Thanks as always to Ryan McCormack for this… there's always so much good reading, listening, and viewing shared here by him!
2020 was an unusual year. As much as I look forward to seeing it in the rearview mirror, I also realize adversity and change is a formidable teacher. I learned a lot this year, and I hope some of you learned from some of the stories I offer up every two weeks. Thank you.
Here are the 10 most clicked links, in descending order, from 2020:
1. Virus forcing rethink of Japanese way of business at Toyota, CEO says. One of the ways Toyota continually improves is to question assumptions, even of deeply engrained traditional practices like genchi genbutsu (“go and see for yourself”). Covid-19 has forced many to rethink how they operate and lead, but does it require a global pandemic to ask these questions? Hopefully, 2021 brings in a renewed commitment to ask questions and challenge our assumptions.
2. Continuous Improvement: Ever Forward. Many practitioners get into quality or continuous improvement because we want to contribute to progress. But over time, many well-intentioned practitioners get discouraged by a lack of support from leaders. “Don't begin an effort with the hope that things will work out. Only commit to do those things that the leadership is going to put their time and effort behind for week after week, month after month, year after year.” Wise words from John Hunter (curiouscat.com). What are you or your leaders committed to in 2021?
3. How to spot an agile faker. When agile or lean is a program or fad that your organization is “implementing”, it often becomes another box to check for leaders and team members. Look for those going through the motions, checking the box, and focusing on output to spot the fakers. How will we avoid fake lean or fake agile in 2021?
4. Responding to Crisis at Virginia Mason. Another benefit of a robust lean management system is its ability to foster agile responses to new problems, or in this case, a global pandemic. Virginia Mason leveraged its internal problem solving capabilities and nimble communication processes to respond quickly to the evolving conditions of Covid-19. How can you better develop a lean management system to respond to crises?
5. How to Communicate Standards to People Who Hate Being Told What to Do. Simply telling or emailing the new standard is not sufficient to create understanding or compliance, yet it persists as a dominant form of training and communication in organizations. Leaders must do better to respect individual learning styles. How can you do better for your team in 2021?
6. A Higher Purpose Brings a Higher Culture. Most people want to spend their time making a difference and contributing to a purpose bigger than themselves. Organizations and leaders have a responsibility to connect work to purpose, beyond the tasks and hamster wheels of day-to-day operations. How will you connect your team's work to purpose in 2021?
7. Us and Them. If you want to assess how well your organization engages employees, listen to how often “they” is said. How can you improve inclusiveness and engagement in your team in 2021?
8. Strategy deployment: from cascade to translation to synchronization. At the beginning of the year, most organizations go through goal-setting and cascading, hoping that the message is easily and readily shipped down to every leader and staff member. Technically from 2019, Jason Yip challenges this thinking and encourages an ongoing process of synchronization throughout the year. How can you better synchronize your team's performance to the organization's directions in 2021?
9. Bullet Journals Are a Simple And Effective Way to Be Kind To Yourself. Obsession over being productive can make us feel guilty when we don't feel like we did enough. A bullet journal is a simple habit to help demonstrate that we do a lot in a day. Be kind to yourself. What habits will you adopt to be kinder to yourself in 2021?
10. (tie) So You Want to Transform a 100 Year-Old Institution. Transformation is hard. It can be even harder in large and long-standing organizations. Here are some tips to help you navigate leading improvement in institutions and help reduce discouragement.
10. (tie) Performance Measurement Metaphors to Get People Engaged. Many people aren't moved or compelled by graphs and data. Stacey Barr shares some metaphors that can be used to help create better understanding of performance measurement. How can you use metaphors to help engage teams in performance measurement in 2021?
2020 was a challenging year for everyone. I want to extend a special thanks and gratitude to those who directly and indirectly support healthcare delivery during these challenging conditions. Thank you for all that you do.
2020 has taught us how resilient, resourceful, and adaptable people are. As leaders of improvement, this is an important reminder that our people can do remarkable things when required to. Please continue to challenge yourself and your teams to be better and kinder.
Happy Holidays and Happy New Year,
Ryan
Follow Ryan & Subscribe:
LinkedIn: https://www.linkedin.com/in/rjmccormack/
Subscribe to receive these via email
Please scroll down (or click) to post a comment. Connect with me on LinkedIn.
Let’s work together to build a culture of continuous improvement and psychological safety. If you're a leader looking to create lasting change—not just projects—I help organizations:
- Engage people at all levels in sustainable improvement
- Shift from fear of mistakes to learning from them
- Apply Lean thinking in practical, people-centered ways
Interested in coaching or a keynote talk? Let’s start a conversation.
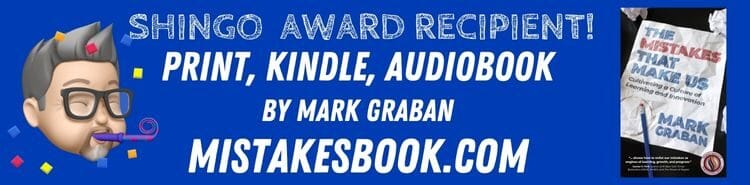