Here is something brief that I posted on LinkedIn while I was in Japan recently, but I also wanted to share it here, elaborating a bit.
In my visits to Japan, I have learned that not every company here utilizes TPS, Lean, Kaizen, or TQM. It's not the default and it's not easier if you're Japanese, as some people think.
One company I visited this week said:
“We were not always a Kaizen company.”
That might surprise some readers.
Kaizen isn't the default. It's been a specific effort they've been making the past few years.
Their new-found emphasis on engaging employees in continuous improvement fame from a new CEO who came from Toyota.
Leadership matters. Leadership is critically important.
The photo below, by the way, is from a manufacturing company that has practiced Kaizen for more than four years. The binders are full of single-page summaries of the Kaizen improvements.

Paraphrasing Mitt Romney, we have binders full of Kaizens!
Here is what one of those Kaizens looks like, along with an automated translation was done via the Google Translate on my iPhone:
Original Japanese Automated Translation
This is a similar format as what I've used in different organizations, something that I've called a “Kaizen Report” or a “Kaizen Summary,” as we've documented in Healthcare Kaizen (and you can find templates like this on our book's website).
Tour participants loved flipping through the binders… even without understanding Japanese, the photos help you get a sense of the types of small improvements that are being made so frequently. I don't have an exact count of how many Kaizens have been documented.
Here is another blog post, from my first visit in 2012, on the theme of “this isn't easier in Japan”:
Lean, TPS, Kaizen, TQM… these aren't magically the default way of being for a Japanese company. It requires effort and dedication…
See more posts about Japan trips and my lessons learned.
Here is the original LinkedIn post with a lot of great comments and discussion:
Please scroll down (or click) to post a comment. Connect with me on LinkedIn.
Let’s work together to build a culture of continuous improvement and psychological safety. If you're a leader looking to create lasting change—not just projects—I help organizations:
- Engage people at all levels in sustainable improvement
- Shift from fear of mistakes to learning from them
- Apply Lean thinking in practical, people-centered ways
Interested in coaching or a keynote talk? Let’s start a conversation.
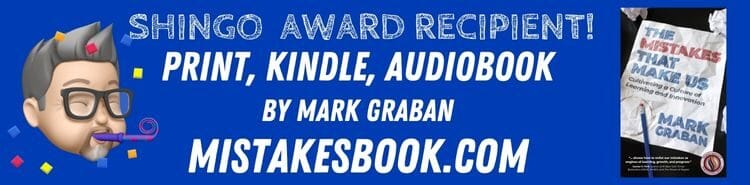
Interesting article, Mark! If the companies you visited don’t admit that they’re not TPS, Lean, Kaizen or TQM, then what do they call themselves in the context of business or operational excellence?
Ray –
I’m not sure if I understand your question. All of the companies I visited say they are using TPS, Lean, TQM, Kaizen and or all of the above.
But the one I’m referencing here would probably say they had no form of operational excellence approach before they started with Kaizen.
Mark