Monday was the first day of my fifth Lean study trip to Japan. Yesterday, I had the opportunity to once again visit a Toyota plant, the Tsutsumi Plant.
Here are two blog posts from 2015, as the plant tour was very much the same… but the visitor center / museum has changed.
I always enjoy revisiting a factory, although the Toyota tours are always a bit of a blur. There's a lot to see in a short time with a large group.
Part of the visit is the chance to visit the Toyota Kaikan Museum. This is separate from the Toyota Technology Museum in Nagoya, which I've also blogged about before. I'll have the chance to visit that museum again on Thursday as part of our formal Kaizen Institute trip.
In the museum — and during the tour — there was a strong emphasis placed on making things and developing people.
These two ideas go hand in hand, as shown in this display:
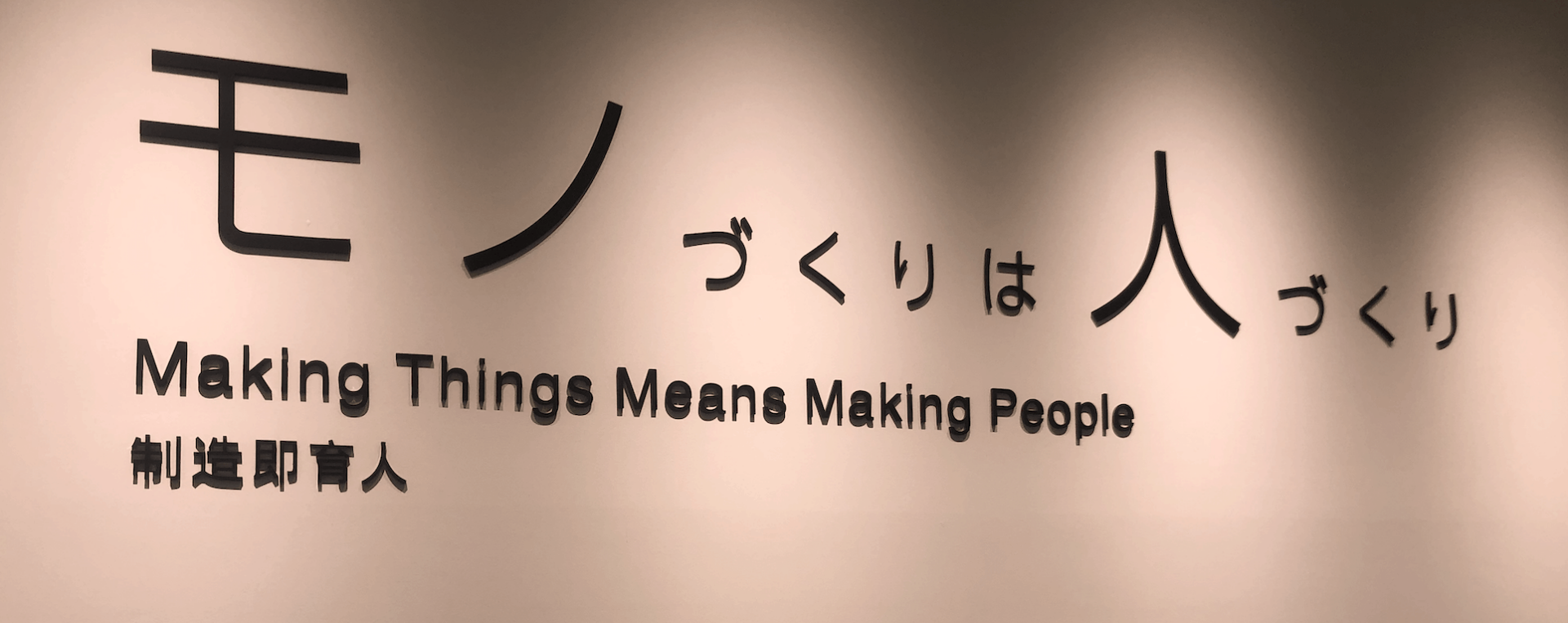
There are many references to the idea of robots and automation assisting and supporting the people who do the work.
Our guide said that Toyota values people and maintains jobs due to the benefit to society — and the sense of obligation they have for this. They're not just maximizing short-term profits like many companies (and hospitals) do, sadly, through layoffs.
