Today's post is written by my friends at Creative Safety Supply. They have been a long-time sponsor of the Lean Blog and I appreciate their support.
The real question here is, can you really implement Lean strategies successfully without being OSHA compliant? And to that, I would say absolutely not. Following federally regulated OSHA standards not only saves a company from being penalized with thousands of dollars in fines, but it also serves as the baseline for workplace safety.
Obtaining and maintaining those baseline safety measures is what gives the company the ability to move forward with facility improvements. Hazardous conditions and OSHA penalties won't have the chance to get in the way of workplace productivity, efficiency, and profitability enhancements. With that being said, staying OSHA compliant is one of the core components required to start and maintain a successful Lean manufacturing program.
Staying compliant with OSHA regulations, and any consensus standards incorporated by reference, is necessary for the following three objectives:
- To follow standardized procedures that have been proven to keep employees safer at work.
- To train employees in becoming experts at their jobs.
- To build a relationship with employees that revolve around trust and a positive safety culture.
All three of these components, a direct result from maintaining OSHA compliance, are at the heart of Lean manufacturing methods. That heart being a fundamental respect for people.
Not respecting an employee's right to a safe workplace with the appropriate tools, training, and established best practice methods is a recipe for distrust, worker dissatisfaction, and a lack in motivation or knowledge to look for improvement opportunities. All of which are the exact opposites of what Lean hopes to achieve.
However, if all compliance hurdles have been tackled, the company can get into the nitpicky details that Lean manufacturing methods regularly deal with. Yes! I'm referring to the eight wastes of Lean, also known as DOWNTIME:
- Defects – Effort wasted by either fixing or throwing away product due to miscalculation, incorrect information, or process errors.
- Overproduction – Too much of one product produced before it's needed and more than what's necessary.
- Waiting – Wasting time due to waiting on product or another step in the production process to begin.
- Non–Utilized Talent – When workers are not given the opportunity to use their unique skills and talents.
- Transportation – Moving product and materials too much and too often.
- Inventory – Excess materials and products taking up space in storage without being used.
- Motion – Any unnecessary movement employees must take to complete simple tasks.
- Extra Processing – Putting in too much work for what the customer requires.
With that baseline of OSHA compliance, the aspects of DOWNTIME will be much easier to address. The goal here is to go one at a time, that way small improvements can be made without the facility being metaphorically spread thin like butter scraped over too much bread.
Forgoing OSHA compliance and solely attempting to achieve a Lean status can be done, sure.
But not well.
The subsequent fines, higher risks caused by workplace hazards, and mistreatment of workers become very real consequences. All of which will negatively impact the company's productivity and the employees' sense of self value.
Please scroll down (or click) to post a comment. Connect with me on LinkedIn.
Let’s work together to build a culture of continuous improvement and psychological safety. If you're a leader looking to create lasting change—not just projects—I help organizations:
- Engage people at all levels in sustainable improvement
- Shift from fear of mistakes to learning from them
- Apply Lean thinking in practical, people-centered ways
Interested in coaching or a keynote talk? Let’s start a conversation.
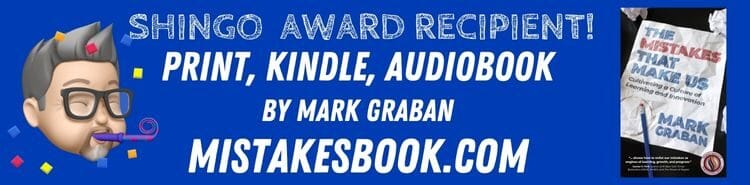