The first part of this post is a pretty long introduction before sharing quotes and views from an article that raises concerns about Lean at Zuckerberg San Francisco General
In general, the following healthcare problems make me very sad:
- Nurses (or other hospital staff) being overworked to the point of being stressed out
- Staff being rushed in their work, which leads to an increased risk of error and harm to them or patients
- Nurses not being able to take proper and humane rest and meal breaks (which causes fatigue which is bad for them and their patients)
- Patients not getting the care they need (in terms of timeliness, safety, quality, or the level of caring) because the hospital they're in is understaffed
All of those problems occur in hospitals. You might even say “many hospitals.” It's been like that for a while. These things make me sad quite often, although being sad isn't helpful really. But that's my (hopefully understandable) human reaction to such things.
These are problems that need to be solved. They might not be easy to solve, but we need to try. Leaders and executives not accepting those conditions is the first step to finding approaches that, at the least, make things somewhat better until we can find solutions.
Hear Mark read this post — subscribe to Lean Blog Audio
Hospitals have a long tradition of cutting staff in an attempt to save money. I've long criticized the practice of “flexing” or sending staff home early as a way to keep productivity metrics in line with a goal.
A Toyota plant NEVER sends staff home early, even if the line is down or if there are no vehicles to build. The employee gets their full paycheck and they're engaged in training, personal development, or improvement work.
It makes me sad (if not somewhat angry) when I hear hospitals say “we don't have time for improvement” but they are frequently sending staff home early. I think that's short sighted to send staff home to save a few bucks. Point #1 of “The Toyota Way” is to take the long-term perspective, even at the expense of the short-term. If you're not copying Point #1 are you really emulating Toyota? Are you really practicing Lean?
“Base your management decisions on a long-term philosophy, even at the expense of short-term financial goals.”
The Toyota Way
Overwork / understaffing can be a big problem in hospitals. Patients will get harmed or killed as a result. A less serious effect is poor care and poor patient satisfaction. One could say it's a moral imperative to make sure staffing levels are set correctly.
The Toyota / Lean approach would be to study and understand the work, understanding the time requirements for safe, high-quality work, and to make sure (if anything) you're slightly
One long-standing problem I've run across in healthcare is that staffing levels are more often set based on budgets or benchmarking. The Industrial Engineer in me cringes when staffing levels aren't set based on the real work being done.
If there's a lot of waste in the process, that means the work takes longer, which means you need higher staffing levels if safety and quality really are your top concern. As you reduce waste through Lean, you don't need as many labor hours to get the same work done with the same
But, a Lean organization wouldn't lay people off as you improve… that would also be
Safety and quality aren't just slogans at Toyota (or in a Lean culture). They're priorities if not preconditions before everything else.
I mentioned waste — the Japanese word is
When you visit a Toyota factory, you don't see people who are stressed and overburdened. They're working with a purpose, but they aren't running around frantically like Lucy and Ethel in the chocolate factory. People are often afraid that Lean looks like that video. There's nothing Lean about that video, as funny as it is.
To be clear, the Toyota Production System and Lean emphasize that overburden (i.e., understaffing) is bad.
Unfortunately, the word “lean” makes people think of not having enough resources. That's just one of the problems with the word “lean.” Lean is a great methodology, but Lean is a horrible name.
An Accusation Against Lean In the News
It also makes me sad to see a headline like this (from the San Francisco Examiner):
Nurses at ZSFGH alleging understaffing leaves patients at risk
Again, understaffing is bad. I agree that understaffing increases risks to patients (and risks are already high enough due to bad systems, as this recent film discusses).
Also, again, at Toyota or in any Lean setting, the goal is NOT to save money by being understaffed. That would be counterproductive to all of the goals that matter, including safety, quality, service, and morale. Hospitals often claim patient safety is their top priority. If so, why are they so often understaffed?
From the article, it appears something is wrong at Zuckerberg San Francisco General Hospital:
“With union contract bargaining set to begin next month, nurses and other Zuckerberg San Francisco General Hospital workers this week alleged that understaffing and high workloads are placing patients at risk.”
It's quite possible (and wouldn't be surprising) that understaffing and high workloads might be a problem for staff and patients. But, I can't help viewing this through the lens of “union contract bargaining.” How much incentive is there to exaggerate the problem or to criticize anything that management is doing as being bad?
“According to the workers, the hospital's shift to a more “lean” and efficient workflow in recent years has led to chronic understaffing.”
Uh-oh, there's the word “lean.” Are they blaming Lean for this? Has the hospital made understaffing worse in a misguided approach to Lean? I hope not.
Was “chronic understaffing” already a problem?
“Understaffing has long been an issue, said [nurse] Cooper…”
Another point is that Lean is not only focused on efficiency. Lean and the Toyota Production System focus on flow and quality. You can't have good flow and good quality if you're understaffed. That would be a false efficiency.
As I said earlier, I'd agree that this is a problem:
“In the period from October 21,
2018 to January 20,2019, the hospital's day shifts had “16 violations in which they did not provide adequate break coverage,” alleged Norlissa Cooper, a registered nurse… On night shift, Cooper claims that the hospital was out of compliance in regard to adequate break coverage “70 percent of the time.”“
What's more of the context here beyond long-standing understaffing allegations and what might be a contentious union-management relationship?
“Ahead of the move into a new, $1 billion facility at its Potrero Avenue campus, the hospital implemented a new management system, Lean, and electronic record platform, Epic. Workers blamed this change for many of the staffing issues.”