Here is another display that references the idea of a training “dojo” (a concept I talked to Joel Tosi and Dion Stewart about in a recent podcast).
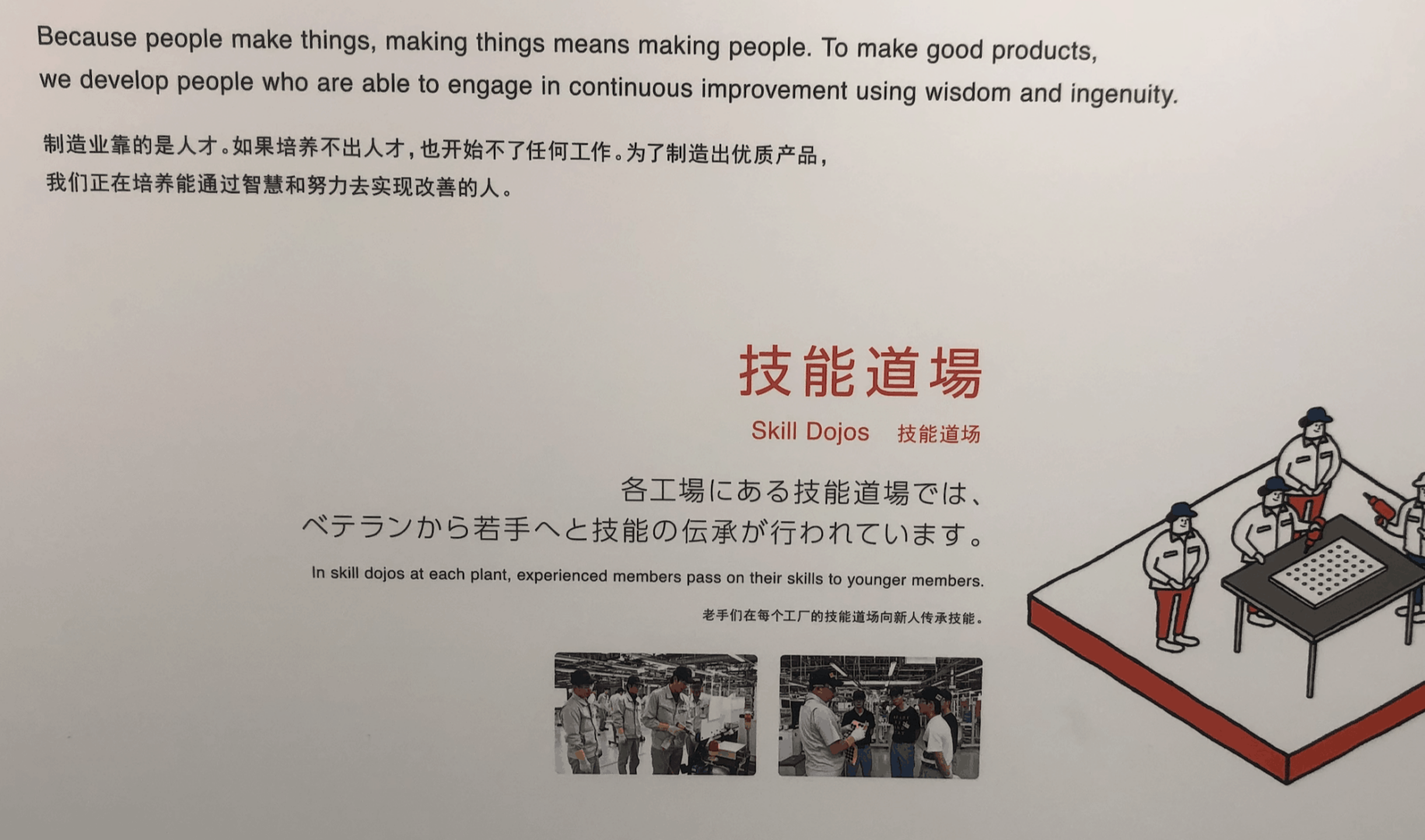
“Because people make things, making things means making people. To make good products, we develop people who are able to engage in continuous improvement using wisdom and ingenuity.”
By the “dojo,” it says:
“In skill dojos at each plant, experienced members pass on their skills to younger members.”
