Listen to today's post (subscribe to the podcast):
A few of you sent me this sad article from the Wall St. Journal:
‘People Are Dying Here': Federal Hospitals Fail Tribes.
By the way, if you ever see something that you think I'd like to cover here on the blog, please contact me via this form, Twitter, or LinkedIn.
I feel like I've some variation of this article and exposé many times over. Sometimes, it's some form of government medicine (active duty military medicine, the VA, or another country) or it's a similar sad story from the private healthcare sector (be it non-profit or for-profit).
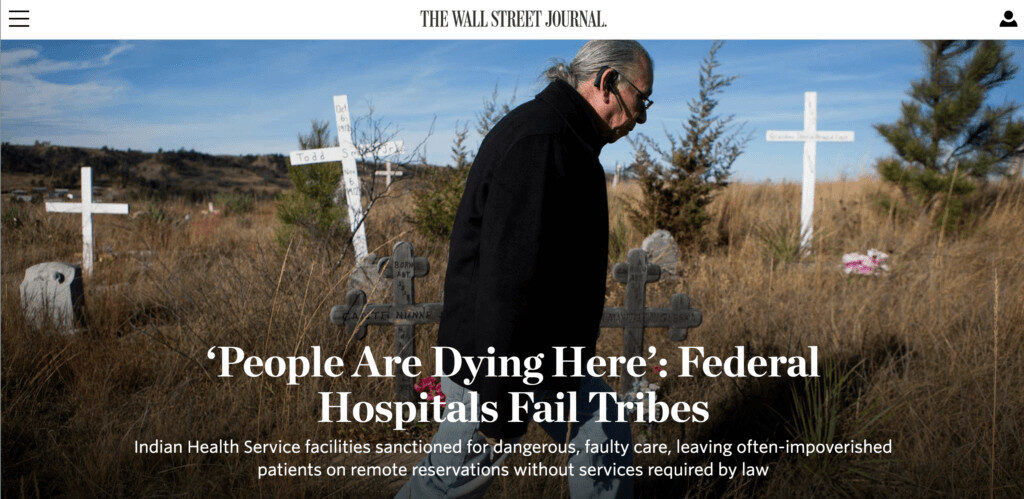
I shared just one line from the article via Twitter and got a a response from John Gallagher of Simpler:
Solutions are so simple #5S This is a leadership issue, though…not so simple
— John Gallagher (@John_Gallagher) July 10, 2017
Here is the full scenario that wouldn't fit in a tweet:
At the Indian Health Service (IHS)… a patient at the federal agency's Winnebago, Neb., facility stopped breathing, nurses responding to the “code blue” found the emergency supply cart was empty, and the man died.
Now, was the “crash cart” empty or just missing some key supply or medication? I've never seen a cart that was completely “empty” — that would be a shockingly bad dereliction of duty (or bad process). But, I have seen crash carts that are not fully stocked.
Page 58 of the detailed report says “they could not locate any emergency resuscitation equipment on the crash cart.” A nurse was sent to the ED to get a “combitube,” but “the nurse returned with the wrong equipment” so (with the clock ticking), they were sent back to get the right item. If I read the report right, that led to a 20-MINUTE DELAY to get the airway opened after the Code Blue was called.
Why was the item not there?
There often isn't an air-tight process for who restocks what and when (and in what quantities).
The crash carts are sometimes not organized well, so you can't see visually if everything is there or if anything is missing. Or, supplies aren't always kept in the same location within the cart, so it takes longer to find items… and that can be a matter of life or death.
That's where the question or issue of “5S” as a Lean practice comes into play, as John points out.
But as John implied, is the solution really that simple? I'll give John the benefit of the doubt that he was working within the limits of 140 characters. Yes, 5S is a simple method. Yes, you need leadership. But, you'd also need related processes for restocking and verifying that everything is there. You'd need “standardized work” for checking to make sure medications aren't expired.
On the leadership front, you'd also need some diligence amongst leaders to make sure processes are being followed — and if they are not, to ask “why?” instead of “naming, blaming, and shaming.”
I shared a similar case study in Lean Hospitals about suction tubing being missing from a private children's hospital in the U.S.
Here is the first part of that, screen grabbed from the Amazon listing for the book. You can probably read pages 145 and 146 by going to the Amazon page, clicking “Look Inside!” and searching for “suction.”