Workers are blaming Lean or Epic? Or both?
Did management “implement” a new management system overnight, like flipping a light switch? No, of course not. This takes time. Has ZSFGH just gotten started with Lean? Are they still in the early stages of practicing Lean?
Is Lean a problem or have things just not been fixed yet through Lean and other approaches?
“Holding up signs that read “Epic + Lean = Racism & Union Busting,” a group of pharmacists and food service workers who rallied in front of the hospital Wednesday alleged that the hospital's implementation of the “Epic” and “Lean” initiatives have kept staffing at minimum, while pushing workers to do more.”
I have no idea
The hospital defined Lean in a way I can appreciate:
“Lean is an “improvement methodology and management system based on the Toyota Management System,” according to a 2014 memo on Lean management at the hospital to the Health Commission's Joint Conference Committee. It is described as an organization's “cultural commitment to applying the scientific method to designing, performing and continuously improving” the work of teams of people.“
How can anybody disagree with that? A staff member says:
“It's based on the Toyota plan where they would design the workflow to be more efficient but at the same time have people do more with less. Less staff, more work,” said Pharmacy Technician John Wadsworth.
That's the thing… Toyota definitely “designs the workflow.” A
You can't just slash staffing levels and assume things will be better. That would be another case of false efficiency. I can't say the hospital is doing that. I hope not. I hope they're working on improving workflows, making work easier, and improving quality and safety.
“Cuttler said that he has been concerned about the hospital's adaption of the Lean quality improvement scheme because “research has not been able to find that Lean improves patient safety or the efficiency of care, patient satisfaction or nurses' satisfaction.”
That's the thing, though. There IS research and evidence, much of which is compiled through the CLEAR center at UC Berkeley. Evidence showing that Lean can work in healthcare doesn't mean that it's going to work everywhere. Not every auto supplier is at Toyota's standard either, even though they all know about Lean and would say they are “implementing it” to some extent.
Cuttler again says:
“Their hope is that [Lean] will ultimately lead to being more efficient and make patients happier, but we are not an assembly line… and speed is not the most important virtue when it comes to safety.”
Lean works in many settings that are not assembly lines. Lean can work well in manufacturing settings that are not assembly lines. Saying “a hospital is not an assembly line” is both a true statement and a red herring.
The other red herring that's also true: Speed is not the most important thing at Toyota. More speed doesn't mean more safety. Lean isn't about “more speed” (again, think to the Lucy and Ethel video — that's not Lean).
It seems the hospital is on the right track if what the spokesperson says is accurate:
“ZSFGH spokesperson Brent Andrew told the San Francisco Examiner on Thursday that Lean is a way to “facilitate better patient-focus, constant improvement in our processes, and greater employee engagement in idea-generation and decision-making,” not “a job-reduction strategy.” He added about Epic that all staff required to use the system will be trained and supported, and that the hospital has communicated that “no one will lose their job because of this effort.”
How can anybody disagree with that? Well, in the context of a contentious labor-management relationship, anything proposed by management is going to be viewed with suspicion or disdain. That's sad… that's not surprising. None of that means that Lean is bad.
Please scroll down (or click) to post a comment. Connect with me on LinkedIn.
Let’s work together to build a culture of continuous improvement and psychological safety. If you're a leader looking to create lasting change—not just projects—I help organizations:
- Engage people at all levels in sustainable improvement
- Shift from fear of mistakes to learning from them
- Apply Lean thinking in practical, people-centered ways
Interested in coaching or a keynote talk? Let’s start a conversation.
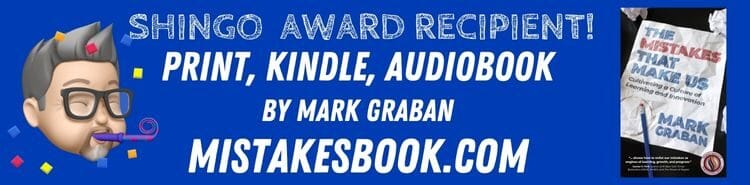
Wow Mark, great post and extremely relevant as of late in healthcare. I too am saddened by the same healthcare problems you have listed. As healthcare has begun switching from fee for service to fee for value, a lot of focus has obviously been placed on becoming more fiscally responsible in terms of productivity, supply costs, etc. What really makes me sad though is that it feels like many health systems are rather quick to invest time and money into benchmarking, data analysis, and reporting to help unearth departments/units with opportunities to improve productivity, but have not invested enough in their managers and front line staff so that they are able to easily identify wastes in their processes and then empowered to make the improvements necessary. What is my fear that ends up happening because of this? Instead of taking the time to improve the processes first, staffing numbers are first reduced to hit target levels, leaving some messy (and potentially unsafe) conditions to clean up later.
Have you by chance ever seen what you feel is a good way to measure safe staffing levels in healthcare? Many staffing models use grids that are not acuity based, meaning day to day fluctuations in the acuity of the patient population can have a big impact on the true nursing demand.
Hi Cory –
I agree that it seems money spent on benchmarking could be better spent on studying and improving the real work — for purposes of improvement, which includes reducing waste AND determining proper staffing levels.
I agree that staffing should be acuity based, since acuity affects the workload. One approach might be to staff not for AVERAGE or expected acuity, but to staff closer to WORST CASE acuity, using “extra” time for better service and more improvement… who is willing to experiment with that approach to see if it delivers better results?
Initial discussion from LinkedIn:
And discussion about this post:
Here is an excerpt from my book “Lean Hospitals” that I shared on LinkedIn: