Yesterday's blog post was about a situation (with my podcast hosting service) that triggered memories of my time at General Motors in 1995. Today's post is about a recent article on Boeing that definitely caused me to think of that broken, dysfunctional “pre-Lean” culture that I suffered through (and learned from) in my first year at GM.
In 1995, nobody claimed GM was Lean so the expectations were low. They were who they were and my new plant manager in 1996 started to change things. Boeing is a company that has been pointed at as a great example of Lean Manufacturing, so it's troubling to read reports that suggest otherwise.
From the New York Times:
Claims of Shoddy Production Draw Scrutiny to a Second Boeing Jet
Workers at a 787 Dreamliner plant in South Carolina have complained of defective manufacturing, debris left on planes and pressure to not report violations.
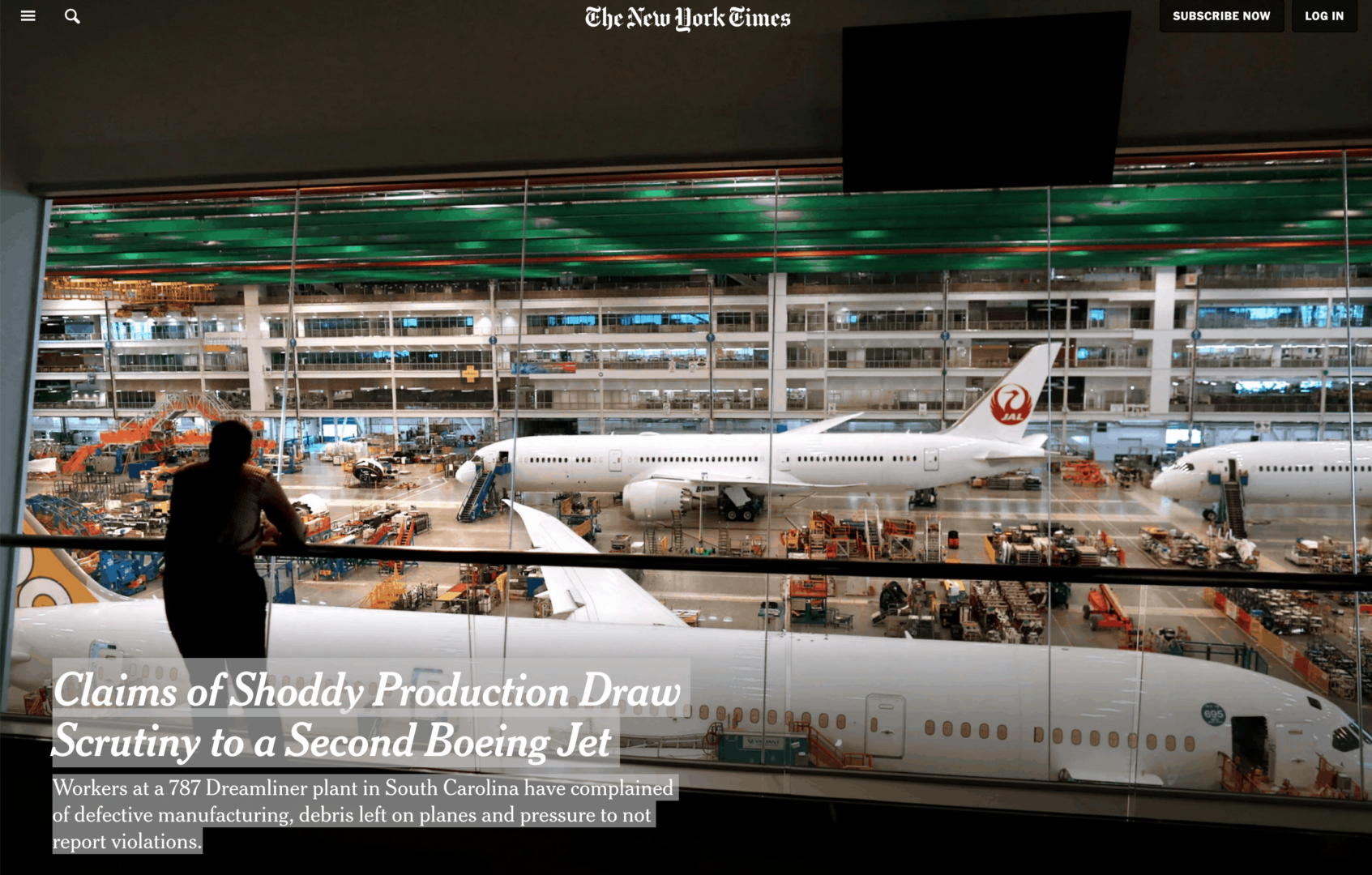
The Times, claims after reviewing lots of internal documents and interviewing many people, that:
“…the factory, which makes the 787 Dreamliner, has been plagued by shoddy production and weak oversight that have threatened to compromise safety… a culture that often valued production speed over quality.
Facing long manufacturing delays, Boeing pushed its work force to quickly turn out Dreamliners, at times ignoring issues raised by employees.“
Sadly, this reminds me of my time at General Motors, especially during the first year working under a very traditional plant manager. It was a “quantity first” culture. Quality suffered because of bad management decisions, as I've blogged about many times before. I was ignored or vaguely threatened for repeatedly pointing out safety risks in the plant.
Some of the posts:
So, can I believe that a company can claim to be “The Standard of the World” as Cadillac did at the time, while still being an internal dumpster fire? Yes. Is that the case at Boeing? I don't know, but I could believe it.
“Workers have filed nearly a dozen whistle-blower claims and safety complaints with federal regulators, describing issues like defective manufacturing, debris left on planes and pressure to not report violations. Others have sued Boeing, saying they were retaliated against for flagging manufacturing mistakes.”
I hear too many stories in healthcare about people claiming that they were retaliated against for speaking up about safety or quality.
There's current a “well, there's two sides to every story” fight going on related to the long-troubled Detroit Medical Center.
Side 1: “Fired cardiologists sue DMC, Tenet, alleging retaliation for quality complaints“
Side 2: “Tenet responds to lawsuit, accuses cardiologists of bullying staff, missing procedures“
Or maybe both sides are true.
About Boeing again:
“Joseph Clayton, a technician at the North Charleston plant, one of two facilities where the Dreamliner is built, said he routinely found debris dangerously close to wiring beneath cockpits.
“I've told my wife that I never plan to fly on it,” he said. “It's just a safety issue.”
There are sometimes nurses in hospitals who say they wouldn't let a loved one get surgery from a certain surgeon they know or have worked with.
I never felt like Cadillac engines I was involved with were so dangerous that I wouldn't let a family member buy one. The quality problems I dealt with would have most likely led to an engine that stopped working… but the risk is minimal compared to a defective plane or a problematic hospital.
As with hospitals, there's always a spokesperson:
“Boeing South Carolina teammates are producing the highest levels of quality in our history,” Kevin McAllister, Boeing's head of commercial airplanes, said in a statement. “I am proud of our teams' exceptional commitment to quality and stand behind the work they do each and every day.”
When I was at GM, the “teams” were committed to quality… but management, frankly, often was not. Is “highest levels of quality” any more verifiable than “patient safety is always our highest priority?”
It's easy to give lip service.
The Times article reminds us that the Boeing plant in South Carolina, the one that's subject of the story, builds the 787 “Dreamliner” and that plane has never crashed. But, it can also be true that the process (and the culture) isn't as good as it needs to be.
“Faulty parts have been installed in planes. Tools and metal shavings have routinely been left inside jets, often near electrical systems. Aircraft have taken test flights with debris in an engine and a tail, risking failure.
On several planes, John Barnett, a former quality manager who worked at Boeing for nearly three decades and retired in 2017, discovered clusters of metal slivers hanging over the wiring that commands the flight controls. If the sharp metal pieces — produced when fasteners were fitted into nuts — penetrate the wires, he said, it could be “catastrophic.”
The article shares more examples of FOD violations — Foreign Object Debris. Customers are rightfully upset with them. That's as serious of a problem as so-called “never events” in healthcare. Yet, “never events” happen more often than never… sad to say.
That's why I generally use the phrase “so-called never events.”
When I was at GM, I saw first hand when there was pressure to use questionable parts inside those Cadillac engines (as I wrote about here).
I'd hate to think that pressure for speed or production numbers would be the priority over safety and quality… but I can understand how a big company bureaucracy sometimes creates measures and incentives that don't drive the right behavior.
Compared to GM though… GM was arguably in the very early days of any sort of Lean transformation in 1995. But Boeing is often held up as a great example of Lean manufacturing. It seems like GM fixed the factories more than it fixed the company culture… is the same true at Boeing?
“[Former quality manager] Mr. Barnett, who filed a whistle-blower complaint with regulators, said he had repeatedly urged his bosses to remove the shavings. But they refused and moved him to another part of the plant.”
A parallel might be a nurse who complains about the quality in one department being moved to another.
More troubling details… things that happened when they got behind on production (which is when the really bad quality problems would happen at GM):
“In North Charleston, the time crunch had consequences. Hundreds of tools began disappearing, according to complaints filed in 2014 with the F.A.A. by two former managers, Jennifer Jacobsen and David McClaughlin. Some were “found lying around the aircraft,” Ms. Jacobsen said in her complaint.
That sounds like a combination of poor process controls and an environment where people were pressured to rush. FOD makes me thing of “retained surgical items,” which is a euphemistic way of saying “we left a sponge inside you, dear patient.” That's a “never event,” by the way. I mean “so-called never event.”
Then there's this:
“The two managers also said they had been pushed to cover up delays. Managers told employees to install equipment out of order to make it “appear to Boeing executives in Chicago, the aircraft purchasers and Boeing's shareholders that the work is being performed on schedule, where in fact the aircraft is far behind schedule,” according to their complaints.”
Those managers, like the managers at the VA offices or managers at Wells Fargo branches, are part of a system. Low-level VA managers and Wells Fargo branch managers were oftentimes fired for being “unethical.” They're not to blame for acting in the manner that the organization's higher ups are demanding, are they?
But wait, there's always a spokesperson at the ready:
Gordon Johndroe, a spokesman for Boeing, said, “We prioritize safety and quality over speed, but all three can be accomplished while still producing one of the safest airplanes flying today.”
Yes, you can get all three… and those can all lead to lower cost… but you need the right kind of environment for that.
“A hospital spokesperson said they were dissapointed to learn of the CMS rating and believe it doesn't reflect performance. Patient safety is always a top priority for our team and we are consistently focusing on the quality of care we provide to each and every patient.”
Some hospital spokesperson
Back to the Times article:
“
While inspecting a plane being prepared for delivery, Mr. Clayton, the technician currently at the plant, recently found chewing gum holding together part of a door's trim. “It was not a safety issue, but it's not what you want to present to a customer,” he said.
I guess it's possible that the spokesperson and the executives think such statements are true… and it's also possible that quality problems exist.
The Beatings Will Continue Until Morale Improves
If true, this story takes the cake. It's leadership's responsibility when they create an environment of overburden and chaos. Blaming the workers isn't the right thing to do. Blaming the workers was what happened at GM (and that didn't help, but we got a new plant manager who ended that). Blaming the workers doesn't help in healthcare (but that's all too common).
The disarray frustrated one major carrier. In 2014, factory employees were told to watch a video from the chief executive of Qatar Airways.
He chastised the North Charleston workers, saying he was upset that Boeing wasn't being transparent about the length or cause of delays. In several instances, workers had damaged the exterior of planes made for the airline, requiring Boeing to push back delivery to fix the jets.
Ever since, Qatar has bought only Dreamliners built in Everett [the other Boeing plant in Washington].
The lack of transparency was not the workers' fault. Why lecture them? Making employees watch that video seems like the height of disrespect (or it's just a waste of time that further delays planes). Oh wait, let's pause for a spokesperson:
In a statement, Qatar Airways said it “continues to be a long-term supporter of Boeing and has full confidence in all its aircraft and manufacturing facilities.”
When There's Production Pressure, Bad Decisions get Made About Quality
Another story that reminds me of the bad-old-days at GM:
Mr. Barnett, the former quality manager, who goes by Swampy in a nod to his Louisiana roots, learned in 2016 that a senior manager had pulled a dented hydraulic tube from a scrap bin, he said. He said the tube, part of the central system controlling the plane's movement, was installed on a Dreamliner.
Mr. Barnett said the senior manager had told him, “Don't worry about it.” He filed a complaint with human resources, company documents show.
He also reported to management that defective parts had gone missing, raising the prospect that they had been installed in planes. His bosses, he said, told him to finish the paperwork on the missing parts without figuring out where they had gone.
The F.A.A. investigated and found that Boeing had lost some damaged parts.
Yeah, “lost.” Boeing claims their investigation found nothing, but I guess that would be in their interest…
This reminds me of the problem with a surgical team “losing” items… and being rushed to sew the patient up without accounting for every item. This, again, is supposed to be a “never event.”
Does this remind you of some hospitals?
“several former employees said high-level managers pushed internal quality inspectors to stop recording defects.”
I know somebody who works in quality at a hospital that receives the top rating of 5 Stars from CMS. This employee says, quite confidently, that management has created such a culture of fear that people are afraid to report problems. Data gets massaged or faked and submitted to the feds, so things look good. But that hampers our ability to be informed “healthcare consumers” and fooling yourself into thinking you are really 5 Stars is going to do nothing but hamper further improvement (“Why improve? We're 5 Stars!”).
That also reminds me of the Deming story about a factory that offered incentives for hitting zero injuries… so people just stopped reporting injuries.
Or, people are pressured or punished in healthcare for hiding problems:
We need more than excellent staff… we also need great leadership and the right organizational culture… and good processes!
Barnett, the quality manager in the story, says he was reprimanded for using email instead of “F2F” to discuss quality problems… the implication being to not put anything in writing.
The story from the NY Times is exhaustive… and exhausting. Again, for a company that's often held up as a Lean exemplar, this is all very very disappointing if even some of it is true.
Please scroll down (or click) to post a comment. Connect with me on LinkedIn.
Let’s work together to build a culture of continuous improvement and psychological safety. If you're a leader looking to create lasting change—not just projects—I help organizations:
- Engage people at all levels in sustainable improvement
- Shift from fear of mistakes to learning from them
- Apply Lean thinking in practical, people-centered ways
Interested in coaching or a keynote talk? Let’s start a conversation.
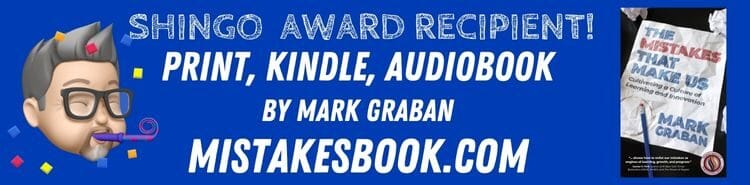
[…] of Shoddy Production Draw Scrutiny to a Second Boeing Jet, and Mark’s blog post about the […]