A version of this originally appeared on LinkedIn — Read and/or see the discussion that's been sparked there.
So many major publications (WSJ, NYT, Bloomberg) have printed a lot of misinformation about the supposed failures of “just in time,” an approach that's a core pillar of “Lean Manufacturing” or the “Toyota Production System.” This is something I've blogged about — a lot. Here's my recent post about the WSJ's bad take on JIT.
Supply chain shortages were a problem at the start of the pandemic and, for different reasons, it's a problem now. Or, I should say, it's quite often a problem with long, slow, global supply chains.
The journalists fail to point out that getting large batches shipped across the ocean is not actually “just in time.” Merely getting rid of your inventory is not “just in time.”
A new video, below, from a relatively unknown source, gets it right. It's worth the 20 minutes. Or jump ahead to about 11 minutes in.
Should we blame “just in time” for parts shortages, or blame factors like a shortage of shipping containers and port bottlenecks in southern California? True “just in time” systems (with relatively local suppliers) don't have the problems that we see with companies who offshored to a low-labor-cost country.
From the video's transcript:
“Just-in-time is such a simple principle, but the pursuit of the elimination of waste is now the central mission of any major manufacturer. However, most did it wrong.
Manufacturers globally saw the headline–elimination of inventory leads to massive efficiency gains–and jumped on that without actually determining what made it work for Toyota.
They ignored that Japan's small physical size made for short domestic supply chains, less vulnerable to things going wrong.
They ignored the company's production leveling–finding the average daily demand and producing that, regardless of short-term changes in demand.
They ignored the fact that eliminating excess inventory is different from eliminating all inventory.
They ignored the principle of growing strong teams of cross-functional workers, predicated on respecting people.
They ignored the culture of stopping and fixing problems, to get things right the first time.
They ignored huge swaths of the Toyota Way and created a system that's less effective and less resilient, but can impress shareholders through short-term savings.”
Is the root cause of these supply problems (and production problems) actually short-term thinking??”
You can also read about how Toyota “broke its rule” — but I'd argue they did no such thing, because their approach has always been more pragmatic (do what works) instead of being dogmatic (get rid of all inventory).
How Toyota thrives when the chips are down
Toyota may have pioneered the just-in-time manufacturing strategy but when it comes to chips, its decision to stockpile what have become key components in cars goes back a decade to the Fukushima disaster.
and it also adds:
“A Toyota spokesman said one of the goals of its lean inventories strategy was to become sensitive to inefficiencies and risks in supply chains, identify the most potentially damaging bottlenecks and figure out how to avoid them.
“The [Business Continuity Plan] for us was a classic lean solution,” he said.”
Businesses love talking about “low inventory,” but how often do they try to emulate Point #1 of “The Toyota Way” management system, which reads:
“Base management decisions on a long-term philosophy, even at the expense of short-term financial goals.”
Maybe we'd be better off if companies emulated the Toyota philosophy instead of trying to (badly) copy tools and methods. Or would they badly copy the philosophy as well?
Please scroll down (or click) to post a comment. Connect with me on LinkedIn.
Let’s work together to build a culture of continuous improvement and psychological safety. If you're a leader looking to create lasting change—not just projects—I help organizations:
- Engage people at all levels in sustainable improvement
- Shift from fear of mistakes to learning from them
- Apply Lean thinking in practical, people-centered ways
Interested in coaching or a keynote talk? Let’s start a conversation.
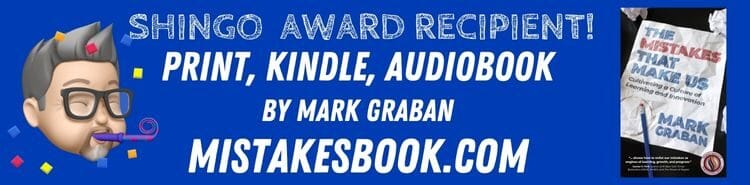
I tracked down the video’s creator:
https://en.wikipedia.org/wiki/Sam_Denby
Not sure where he got his Toyota knowledge, but clearly has some good sources!
Hi Mark
Anyway, can we be sure that Toyota has not supply chains problems nowadays?
Your reflexions are very interesting. We have to think again the lead time reductions.
Best regards
According to news reports, Toyota has definitely been affected by supply shortages, but they seem to be doing better than other automakers.
https://www.bloomberg.com/news/articles/2021-11-04/toyota-boosts-profit-outlook-despite-supply-disruptions
[…] is a potential tradeoff between efficiency and resiliency that businesses (especially those that misunderstood all aspects of the Toyota Production System) and policymakers should […]