One of the healthcare professionals who is here on the tour, asked how a new team member (or somebody in a new role) might slow down production. Doing offline training and practice seems like one countermeasure to mitigate some of that problem.
Toyota also engages people in “Quality Circle” activities (something that's still common in Japan, as I've blogged about).
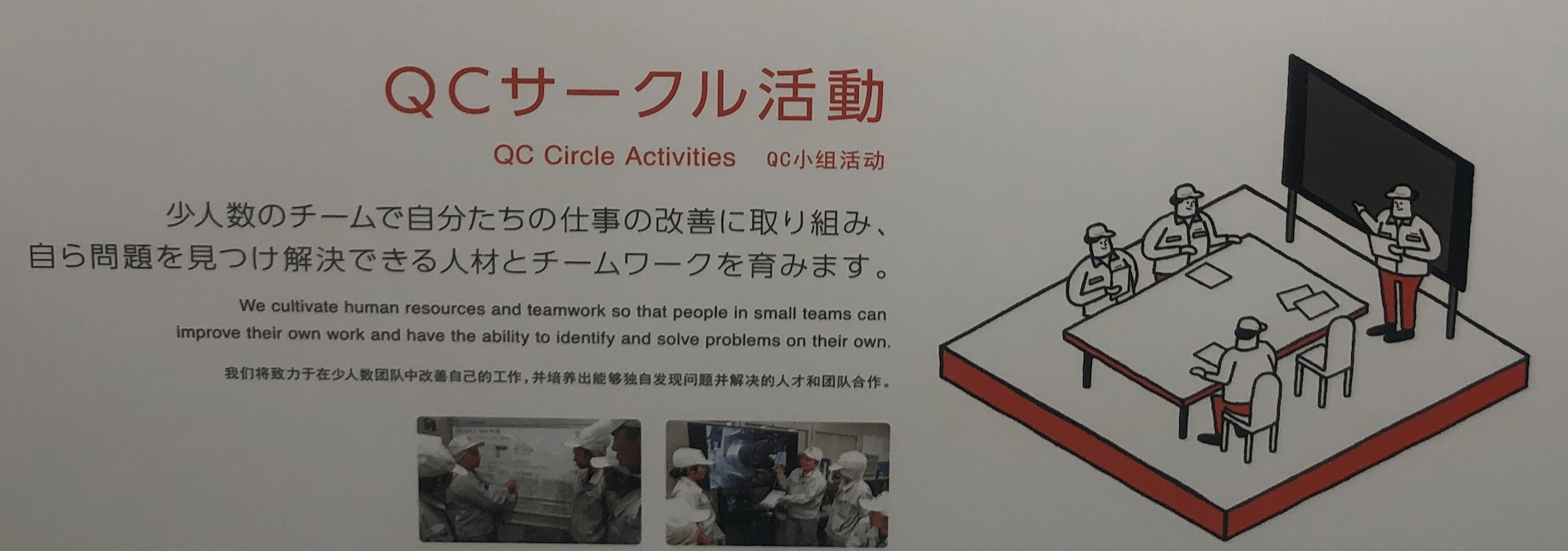
“We cultivate human resources and teamwork so people in small teams can improve their own work and have the ability to identify and solve problems on their own.”
They still also have the “Toyota Creative Ideas and Suggestion System” for smaller Kaizen opportunities that don't require a formal team. See a video about this:
In this illustration of Toyota's strategy and vision, you can see that “engaging talent & passion of people” is pretty prominent. The display also talked about “the spirit of making things” that is strong at Toyota.
