I've heard a lot of rumblings recently about what might be happening at ThedaCare, a health system in Wisconsin that's been considered one of the best examples of “Lean healthcare” anywhere in the world for more than a decade. It seems that there is an evolution occurring in their approach to Lean.
I've received a formal statement from ThedaCare public relations, which you can find in this post, so I will stick to the facts that they have given me and other information that's publicly available online.
My History with ThedaCare
I've never worked there (as an employee or as a consultant), but I've visited ThedaCare many times over the past nine years. I've been impressed with much of what I've seen at “the gemba” of various care delivery sites and departments, their “visual room,” and their famed “weekly report outs” of Rapid Improvement Events.
In 2010, I helped produce an instructional DVD about their “strategy deployment” approach and management system. I added new material to the third edition of my book Lean Hospitals based on what I had learned about their management system over time, supplemented with a site visit they hosted for me in 2015.
As a faculty member for Catalysis (formerly the ThedaCare Center for Healthcare Value), I have a lot of vested interests (if not conflicts of interest) in this story. It's probably in my best interests to focus only on the positive, but I've been doing my best to figure out the real reality.
What do we know about ThedaCare?
The new CEO has expressed an admiration for ThedaCare and their approach to Lean.
Fact: They have a new CEO, Dr. Imran Andrabi, who was hired from another health system in 2017 (release)
Fact: ThedaCare said the three finalists for the job were all outsiders (release)
Fact: By comparison, at least the last two ThedaCare CEOs (Dr. Toussaint and Dr. Gruner) had been internal promotions.
Fact: When hired, Dr. Andrabi expressed his long-standing admiration for ThedaCare's Lean journey (article)
What led you to ThedaCare?
“Back in 2007-2008, I was doing some work in lean (practices) at our institution in Toledo. As I was looking around with respect to other health systems that were doing that kind of work, I found ThedaCare.
At that time, ThedaCare was really front and center with respect to using the lean methodology within health care. I ended up sending a few teams of folks from Mercy to ThedaCare to learn what ThedaCare was doing and actually brought some of those learnings back to Mercy. “
The retired CEO talked about some challenges they've faced in the past few years.
Fact: Retired CEO Dr. Dean Gruner said, in my podcast with him after his retirement, that ThedaCare had run into problems with Lean in recent years:
“We believe that we, at a certain point, started to read too many of our own press clippings. We stopped studying what was really going on.”
When the former head of the ThedaCare Improvement System, John Poole, left the organization in 2015, Gruner started studying what was going on. Gruner said:
“[What employees] drew was a picture of an organization that had become very hierarchical and required approval from senior leaders to do things.
It had become an organization that was very dependent on facilitators to do improvement work, and an organization that had become much more inflexible and more rigid than we ever had imagined. All those things are exactly the opposite of what you intend to do with Lean.
We looked at ourselves and said, “How did this happen? We've been doing this for 12 years, we got everybody who comes here and tells us how great we are.”
One of the answers was we hadn't sat down and looked in the mirror really thoughtfully for several years. This had happened gradually. Maybe it's akin to the boiled frog metaphor. We didn't really think it through.”
Gruner also quoted Michael Hoseus, co-author of Toyota Culture as saying:
“The most common mistakes implementing Lean is thinking that Lean is a set of tools to be delegated to some Lean champions to implement, while leaders go around running the business as usual.”
Gruner said:
“I would say we made some of the mistakes that they reference there. We developed a group of ThedaCare improvement system facilitators to do the improvement work throughout our organization.”
He added:
“I would say that Lean really sped our improvement journey for a bunch of years. Then, probably, for a couple years the feedback is it might have actually slowed our rate of improvement for a couple years because we were learning some difficult lessons.
Now that we think we've learned these lessons, we think we're back accelerating again, and stuff. That's why they call it learning and why they call it work. It's not like it's easy, or anybody would do it, right?”
Gruner ended the podcast by saying they had learned from their reflections and he was positive about the future.
What Comes Next?
At the very least, ThedaCare has decided to rely less on the “Lean facilitator” role.
Fact: The “lean facilitator” group at ThedaCare has been reduced in size in recent years from over 20 to just 7 people, which included a director of operational excellence. Those seven were all recently terminated by ThedaCare.
