Back in 2015, my frustration over finding so many empty hand-sanitizer dispensers in my hospital visits led to me writing this blog post where I brainstormed the idea of a “two-bin” system for dispensers, since two-bin kanban systems are a simple, yet effective, method for making sure hospitals don't run out of supplies in other settings.
Here is a past post of mine that shares a video from a health system in Pennsylvania:
Kanban systems, with bins or without, are also effective in a veterinary medicine setting, as my friend Chip Ponsford, DVM blogged about just the other day. Here is a photo from a clinic he helped:
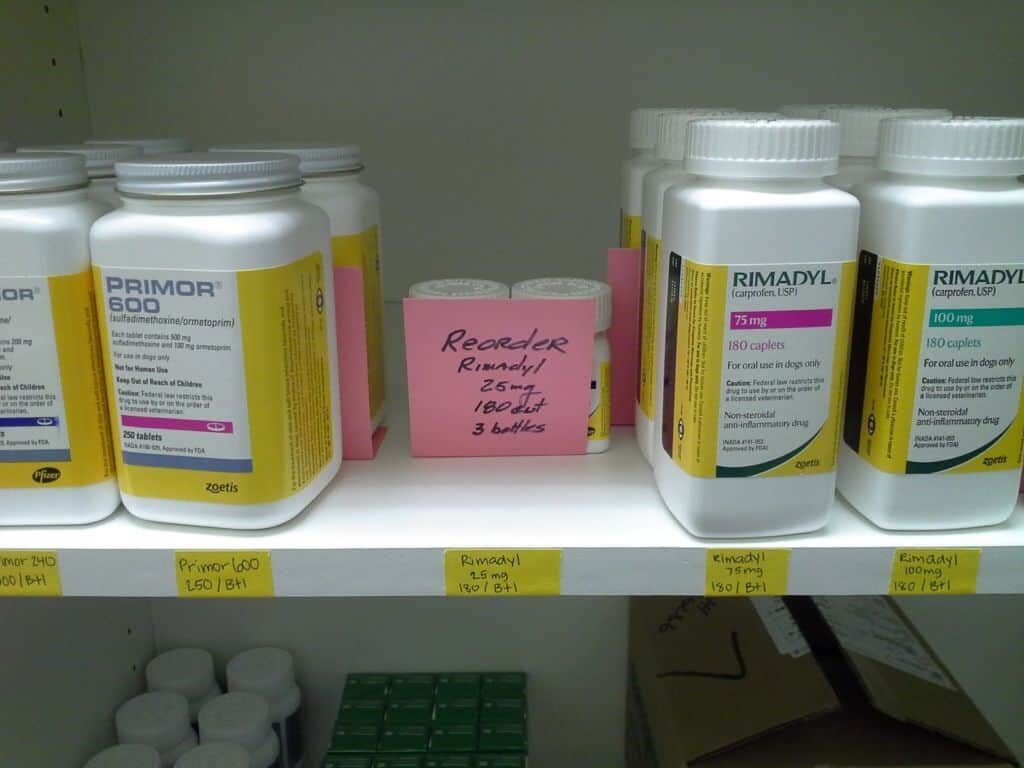
Anyway, here was my post about applying this concept of kanban systems to hand sanitizer and the important issue of hand hygiene:
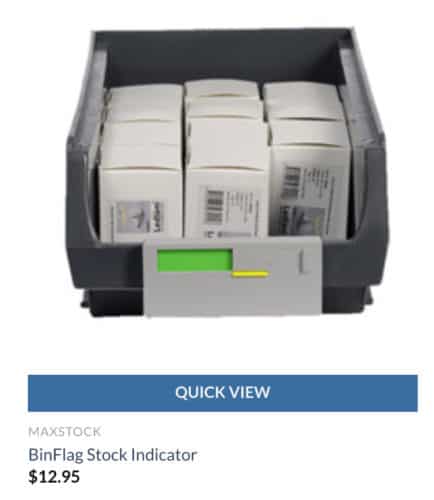
I offered to let any company run with the idea and I finally got some interest from Spencer Fullerton from Maxpert Medical, which makes a number of products, including different devices that create visual signals for when to restock supplies, such as this “Bin Flag” stock indicator that attaches to the front of a supply bin (shown at left).
