA degree in a STEM field versus a non STEM field.
Sarah Boisvert (38m 53s):
And I think the STEM field people made 23% more than the non STEM field. So, you know, it's one thing, if you, if you have an inclination, you wanna be a doctor, you wanna be a lawyer, you wanna be a brain surgeon. You wanna, you know, you wanna be a rocket scientist up the hill near me at Los Alamos. Clearly you need to go to college. And if you have the inclination and the desire and, and the, the capability both in terms of the school capability, but also, you know, the, the financial wherewithal, that's all great.
Sarah Boisvert (39m 34s):
But what colleges did is they convinced people that they all needed to go to college. So if you didn't have an inclination in a STEM field, you would end up going to, you know, a field like English. And while I, I think it's wonderful that we have English majors and I'm really thankful that I know how to write well, you know, if you're expecting to get out of college and pay back all of that debt, it's just not gonna happen. And so all degrees are not equal. They're, they're just not equal. And, you know, I hate to say it, but, and where you went to school is not equal.
Sarah Boisvert (40m 17s):
So I have an undergraduate degree in piano performance from a very famous conservatory. And, you know, I then did a master's in pedagogy on, at the University of Rhode Island. And it was shocking to me that there were people getting piano, performance degrees from this very nice little school. But, but I mean, my class in New York was not going to all get jobs or become famous concert camp. And if we weren't gonna make it, I mean, how are these poor kids? And you know, this other, you know, low level school, not disparaging, but you know, it was not the same level that I was used to.
Sarah Boisvert (41m 1s):
So I think we've done a real disservice to people by convincing them. And so the colleges then were churning out all these people. And as the employers started to look at it, it was like, well, you know, we could have somebody with a bachelor's degree and now if they have an AA degree, you know, they can actually do wiring or they can actually do welding or, you know, whatever it was. And there was a lot of assumptions there. And I, I think that it, it started to become with the HR people. It was easier for them to just say, oh, it requires an AA degree.
Sarah Boisvert (41m 44s):
Not, not just the skill of running a 3D printer or running a, a welding machine. I had a, a, an incident here in New Mexico where a 3D printing software company had asked me about the community college, developing some training programs for them. And they ended up doing it, hiring the people and the people got there and couldn't do any of the tasks. And he, and I had said to him at the time, the college could do this, but, you know, I can just develop digital badges for you.
Sarah Boisvert (42m 26s):
And he called me not long ago and said, I made such a mistake. I had to invest so much into the college and you could have had the badges and the people could have, cuz I've sent in people who could actually perform. And I think GM moving to, to this model was really important. It's more work for the HR people because now you, you know, you can't just check a box, you have really examine it more closely. This movement started with Ginny Rometty and Tim cook when they were on the workforce task force in the Trump White House.
Sarah Boisvert (43m 11s):
And in 2020, the Trump White House issued an executive order that required that all government agencies, federal government agencies had to reexamine their hiring practices to look at skills, not just degrees. And IBM has been doing this for almost decades, you know, IBM has that wonderful apprenticeship program in it. Ginny Rometty is really my role model. And in more recent times, it's Byron, August, August I think is, is the pronunciation from opportunity at work and are helping the states of Colorado and Maryland.
Sarah Boisvert (44m 0s):
For example, to see that we've between the colleges and the HR departments we've created, you know, really something that's not 10, sorry, that was a long answer.
Mark Graban (44m 13s):
No, it's a complex topic. And, and to that more relatively local to you, you've been working with Los Alamos National Laboratories, are you're helping convince them or helping them make progress on looking at skills more so than just
Sarah Boisvert (44m 31s):
Degrees. Yeah, we have. And we have worked with LANL for two years on this topic. So, you know, it's slow changing perceptions and particularly in an institution that has run all by PhDs, right? I mean line school of rocket scientist. And so their bias is for degreed people. Sure. But particularly when the white house executive order came out, they started to open up a little bit. And what I was particularly interested in is they have an entry level technician job through, and they had to also work with DOE because they were DOE labs.
Sarah Boisvert (45m 25s):
So they had to get DOE on board. So it's way more complicated, you know, than just the HR department saying, oh gee, you know, we're now gonna take skills. So they finally got everybody together and what they are calling it is an AA degree or equivalent experience, you know, so that does give some leeway to each department. So it could be a registered apprenticeship. It could be work on the job. You know, there's just a lot more options for how people can get into that pathway to learn, which are very good jobs.
