Listen to Mark read this post (subscribe to the podcast):
This post builds off of a little rant I went on over on LinkedIn. I wrote:
The Catch-22 of “Lean” training and “implementation”…
Executives want big returns and high ROI. That's understandable.
But, at the core of Lean, if you're going to call it that, is “#Kaizen,” which means allowing everybody to do small improvements even if there isn't big ROI.
Encouraging people to make small, simple improvements focused on making their work easier unleashes a huge number of improvements and, guess what, some will end up having a big ROI. The executives would be surprised. Plus, the cumulative effect of many small ideas is larger than what you get from demanding a few high-impact ideas.
The counterintuitive thing is that you get *better* results by not demanding a huge ROI for each improvement or project. Studies have consistently shown that 80% of an organization's improvement potential comes from the small stuff. Yet, executives are ignorant to that truth or choose to ignore it.
You can, of course, choose to focus on big projects that you think will have big ROI. But call your approach “improvement projects,” not #Lean.
Here's a Toyota article on Kaizen. They don't talk about ROI.
“Within the Toyota Production System, Kaizen humanises the workplace, empowering individual members to identify areas for improvement and suggest practical solutions. The focused activity surrounding this solution is often referred to as a kaizen blitz, while it is the responsibility of each member to adopt the improved standardised procedure and eliminate waste from within the local environment.”
Quite a contrast to a hospital executive team telling people to only focus on high-ROI projects.
You can hear Alan Robinson talk about the “80%” finding that they uncovered in this podcast, where he talks about his latest book, The Idea-Driven Organization.
And Joe Swartz and I, of course, wrote about this in our Healthcare Kaizen books.
Here is a perspective from Kaizen Institute:
“Deming was basically saying, “go ahead, compute an ROI for your Continuous Improvement projects and for your client's projects, but it won't matter too much because it will be greatly underestimated and this must be realized.” Dr. Toyoda supported this as he said Deming and his beliefs are the core of Toyota's management …. not an ROI analysis.”
It's frustrating that hospital executives will call for “evidence-based medicine,” but then so blindly ignore “evidence-based leadership” (credit to Studer Group for that phrase).
This large-ROI approach should be called “project-based improvement attempts” instead of Lean.
Of course, it's not just hospital executives who make this mistake of ignoring the potential of many many small improvements.
Please scroll down (or click) to post a comment. Connect with me on LinkedIn.
Let’s work together to build a culture of continuous improvement and psychological safety. If you're a leader looking to create lasting change—not just projects—I help organizations:
- Engage people at all levels in sustainable improvement
- Shift from fear of mistakes to learning from them
- Apply Lean thinking in practical, people-centered ways
Interested in coaching or a keynote talk? Let’s start a conversation.
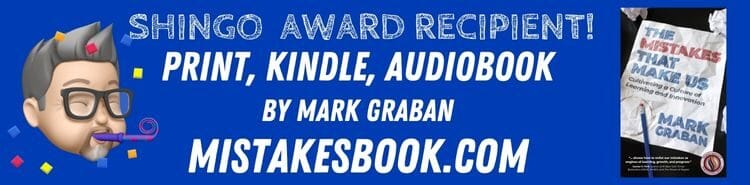
The original LinkedIn rant if you want to comment there:
Andre De Merchant (former Toyota Canada):
Tracy Richardson (former Toyota Kentucky):
I had an interesting conversation with a Theory of Constraints disciple about a similar theme a few years ago. He was pointing out how useless it was to do process improvement in areas that are not *the one* bottleneck of the factory.
And of course, I took issue with it. After a bit of discussion, I recall he finally conceded when I pointed out that as constraints moved through the factory, it was always useful to have a team trained and ready to respond to them. And this, of course, is what lean does. It creates the fundamental problem solving skills *throughout* the operations to respond to short-term disruptions that might introduce temporary bottlenecks as well as the long-term systemic bottlenecks.
This is consistent with my experience at Toyota. When I was interviewing at another company, I told them about how an A3 that I facilitated reduced the top supplier-related parts defect at the plant by over 75%. The interviewer asked how much cost savings that translated to, and I had no idea, although I estimate it’s in the hundreds of thousands of dollars range. In my entire time working in Quality Engineering at Toyota, cost savings was never mentioned. The primary metric was DPV (defects per vehicle) which drove our focus on protecting our customers and delivering high quality vehicles. Great post!