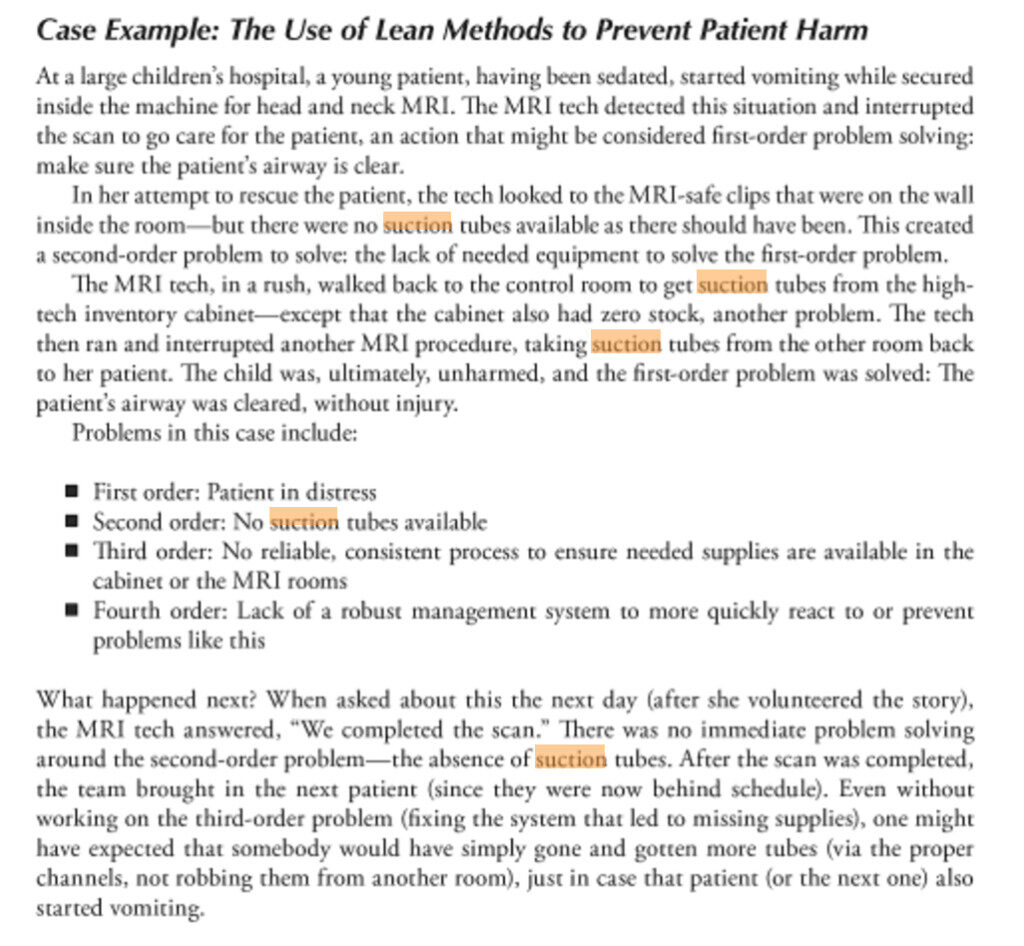
As I said on page 146, it's not as simple as blaming one of the employees working in the area, whether it's the MRI or the IHS facility and its crash cart. Everybody works in a system.
We can ask why the IHS crash cart was “empty.”
We could react and take action by sending in a federally-funded 5S tiger team to go and organize, label, and fully stock the crash carts using 5S, visual management, and such.
The carts might look like some that I've seen in Japan, as I've blogged about before:
The preview photo (click to view it directly) from the post shows a meticulously organized crash cart in a Japanese hospital.
We could have labels… foam cutouts… everything stocked to look like that reference. But that might be just a one-time fix. Would an urgent effort around “fixing the carts” really improve the system? Should we be fixing the carts or teaching people how to improve? Or maybe doing both.
We would do better to make sure there are systems in place over time to:
- Sustain the improved crash cart (making sure it stays stocked and organized)
- Improve the crash cart over time
Improving systems takes more time and effort than “doing 5S” (and, again, I'm not criticizing Mike Gallagher or saying he said to just do 5S… his tweet provoked the thought that led to this post, so I thank him for that).
We also need to think about culture, as I wrote about in the suction tube case study.
