tl;dr summary: Lean isn't just efficiency… it's safety, quality, delivery, cost, and morale. People often misunderstand that — they don't know or they were taught the wrong things
I often have the opportunity to teach a group of experienced healthcare professionals, from a wide range of disciplines, about Lean. My session is part of a longer professional development program that's framed as “clinical outcomes and patient safety.”
Lean has a lot to contribute to those outcomes, and you can see a collection of results here or here.
Since my last session had to be virtual, due to the pandemic, I took advantage of the opportunity to use some interactive tools from Mentimeter.com. This is something I'll continue doing even when I have the chance to teach in person, as people can vote or give input from their phones, anonymously, while sitting in class.
One question I asked the group was:
What does “Lean” mean to you in terms of improvement?
The word cloud responses showed as this:
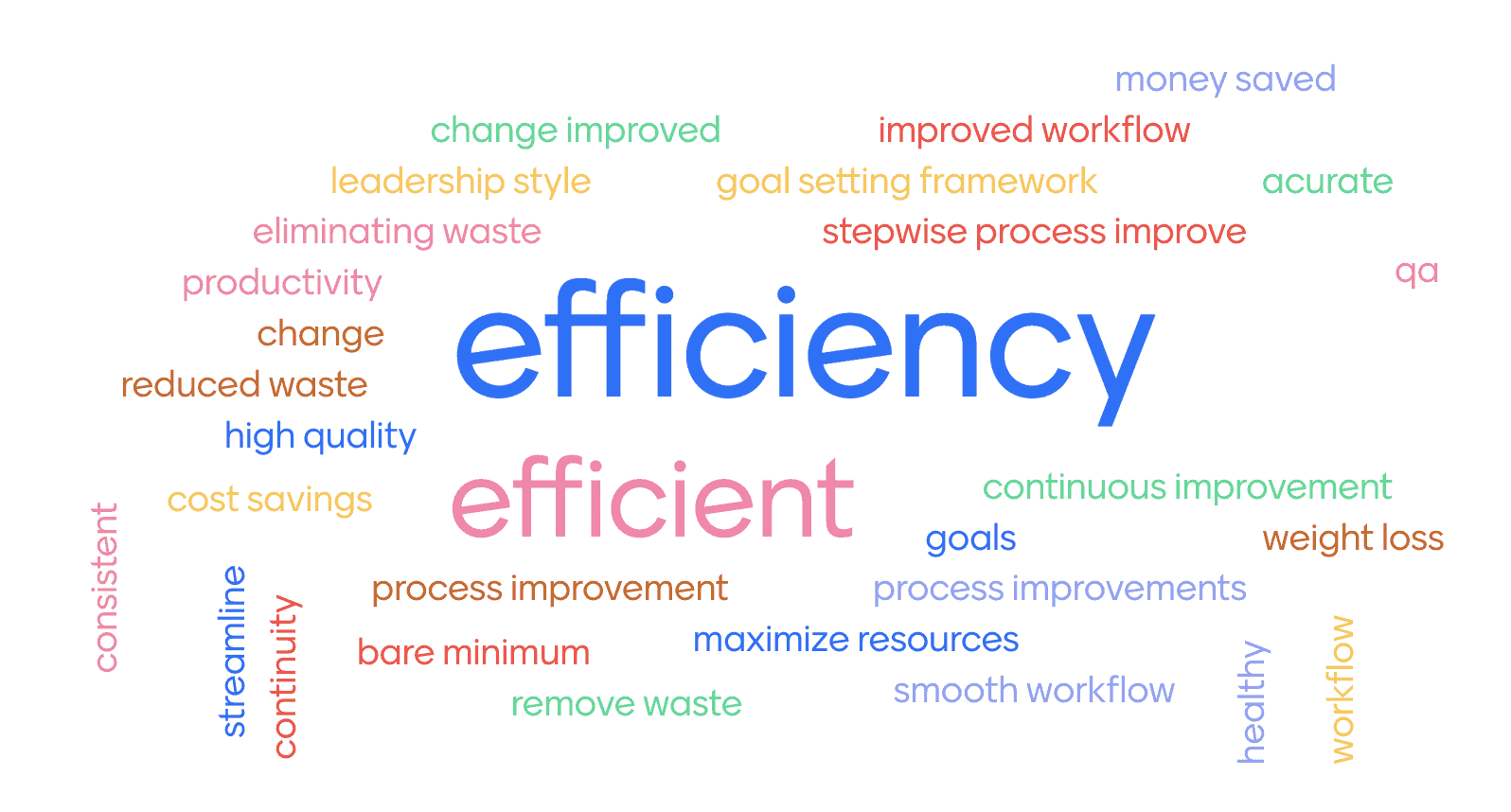
I wasn't too surprised that “efficiency' and “efficient” were the two most commonly entered words (hence the reason why they are biggest in the wordcloud).