That's clever, although I'd generally challenge a team to first try creating a visual signal that doesn't require somebody to manually move a slider over. Two-bin kanban systems are great in this regard because the empty bin is a simple, automatic, binary signal that says it's time to replenish something.
We traded emails, which led to Spencer creating a mockup and a prototype of such a device… and I asked him to write about it. Here's what he wrote…
Hear Mark read this post (subscribe to the podcast):
“Two Bin” System for Hand Sanitizer Dispensers Anyone?
By Spencer Fullerton, Maxpert Medical
Common and annoying.
These two words describe what happens when you walk into a medical center and go to the hand sanitizer dispenser on the wall to follow proper hand hygiene and then low and behold nothing comes out of the dispenser.
Yes, it is empty.
It happens all too often, making it common and it is annoying because the purpose of having dispensers strategically placed is to follow precautions and ensure clean hands. With emphasis on infection prevention and hand washing being a key factor, it would make sense to always have hand sanitizer available when needed.
Employees in some facilities rely heavily on sanitizer dispensers as they come and go through different areas and in and out of patient rooms. With hand hygiene compliance being a key factor in any infection prevention program, it is critical that employees have hand sanitizer available when needed. Otherwise, they might skip this step because they have tried the dispenser to find it empty and do not have the time to go to another area to sanitize their hands.
Visitors are also affected. There are many signs and stations around the hospital encouraging them to use hand sanitizer from one of the many dispensers — especially during flu season. Again, when the dispenser is empty, the rate of compliance goes way down because people may not search for the next and decide it's OK to not sanitize their hands.
What to do?
There are some really good systems in hospitals for ensuring supplies are available for patient care when needed. One highly effective system is a “two bin” supply system in which Items are consistently stocked from the back, using the First-In-First-Out (“FIFO”) approach. When the first bin runs out, the employee who uses the last item places the empty bin in a common area. Then, the label on that bin is scanned the same day, activating a new order of supplies that will fill up that bin. While the team waits for the new supplies to arrive, there's still another full bin on the shelf — it's been there waiting behind the previous bin — and it's ready for the next employee who walks in. When the new supplies arrive, they're placed in the empty bin, and the bin filled with new supplies is stocked behind the current bin.
With such a system, the supplies are available when needed. This helps make the organization's employees have trust in a system that gives them what they need, when they need it.
What if the ‘two bin” approach was used for hand sanitizer dispensers?
Imagine for a moment a small cabinet system in which two dispensers were mounted side by side, one active and one reserve. The reserve would have a sliding door covering it so the active dispenser would be used until out of sanitizer.
Once the active hand sanitizer dispenser has been depleted, you'd simply slide the door across to access the reserve dispenser, leaving the first dispenser ready to be replaced with new stock.
