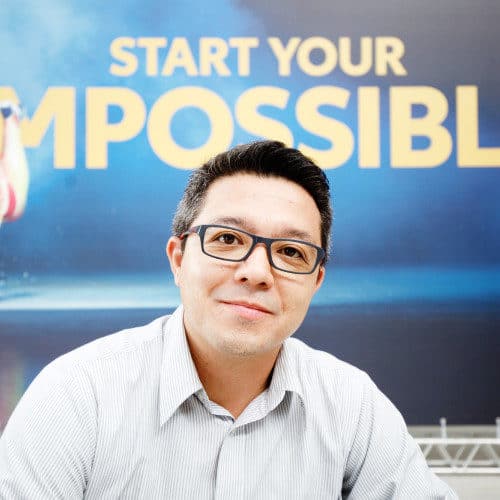
When I was in Brazil recently (read more), one of the presenters at the Lean Six Sigma Conference was Bruno Kosima, pictured at left. He is the department chief of the Latin American / Caribbean group that teaches the Toyota Production System — a group called OMDD or the Operations Management Development Division. Bruno has a similar role as Jamie Bonini does in the U.S.
During his talk, Bruno shared an amazing video that shows how he and Toyota helped improve care in a São Paolo hospital (the video has English subtitles):
The video starts by talking about:
- Quality
- Efficiency
- Productivity
as things associated with Toyota cars and the way they work.
It says Toyota has been engaged for 70 years in “improving and enhancing our processes” so that the brand “is always linked to quality.”
The Toyota Production System is “followed by all of us at Toyota.” TPS is “based on the philosophy of completely eliminating all waste in production processes.”
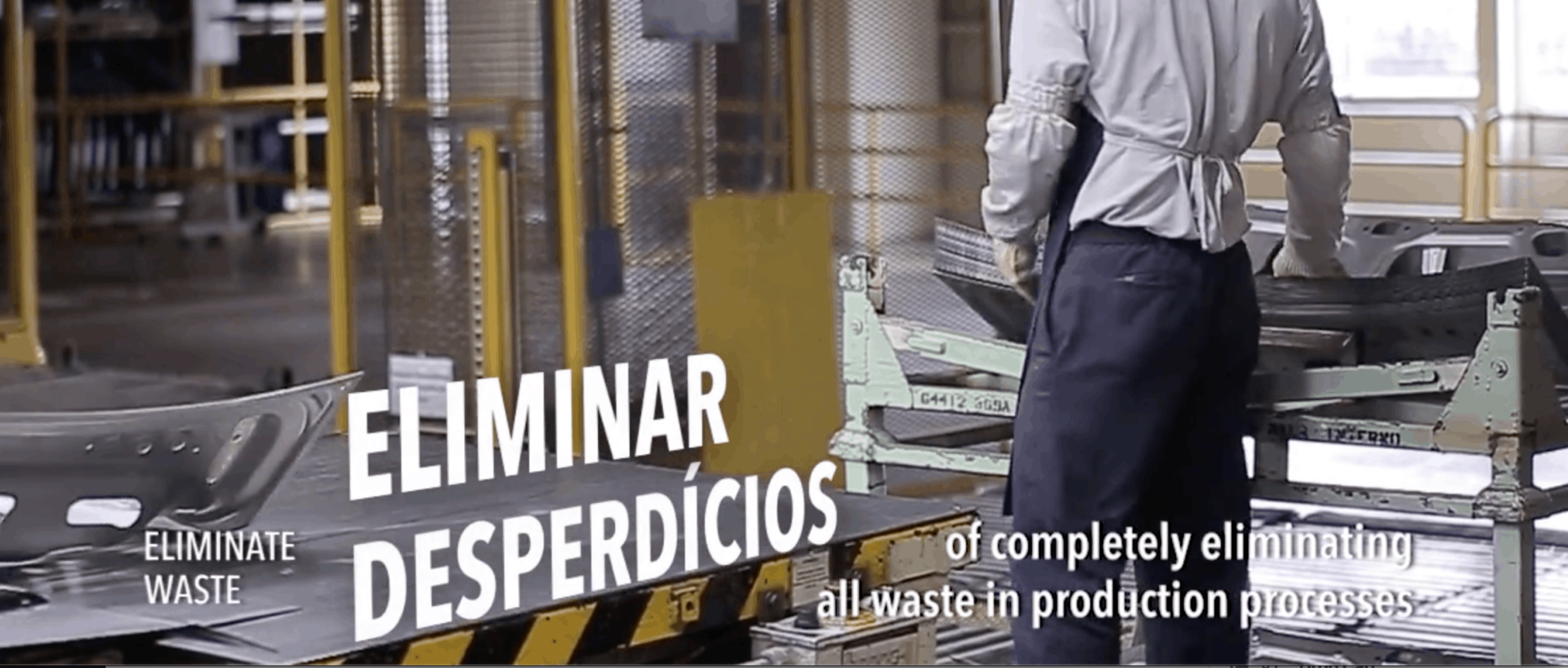
That's their aim, but nobody (including Toyota) has completely waste-free processes, but they are “constantly striving for the most efficient method.”