Questions: This seems to signal a change in approach. It's unclear what that future direction is. Does ThedaCare continue their Lean improvement approach and Lean management system without having a central group? Are they far enough along on their journey to not need a central group?
Random Fact: As I blogged about, Toyota recently announced they are centralizing their TPS group, which is 200 people strong (article)
“The automaker last month created a single group, staffed with 200 employees, to manage the Toyota Production System, centralizing a function that was spread out through the organization.”
Questions: Does this mean “the end of Lean” at ThedaCare or is it just a shift in approach? Are Dr. Andrabi's actions that much different than what Dr. Gruner and his team would have done if he had not retired?
Asking ThedaCare Some Questions
I asked the public relations person at ThedaCare a number of questions via email. It seemed like the right thing to do, to get their reactions and statement instead of just speculating.
I asked her:
- Have ThedaCare lean facilitators been fired? If so, why?
- Is ThedaCare, under the new CEO, shifting away from a focus on Lean to another strategy for process improvement?
- What happens with the ThedaCare management system that has former executives have written about in recent years?
- Have 2017 margins or financial data been made publicly available yet?
Here is the response I got from ThedaCare:
“ThedaCare is committed to our mission of improving the health of the communities we serve by ensuring world-class outcomes and a strong future for our organization. We recently removed the centralized function specific to continuous improvement. As we go forward on our continuous improvement journey, we will be training team members, embedding best practices, and further empowering leaders to use rapid-cycle, results-oriented improvement and problem solving in our daily work.
ThedaCare is strong and will become stronger as we further enhance best-in-class access to expert, local care.”
So, ThedaCare confirmed the layoffs of the remaining Lean facilitators.
Notable in the statement are the things they did not say. The word “Lean” is not used once. The statement did not address the future of the management system… it spoke of training, team members, and problem solving.
It's unclear if ThedaCare's Lean management system, including the strategy deployment process or the daily management system (as documented in the book Beyond Heroes) remains in some form.
Concluding Thoughts
For what it's worth, I hope ThedaCare finds a path forward that provides the right care, the safest care, the most cost-effective care in a workplace that's engaging and stable for people.
I hope they can continue to be on the leading edge of Lean practice and that they find a way to continue improving their approach to improvement.
Please scroll down (or click) to post a comment. Connect with me on LinkedIn.
Let’s work together to build a culture of continuous improvement and psychological safety. If you're a leader looking to create lasting change—not just projects—I help organizations:
- Engage people at all levels in sustainable improvement
- Shift from fear of mistakes to learning from them
- Apply Lean thinking in practical, people-centered ways
Interested in coaching or a keynote talk? Let’s start a conversation.
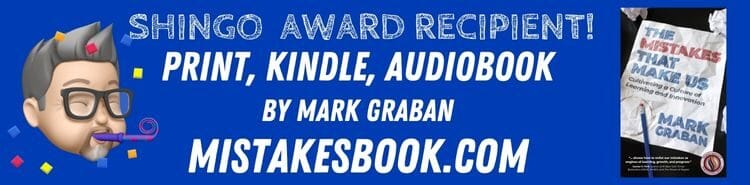
Thedacare Regional Medical Center in Appleton doesn’t perform well for clinical quality (21st percentile for HAC’s, 13th for VBP, and 12th for Serious Complication Rate nationally). That’s well below average. HealthGrades also shows them as having zero safety indicators better than expected (12 as expected and 1 worse than expected). This isn’t a recent development as their quality scores and CMS penalties have gotten progressively worse since 2015 (pre-dating CEO changes).
This isn’t to disparage ThedaCare. They also score pretty well in HCAHPS and All Cause Readmits. But it just shows there are no easy answers.
If your point is that ThedaCare is not the country’s best-performing hospital, that’s a fair point. I’d hope that they would find ways to tweak their approach to Lean (and other methods) that can make them a peak performer.
Sad, if reality tends to become what can be read through the lines. Lean efforts can quickly go to just program delivery, cutting out the learning about critical thinking, humble inquiry (an approach favored by former MIT professor Edgar Schein from whom I learned about ThedaCare during a workshop in 2009) and applying the scientific method to the complex processes in a hospital (a hospital is way more complex than a car manufacturing plant, for sure as I can tell)
Based on the response you got from ThedaCare some of the tone sounds like they are shifting to daily kaizen? “…and further empowering leaders to use rapid-cycles, results-oriented improvements and problem solving in our daily work.” However, I too am curious about the state of ThedaCare’s Lean Management System as outlined in Beyond Heroes.