Even better is that, when you slide the door to access the reserve stock, a TripFlag turns from green to red indicating that reorder is necessary, as pictured below in this concept mockup:
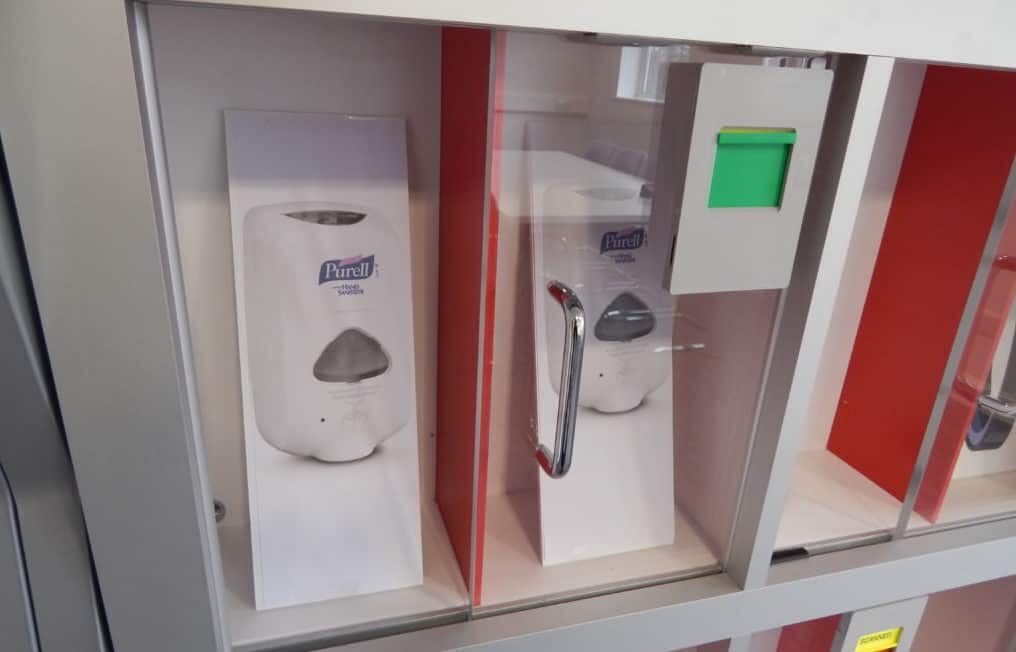
Now if you've activated the TripFlag, each dispenser that is empty around the hospital is easily identified, yet they have reserve supply to use. Once the appropriate personnel see the red flag and reorder, they flip the red flag to a yellow flag to alert everyone that the new sanitizer has been ordered. When the sanitizer refill is brought to the dispenser and it is ready for use again, the TripFlag can be turned back to green indicating all systems are good to use.
So, common and annoying are words that can be removed from the conversation when speaking about hand sanitizer dispensers. This simple concept could not only eliminate aggravation but support infection prevention practices that start with clean hands.
As a company, we feel we are in a position to solve challenges with creative products. We see that hand sanitizer availability is important in today's world and we could potentially offer a solution if users feel like it is a big enough challenge that calls for a solution.
We wish to share with hospitals and other medical facilities that we have simple products that will aid in their process improvements and goals toward lean healthcare. Maxpert would be interested in providing a product solution for the market. Our interest would be a cabinet and indicator flag system.
What do you think of this concept? Would you consider using a “two-bin” approach to hand sanitizer in your hospital?
The tweak I would make, from what's shown in the video above is that I'd follow this process:
- If the left dispenser is empty, slide the cover left to expose the right dispenser (which is full)
- Flip the indicator to be red, meaning it needs to be filled
- Within a daily cycle, materials management / supply chain would see the red and either
- Refill it and move the indicator green (if they're roaming with canisters)
- Signal that it needs refilling and move the indicator to yellow (meaning it's on order) and then refill it during the next delivery cycle
- When the empty is refilled, keep using the “active” dispenser until it's empty and then slide the door over to cover the empty one, exposing the full container
If you don't think this approach would work, do you have other solutions to this problem that you'd share with fellow LeanBlog.org readers?
Please scroll down (or click) to post a comment. Connect with me on LinkedIn.
Let’s work together to build a culture of continuous improvement and psychological safety. If you're a leader looking to create lasting change—not just projects—I help organizations:
- Engage people at all levels in sustainable improvement
- Shift from fear of mistakes to learning from them
- Apply Lean thinking in practical, people-centered ways
Interested in coaching or a keynote talk? Let’s start a conversation.
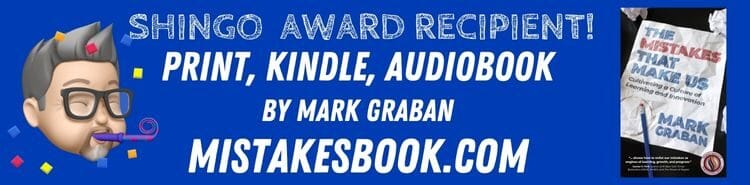
Here is LinkedIn discussion activity:
Yvan Lévesque
Great Kanban that really make a difference in reducing nosocomial infections that can become the standard in all health center,!! On my last visit to a Montreal hospital, I did test 11 dispensers out of which 7 were empty ?. Simple but effective !! ?? ?????
My reply:
That’s not surprising about the dispensers. Right now, this prototype is just a hypothesis. I’d love to help somebody design and test the process around something like this.
Yvan Lévesque
Wish this can earn some traction with MUHC managers during my Lean Healthcare course at McGill this Fall
More from LinkedIn:
Brock Goodrick
Fantastic idea! As a healthcare life safety professional, I encounter this issue all too often. That being said, effectively doubling the number of alcohol-based dispensers would cause some life safety deficiencies.
My reply: I’m not sure how that causes a safety problem to have more sanitizer dispensers. Fire risk? That seems trivial compared to the known problem of infections.
Trevor Waldo
Great idea Mark Graban and excellent post
– the root cause of why your solution is necessary = the makers of the dispensers have not successfully integrated effective visual controls that make it obvious when the dispenser is low or empty. A full canister looks just like an empty one. Dispenser maker challenge: solve that problem and take over the market by setting the standard.
– the dispensers that have a mechanism to dispense without physically touching them are inherently “safer” than those which require a physical push or pull. The surface of those levers, as you can imagine, contain millions of nasty particles from pre-wash hands… Some of which can be “immune” to the effects of the alcohol based solution contained within. Even when it’s full you could be walking away with more germs than you had before touching it, this effect is way worse when it’s empty.
My reply:
Great point about the design of the dispenser or canister itself. Of the main styles I see out there, they all look the same when full, empty, or half full.
Good point about the need for hands free dispensers. If it’s good for soap in the bathroom, why not here?
These are solvable problems. It’s not curing cancer here.
More from LinkedIn:
Sonia K. Singh
Mark Graban From my understanding, there is a safety concern with the amount of alcohol in a specific sq footage of a space (fire hazard?). That’s why hospitals have to limit the number of gel dispensers in a given area and have to be strategic about placement to optimize limited space.
Mark Graban
OK, then hospitals need to find another way to keep the dispensers from being empty. The risk and actual harm of infections seems to FAR outweigh fire risk. If this were an actual discussion in a hospital, I’d ask somebody to point me to the exact regulation (which might vary from state to state and might be misunderstood). https://www.rjschinner.com/linked-files/videos/FireCode.pdf
How close can the ABHR dispensers be to each other?
Dispensers shall be separated from each other by horizontal spacing of not less than
48 inches (1220 mm).
Well, that seems to cause a problem. What about putting them vertically above and below each other then? ;-)
Just a thought, but according to me, however beautiful the design and the replacement or indicating method you may design, non of this will help if the visual designs aren’t picked up by the staff who’s task it is to refill. Additionally, unless you want to develop a system where a warning light goes off any time someone uses the last bit, the refill will only take place when someone checks the visual indicator, whatever this may be. This will normally only be done at standard times. So wouldn’t an easier solution be to let the colleagues who’re responsible for filling up the dispensers, use every dispenser when they pass by during their normal daily routine (for instance as part of the tour of the cleaning staff) and maybe even letting them keep track of when they refilled? By doing it this way you could engage them as ambassadors for clean hands, and by using this themselves they will immediatly be able to see whether there’s still enough left in the container. Additionally, when you would notice that there is a lot more time of needed refills then normally, you could use this as an indicator that maybe the discipline of washing your hands is slipping or the usefullness of this is getting less well known with visitors. Of course the latter option includes extra work but taken from the point of view of a need for hygiëne this wouldn’t necessarely have to be considered waste I think.