The video talks about aiming for “effectiveness” by eliminating the seven types of waste, as shown below in Portuguese (and if you're familiar with the types of waste, you can tell what they are from the graphics).
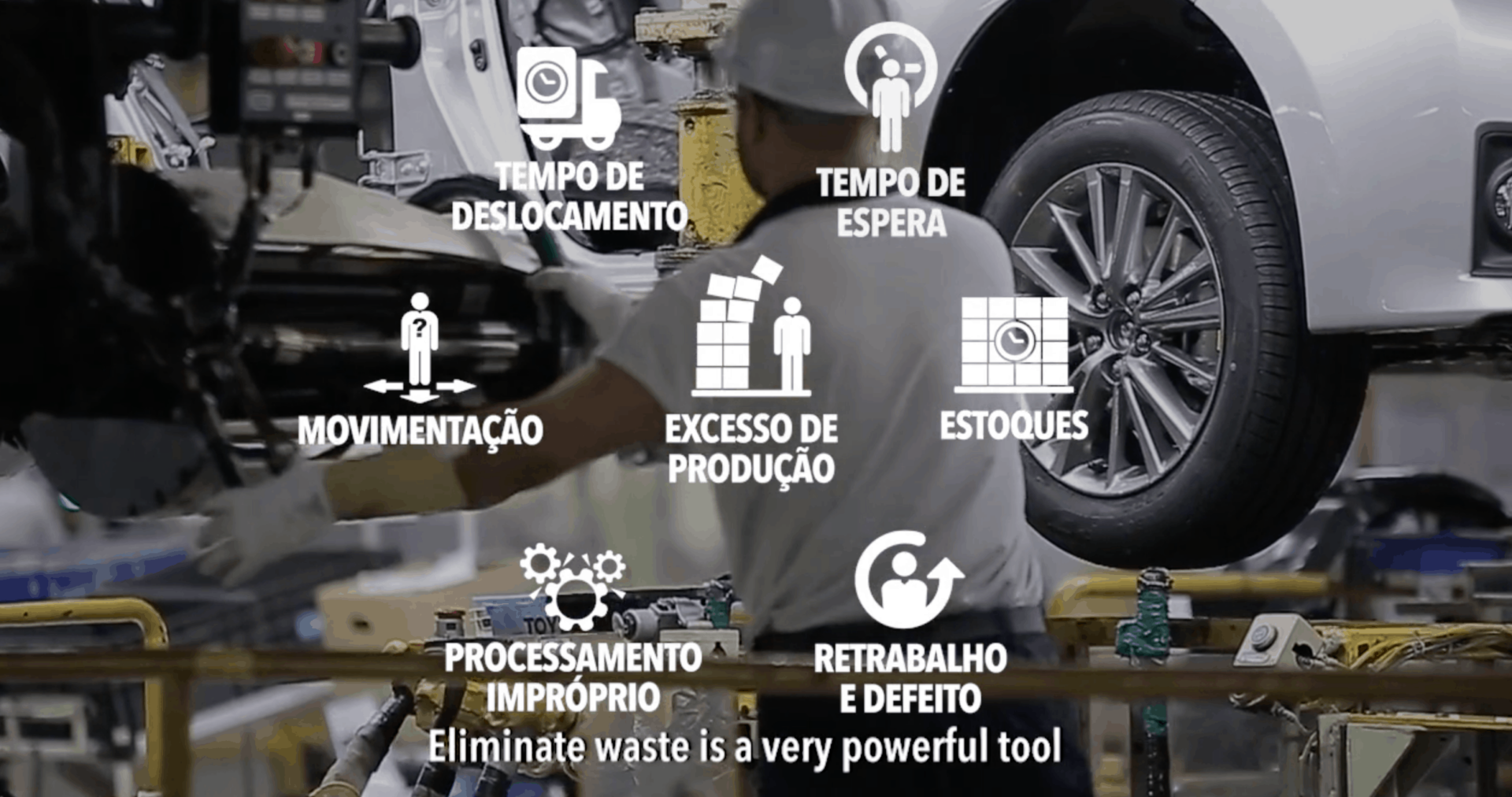
It's interesting that Toyota doesn't mention what many of us call the “eighth type of waste” — the waste of not fully utilizing human potential (read more about waste here).
