Healthcare – Creating Value for Patients
Healthcare innovation is prone to continuous pilots of improvements that are already proven and a half-hearted embrace of meaningful change. Sachin Jain, CEO of CareMore Health provides us with a sense of urgency and duty to close the gap between change and reality in his excellent essay The Healthcare Innovation Bubble.
Saskatchewan famously paid $44 million on a province-wide Lean implementation. Was it worth it? It's hard to find sufficient evidence according to Thomas Rotter. The consulting firm that received most of the money, John Black and Associates, blamed the media and racism for some of the failures, and once said to himself after a meeting with healthcare executives, “If you're not dead (in 20 years), you're going to be in one of your health-care systems here in bed, with a tube up your ass and one down your throat. You're going to be saying to yourself, ‘My God, I wish I would have asked John Black to come in and help improve my care,' “, JBA's website touts the success of their work. The truth is likely complicated
Hospitals have been gathering patient experience survey data for a long time, mostly to ‘check the box'. These are usually ill-defined and noisy measures of patient experience, and there is no guarantee on if or how a hospital will choose to act on it. The gold standard in improving patient experience is co-designing the system with patients and providers. Canadian hospitals would be wiser to spend more time on this than building a better dashboard.
Operational Excellence
“Just put up a huddle board” is a common refrain from those early on in developing a lean management system. This is evidence of the common confusion between making things visual (information sharing) and visual management (driving behaviour). Pascal Dennis shares Level 3 (Organizing Behaviour) and Level 4 (Eliminating Defects) Visual Management to demonstrate the differences and provide a maturity model for visual management in the workplace. His post on Level 1 and 2 Visual Management is here.
What can help sustain a lean culture once the leader is gone? I have direct experience working for a lean organization that suffered decline after the departure of leaders and board members. Aravind Chandrasekran and John Toussaint examine some examples of health systems that failed and succeeded in sustaining cultures of continuous improvement amid some key departures.
Through the popularity of Agile, DevOps workers are discovering lean and continuous improvement principles. I enjoyed reading this blog post on A Different Meaning of CI and that Deming's points are alive and well in DevOps.
Similarly, I find great overlap between articles on Lean Transformation and Digital Transformation. This excellent article from MIT Sloan Review discussed the challenges of building digital-ready culture in traditional companies and the need to discover what practices are helpful to preserve and which need to be prepared for transformation.
Lean is not “about speed” despite a lot of nonsensical tropes to the contrary. If you're using Lean to make your IT department “efficient” instead of also transforming your leadership, staff, and management systems, your results will be disappointing according. Read more in “Is Lean IT Killing Your Digital Transformation?”.
Creating value for the customer is a basic principle of OpEx. This requires one to deeply understand her customers. Our dubious love of surveys, big noisy metrics, and benchmarking has caused many organizations to replace a deeper understanding of the customer experience with Net Promoter Scores. Last mixtape, I shared the Wall Street Journal's article on Net Promoter Score. Here's another article on Why Net Promoter Score is past its Prime.
Leading & Enabling Excellence
The ‘Pyramid' hierarchy with ‘command and control' structure is still the norm – partly because it has worked for a long time. Many organizations are discovering that the bottom of the pyramid has been ignored, and progressive companies are turning rigid pyramid structures into agile, autonomous teams. Corporate Rebels describe 5 Steps to a Progressive Organizational Structure.
Leaders are most prone to fall in love with their own ideas, which can lead them to overvalue and oversell their ideas while ignoring others. HBR with more on How to Overcome the Bias We Have Toward Our Own Ideas.
Transparency and humility are required for sustainable levels of excellence in quality. Boeing is finally admitting it fell short when implementing safety features in the 737 Max, and is fixing the problem.
Coaching – Developing Self & Others
Productive people say “no”, develop systems to manage their work, focus deeply, and ruthlessly prioritize. Busy people are constantly adding to their plate, multi-tasking, working late, and moving around distractedly. Read more in the Differences Between Busy and Productive People.
Just because you see does not mean you observe. Read more in The Art of Observation.
Many who work in large organizations are part of a matrix-reporting structure. This can offer ideal conditions for sincere uses of coaching conversations, whereas relying on direct report relationships for practicing coaching conversations can be risky.
How to deal with a jerk, without being a jerk.
Continuous improvement requires discovery and analysis of facts. Unfortunately, we are deeply susceptible to ignoring the facts if they get in the way of the narrative we've built up. This is no more prevalent in the post-truth world of “fake news”. Here, a cognitive scientist explains why we are so susceptible to fake news.
Books, Podcasts, Videos
Deming stated long ago in his vaunted 14 Points that we must “Drive Fear Out” of our organization. Amy Edmondson provides a masterful, modern take on this point in The Fearless Organization: Creating Psychological Safety in the Workplace for Learning, Innovation, and Growth. I highly recommend this book.
People often tell me “we don't make widgets”, usually to imply that their processes are more complex than making things. I recently re-watched Thomas Thwaites' Ted Talk on How I Made a Toaster from Scratch. , a reminder to us all of the inherent complexity of making everyday items and the inter-connectedness of the world.
Great podcast on Gemba Academy with Skip Steward on Establishing a Standard Behaviour.
Get These Mixtapes via Email
Please scroll down (or click) to post a comment. Connect with me on LinkedIn.
Let’s work together to build a culture of continuous improvement and psychological safety. If you're a leader looking to create lasting change—not just projects—I help organizations:
- Engage people at all levels in sustainable improvement
- Shift from fear of mistakes to learning from them
- Apply Lean thinking in practical, people-centered ways
Interested in coaching or a keynote talk? Let’s start a conversation.
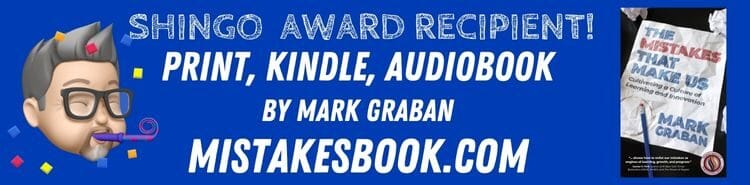