I hope what they are describing is an evolution of “daily kaizen.”
ThedaCare had already, years ago, shifted away from a Rapid Improvement Event-heavy model to one where they expected that 80% of improvement benefit would come from small kaizen. That daily / small kaizen approach was part of their Lean Management System.
Dean Gruner’s comments say a lot. The role, structure, and goals of a central improvement team determine a lot about how improvement is delivered, perceived, and sustained. I’ve had personal experience at each end of the “ownership” spectrum as a central improvement resource. My personal opinion : if the central improvement team is accountable for operational improvement results (rather than operational leaders being accountable), a whole host of unhelpful behaviours follow. There’s no one right way – but there’s some predictably ugly ways.
This took my totally by surprise. As a lean practitioner in a great healthcare organization, Thedacare was one of the models I looked up to. Let’s humbly reserve judgement and wait to see what comes out. We have to respect that the people at Thedacare who do the work of providing safe, quality, effective, timely, and patient-centered care, know what is best to improve their work.
As a 10 year Lean Healthcare “Sensei” with prior 23 years of Fortune 500 experience i was just released from a 13,000 employee health system after a successful 5 year deployment. The reason “my style does not fit the culture”. I wonder what that actually means? Healthcare is in the “it’s not you, it’s me phase”.
Lots of discussion on LinkedIn:
ThedaCare has been an inspiration for me as well, as I was just developing as a lean coach around the time On the Mend was published. When I visited ThedaCare on a site visit with health system execs in 2013, the strongest statement for lean in healthcare we came away with was the feeling that it had genuinely become part of the culture in regular, every day staff. We observed nurses and other staff (not lean coaches) running daily huddles and reviewing improvements and methods at the gemba and in their weekly report out. Much more than their strategy room or other high level presentations we heard, it was that sense that it had taken hold with staff and was a positive in their culture, that convinced us to take some big steps forward in our lean journey. It’s hard to tell what’s really going on by reading between the lines, but the quotes don’t sound good. If there has been a revolt, I wonder if it came from staff, senior leaders, or the middle?
Just to add an update…
https://www.beckershospitalreview.com/finance/5-recent-hospital-health-system-outlook-and-credit-rating-actions-8-24-18.html
coupled with this….
https://health.usnews.com/best-hospitals/area/wi/appleton-medical-center-6450045
Their clinical performance is not significantly worse or better than it has been any time over the last 15 years. If it’s substantial investments in Lean over that same time period haven’t moved needles that really matter, should we be surprised that leadership is going in a different direction?
If we objectively look at their actual clinical performance since the early 2000’s, its difficult to see any sustained performance benefit proportional to their lean investment aside from some local optimization.
Real healthcare transformation is hard and takes more than even the most rigorous Lean engagement. The reality of ThedaCare should reinforce that.
Yes, it’s terribly hard. ThedaCare was doing far more than “the most rigorous Lean engagement” in that timeframe too. They made many changes.
If you were to step back and look at the organizations that have improved their safety and quality results the most, what are the most effective organizational countermeasures or strategies?
Intermountain Health drove a lot of process discipline around clinical variation reduction. Defined and executed consistent clinical protocols. Focused on really effective data collection and analysis strategy to both continuously improve those protocols and optimize reimbursement. They certainly supplemented that work with Lean, but they transformed mostly through clinical variation reduction and care pathway implementation.
They’re not the only example, but they continue to drive great outcomes consider their relatively high Medicare/Medicaid population.
I generally have one standard that I measure hospitals against – would I want someone I cared about to be treated there? Intermountain Health definitely checks that box.
You should revisit this. The hospital is a mess. Vast quantities of physicians have left and the system is relying on locums. Ortho is down to only 2 doctors at the main hospitals. Every cardiologist left, including their staff of 70 some employees. Quality of care is negligent in many cases. It’s sad.
lean is innate, all this “lean management” and army of consultants and facilitators who mostly no nothing about taking care of patients (the prime directive) equate to BLOAT, not LEAN
Just wondering if anyone has a further update on this topic. I’m curious to know whether Thedacare’s Lean Journey continues in some form or if it has essentially ended.
Thank you.
I have not heard anything positive about Lean at ThedaCare in a few years.