I'm guessing that Toyota assumes that team members are going to be engaged in improvement. They focus on developing people through Kaizen. So maybe this waste isn't even worth mentioning in this context?
Bruno Kosima does work that's similar to the TSSC group in North America, working with other organizations to learn and practice TPS. See blog posts about TSSC and their work.
Bruno says, via the subtitles:
“With the success of the use of the TPS on a day to day basis at Toyota, we realized that the system can collaborate with the development of society in general. The pursuit of continuous improvement can be used to improve working methods in any activity.”
The division he leads was created to “maintain the essence of the TPS and to apply it in other companies” and organizations.
The example they share in the video is from a hospital in São Paolo, the Santa Cruz Hospital.
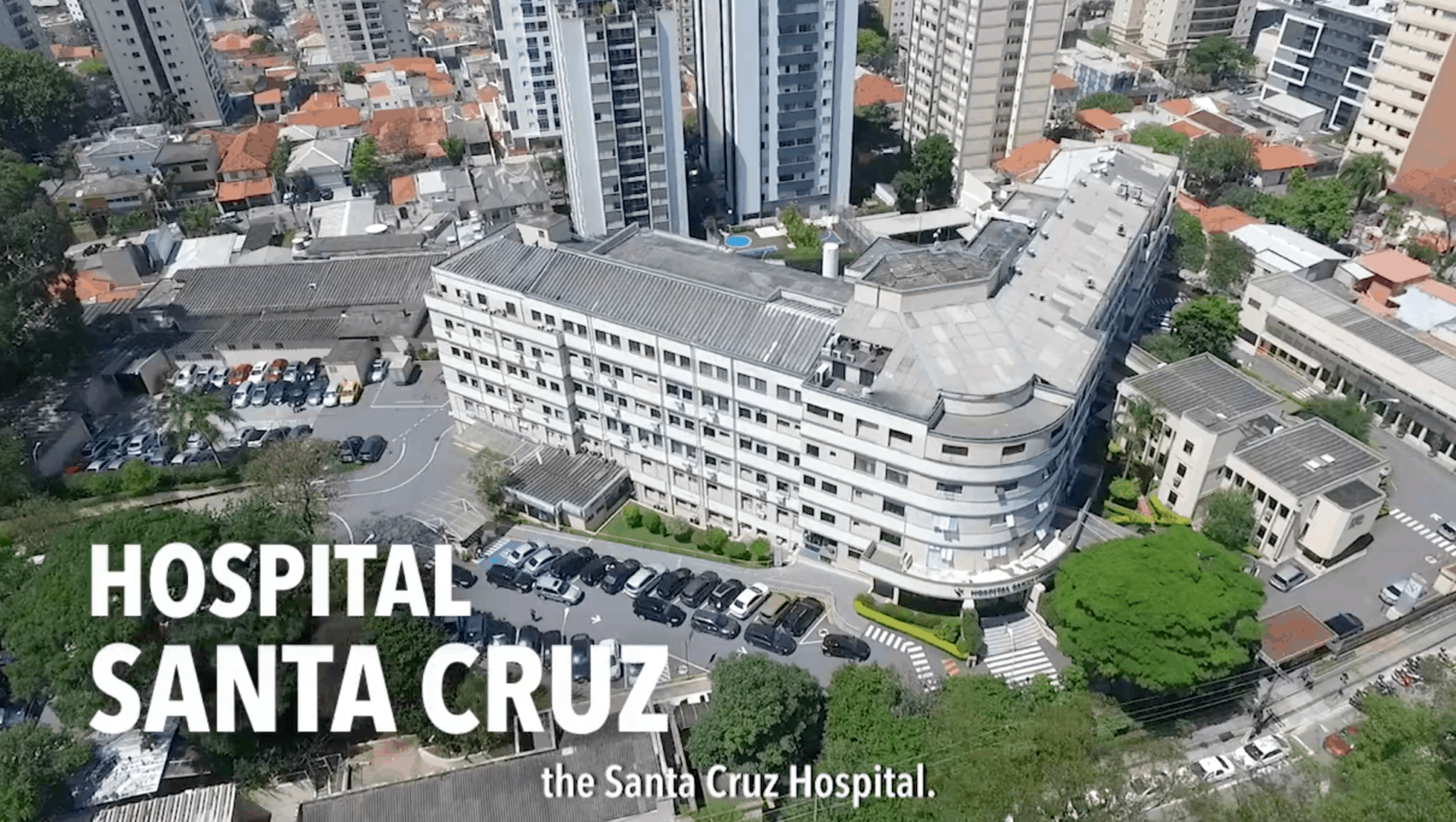
Toyota identified, together with the hospital, that the “ideal” place to start was in Emergency care “because it was a complex” area “that needed more agility.”