I'd hope that IHS looks deeper than that crash cart. That crash cart is probably just a symptom. What are the root causes? I hope they'd conclude that it's about process, culture, and leadership rather than just blaming lack of funding or lack of staffing (although lack of staffing can be caused by culture and broken processes, not just the geographical isolation that makes it difficult for the IHS).
Why did people not speak up about the missing item(s) in the crash cart? Did they not know? If not, why? Did they not check the carts? Did they have an unclear standard?
If somebody knew about the problems (likely, I'd guess), did they speak up? Maybe they spoke up and didn't get the right support. Maybe they didn't speak up out of fear or “futility.”
In the WSJ article, it talks about fear:
One doctor, Alida Asencio, said she was ridiculed at staff meetings after telling the Winnebago medical director about problems in 2014. Dr. Asencio later raised a concern about a death at the hospital with regulators, who, documents show, concluded it was avoidable. She later complained to top agency officials that her supervisor pressured her to take paid leave ahead of an inspection to keep her from raising further concerns, an email viewed by the Journal shows.
Yet, leaders there claim they want people to speak up:
The agency said its “leadership maintains a culture where employees are encouraged and expected to report any reasonable suspicion of wrongdoing, misconduct, waste, or abuse, particularly when it involves the safety and wellbeing of patients or employees.” It said such disclosures can “save lives.”
As with continuous improvement or patient safety, it's easier to talk the talk than it is to walk the walk.
What's necessary to create a process-focused culture where people feel safe to speak up and then get the right supportive and empowering response from leadership?
That's more difficult than organizing a cart. But, it's important work that needs to be done.
Other excerpts from the WSJ article:
The problems have come to a head in recent months after IHS hospitals repeatedly failed inspections, shut down services or lost access to crucial federal funds.
Why do things not get fixed after “failed” inspections?
The latest crisis has arisen after the IHS and the Health Department failed to address a chorus of warnings over many years about neglect at the agency's facilities. The warnings came from lawmakers in both parties, internal whistleblowers and the families of patients who died. Over and over, they reported that IHS hospitals were plagued by inadequate supplies, poor training, overwhelmed staff and critical positions left unfilled.
Is “inadequate supplies” due to lack of funding or bad processes? Or do unfilled positions and “overwhelmed staff” help create that problem? How can the IHS work to reduce waste so that staff and leaders are less overwhelmed? Is that fixable?
What's the leadership response?
Rear Adm. Michael D. Weahkee, the agency's current acting director, said in a statement after this article was published online, “IHS is committed to improving patient safety and the quality of health care across the agency. We are faced with many challenges, but that is no excuse for substandard care.” He said the agency is “holding all employees fully accountable and working to improve the systems that recruit, retain, and support those employees to meet standards.”
As I've blogged about before, it's easy to say things like “patient safety is always our top priority.” I also cringe and hope that the common expression of “hold employees accountable” includes leaders… ALL employees… and not just blaming or punishing people, as I've also written about a lot, including here:
Here's a link to the inspection reports (all 210 pages) if you'd like to dig deeper. What else do you see in those reports?
For one, it says:
The South Dakota and Nebraska facilities have each been cited for putting patients in danger multiple times. Since 2011, regulators reviewing cases at those four IHS hospitals said inadequate care contributed to at least 11 deaths, documents show.
Do citations fix anything? Apparently not…
Upon learning of these survey results IHS immediately began instituting improvements at each hospital.”
I hope that's the case. I hope they are getting results, now and/or in the future. The patients and staff deserve better.
Please scroll down (or click) to post a comment. Connect with me on LinkedIn.
Let’s work together to build a culture of continuous improvement and psychological safety. If you're a leader looking to create lasting change—not just projects—I help organizations:
- Engage people at all levels in sustainable improvement
- Shift from fear of mistakes to learning from them
- Apply Lean thinking in practical, people-centered ways
Interested in coaching or a keynote talk? Let’s start a conversation.
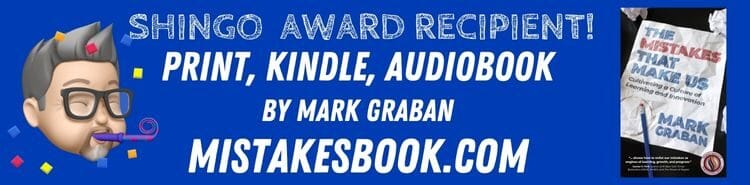