Mark's Note: Here's another guest post by Paul Critchley, a regular contributor to LeanBlog.org. I'm also not a fan of signs in the sense that they are rarely an effective root-cause solution to any problem, as I blogged about here in 2007: “Signs are not Error Proofing.” See my other blog www.BeMoreCareful.com for more.
By Paul Critchley:
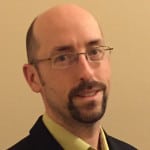
I'm not a big fan of signs.
Mind you that I'm often thankful for them, like when I go to an airport that I'm not familiar with, but that's really thanks to industry standardization more than the signs themselves. I know I can always look at the Arrival / Departure Board to find my assigned gate, and follow the signs to baggage claim once I've landed. By and large, each airport has the same signage and posts them in roughly the same places, so I know what to expect and where to look to find my way around.
Here's my issue: too often, in industry, the concept of “posting” something has replaced its true meaning of ensuring that its contents are understood. There's an overwhelming belief that if a rule or law or decree is “posted,” then it is somehow magically known and understood by all who read it, which is simply not true.
For instance, here in Connecticut, in order to comply with state and federal regulations employers must post 14 different notices to their employees. They cover very important topics like Equal Opportunity Employment, Minimum Wage, and Sexual Harassment, to name a few.
The problem is that the requirement states that these regulations must be posted, not necessarily that anyone is trained on what they mean or how they affect you as an employee. Simply posting a notice like this doesn't truly accomplish anything, as I doesn't ensure any amount of understanding. For instance, there are companies who have made a business out of conglomerating all of these notices onto one giant 2'x3′ poster, so for a few mouse clicks, four thumbtacks and $30, you can be technically compliant to the regulation.
Whenever I interview the associates at a new client, I always ask them about this poster specifically.
Do they know where it is, what it is or what it means? Have they ever actually read it?
The answer is almost always “no” to all four questions, which means that the poster, like outdated KPIs or work instructions, is just wallpaper.
I've found similar results for other signs, too. In one case, when I asked an operator about signs, he took me around to the back of his machine to show me the doors of its electrical cabinet. Measuring approximately 4'x4′, the doors were almost completely covered with signs, stickers and placards about electrical hazards, required Personal Protective Equipment and the like.
It was obvious that the large, flat area was just too much of a temptation, and so over the years it had become the favorite repository for said signage. But again – it was on the back of the machine, out of sight to everyone except a maintenance guy when he needed to lock it out to work on it.
When I asked the operator if he'd ever read all of the signs or been talked to about them before, he looked at me with a “You're kidding, right?” look on his face. No words needed.
The counter argument I get sometimes is that by posting signs, folks can't claim that they “didn't know” about a rule. That's a cop out. Posting a sign about an important topic in some random place in the shop doesn't support “Respect for People,” a pillar of Lean. If a manager can't spend the time to talk with his or her direct reports about important topics to ensure understanding, there is something wrong beyond whatever the sign says.
Another issue surrounding signage is that of enforcement. If there is a sign posted with some sort of instruction on it, you need people to make sure that the rules on the sign are being followed.
Take posted speed limits for example. We all learned in driver's education that by law we have to stay under the speed limit. Try doing this today on the interstate and watch how many dirty looks you get from other drivers.
Police officer friends of mine admit (off the record, of course) that they'll seldom pull anyone over for doing 5 or even 10 miles over the posted limit. So societally, we allow non-compliance through a level of ambivalence, even from those whose sole job it is to enforce the law.
So why should work be any different? In some cases, it isn't.
As an engineering manager at an aerospace company, I once had to throw a senior-level engineer out of a Foreign Object Debris (FOD)-free area for eating a bagel…right next to the hardware we were building for the United States military.
There were signs at every entrance to the area (plus many more hanging from the ceiling) that described the area as “FOD-Free,” yet there we were, on opposing sides of a thin line of cream cheese.
He knew better, of course. He just figured the rules didn't apply since he'd gotten away with it before and no one had said anything.
Signs are valuable tools that provide needed information, but they aren't meant as a replacement for training and proper follow up by supervision.
A Lean culture encourages interaction, and supports the two-way communication that happens during such. So keep the signs that point to the exits and mark the fire extinguisher locations, but lose the ones that seek to teach. Those moments are best spent face-to-face.
Please scroll down (or click) to post a comment. Connect with me on LinkedIn.
Let’s work together to build a culture of continuous improvement and psychological safety. If you're a leader looking to create lasting change—not just projects—I help organizations:
- Engage people at all levels in sustainable improvement
- Shift from fear of mistakes to learning from them
- Apply Lean thinking in practical, people-centered ways
Interested in coaching or a keynote talk? Let’s start a conversation.