A supervisor in the Emergency area said:
“Our aim is to be searching for changes, new concepts to reduce time, gain agility, quality, and safety in the service that is provided to our client.
To me, good Lean work should follow this ideal of TPS — focusing not just on flow and efficiency, but also on safety and quality (and safety should come first).
Studying the Work, Respectfully
Toyota helped the hospital analyze the layout and the workflows to “identify unnecessary efforts and wastes.”
Yeah, those are the stereotypical tools of my field (Industrial Engineering) — a stopwatch and a clipboard.
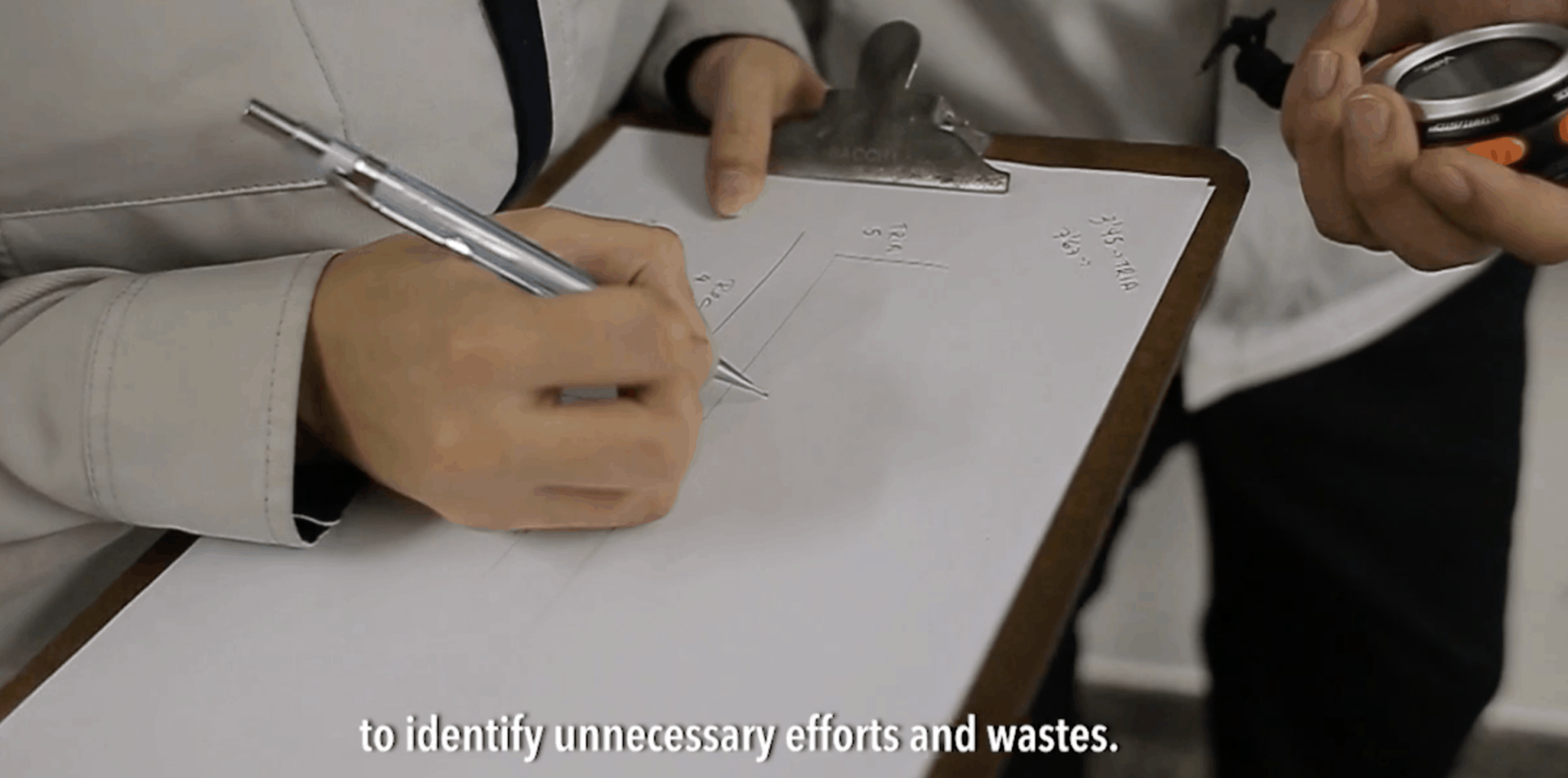
Time and work study can (and MUST) be done in a way that's respectful to those who do the work — and I'm sure Toyota does that. I've blogged about this before.
Later in the video, it talks about the collaboration and engagement:
“The great results we achieved would not be possible without the complete integration between [the Toyota team] and the hospital staff.” — as pictured below:
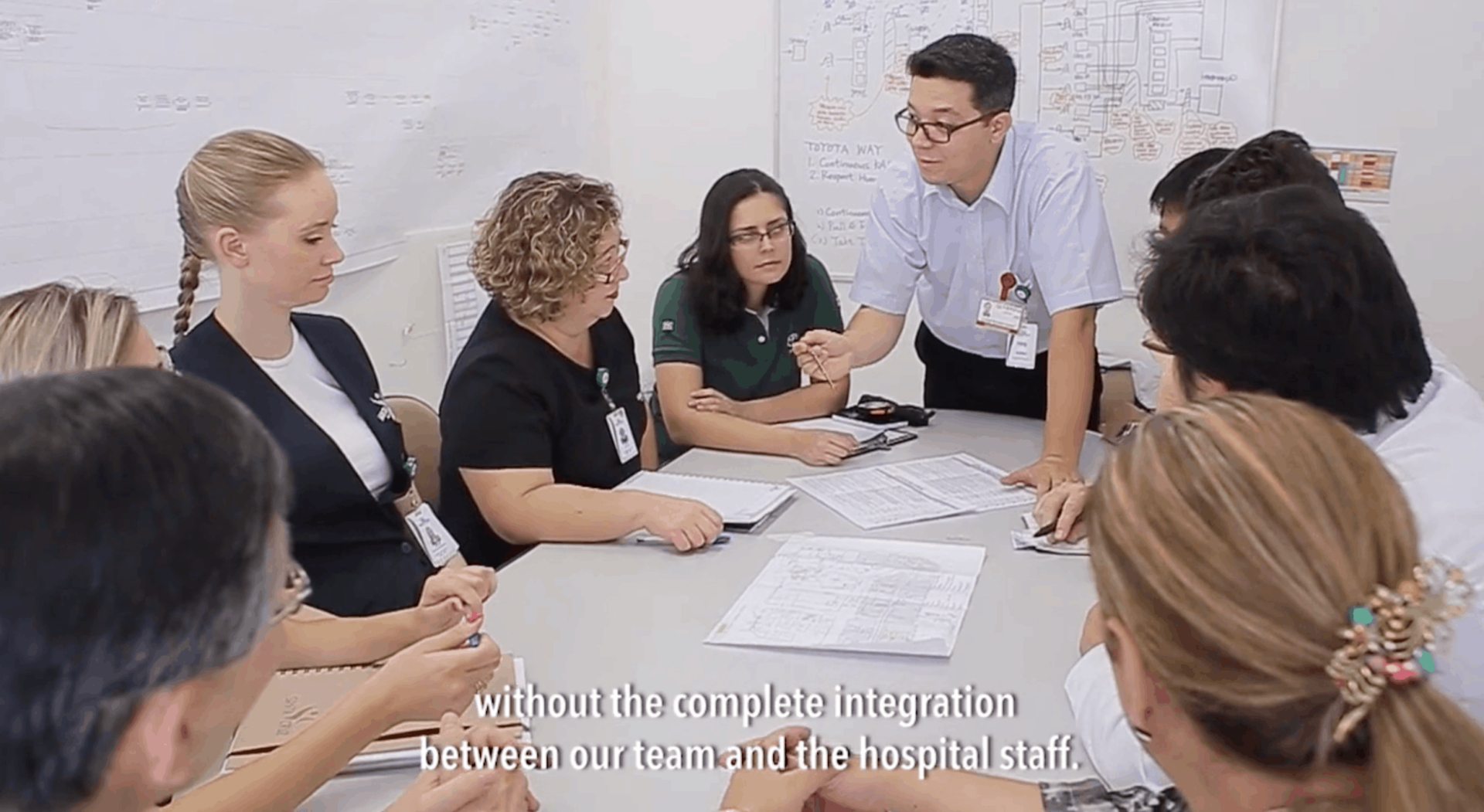
Improving Systems
Studying patient flow showed that patients in the waiting area had “to constantly come and go from different rooms.”
They also wanted to make it easier for doctors to always know “where to find their patients.”
They changed the room layout and flow:
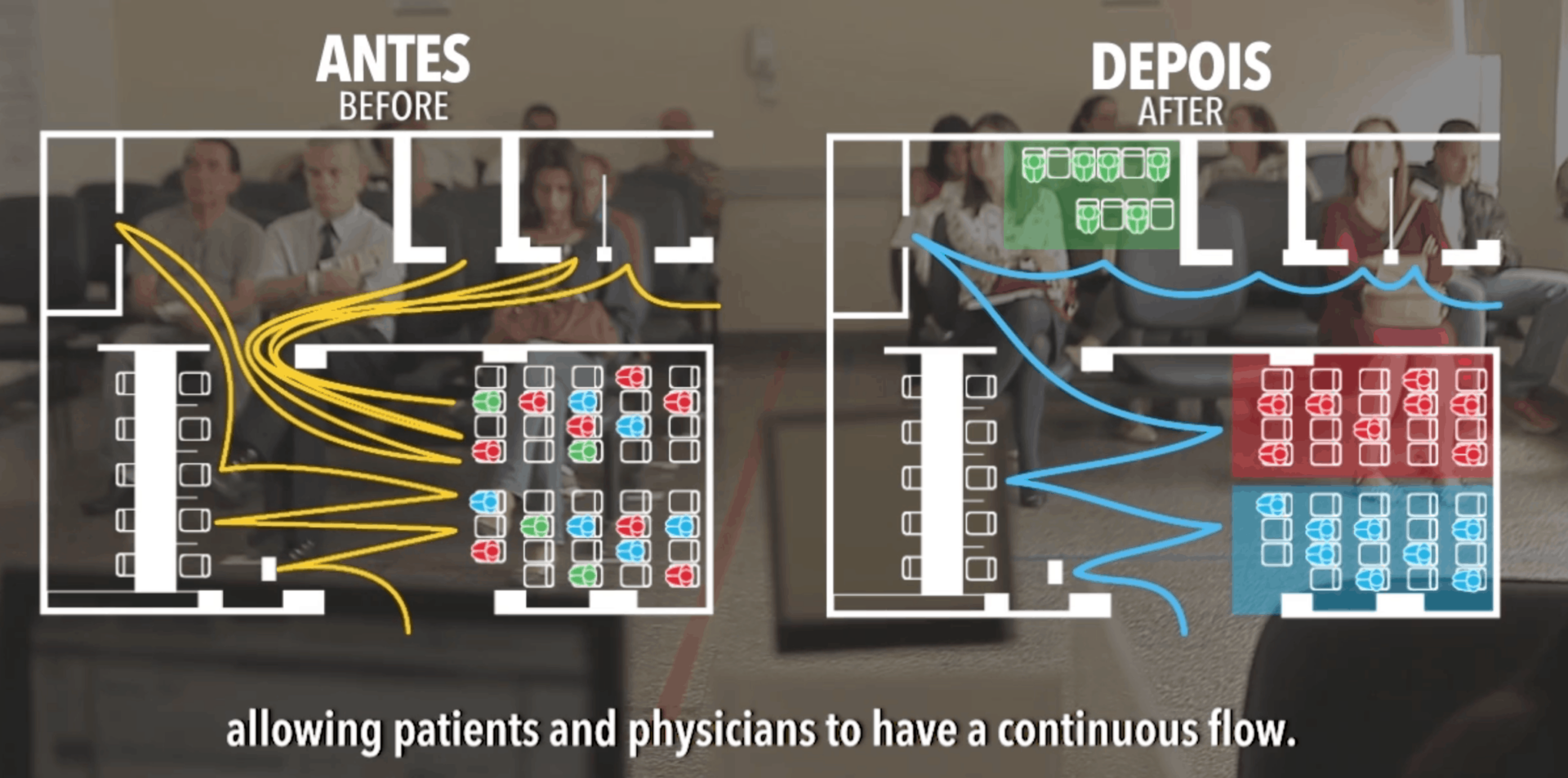
This is a great example of improving the system instead of just telling staff to work faster or to try harder.
