Scroll down for info, videos about Lucid Motors, how to subscribe, and more
My guest for Episode #410 of the Lean Blog Interviews podcast is Keith Champion, Senior Manager ofOperational Excellence at Lucid Motors, a new entrant in the electric vehicle marketplace, with their Lucid Air luxury sedan hitting the market very soon.
Keith worked for Toyota for more than 17 years (thanks to fellow Toyota alum and previous podcast guest Tim Turner for making the connection). As Keith talks about in the episode, he started as a Team Member at Toyota Georgetown, progressing his career to Team Leader, Group Leader, and other roles. He then spent nine years working for Tesla Motors. Keith then joined Lucid in 2019 — BTW, the CEO of Lucid, Peter Rawlinson, was previously Vice President of Vehicle Engineering at Tesla and Chief Engineer of the Model S.
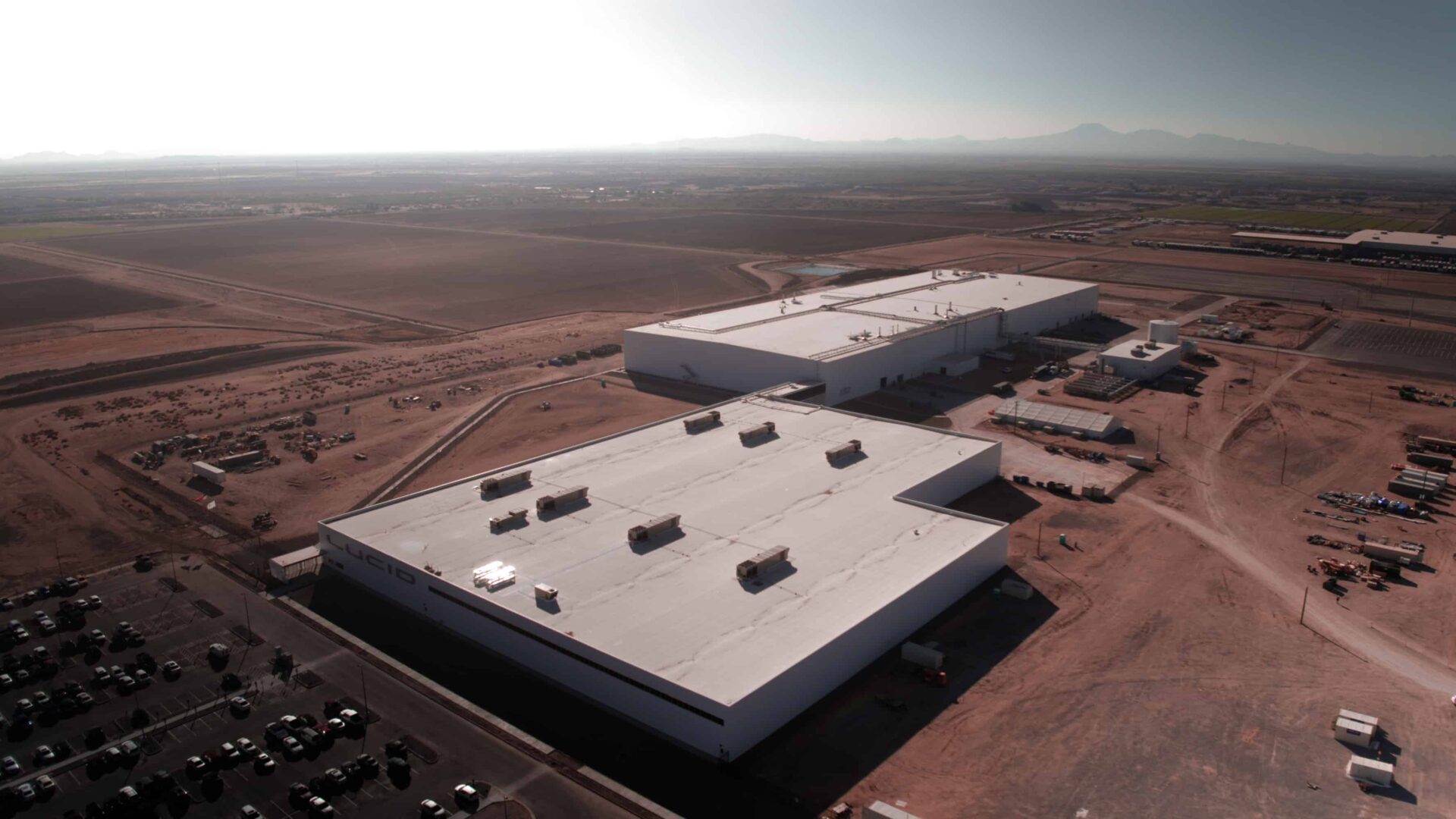
Topics and questions in today's episode (and related links):
- What's your Lean / TPS origin story? It sort of starts before Toyota
- What happens when you “pull the andon cord” at Toyota?
- How is Lucid trying to build the culture right the first time?
- What is the leadership team like at Lucid?
- Is there a management “philosophy” as Toyota might talk about?
- What are the core values of Lucid Motors?
- What's the biggest operations (and supply chain) challenge related to starting a new factory in Arizona?
- How do you build for scalability?
- How important is it to have “built in quality” for a luxury vehicle (or any car)?
- What is an empowering continuous improvement program? Not just suggestions, but implement…
- What are the five key goals and metrics that are used throughout the factory?