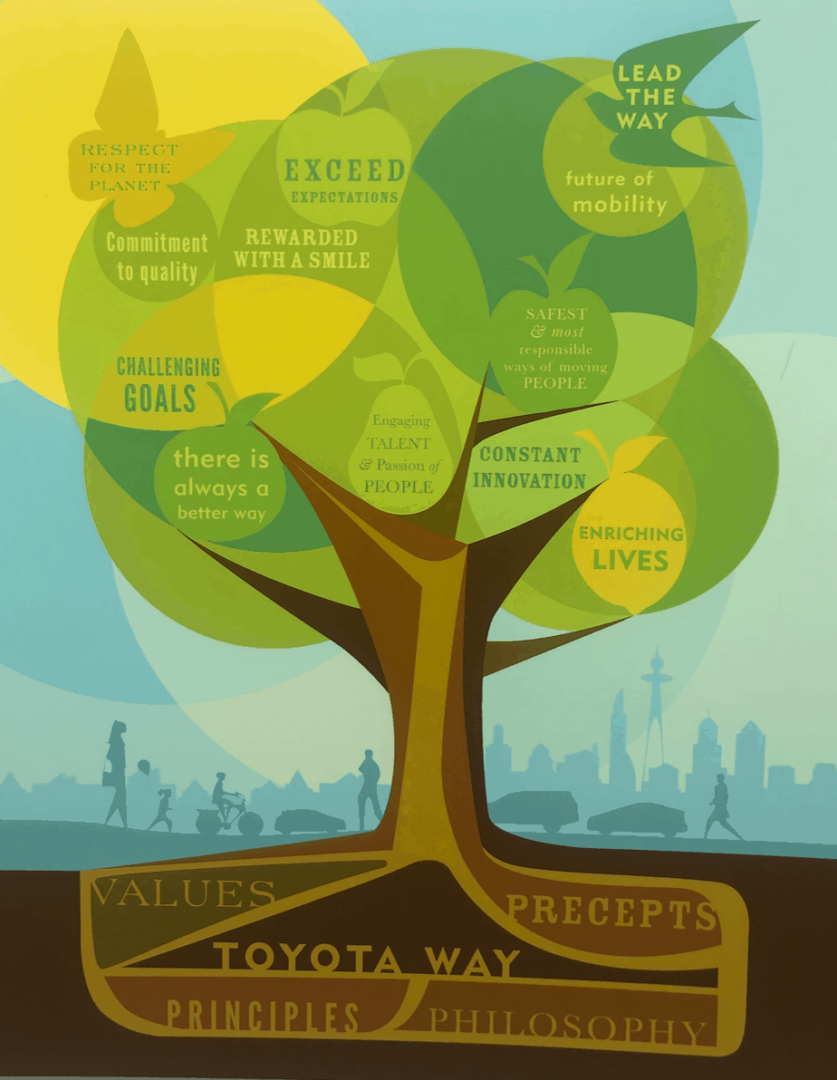
Here is a page from a Toyota company profile book:
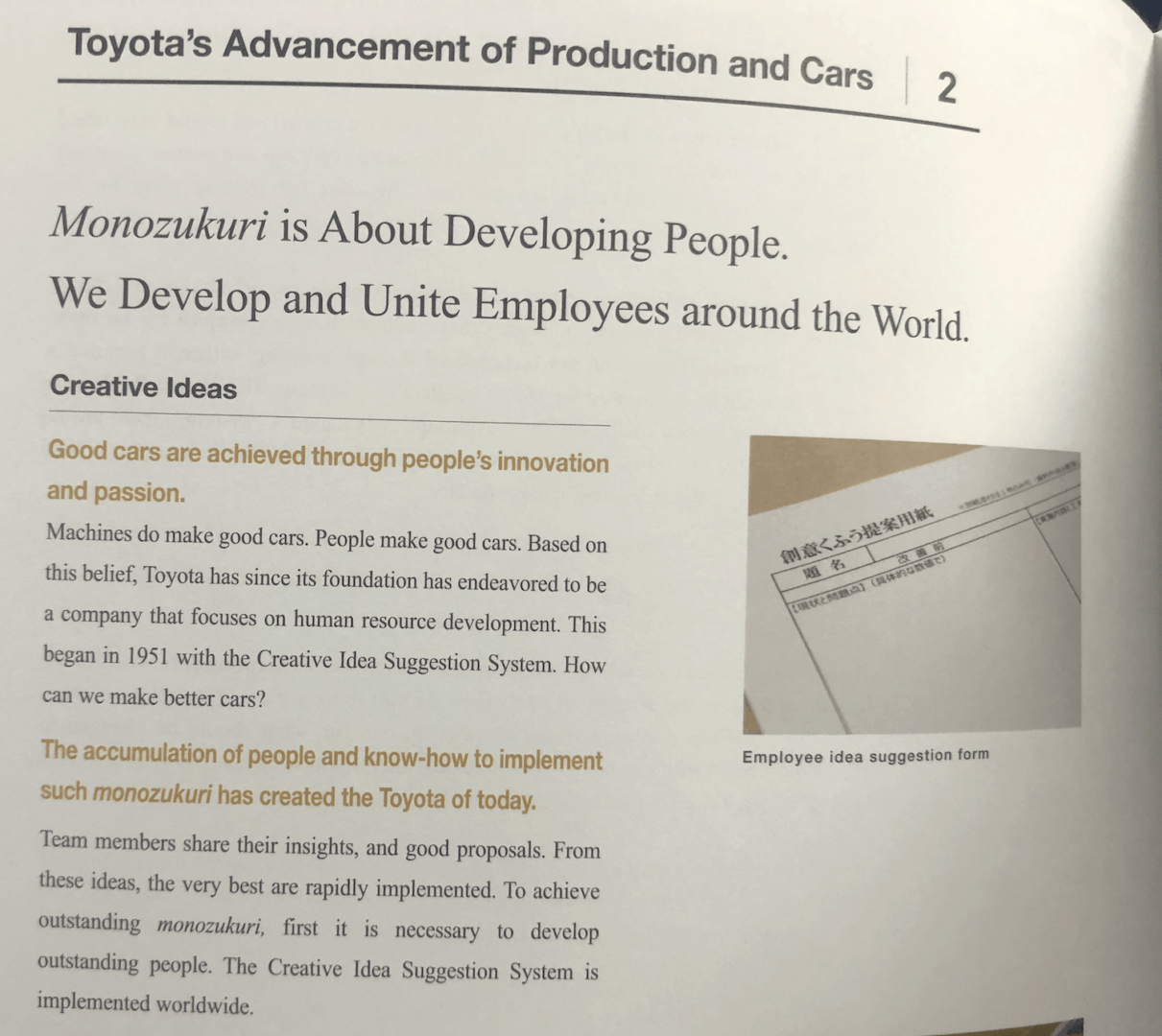
“Good cars are achieved through people's innovation and passsion.”
The tour guide said that over 600,000 Kaizen ideas are implemented across Toyota Japan each year, including some related to tours:
So what's the connection to Mr. Rogers? I recently stumbled across this page that has videos from the Mr. Rogers' Neighborhood show… virtual factory tours to learn how people make things.
Watch one of these as a moment of zen if you need it during a busy or stressful day:
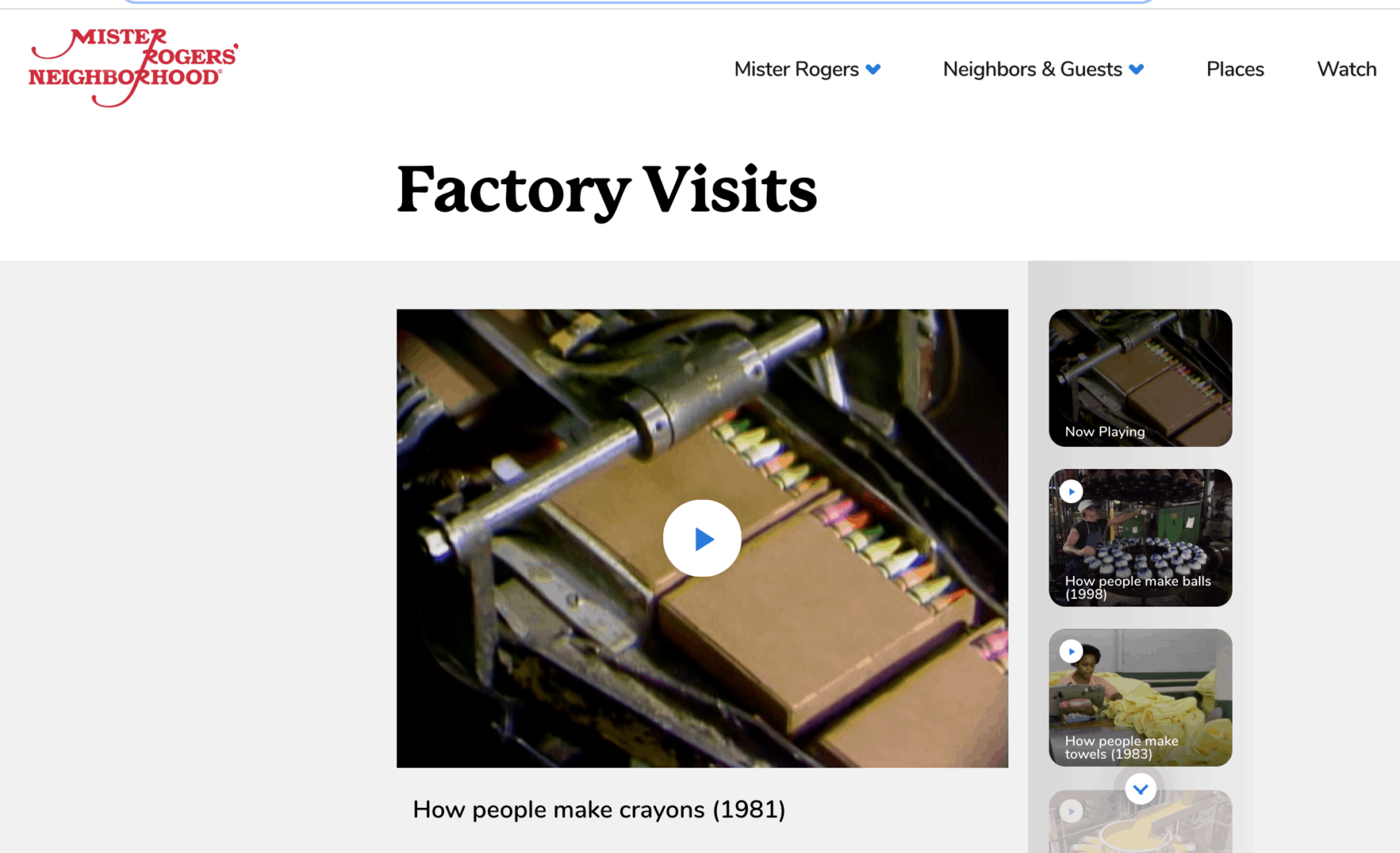
Mr. Rogers is all about “respect for people,” right? Even when the process involves automation, the focus is always on “How people make…” since people do invent automation, after all. And, people work alongside automation, as we see at Toyota.
You can also see the videos on YouTube, it seems.