What do you think?
Thanks for your comment, Bart.
Yes, even a 2-bin system requires some good process and standardized work around it.
Who is responsible for replacing empty containers? How often do they go around in a route looking for the signals? Do they carry kanban signals back with them, scan a bar code, or have a rolling cart with full canisters that allows them to replace an empty canister immediately? If each canister typically holds a week’s worth of sanitizer, then is a weekly route enough? Those are the types of details we’d have to sort out.
I think if “everybody” is responsible, then nobody is…
One other thought… there’s all sorts of data that could be collected. But, that would require a lot of work.
I propose the two-bin approach because, if it doesn’t violate fire codes, I think it’s the simplest approach that would work… guaranteeing that you never have a lack of hand sanitizer at any given location.
I’m open to other solutions… I’d love to hear from others who have solved this problem in other ways, because what I really care about is solving the problem.
Enjoying the discussion. I think the idea is great, but suggest trying to design this in such a way that it doesn’t take up twice as much space on the wall. Same receptacle but with two bags of solution inside; when one empties the 2nd bag is opened, and the same flag flip approach visually indicates a replacement is needed, to notify materials managers on daily rounds to replace it. I’m not a mechanical engineer so I can’t design the mechanics of how this would work in a semi-automated fashion, but it would be visually and functionally less obtrusive than doubling the wall space taken.
That’s brilliant. A dispenser could be designed so instead of one large container, there’s two side by side.
You’d need a mechanism to switch the pump flow from one container to the other… and you’d need a way of visualizing when one side is empty.
Hope fully two bags or containers within one dispenser doesn’t run afoul of fire code.
Here’s a picture of the insides of one dispenser with its single container via this YouTube video:
Great idea about the need for a 2 bin system for hand sanitizer. The cabinet idea is great too. Seems like there is a huge opportunity here for tens of thousands of systems and it would be worthwhile designing a purpose built dispenser.
Your cabinet idea is excellent but large and might be confusing to some. Not hospital staff but I am thinking of visitors and patients.
Automation is in my blood and I always prefer automation.
How about a double bag dispenser? You would have one dispenser with two bags of sanitizer back to back. The discharge nozzles would be side by side with a single lever to push. The user would not know there were two bags.
A sensor would monitor the bags. The dispensing lever would dispense from bag A until it is empty. When empty, bag B would automatically start dispensing when the lever is pressed.
When a bag is empty, a red LED would come on to indicate that it needs service.
Someone would notice the light, report it and the empty bag would be replaced and the LED reset. Bag B would continue dispensing til empty when the bags would switch and the LED come back on.
If you want to get really fancy, a small wi-fi transmitter to notify maintenance when a bag is empty.
I started off thinking of some minimal, battery powered, electronics. As I write this, I think it could be all mechanical with a little red flag that pops up instead of an LED.
John Henry
Thanks for your comments, John!
Yes, somebody above had the idea for a double-bag dispenser. You’re right we’d have to make it not confusing… without automation, it would have to be clear to users (especially visitors) that if one bag in the dispenser is empty that you’d have to move a lever or something to switch over to the full bag that remains.
So maybe some sort of sensor and internal robotics would help. Hospitals would have a concern about the cost, but look at the cost of infections!
And add a removable kanban card to the flag. When it pops up, the nurse grabs the card, leaving the red flag up. The card would have the location of the dispenser written on it.
When maintenance replaces the bag, they write the location and perhaps date on a kanban card and put it on the flag before resetting.
Not sure how these bags come but if in an individual carton, perhaps the carton flap can be torn off and used as the kanban card.