Hear Mark read this post — subscribe to Lean Blog Audio
The people in the room worked for a couple of different organizations. Some of the people in the room, which included nurses, physicians, department leaders, etc., work for an organization that “uses” (whatever “uses” means) Lean Six Sigma as a methodology. Some of the participants probably have some knowledge or experience related to Lean… some had at least some experience… and some knew nothing.
Lean Six Sigma education too often shares the incorrect mantra of “Lean is for speed and Six Sigma is for quality.” Or, replace “speed” with “efficiency” or “cost.” I've complained about this before…
So, people in the room could have been repeating the incorrect thing that somebody taught them (“Lean is for speed or efficiency”) or they were guessing based on what they think the word “lean” means.
If you look at the roots and the core of “Lean,” meaning the Toyota Production System, you'll see that they say TPS is about “flow” and “built-in quality.” Quality is by no means the exclusive domain of Six Sigma.
As I've written about before, the goals of Lean / TPS are often stated as:
- Safety
- Quality
- Delivery
- Cost
- Morale
One person, in my wordcloud class survey, did type “qa” (meaning quality assurance), so that's good. Other quality related items included:
- high quality
- acurate [sic]
- consistent
- eliminating waste
- removing waste
Now, talking about “waste” could include, of course, the “waste of defects” as we talk about in Lean frameworks. Not everybody in the class was completely fixated on efficiency, but many did:
- streamline
- money saved
- improved workflow
- workflow
- productivity
- cost savings
Sadly, one person typed “bare minimum.” That's the problem with the word “lean” and the dictionary definitions that talk about scarcity or not having enough resources. I've had people in healthcare say, “We're already lean… we don't have enough resources as it is.”
“Lean” is often used in a very negative way, as we saw back in 2008.
They didn't mean capital-L Lean as in TPS… on the cover, nor did the people who say “we don't have enough.”
Lean / TPS is about having enough resources to do the right work, the right way. That means not having to cut corners or make compromises on safety or quality. It's about the RIGHT amount of resources, including people (and I hate calling people “resources” — sorry).
Some others in the class were on the right track about Lean:
- leadership style (and I wish somebody had said “culture”)
- stepwise process improvement (although I'll add that sometimes we make step-function changes by redesigning processes completely)
I can't blame the individuals in the session for responding the way they did. It goes to show how much more work is required to educate people in healthcare. And it also illustrates how some people are taught the wrong things and that can be difficult to recover from.
“It's Easier to Fool People Than It Is to Convince Them That They Have Been Fooled.”
Mark Twain
What do you think? Please scroll down (or click) to post a comment. Or please share the post with your thoughts on LinkedIn – and follow me or connect with me there.
Did you like this post? Make sure you don't miss a post or podcast — Subscribe to get notified about posts via email daily or weekly.
Check out my latest book, The Mistakes That Make Us: Cultivating a Culture of Learning and Innovation:
Hey Mark! I really enjoyed this article. Like you said, there are a lot of words that we can think of as lean. Some of the ones you mentioned (especially efficiency) are words that usually pop into my mind when I think of lean. Now that I have taken supply chain classes for a while, I have truly improved my knowledge of what Lean Six Sigma actually is, but when I first started out I definitely think I was one of those people who had that incorrect mantra. Lean has a lot of factors that go into it, but it mainly means to have the right amount of resources to do work the right way. I think all people should be taught about lean principles, especially like you said those in healthcare. I believe it can truly enhance process improvement. Thanks for sharing!
Hi Mark:
I enjoyed this article very much. The terminology associated with “Lean” business has been very prevalent to me as a major in supply chain – I especially relate to the word chart showing the wide range of defining characteristics of lean management (I do agree that effectiveness/efficiency are key factors). Thanks for the information!