From the site:
“How people make things” – that's how Mister Rogers refers to the factory visits. He wants to remind children that it's people who make things, not just machines.
Fred Rogers also talks about “pride in work,” which reminds me of W. Edwards Deming, as well:
“My father and my two grandfathers worked in factories, and I was always interested in their work. When we show factories, they certainly have fascinating machines, but I always emphasize that it takes people to make machines and to make them work. I like children to know that people can take pride in their work and that everyone's job is important.”
I think a truly Lean organization has that sense of respect for each individual — that everyone's job is important and contributes to our goals.
Oh, and Mr. Rogers changes his shoes when he comes inside, which is pretty common here in Japan :-)
Please scroll down (or click) to post a comment. Connect with me on LinkedIn.
Let’s work together to build a culture of continuous improvement and psychological safety. If you're a leader looking to create lasting change—not just projects—I help organizations:
- Engage people at all levels in sustainable improvement
- Shift from fear of mistakes to learning from them
- Apply Lean thinking in practical, people-centered ways
Interested in coaching or a keynote talk? Let’s start a conversation.
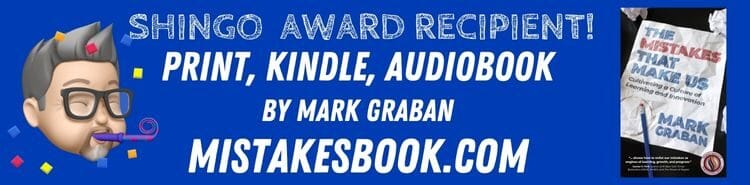
He says the real problem with making toys in the U.S is this: People expect things to be cheap. When the toy factory closed, people were only willing to pay around 99 cents for the basic ball. That’s less than people paid for the same ball in 1967. Braeunig says he just can’t make products for that price here anymore. There is a factory using the same process and the same space Mr. Rogers saw in 1985. It’s in Oak Park, Ill.