This image — a huge container ship coming from a far-off land — does NOT represent the Lean and Toyota Production System notion of “Just in Time.”
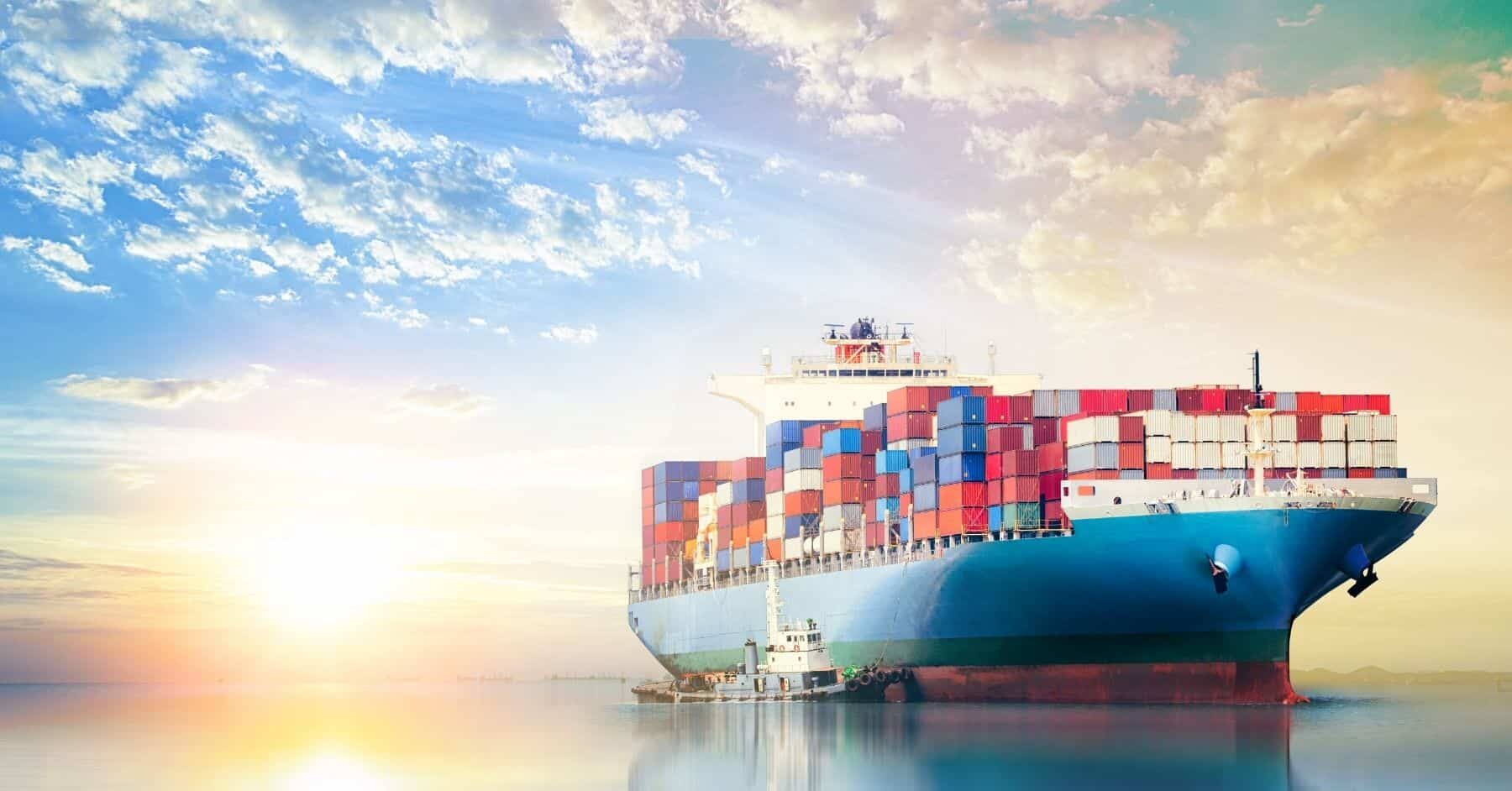
If you visit, for example, the Toyota factory in San Antonio, they have at least 18 ON-SITE suppliers. I've been in the factory. Many of these key suppliers are basically in the same building as the assembly line… with a bit of a demarkation.
Having local suppliers allows for FREQUENT deliveries, in small quantities — what is needed, when it's needed.
The default is NOT shipping parts across the country or halfway around the world, from China or elsewhere.
How does Toyota describe “just in time“?