- Lucid article (and video) about General Assembly
- A look at the paint shop
The podcast is sponsored by Stiles Associates, now in their 30th year of business. They are the go-to Lean recruiting firm serving the manufacturing, private equity and healthcare industries. Learn more.
This podcast is part of the #LeanCommunicators network.
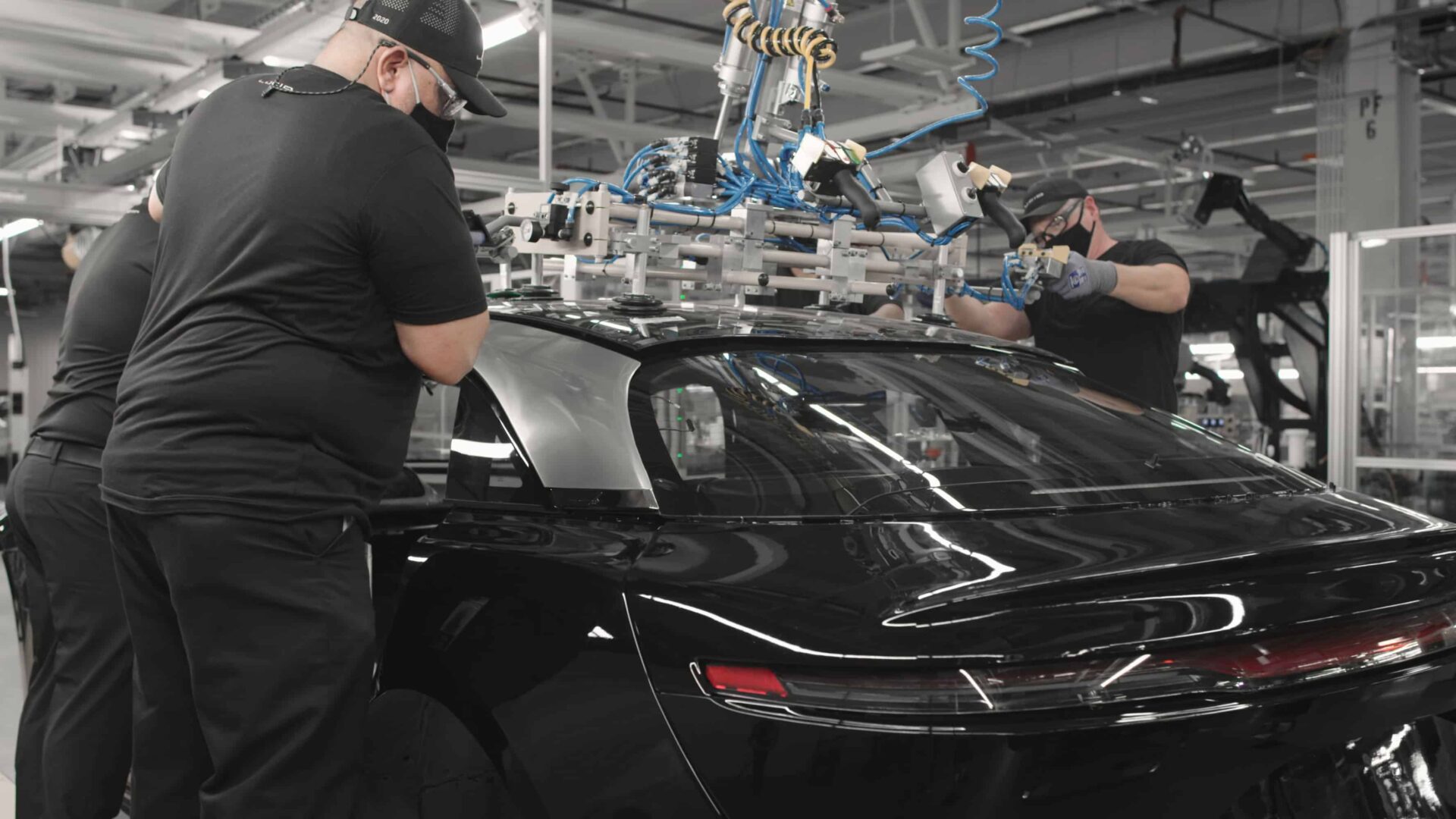
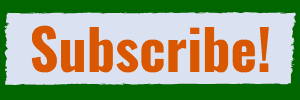
Videos about Lucid Manufacturing and the Lucid Air:
Thanks for listening or watching!
Automated Transcript (May Contain Defects):
This podcast is part of the Lean Communicators network… check it out!

What do you think? Please scroll down (or click) to post a comment. Or please share the post with your thoughts on LinkedIn – and follow me or connect with me there.
Did you like this post? Make sure you don't miss a post or podcast — Subscribe to get notified about posts via email daily or weekly.
Check out my latest book, The Mistakes That Make Us: Cultivating a Culture of Learning and Innovation:
Why was it such a challenge to implement the supply starting a new factory in Arizona?
Because there were probably no auto parts plants (suppliers) in Arizona or anywhere nearby.
If they are emulating the Toyota Production System, then the “just in time” supply chain strategy requires local suppliers who can make frequent deliveries. More importantly, being local means easier collaboration on improvement in quality and cost.
Here’s one article about the Toyota Texas plant in 2009:
https://www.automotivelogistics.media/logistics-challenges-for-toyota-in-texas/22596.article
And a 2004 article about their plants for “on-site” suppliers and the work that went into that (on-site means, often, that they’re in the same building pretty much):
https://www.wardsauto.com/news-analysis/toyota-advances-onsite-suppliers-texas
Here is a piece by Keith about the Lucid Production System on Linkedin: