Kim Hollon is CEO and President at Signature Healthcare. I don't know him well, but I've heard a lot of great things about him and his leadership from a friend who used to do Lean work at Signature.
I did some Lean training for the organization about 10 years ago when I was full time with the Lean Enterprise Institute — but I can't remember if that was right when Kim took the job or right before. Edit – He was already there when I did the training session, as he reminded me during the podcast we recorded (coming soon).
Kim recently shared a post on LinkedIn that pointed to an excellent article that he wrote in “Health Progress” — the journal of the Catholic Health Association of the U.S.
Here is the article:
“The Health Care Leader's Role in Safety“
I appreciate his humility in saying, after being in senior leadership roles for over 30 years:
“I know from experience that if I had known years ago what I do now, lives could have been saved and suffering avoided.”
In his most recent role:
“When I had the opportunity to join and lead Massachusetts-based Signature Healthcare, I took to heart the philosophy of Lean, a well-known management approach, and began a comprehensive transformation of our strategic planning, daily operating systems, communication, process improvement, inventory management and human resource systems.”
Kim writes that many organizations look at Lean as a set of tools, or they limit it to “process improvement,” but he wanted to make Lean an organzation-wide approach and philosophy. What does this mean? In part…
“So, we started shift-related daily huddles, transparent public posting of our departmental goals, performance metrics, workplace standardization, a standard problem-solving method to determine the root cause and counter measures, a suggestion system, and a monthly meeting process.”
Kim realizes that Lean is about leadership and that leaders have to participate — they have to lead by example.
Lean leadership concepts and principles might seem easy, but “unlearning” or relearning something new can be really difficult when you have decades of old habits.
“Relearning how to lead after 30 years of success was difficult for me and all of our team.”
It's a challenge… and people will naturally push back when presented with something new, but Kim said:
“I responded that as long as any of our patients received less than perfect care, we had a moral obligation to change how we managed, making it easier for our staff to reach zero harm.”
And what sorts of results are they seeing?
“To my surprise, we reduced our serious patient safety events by over 80% and have maintained that level of improvement for over three years. Experiencing that dramatic decline in harm affirmed what I was beginning to understand — that implementing a culture of safety and robust process improvement are both necessary to reach zero harm. If anyone had told me 10 years ago that we could reduce our serious safety events by 80% I would not have believed it, because I had no mental model of how different an organization could be.“
There are a lot of great insights and reflections in the article, so I'd encourage you to please click over and read it.
I'll be recording a podcast with Kim soon to talk about the article and more of his thoughts on leadership, Lean, systems, and patient harm.
Please scroll down (or click) to post a comment. Connect with me on LinkedIn.
Let’s work together to build a culture of continuous improvement and psychological safety. If you're a leader looking to create lasting change—not just projects—I help organizations:
- Engage people at all levels in sustainable improvement
- Shift from fear of mistakes to learning from them
- Apply Lean thinking in practical, people-centered ways
Interested in coaching or a keynote talk? Let’s start a conversation.
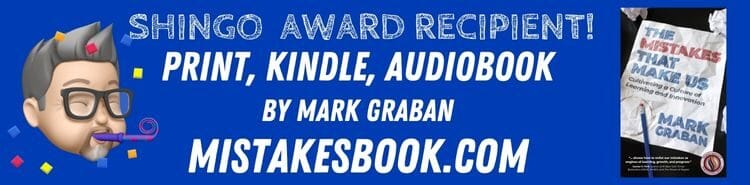