“…the “Just-in-Time” concept, in which each process produces only what is needed for the next process in a continuous flow.”
There is more detail on that page.
A literal slow boat from China is not “continuous flow.” When you have such long distances, you have to guess what is needed instead of being able to product and ship only what is needed.
Just in Time should not bring to mind images of container ships and train cars. You should think of flow racks and AGVs.
Now, there are times when there are exceptions to the local supplier ideal. Sometimes a special component only comes from a plant in Japan. As we've seen in the news recently, computer chips increasingly come from China and that means longer, less predictable supply chains.
There are times when the automakers need to deviate from the JIT ideal. But, the media often thinks ALL deliveries to auto plants (even from China) should be labeled “just in time.” They're missing the details and they're mislabeling some of what automakers do as the general practice of JIT.
Case in point, yet another article from the WSJ that gets it wrong (as I've been cataloging for over 15 years on this blog):
Auto Makers Retreat From 50 Years of ‘Just in Time' Manufacturing
Pressured by pandemic, the hyperefficient supply-chain model pioneered by Toyota is under assault
The Journal confuses real JIT (flow and local suppliers that result in low inventory) with the result or goal of low inventory.
“Toyota Motor Corp. is stockpiling up to four months of some parts.”
That fact doesn't mean that Toyota is “retreating” from JIT. It just goes to show that JIT doesn't work for all parts from all suppliers — and that's ALWAYS been true. When you have longer, slower, less reliable supply chains — you need more inventory. That, again, has always been true.
Think of a healthcare example, like a vaccination clinic. If you're filling syringes in a subassembly area that's in the same large room as the vaccine injections, you can have a “just in time” delivery of syringes to vaccinators and the patient.
But, the vaccines themselves are shipped in large batches, which requires storage as the amount shipped doesn't match exactly hour-to-hour with the number of people vaccinated. There are degrees of “just in time” — it's not binary yes/no. The vaccine supply chain might be more JIT than some of these automotive semiconductors or other parts might be.
“The hyperefficient auto supply chain symbolized by the words “just in time” is undergoing its biggest transformation in more than half a century, accelerated by the troubles car makers have suffered during the pandemic. After sudden swings in demand, freak weather and a series of accidents, they are reassessing their basic assumption that they could always get the parts they needed when they needed them.”
When the supplier is next door, the “basic assumption” that you can always get the parts that are needed, when they are needed isn't a bad assumption. When parts are on the slow boat from China… bad assumption. Parts can get stuck in the Suez Canal, for goodness' sake.
I was surprised by this comment from a Nissan executive:
“The just-in-time model is designed for supply-chain efficiencies and economies of scale,” said Ashwani Gupta, Nissan Motor Co.'s chief operating officer. “The repercussions of an unprecedented crisis like Covid highlight the fragility of our supply-chain model.”
I'm surprised he would mention “economies of scale” instead of focusing on flow. Former CEO Carlos Ghosn sure did a number on them, with his more traditional auto industry mindsets.
The WSJ gives a rather poor definition of JIT:
The basic idea of just in time is avoiding waste. By having suppliers deliver parts to the assembly line a few hours or days before they go into a vehicle, auto makers don't pay for what they don't use. They save on warehouses and the people to manage them.
But as supply chains get more global and car makers increasingly rely on single suppliers, the system has grown brittle. The crises are more frequent.
Effective JIT would have parts delivered seconds or minutes before they go into a vehicle (as opposed to hours or days). You can do that with local, tightly-connected suppliers.
There are always going to be freak events that occur:
“A freak snowstorm in Texas in mid-February shut down a refinery that feeds production of 85% of resins produced in the U.S. Those resins go into components from car bumpers to steering wheels. They're some of the least expensive raw materials in a car, but they go into seat foam, and dealers can't sell a car without seats.
At the end of March, Toyota shut down production at several U.S. plants due to the shortage, according to a schedule seen by The Wall Street Journal, hitting production of some of its bestsellers, including the RAV4 sport-utility vehicle.”
I doubt Toyota will abandon JIT over this one incident, just as they haven't abandoned JIT after previous freak events, like the earthquake and tsunami back in 2012 that knocked a key Japanese supplier plant offline.
If you're afraid of freak events and you then decide to pile up inventory somewhere, that creates all sorts of other risks. If if that warehouse gets hit by a tornado?