John Henry
I am going to be at a hospital today and will take a better photo of the insides of one dispenser. Not sure what packaging the sanitizer bag/pack comes in…
I had not considered the fire code. In the US this is pretty universal and is promulgated by the National Fire Protection Association then adapted by localities.
I wonder if the restriction is on number of dispensers or quantity of liquid?
Re switchover, I figured it should be automatic. The user should never know, except by the flag, that one container is empty.
I was thinking a spring loaded plate, pushing gently against the bag. When the bag is full, the plate is to the back. As the bag empties, it moves forward and eventually moves a rod. The rod connects the dispensing lever (that the user pushes) to the bag in use. When that bag is empty, it moves, connecting the other bag and raising the flag.
If electrical, it can be done electronically.
This raises another issue: How do the batteries get replaced? Doesn’t matter if the bag is full if the batteries are dead.
John Henry
Re NFPA regulations, I found this at http://www.symmetryhandhygiene.com/training/FireCodeRegulations.pdf
Frequently Asked Questions
How does the National Fire Protection Association define alcohol-based hand-rubs?
An alcohol-containing preparation designed for application to the hands for reducing the number of visible micro
–
organisms on the hands and containing ethanol or isoproponal in an amount not exceeding 95 percent by volume.
2
What is the maximum allowable amount of alcohol-based hand-rub per dispenser?
The maximum individual dispenser fluid capacity shall be as follows:
•
0.32 gal (1.2 L, 1200 ml)
for dispensers in rooms, corridors, and areas open to corridors
•
0.53 gal (2.0 L, 2000 ml)
for dispensers in suites of rooms
1
What is the total quantity of alcohol-based hand-rub that can be used in any one area?
Not more than an aggregate 10 gal (37.8 L) of alcohol-based hand-rub solution or 1135 oz (32.2 kg) of Level 1
aerosols, or a combination of liquids and Level 1 aerosols not to exceed, in total, the equivalent of 10 gal (37.8
L) or 1135 oz (32.2 kg), shall be in use outside of a storage cabinet in a single smoke compartment, except as
otherwise provided in 19.3.2.6(6).
1
One dispenser complying with 19.3.2.6 (2) or (3) per room and located in
that room shall not be included in the aggregated quantity addressed in 19.3.2.6 (5).
1
How much spacing is required between each installed dispenser?
Dispensers shall be separated from each other by horizontal spacing of not less than 48 in. (1220 mm).
+++++++++++++++++++++++++++
So you can have 1.2 liters in a dispenser. So 2 half liter bags in a single dispenser? A bit more expensive, unless they are refillable but still cheaper than the cost of poor hand hygeine.
John Henry
When it’s REALLY important that you do NOT run out of something:
I love this exercise!
I visit a local critical care hospital almost daily(my wife works there.) Much to my wife annoyance, I spent most of our lunch break today staring at and then bugging EVS staff to see hand sanitizers around the cafeteria. My first thought there is a lot of time and cost for a manufacturer to change a relatively standard seemingly cross-platform design of the dispensers themselves. I came up with two possible hypotheses.
1a. Alter the material of the dispenser allowing for a transparent case around the soap 1b. Convince the soap companies to use a color that is easily visible. A combination of change in material and bolder color could allow EVS or nursing staff to see the soap needs changed.
2. Perhaps the base that the sanitizers hang/sit on could have a counterbalanced/weight sensing system (either mechanical or digital) that allows the hospital to mount a dispenser and set the weight of the empty dispenser. As the soap gets used and the unit gets lighter the weight difference could correspond the percentage used with a trigger either a light or colored scale that changes to red once the weight is withing a few ounces of an empty container. That flag would signify that the soap needs to be replaced.
Thanks for your thoughts. I wonder if there are any implications from having a non-clear solution?
Interesting idea about using weight. Mechanical devices that don’t require any batteries or power are intriguing for this use.
I appreciate the group brainstorming that’s taking place here!