This is an interesting article:
Inside Toyota's Takaoka #2 Line: The Most Flexible Line In The World
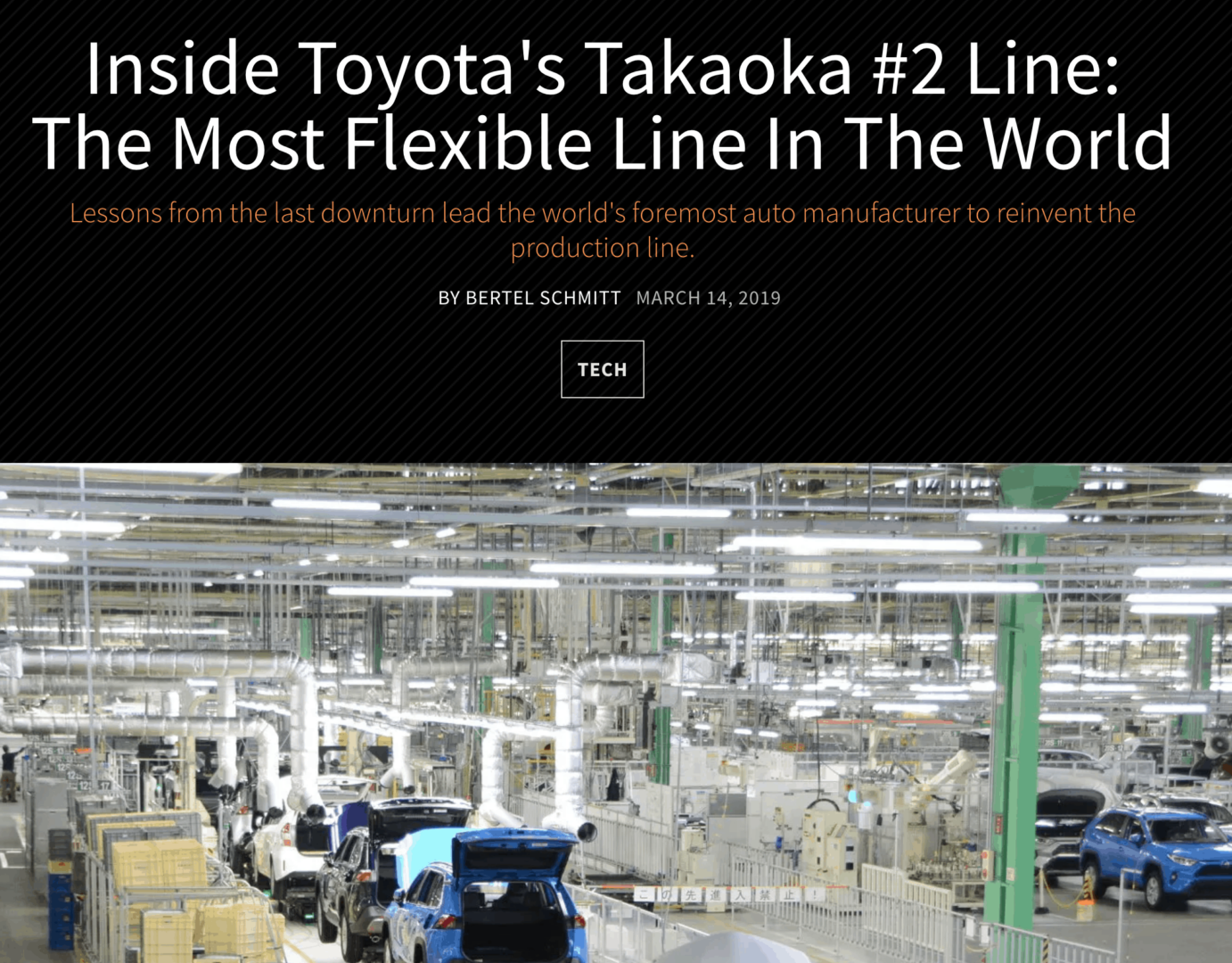
I had a chance to visit the ‘Takaoka #1″ line in February 2018 as part of my tour with Kaizen Institute. This article makes me wish we had been able to see Takaoka #2, but that sounds like a somewhat rare and special opportunity (even more special than visiting Toyota is normally).
Here's a picture I was able to take from the bus, where you can see the plant's logo:

You can also see a “safety arch,” which you can also see in this photo that I took as we drove past:
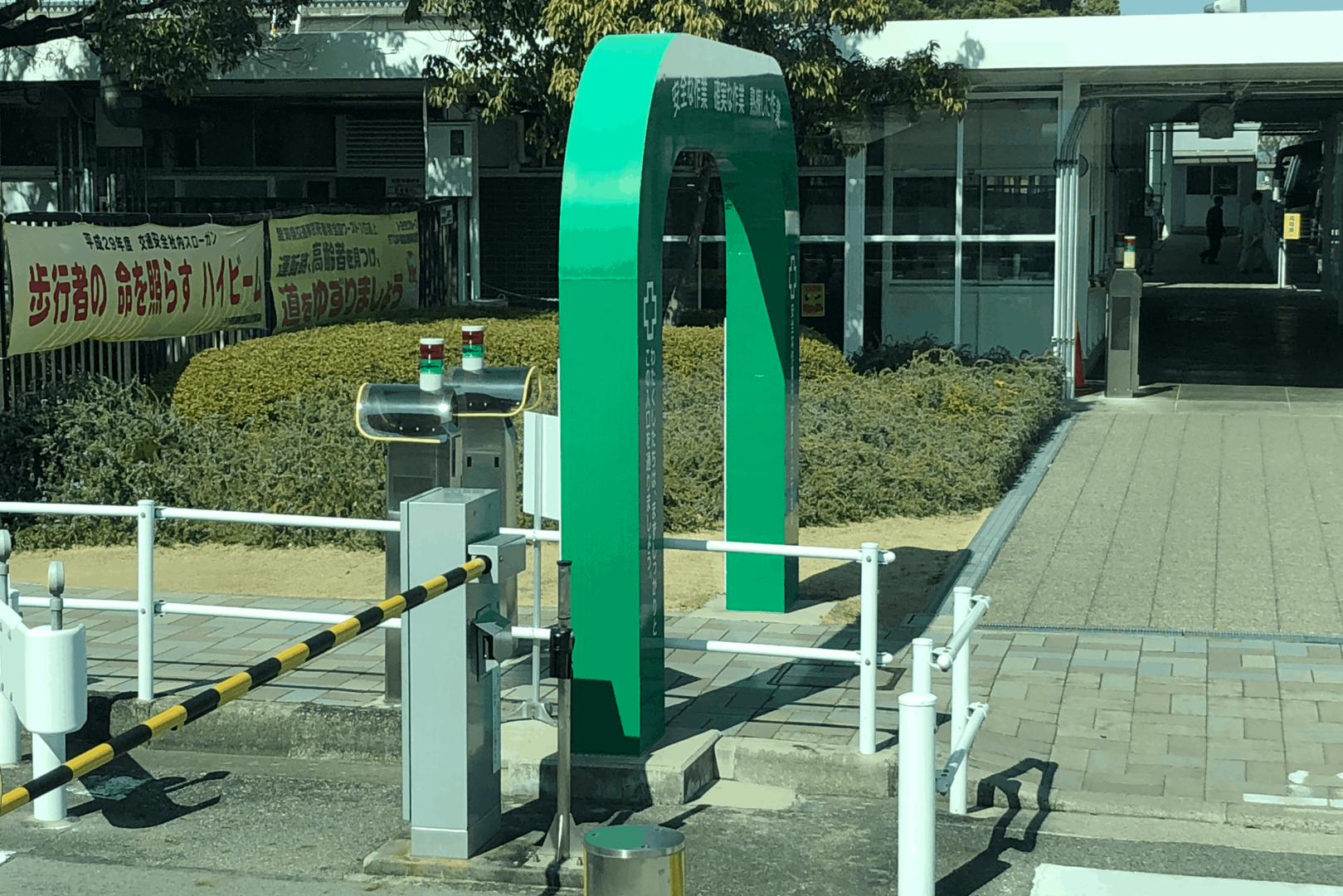
I'll share some highlights from the article along with some of my notes from my visit.
The article has a somewhat long introduction that's the least interesting part of the piece, at least to me. It describes things I know well as an Industrial Engineer about designing and re-balancing assembly lines.
The article does make an interesting comparison between the old Takaoka #1 line and the new Takaoka #2. Takaoka #1 uses a robot to grab and install a spare tire. This takes 57 seconds, which creates a bottleneck or a constraint for the plant. Even if you rebalance the rest of the assembly line, it can't run faster than a car every 57 seconds (without buying a second machine to run in parallel).
At Takoka #2:
“Takaoka II is the Judo fighter of car plants: Quick on its feet, flexible, and smart.
Here, a worker pulls the spare tire with something that looks like a pushcart with long arms. The worker wheels the cart around, and he drops the tire into a Prius. Elapsed time: 17 seconds. I am looking for electric cables, or air hoses that power the lightning-fast spare tire machine. I don't find any. “It's all done with springs and counter-weights,” [plant project general manager] Akahane beams.”
Takoka #2 is more flexible in how volume can be adjusted:
“Takaoka II can increase and decrease capacity, and production cost stays the same” says Akahane.
The factory, of course, epitomizes the “kaizen” philosophy:
“Like all Toyota factories, Takaoka II is built on the on-going “kaizen” improvements developed by its workers who want to make their work go faster, smoother, smarter. Asked what kind of people he's looking for to work at Takaoka II, Akahane answers: “We want people who can think for themselves, not robots who do as they are told.”
The article also picks on Tesla a bit:
“When we were theorizing about a gifted car plant, the example may have vaguely sounded like Toyota's NUMMI plant, that was, for practical purposes, given to Tesla in 2010 in exchange for shares. A year later, Toyota opened its first simple, slim and flexible plant as a pilot north of Sendai, Japan, and a few years thereafter, Toyota sold its shares in Tesla. If the relationship would have lasted a little longer, and if Elon Musk's hubris would have been a little less pronounced, Tesla could have learned something.”
That's why the Toyota Production System seems to not at all be a part of the Tesla approach, sadly — something I've blogged about before:
Back to the Takaoka plant. The manager says something surprising (maybe it was an issue of context or translation):
“How long does Akahane have to stop the line when a new model is introduced?
He shapes thumb and index finger to a zero. “There is no stoppage of the line at all. We spend less than an hour exchanging parts and tools, but we do that while the line makes other models.” As production of the new model starts at the beginning of the line, the last of the older models exit at the other end while the line keeps moving.
What would happen if the line stops? Akahane's hand slices across his throat. “My boss would cut my head off if the line would be down.”
I think the context about stopping the line is related to changeovers, rebalances, etc. I doubt anybody's head is being cut off (figuratively) if the line is stopped temporarily due to an “andon cord” pull (or button push).
Back to my plant visit…
I certainly heard andon cord chimes and saw andon lights flashing. I jotted down that there were at least three andon cord pulls that occurred when standing in one area. One of the pulls was resolved immediately by a team leader without the line actually stopping.
One comment from the guide or the displays:
“Toyota workers produce high-quality automobiles with the support of highly-efficient robots and machines.”
Robots are there to support people, not replace them. Their painting area is 90% automated… not 100% automated because there are some painting jobs that are done better by humans.
“TPS is based on the customer-first principle.”
Yes, it's a very customer-driven approach.
“Toyota aims to achieve high-quality and low costs by eliminating waste in its production to meet ever-changing customer demands.”
As we walked through the tour, the guide didn't hang her bag on the hooks that were there when she stopped to talk. The hooks were something that I blogged about in 2014 when our guide at the Tsutsumi plant said it was her idea to put up those hooks… did the idea spread to other plants? Or was that idea developed in parallel at different plants?
If she's comfortable holding her bag, it's OK that she doesn't follow the “standardized work” for tour guides? It might be OK if using the hooks is optional.
As Brad Schmidt told us in my 2012 tour, “Unity in the essential, liberty in the non-essential…”
She did use one of the hooks before we stopped for our group picture.
The kaizen process there was described as a very non-bureaucratic approach:
- Have a good idea
- Express our opinion to the company
- Write it down
- Suggest it to the Team Leader
- Discuss
They receive 500 yen for every idea (which is less than $5 USD) — it's more about the recognition than it is about the money.
They talked about their new employee training process. It's six to nine weeks and it starts with “an introduction to the company philosophy.”
Well, that's it for my notes… hope you enjoyed the post.
Please scroll down (or click) to post a comment. Connect with me on LinkedIn.
Let’s work together to build a culture of continuous improvement and psychological safety. If you're a leader looking to create lasting change—not just projects—I help organizations:
- Engage people at all levels in sustainable improvement
- Shift from fear of mistakes to learning from them
- Apply Lean thinking in practical, people-centered ways
Interested in coaching or a keynote talk? Let’s start a conversation.
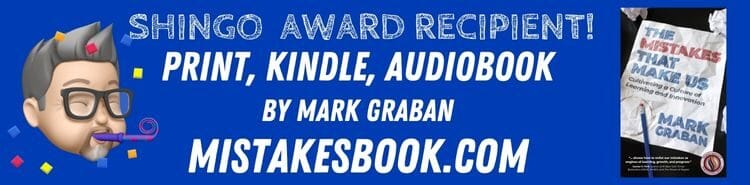
Great post. I’d love to see the Takaoka plant as well. What the manager said about not stopping the production line for a model change was true in Georgetown, KY as well. While no heads would roll if the line did stop, there would be a tremendous amount of visibility and pressure to start the line again – although this was no different than if they were running normal production.
Another aspect of a model change I found interesting were the test vehicles we produced before the formal model change. The first round was for the model change team (called the ‘Pilot’ group) to evaluate the vehicle for fit, function, ease of assembly, etc. The next rounds were for the production team members on the line to have a chance to practice building the new model so they could have some learning cycles prior to the actual start of the model build.
However, I remember one hiccup during a model change where 80+ new models were accidentally welded with the old model’s C pillars (formed sheet metal part that creates the ‘blind spot’ in the back corners of the car) that were not quarantined and removed as they should have been. Long story short, my upper leadership decided to scrap all the vehicles. In true Toyota style, we dug down to the true root cause and discovered that moving the datum hole on new parts just a few centimeters would make it nearly impossible to install older parts on the new model.
Thanks for your comment, Jess!
It sounds like Toyota learned from that hiccup… “moving the datum hole” sounds like an effective form of error proofing.