The alleged countermeasure here is likely something that's been happening all along with parts that come from a long way's away:
“Executives say they don't want to replace just in time entirely, because the savings are too great. But they are moving to undo it to some degree, focusing on areas of greatest vulnerability. They are seeking to stockpile more critical parts, especially if they are light and relatively inexpensive yet irreplaceable like semiconductors.”
If parts are light and inexpensive (and small), then you'd tend to err on having more inventory. JIT does not place low inventory as the primary goal. It's the end result of good flow.
As I learned from a Japanese sensei 20 years ago, visiting a large industry crane factory that was struggling to produce and deliver to customers on time: “Job 1 is meet customer demand. Job 2 is low inventory.”
He was being practical, not dogmatic. He wasn't excusing a HUGE amount of inventory. But, this company we were visiting had confused JIT with “low inventory.”
The WSJ gives a bit of a Toyota history lesson in the story, including this:
“Thus emerged the system later known as just in time. Each day a stream of trucks would pull up to Toyota's factories and disgorge just enough to cover a day's worth of production.”
A “stream of trucks” is different than an occasional big-batch slow boat from China. The suppliers in Japan tend to be very local, as well.
The WSJ recognizes that, on some level:
“[JIT] was easier for Toyota to pull off, thanks to the coterie of loyal suppliers known as its keiretsu clustered around its factories.”
But then they make a questionable claim:
“The idea spread through other industries. Apple Inc., McDonald's Corp. franchises and big box stores like Target Corp. all use some form of just in time to keep inventory low.”
Apple, in particular, is build around the “chase cheap labor” strategy. I've never heard a Lean person refer to Apple as JIT. When I worked at Dell Computer 20+ years ago, most parts came in from halfway around the world. Dell brought parts into the factory every two hours, but the “just in time” was only the very last leg. It was sort of “fake JIT” because Dell could pressure suppliers into keeping WEEKS of inventory in a nearby “supplier logistics center” so Dell could do JIT order.
Toyota aims to have more of a JIT supply chain, end to end, when possible.
Current events and recent risks don't invalidate “just in time.” The same principles apply. The ideal is hyper-local suppliers with super-frequent deliveries. If that's not possible, you need more inventory. That's not “hitting the brakes on “just in time” — that's just being reasonable.
See below for some LinkedIn discussion that was prompted by me sharing this article yesterday:
Here is another article, from Bloomberg, about Toyota's practices:
How Toyota Steered Clear of the Chip Shortage Mess
There was already a shortage of semiconductors, then another freak event happened:
“On March 19 the situation got even worse, when a fire broke out at a giant Renesas chip plant in Hitachinaka. The damaged factory, which could take at least 100 days to get back to normal production, accounts for about 6% of global automotive semiconductor output, according to Barclays Plc. Toyota is one of Renesas' largest customers.”
The article describes how visibility and management are the key factors for success in complex supply chains, not more inventory.
“But the Tohoku earthquake's aftermath pushed Toyota to increase flexibility, and the value of inventory Toyota carries has almost doubled since 2011. Speaking at a briefing in February, Toyota Chief Financial Officer Kenta Kon said as part of the company's business continuity plans, it keeps as many as four months of stock for some crucial components such as chips. Toyota didn't expect the semiconductor shortage to disrupt production in the near term, he said.”
JIT, Lean, and TPS don't call for “zero inventory.” It calls for the lowest possible inventory level that keeps production flowing…
Please scroll down (or click) to post a comment. Connect with me on LinkedIn.
Let’s work together to build a culture of continuous improvement and psychological safety. If you're a leader looking to create lasting change—not just projects—I help organizations:
- Engage people at all levels in sustainable improvement
- Shift from fear of mistakes to learning from them
- Apply Lean thinking in practical, people-centered ways
Interested in coaching or a keynote talk? Let’s start a conversation.
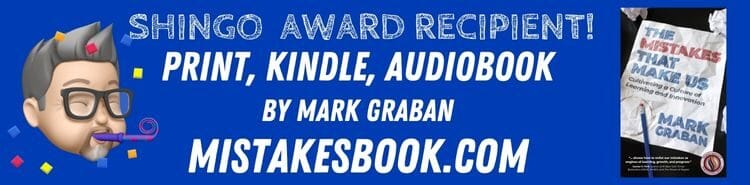
This article, by an MIT senior lecturer, has a better grasp of JIT:
How to Manage your Supply Chain Shock Waves
“Cycle time compression” is key — that leads to lower inventory, but as an END RESULT.
Local suppliers leads to cycle time compression, for example…
Does this count as a retraction or correction from the reporter?
Check out this piece by Jeff Liker, published at the LEI website: