I've been battling some sort of bronchitis or respiratory infection for about five days now…. blah. Lots of coughing and my voice is shot. Good thing I'm traveling or speaking this week. And, I'm glad not to be in a hospital.
Our friend Bruce Hamilton was, unfortunately, hospitalized recently and he, of course, had some insightful observations that he's blogged about. So, I'll point you to those posts.
Bruce is, among other things, the creator of the “Toast Kaizen” video.
In his first post, “Sorta-Systems,” Bruce noticed a number of systemic problems, including a patient information whiteboard that wasn't being used as designed. I see too many unused whiteboards in my travels.
Bruce quipped, “I wish I'd invested in the whiteboard market when I began my consulting career. They've multiplied exponentially since the advent of Lean.” That and 3M Post-It Notes, right?
Bruce asked:
My question is “How often do we audit systems that are supposed to be making us more productive?”
I think we should also ask questions like, “Were the intended users of the boards involved in their design?” I agree with Bruce that if something is important, then it's important for supervisors and managers to check to see that the process is being followed (or that boards are being used).
I think Bruce and I would agree that the follow up should involve questions about why the boards aren't being used. Or, we could use the “Motivational Interviewing” approach to have conversations about WHY it's important to use them.
Bruce also wrote a post called “Small Things,” where he tells a story about repeated problems with staff not knowing which light switch controlled which light. The same mistakes were being made over and over again. It was a systemic problem and it probably annoyed Bruce (it would have bothered me).
He summarizes the situation:
“You shouldn't have to deal with a broken process,” I said, “why don't you just label the switches?” She thought for a second and replied, “Good idea.”
Before her shift was over, the two errant switches had been marked to clarify the lighting sequence over the beds. And, guess what? The following night lights were switched on without annoyance to staff or patients.
When it was my turn for a visit from the CNA, I thanked her for fixing the problem. “It was a small thing,” she humbly replied. I thanked her again and responded, “Yes, but you'll never have the problem again.”
There's power in asking people to identify and fix small things, and it reminds me of this blog post:
Sometimes, one little idea is all it takes to spark what grows and becomes a culture of continuous improvement.
Please scroll down (or click) to post a comment. Connect with me on LinkedIn.
Let’s work together to build a culture of continuous improvement and psychological safety. If you're a leader looking to create lasting change—not just projects—I help organizations:
- Engage people at all levels in sustainable improvement
- Shift from fear of mistakes to learning from them
- Apply Lean thinking in practical, people-centered ways
Interested in coaching or a keynote talk? Let’s start a conversation.
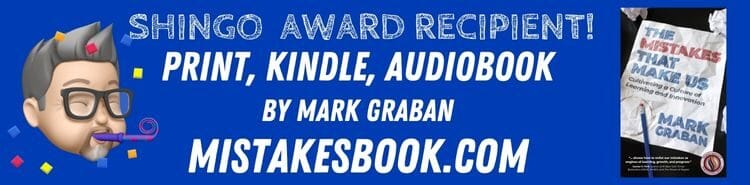
This brings up a great point of how even small things can start a trend of improvement which could lead to even bigger problems being fixed. You have to start somewhere anyways. With this I also agree that when a system is put in place the people using and involved in that system should be present for the design and creation of it so it can be put to its full use like the whiteboard example.
One of the most overlooked parts of making a change to a process or implementing a new one is consulting the users. There are probably thousands of cases where leadership has neglected to ask employees about lean improvements, and those are bound to fail. I also notice the inefficiencies in the supply chain of healthcare whenever I go to the doctor. There has to be a better way to put down new patient info, the amount of clipboards I have been handed makes me go crazy. There has to be a better way.