Sarah Boisvert (46m 10s):
People stay, you know, people stay, people don't leave LA and they have wonderful benefits. And for poor state like New Mexico, it's, it's really important. And I'm, it was announced by their head of HR. Lori. Now I won't think of Lori's name Monto I think is her last name at our workforce summit in May in Santa Fe. And I was just so thrilled to see that progress at a big institution that we can point to. And, but it is more work for HR. You know, it is more work and the way that we teach with our digital badges, all portfolio based.
Sarah Boisvert (46m 58s):
So what allows me to do as an employer is to look at the portfolio. The student has to identify a problem either at life work, school sports, and then solve that problem and with photography or video and write up this portfolio. And it tells me an awful lot about a student's ability to solve problems, but that's a lot more work because I have to read through all these, I can't just say, oh, they've got a piece of paper. Yeah. And Byron from opportunity at work calls that the paper ceiling.
Sarah Boisvert (47m 40s):
And I think that is just such a great, great term.
Mark Graban (47m 43s):
Sure. So maybe one other topic, Sarah, that we can talk about a little bit 3D printing, you know, as, since you're an expert in that domain, you know, how would a company decide? How would you help them decide when 3D printing isn't just like cool, but actually the preferred technology, because it's more effective and in different dimensions of, of quality, or just being able to do things you couldn't do otherwise, how do you help them sort that out?
Sarah Boisvert (48m 17s):
Well, it's, you know, it's, it's changing really rapidly. There are three areas where hands down 3D printing is, is the solution of choice. The first is rapid prototyping, which has been used for a very long time on, I think it was Ford who like God, 10, 15 years ago bought desktop 3D printers to put onto the desks of their, their R and D staff, their R and D engineers. And so rapid prototyping has been a solution for a long time, for a lot of reasons, it's cheaper and faster than trying to do something where you have to make a mold or even to use a subtractive technology.
Sarah Boisvert (49m 6s):
And it comes, you can get a functional prototype immediately. It comes out of the printer, able to demonstrate a function. The other time that it makes sense is complex geometries. And you're seeing a lot of that in the aerospace industry. ABUS has told our group at MIT that, that we do a contract R and D for that they're saving 55% in weight when they go to complex geometries things.
Sarah Boisvert (49m 47s):
And when you're doing a complex geometry in 3D printing, you're able to design something in a way that could never be manufactured with subtractive or any other methodology. And so when you have those complex geometries, you're really looking at a whole different ballgame in terms of weight, in terms of number of parts. There's so many factors that are, that bring cost savings to, to the whole process. And the third time is when you're using mass customization.
Sarah Boisvert (50m 28s):
And that is because you can quickly produce one. And so you can produce a million different designs and print a million that are different. If I wanted to make money in the jewelry business, I would not 3D print my earrings. I would get a mold made and take them to China. And I could make them for less than a penny. A piece probably costs less than half a penny, a piece I can make 16 of these cubes in seven hours. That's not, that's just not economically viable.
Sarah Boisvert (51m 9s):
Sure. So, and I am always surprised when I talk to 3D printing people in different fields that, you know, they're, they're always trying to shoehorn the application into 3D printing and it's not always the right choice, many times it's the right choice, but sometimes it's not, and it's just another tool on the factory floor.
Mark Graban (51m 35s):
And when you and I had a chance to talk previously, you told me about something happening here in Dallas. I was able to go find a, a video of a 3D printed home that looked like it was actually, if I heard right. 3D printed concrete, you're kinda familiar with some of these applications.
Sarah Boisvert (51m 55s):
Yeah. It's really printed houses are pretty hot topic right now. And I'm still not a hundred percent convinced that they're advanced enough for the economics side of it to be viable. I, I heard that a company in Dallas went to 3D print a house in Tucson or Tempe, I guess it was. And suddenly the concrete is in a totally different humidity situation. And it took them three weeks to, to figure out how to fix the humidity problem.
Sarah Boisvert (52m 41s):
So there's still, I think working out the, the logistics of it, I am working with a company out of New York and that is able to 3D print a 1700 square foot house in 36 hours. So they have some very sophisticated processes that are able to increased speed. And as you know, speed, you know, time is money. So what we're trying to do in Dallas for the, the AME conference is to 3D print a house with habitat for humanities, Dallas chapter.