This reduced the average waiting time by about 30 minutes.
Yeah, I'd love to see a “Process Behavior Chart” instead of a simple before-and-after comparison :-)
Another improvement was making it easier to collect medicines and nursing equipment. This is an example of more detailed work analysis at an individual level instead of the broader patient flow. They again studied the work and used a spaghetti diagram to illustrate the waste.
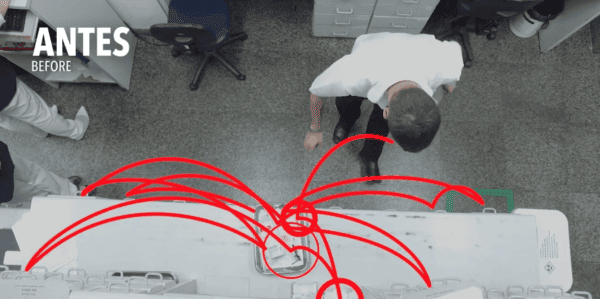
This illustrated “unnecessary effort that took the time and energy of the teams.” Making work easier for nurses and staff leads to better patient care in so many ways.
The prep time was reduced by 22% by arranging the gathering work into a linear flow.
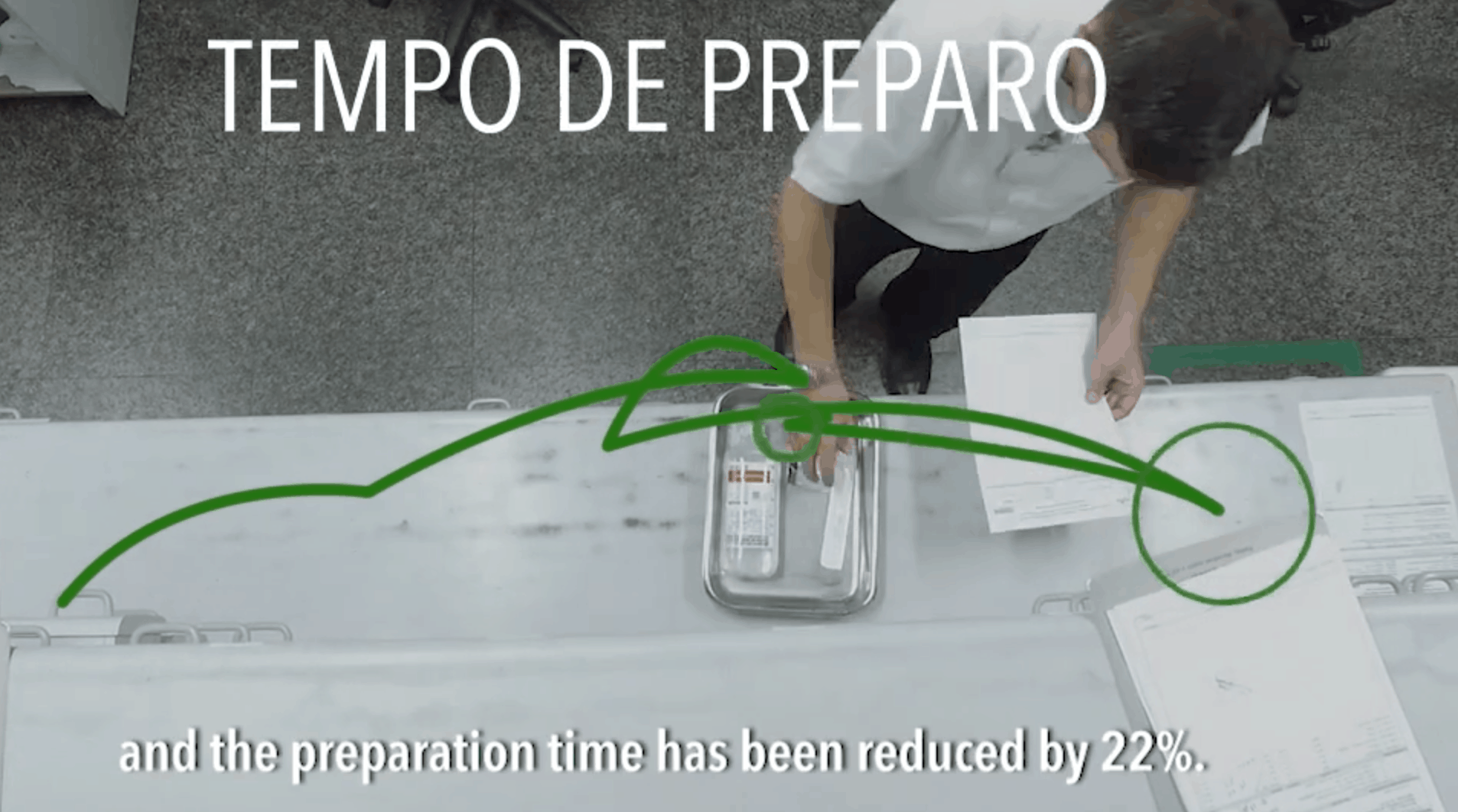
Executive Perspectives
The hospital president says:
“For us, it is a great joy to receive this Toyota system that is quite applicable also in the hospital [in which] we serve people” where we “save lives.”
The recently retired Toyota executive Steve St. Angelo says:
“I've been a student of the Toyota Production System for 30 years and I've always believed that the Toyota Production System could be utilized anywhere to do anything.”
Speaking of the hospital work, he added:
“… you could see that the employees improved their jobs and you could see the smiles on their face and less stress doing their work, and also the biggest benefiter are the clients, the way time is reduced.”
St. Angelo thanked the hospital team for their “courage” to take on new ideas. I love it when Toyota shares examples like this… and I hope there will be more stories I can continue to share here.
See more past examples of the great work Toyota does in healthcare and other non-profit settings:
Thanks again to Toyota for their inspiring work around the world!
Please scroll down (or click) to post a comment. Connect with me on LinkedIn.
Let’s work together to build a culture of continuous improvement and psychological safety. If you're a leader looking to create lasting change—not just projects—I help organizations:
- Engage people at all levels in sustainable improvement
- Shift from fear of mistakes to learning from them
- Apply Lean thinking in practical, people-centered ways
Interested in coaching or a keynote talk? Let’s start a conversation.
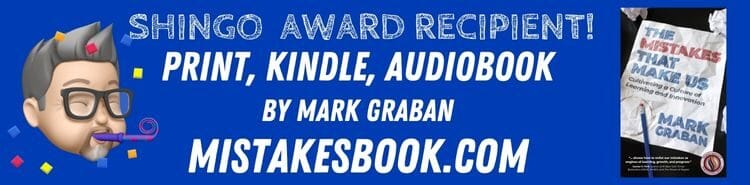
Mark, what a great article. I think that you are right with respect to why Toyota doesn’t focus on the 8th waste (which is addressed with their Daily Lean Management System and Huddles and the fact that everyone is always engaged and encouraged to improve the process) in much the same way that in my early days as a consultant my Lean coach, who was Toyota trained, basically said we don’t sell 5S, 5S is always the starting point for all projects. That being said I really enjoyed the visuals from your article and how the point to point diagrams show the reduction in motion waste.
I found this very interesting to read. Helping a hospital, specifically the emergency room layout, is such a useful thing to improve. By doing this, the patients and doctors are much more organized and lose that feeling of being lost or overwhelmed by chaos.
We are a non profit organization here in Rio de Janeiro and we have two large public hospitals under our care. We’ve started the process to implement this method to help us to improve the whole for benefits of the people and, for sure, this article shown us that we are following the best way to achieve it. Thank you!