Sarah Boisvert (53m 27s):
And I just think it would be a great example of, you know, we, our theme is disrupting embracing disruption and, and all the technologies that are bringing disruption to, to our fields, whether it's manufacturing or anything else. And I thought, well, you know, that would be something that would definitely disrupt a company like, or, or an organization like habitat. I think that beyond 3D printing, I think the other opportunity in, in construction is in robotics. And there's a lot of things that robots can do that.
Sarah Boisvert (54m 11s):
And I'm thinking particularly of skyscrapers, where you're looking at something where you're reducing safety risks for human beings. I mean, my feeling is I work with the augmented worker group out of the world economic form. And our feeling is that, you know, robots are there to their cobots. They, they are there to, to really enhance the capabilities of humans and free us up to do the cognitive functions that are so special to us. And someday the robots will be equal to us, but they're not there yet.
Mark Graban (54m 52s):
Yeah. That I've, I've, I've heard toy to people talk about the application of robots as with any technology, not doing it, just to do it. But like you said, in instances where safety for humans would be a concern, let the robot help or let the robot do it right. Or if you really can prove quality would be better. You know, my understanding is that certain painting or certain welding is done better by robots. And some of those tasks are better done by humans and the humans sometimes can be more flexible. So it's interesting to figure that out. I was gonna ask one other thing about the, the 3D printed house. You know, what they showed was, you know, I think they admitted, it was pretty simple.
Mark Graban (55m 34s):
It almost looked like cinder block or poured concrete. And, and I think they made a point that you made even about earrings or other products, that there were probably certain homes that could only be built with 3D printing methods, complex geometries or something really architecturally. Interesting. We, we might see that more so than a replacement of, like you said, the, the plastic molded part versus 3D printing prefabricated traditional home versus 3D printed. But I guess it, it starts with these experiments.
Sarah Boisvert (56m 9s):
It does. And, and I think that, I don't know if I sent you the link to the house in, in, I think it was in Austin where it had curved walls and it was, was so interesting because on the inside of those curved walls, you know, then you had these really interesting rooms that were not squares. You had these rooms that had little alcoves where you could put a little table and chair and they were adorable. That was just really, really cute.
Mark Graban (56m 41s):
Yeah. Well, Sarah, it's great that, that you're helping people in all sorts of settings, figure out not just new disruptive technologies, but in a good way, disruptive approaches to training and hiring and developing and, and leading. So again, our guest here today has been Sarah Boisvert again, she's gonna be part of this panel discussion in Dallas at the AME annual conference, October 17th to 20th. I'm sure if you're there, you'll get a chance to, you know, come ask Sarah your own questions about these things, either as part of the panel or just being there around the conference.
Mark Graban (57m 21s):
So Sarah, thank you so much for sharing with us today, you know, a wide range of, of topics and expertise that you have to share. It's been a lot of fun.
Sarah Boisvert (57m 30s):
It was my pleasure.
Mark Graban (57m 32s):
Again, for more information about the AME annual conference being held in October in Dallas, go to ame.org or look for links in the show notes, leanblog.org/453.
Announcer (57m 44s):
Thanks for listening. This has been the lean blog podcast for lean news and commentary updated daily visit www.leanblog.org. If you have any questions or comments about this podcast, email Mark at leanpodcast@gmail.com.
Please scroll down (or click) to post a comment. Connect with me on LinkedIn.
Let’s work together to build a culture of continuous improvement and psychological safety. If you're a leader looking to create lasting change—not just projects—I help organizations:
- Engage people at all levels in sustainable improvement
- Shift from fear of mistakes to learning from them
- Apply Lean thinking in practical, people-centered ways
Interested in coaching or a keynote talk? Let’s start a conversation.
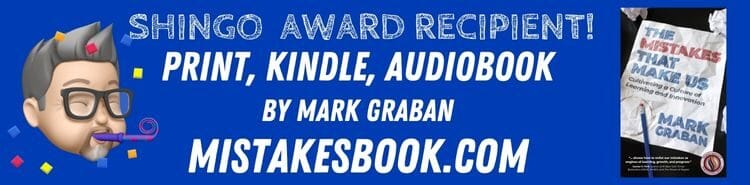